Vented roof in the Pacific Northwest

I was interested in the brief thread started by Malcolm Taylor, referring to condensation problems for vented roofs in the Pacific Northwest:
https://www.greenbuildingadvisor.com/community/forum/general-questions/99637/roof-sheathing-pnw
It looks like there has been a flurry of research, mainly done by RDH, but I haven’t seen much follow-up.
http://www.rdh.com/re-thinking-ventilated-attics-how-to-stop-mold-growth-in-coastal-climates/
It is my understanding that, with high winter humidity, night-time radiative cooling causes condensation on the underside of roof sheathing regardless of how well air-sealed the house is, or how well ventilated the attic is.
I am a big fan of metal roofing, but my experience comes from a drier climate. My question is whether having a (small) thermal break between the roofing and the sheathing might stop the radiative cooling enough to reduce/prevent the condensation?
I wondered about traditional purlins on top of the sheathing, but that brings the possibility of condensation on the underside of the metal itself. Perhaps this isn’t a big deal, if the underlayment is good quality?
The other thought I had was using something like cedar-breather. This would give a thermal break between the metal and sheathing, allow drainage, but not invite enough air-flow to bring condensation to the underside of the metal. However, I wasn’t sure if it provides a firm enough base for the metal to avoid waviness.
A slightly unrelated factor is that the location we are building is almost guaranteed some kind of forest fire in the next 50 years and I have concerns with cedar-breather being synthetic, even though the metal would protect it from direct contact with falling cinders.
People’s thoughts would be welcome!
GBA Detail Library
A collection of one thousand construction details organized by climate and house part
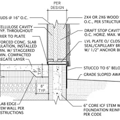
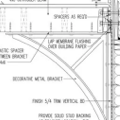
Replies
John,
Condensation on the underside of metal roofing is common, in almost all climate zones, when the weather conditions are right. The solution to this problem is (a) to install solid sheathing under the roofing -- not just purlins -- unless you are building a barn, and (b) to include the code-mandated roofing underlayment above the roof sheathing.
If these steps are followed, you shouldn't have any problems. The condensation generally evaporates before it can find a hole to reach the roof sheathing.
I think that including an air space between the roofing underlayment and the metal roofing is a good idea, even though it isn't strictly necessary. Either 1x4 or 2x4 purlins, 24 inches on center, will work, as long as the manufacturer of the metal roofing approves of installations over purlins.
In my opinion, black mold on roof sheathing in the Pacific Northwest is usually a cosmetic problem, not a sign of incipient rot. Some homeowners freak out when they see mold -- my common-sense advice to these homeowners is, "If you don't want to see mold, don't stick your head into your attic."
If that advice doesn't calm the homeowners, you may want to take the advice of the RDH researchers, and simply build unvented conditioned attics with rigid insulation on the exterior side of the roof sheathing.
Hi Martin,
Thanks very much for your thoughts. I agree that condensation on the underside of the metal itself shouldn't really be a problem, but wasn't sure if PNW climate made any long-term difference because of winter humidity rather than summer humidity.
Solid sheathing is code here for seismic reasons, so my question was whether or not to put purlins on top of the plywood, or just attach directly to the plywood, which I think is pretty common. While some mold is certainly inevitable, I thought that some kind of simple thermal break might slow it down enough to be worth the extra effort.
The RDH study was done with asphalt shingles, so I have some concern that the condensation will be amplified with metal. In essence, the metal roofing is a huge cooling heat-sink pulling all the heat out of the sheathing at night.
I like the simplicity of a vented roof from a cost, insulation, air-sealing, and maintenance perspective. I also wonder if unvented roofs may just cause the problem to reappear in a different way.
Thanks again.
John,
I've been thinking and worrying about this for a couple of years and have come to the same conclusion as Martin. In the absence of some other factor, like poor air-sealing or blocked ventilation, the problem is entirely cosmetic. I have discoloured sheathing on the underside of my ventilated and unheated shed. There is some on the north side of my attic too. Both have been that way for twenty years with no discernible deterioration of the plywood.
Malcolm and John,
I was on the phone this afternoon with Joe Lstiburek, talking about buried ducts (for an upcoming article on burying ducts in attic insulation), and we ended up talking about the problem of mold on roof sheathing in vented attics in the Pacific Northwest.
Joe's solution -- not allowed by code, but that never stopped Joe -- is to seal up the soffit vents, and convert the ridge vent to a diffusion vent. (Basically, this means temporarily removing the ridge vent, and covering the ventilation openings at the ridge with a layer of housewrap, installed in an airtight manner.) Joe says that inviting outdoor air into your attic makes things worse in some climates.
The usual caveats apply -- namely, that this approach isn't a good idea anywhere where ice dams are a concern.
The "diffusion vent" approach is outside the envelope of code-approved solutions, so experiment at your own risk.
For more information on diffusion vents, see these two GBA articles:
Smart Vapor Retarders for Walls and Roofs
Can Unvented Roof Assemblies Be Insulated With Fiberglass?
Diffusion vents are generally MUCH larger in area the ventilation area of regular ridge vents. To be effective requires replacing the decking at LEAST 6" to a foot or more either side of the ridge with something highly vapor permeable such as MDF or asphalted fiberboard (if you want something rigid) or housewrap.
