ZIP R-Sheathing Climate Zone 5?

I am considering ZIP R-sheathing for a home in Climate Zone 5. The wall assembly would be a ventilated rainscreen as follows (exterior to interior)
1. Hardie Panel siding
2. 3/4″ furring/airspace
3. ZIP 1.5″ R-sheathing (R6.6 total, 12-16 perms for the OSB, <1.0 perm for the polyiso) 4. 2×6 studs 5. Icynene Low Density (5.5″ thick R-20, 11 perms) 6. 1/2″ gypsum The idea is to create an easy-to-build wall system that is hard to screw up, economical, and maximizes R-value per unit of labor. It seems to me that the dewpoint would occur within the Icynene, and would dry to the interior. The polyiso in the ZIP system would protect the backside of the sheathing, which should be able to dry to the exterior. I am considering dense-packed cellulose in lieu of Icynene, but my sense is that I will ultimately need a spray-foam contractor anyway, so why hire two guys when I can hire one? Thoughts?
GBA Detail Library
A collection of one thousand construction details organized by climate and house part
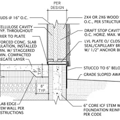
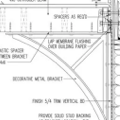
Replies
Joseph,
There are several issues related to the question of whether it's a good idea to use R-6.6 Zip-R sheathing on 2x6 walls in Climate Zone 5.
In theory, if you want to install rigid foam on the exterior side of a 2x6 wall filled with air-permeable insulation, you have to follow the rules set out in this article: Calculating the Minimum Thickness of Rigid Foam Sheathing. That article notes that the minimum R-value for the rigid foam layer in this case is R-7.5 -- so R-6.6 won't work.
However, in your case, you aren't suggesting the insulation of air-permeable insulation between the studs; you intend to install open-cell spray foam. The open-cell foam is an air barrier, so it reduces the risk. That said, the open-cell foam still allows outward vapor diffusion during the winter, so the installation of a smart vapor retarder on the interior side of the wall might be cheap insurance.
There are other complicating factors to this discussion; for example, some people maintain that because the polyiso layer in the Zip-R sheathing faces the interior, the sheathing is protected by the polyiso, reducing the chance that the sheathing will accumulate moisture during the winter. That's true, but the inside face of the polyiso still represents a potential condensing surface during the coldest days of the year.
In short, this is a complicated question. But on balance, I think your proposed wall assembly will work.
While it technically meets code and the OSB is protected from interior moisture drives by the interior side facer, with that stackup there is a slight risk of moisture accumulation (or if excessive, frost damage) in the Icynene where it meets the interior facer of the ZIP-R unless you install a smart vapor retarder on the interior. From a good/better/best practices point of view using vapor barrier latex on the interior or a more vapor-open variable permeance smart vapor retarder such as MemBrain between the gypsum & foam would mitigate that issue. If going with cellulose you'll definitely need/want the smart vapor retarder.
In a zone 5 climate the performance will probably be substantially LESS than labeled R-value of ZIP-R due to the temperature dependent properties of polyisocyanurate foam. When the average temperature through the polyiso layer is below 45F or so (which will be most of the winter in most of climate zone 5 with your stackup) the performance of polyiso is less than EPS:
https://www.greenbuildingadvisor.com/sites/default/files/Karagiozis%20-%20thermal%20conductivity%20of%20a%20variety%20of%20insulations%20as%20a%20function%20of%20mean%20temperature.jpg
When the average temp through the foam is below freezing you're looking at no more than about half it's labeled performance, so even with 24" o.c. stud spacing your mid-winter whole-wall performance is going to come in at about R17-R18. (For this reason ZIP-R really only makes performance-sense in warmer climates, from the warm edge of zone 4 on south, so that the polyiso stays within a higher-performance range at the winter temperature averages.) Ideally you'd be north of R20.
At about the same wall thickness with a 2x4 16" o.c. studwall w/cellulose or Icynene and 2.5" of exterior EPS you'd be at R20-R21nominal for whole-wall-R at the labeled performance of the EPS, but it would perform at about R23 in January when you need it the most, and you would have HUGE dew point margin at the sheathing, no interior vapor retarders needed. You'd need some form of weather resistant barrier at the appropriate layer too. On a material cost basis it comes out a bit cheaper, but there is more assembly labor involved.
Thanks, guys. In my day job as a commercial architect, our standard wall sections usually involve 3" of XPS rainscreen outside sheathing & vapor barrier (although it occurs to me that we could probably add some interior spray foam and keep the dewpoint in the plane of the XPS); however I am leery of expecting residential builders to understand an exterior insulation concept. In my limited experience, rainscreen in & of itself is a foreign concept to this group of people- despite the fact that James Hardie has recently started recommending this approach in its official literature. Is my limited experience just bad, or is the exterior insulation approach one that builders are actually catching onto?
For what it's worth, we'd be only 60 mi. north of climate zone 4 - if that matters.
Joseph,
I suppose builders' familiarity with exterior insulation varies by location. Here in northern Vermont, the exterior insulation approach is by now quite common.
Would the same assembly work (in Zone 5 or 6) with the use of closed cell high-density foam at 4" inside the cavity, thereby rendering the dewpoint/condensation issue moot?. That would put R24 into the wall, eliminate the bridging and allow a practical R3 on the R-Sheathing polyiso in typical Zone 5 condition mid-January weather. It would seem like a practical and tight R-27 wall with minimal bridging. Thoughts on that system?
Joe,
Like any system that depends heavily on closed-cell spray polyurethane, the approach you suggest is both expensive and environmentally unfriendly. (Closed-cell spray foam uses a blowing agent with a very high global warming potential.)
But the wall assembly would work.
Perhaps the assembly would have a smaller footprint with 2x4 framing done in "smart framing" fashion, with the 3.5" of closed cell. I would just think it scary to use that with cellulose. But you sure are right about the cost. Some architects I talk to seem to think that the code will eventually embrace the foams and require them. I can't say whether that is a reality or not, but more than one seems to think this is coming. I am just also wondering why we don't see nail base (foam and OSB on one side) used with 2" foam in more application like this, but maybe at less expense.
Joe,
In comment #5, you mention that your proposed structure would "eliminate the bridging." That is not the first time I have heard someone imply that having any amount of continuous insulation makes the thermal bridging issue go away completely. That is not my understanding. There is still a thermal bridge through much of the wall. My understanding is that the thermal bridging issue gets progressively less significant as the continuous R-value increases, but it never completely goes away.
I wonder if this impression is a carry over from people used to working with electrical wiring where insulated or not is largely a yes or no proposition. When it comes to thermally insulating houses, it is always a matter of degree.
Reid has it right- putting R6 over the framing fraction doesn't eliminate the thermal bridge, it just doubles the R-value at the 2x6 framing to R12.5 -ish (instead of R6.5 ish) for that ~25% fraction, which is still WAY below the center-cavity R of the other ~75%. It's not a very significant thermal break, but it's better than nothing.
With only 4" of cavity fill the thermal bridging is even higher, since there is now only a 4" path through the framing, for an R5 rather than R6.5-ish thermal bridge. R20 cellulose or open cell foam will outperform R25 closed cell foam in a 2x6 cavity, due to this factor. The cavity has to be completely full to bring the framing fraction up to R6.5. But even then, going with a full cavity fill of closed cell foam in a 2 x 6 assembly adds about R2 to the "whole wall R" above what you'd get with open cell foam or cellulose.
The insulation in ZIP-R is polyiso, which has to be SERIOUSLY derated for temperature in climate zone 6 if it's only 1" thick. That R6 is probably only performing at R3 when it's 0F outside, when the average temp through the foam is under 20F. The labeled R is it's performance when the average temp through the foam is 75F, with a 90F warm side and a 60F cold side. That performance rises a bit when the average temp through the foam is about 55F (hot side 70F, cold side 40F), but falls pretty fast as the average temp drops. In thin sheathing applications on the outside of R20+ cavity insulation in a cold climate it's wintertime performance is well below it's labeled performance, since it's average temp is below 40F most of the season, often WAY below.
ZIP-R is great for US climate zone 3 or even marine 4C, but it's somewhat marginal for zones 5 & up.
If you want to add some closed cell foam to the interior side of ZIP-R for dew point control in a zone 6 climate it only takes a an inch. Fill the rest with R4-R4.3/inch high density fiber or R4/inch open cell foam. That leaves you R9-R12 on the exterior of the fiber or vapor open layer (depending on outdoor temp) which is sufficient dew point control for ~R20 in the fiber (or open cell) layer without interior vapor retarders. But for the money you'd get more thermal performance out of standard sheathing with 1" of polyiso on the exterior (R6-6.5 nominal, R5 derated for temp in this stackup), and a 1.5" layer of Type-II EPS (R6.3 nominal R7 up-rated for temp) over that, to keep the iso warm enough to perform, and use R20 damp-sprayed cellulose or R23 rock wool in the cavities. That way you'd get R26-ish whole-wall performance out of it instead of an R19-20-ish performance (less, with the 4" closed cell foam proposition.)
Reid, I should have used the term "reduced" so I stand corrected. Dana, are you saying to use 2.5 inches of foam on the outside of sheathing in two layers? I often find the more complex the detail, the more chance for mess-ups.Why aren't people just using something like 3" thick EPS nailbase with the foam under the sheathing facing the studs? plus an inch of closed cell and then rock wool at R-23 in a 2x6 wall? It would seem simpler. This R--Sheathing by ZIP is just a glorified nailbase, correct? Why don't they make this stuff with at least two inches of EPS instead of the Iso? I suppose it would be too easy to damage (???)
Joe,
You can purchase EPS nailbase if you want. Before using this product as wall sheathing, however, check with an engineer to be sure that you have a good wall bracing plan.
Here is a link to a GBA article about using EPS nailbase on walls: A Deep Energy Retrofit Using Nailbase Insulation Panels.
Here is a link to web page by a manufacturer of EPS nailbase:
http://www.achfoam.com/NailbaseRoofInsulation.aspx
Multiple layers is somewhat more effective than one due to both seasonal and long term expansion/contraction of the foam leaving gap between abutting sheets.
In this case we're talking about two layers of foam of differing types to maximize performance per inch of thickness. If going with nailbase EPS for the outer layer it would still make sense to have a another foam layer, seams taped and staggered with those of the nail base.
ZIP-R is a "glorified" (?) purpose made thin nailbase panel, with a WRB coating pre-applied to the exterior side, and a Class-I vapor retarder on the interior side. But they have also engineered & qualified it as a structural panel sufficient for the racking forces when the specified fastener regimen is followed. If you're hanging a 3" nailbase panel on bare studs with 4.5" screws you may have to do the math on whether it makes it as a structural panel or not (or what the fasteners & spacing requirements would be to get you there.) It's one thing to hang nailbase on the exterior of an existing structural wall, but it's a bit different if you're requiring the nailbase panel to be something more than a convenient nailer for the siding.
I think what is initially attractive about a product such as this is that it puts the foam insulative layer btwn the studs and the sheathing, thereby eliminating the difficulties inherent in the foam on the outside, while still decreasing the bridging between studs and sheathing. Also this product, which includes the flashing tape for a dried in stud bay also has it's appeal over house wrap and regular sheathing which is not typically taped at seams. I am wondering what the future prognosis is for s similar or more advanced product to come along that may include EPS AND Iso and at greeater thicknesses. Time may tell, if these companies are listening. But currently the foam over sheathing is not appealing for a number reasons to the crews and those who handle window and door installs after the sheathing is up. Subcontractors are not always in synch on the details.
After thinking a bit more, I was wondering about the inclusion of "Mooney" wall with sleepers on the inside of the wall just before you place your sheet rock, if you are dead set in this wall. Perhaps you reduce bridging further with this method and then it allows more dense pack cellulose or other insulation beyond the five and a half inches...food for thought? If you were doing the foam, you could then cover most of the 2x6 lumber to get the fuller cavity and less bridging via those studs. It might be a good compromise on the double stud wall.
Joseph, I was kind of curious if you went ahead and built this assembly or modified it to use the "Mooney wall" strapping to reduce bridging as I suggested. And also if you are building this wall, did you include a smart vapor retarder?
We're still in the planning phase, but we're not planning on using the zip R-Sheathing anymore. We're going to do 2" (maybe 3") of rigid foam on the exterior, standard zip sheathing, and then icynene between the 2x6's. No plans to use a Mooney wall or smart vapor retarder. Our interest in the Zip product was related to the potential to save a step in construction, but I don't think it's really the right product for northern climates.
Zone 3A (Northern Edge)
Q: For my climate zone how would this wall perform with rockwool batts used as interior insulation in lieu of foam?
Joseph, you are sticking to the open cell spray foam product, correct?
Response to Chris M (Comment #17):
In your climate zone, there is no minimum R-value requirement for exterior rigid foam. Any R-value will work. For more information on this issue, see Calculating the Minimum Thickness of Rigid Foam Sheathing.
Zip R sheathing over a wood-framed wall insulated with mineral wool batts will work fine, as long as you pay attention to airtightness. Use Zip System tape on the sheathing seams, and seal air leaks at windows, doors, and penetrations, and your wall will perform well.
Joe, What is your logic for using Icynene in combination with Zip system? In my view, the premium price of either product relative to alternatives is justified by the air sealing capability. However, once you have chosen one of those products, the air sealing capability of the other one isn't buying you much. Two air sealing layers isn't a problem, but the extra money might be better spent elsewhere.
We are planning to do the open-cell Icynene, but our decision to use Icynene as opposed to cellulose or other products is largely driven by the fact that we're doing a basement, which will have rim joist spaces to insulate. Spray foam seems to be the best product for that application, and since we would already have that contractor out on site, I'm not sure that we'd realize much in the way of cost savings by bringing another contractor out to put in a less costly type of insulation. Were we doing a slab-on-grade, we'd probably choose cellulose.