From Joe's site it looks like he's recommending replacing the roof deck 12" either side of the ridge:
https://buildingscience.com/sites/default/files/migrate/jpg/BSI088_Figure_04r_web.jpg
https://buildingscience.com/documents/insights/bsi-088-venting-vapor
Interesting.
I had never heard of diffusion vents before. Thanks Martin, and also Dana for clarifying size requirements. I have to admit that I have some gut resistance to the idea of an "airtight" attic, even with moisture diffusion ability.
I guess it sits in a larger general discussion of how much ventilation an attic needs for a well-sealed house. If there is little (or no) moisture getting to the attic from the living space, can the ventilation requirements be scaled down significantly? I guess Joe's idea is that zero ventilation may be fine. Not sure I am willing to be the lab rat for that one, though!
As a much smaller step, would making the roof venting "just" meet code, and no more, go some way to reducing the moist exterior air load?
Malcolm, in your experience on Southern Vancouver Island, have you seen much difference between metal roofs directly screwed to sheathing vs raised on strapping/purlins? As you say, I don't think it is worth a lot of effort, but I wonder if a simple thermal break like that might give the roof sheathing an extra 10 years of life. I am also still curious if anyone has experience putting cedar-breather under metal roofing.
I finally had time to read Joe's article that Dana linked above. He makes a fascinating case for the diffusion vents. Just a few things I noticed, though.
1) The vent area was actually the same as for regular "airflow" vent systems, but also needed to extend down any roof hips by 4'.
2) He only recommends this in Zones 1,2,3. I am in 4C and would not want to try to convince a building inspector to take a risk. I am guessing that the humid south behaves differently than the PNW, where our winter is humid and our summers dry.
3) He requires a supply of conditioned air to the attic. That seems like a huge waste of energy if the insulation is on the attic "floor". I am guessing he is only doing this on roofs where the insulation is under the sheathing, which is more common in Zones 1,2,3 where the mechanicals are in the attic.
Interesting read, though. Lots of food for thought.
John,
i've never seen or done a house here with purlins over sheathing. I do think metal roofs with purlins work well here, partly because the wood is more resilient to moisture than plywood. I've never seen the black mold on purlins or the trusses themselves, it's always on the sheathing. That's not much help here though as the seismic provisions in our code requires that roofs be sheathed.
I don't think the problem is anywhere severe enough to think about the sheathing needing something to give it an extra ten years. I've got metal roofs on some projects that are now 25 years old, and neither the roofing or the sheathing below looks like it has any appreciable ageing or damage - even if it shows some discolouration.
I guess that the one situation where this could become a problem would be in a roof with other borderline problematic conditions - say poor venting, a complicated geometry or inadequate air-sealing. Then the night-time cooling might tip the balance and make the sheathing more susceptible to damage.
Malcolm,
Thanks for your observation about purlins vs sheathing. Looking at the cost of cedar breather makes it much less interesting, even though the manufacturer does certify it for metal roofs. As you say, a minor improvement in sheathing life is probably not worth a big effort.
However, I have stayed in buildings in Europe that have been standing for 300 to 500 years, and think that we perhaps don't take longevity as seriously as we could. I know that many people over-reacted to the mold scare, but low-grade moisture over many years cannot be great for helping a building last 300 years.
As a simpler alternative, I noticed this older video by Matt Risinger where he did diagonal strapping with skips for airflow:
https://www.youtube.com/watch?v=DpxLi_Rm30s
His application is for very different reasons (on top of insulation board on an unvented roof), but the idea seems basic enough that it might be worth the effort. I would have to find a roofer being willing to try it, though.
Breaking some of the thermal contact between the metal and the sheathing should also reduce attic heat in the summer. Although, we don't get nearly the high temperatures seen in other climates.
In the end our roof may well just have the roofing straight on the sheathing, like everyone else. I do appreciate the chance to hear people's thoughts and feedback, though.
John,
There were several discussions about small air-spaces under metal roofing a couple of months ago. I came down on the side of them being counter-productive for a couple of reasons. I'm not sure that they can be ventilated effectively, and in the absence of ventilation they may create a space for condensation to occur which would have no where to go. I also have doubts about installing metal roofing over a flexible substrate like Cedar-breather (particularly the penetrations and trim that rely on gasketted-fasteners) despite the manufacturer saying it's an approved use. It would be interesting to ask several of the roofers in your area if they would guarantee such an installation.
The discussion of longevity is an interesting one. Houses in North America don't generally get abandoned because they have deteriorated while being lived in. They are demolished for demographic reasons, or because they no longer fit the prevalent lifestyle of potential owners and aren't seen as being worth maintaining. The chances of a house either of us builds, no matter how robust, avoiding this fate and still being in use 300 years from now is almost nil.
That isn't to say I don't think it's a good idea to build disposable houses, just that we should be realistic about their potential lifespan. I try and divide the parts of a house into those that will last the whole life of the dwelling (foundation, framing, etc) and those elements that will have to be replaced - and then try and detail them so this work can easily be done. I also try and design houses and building assemblies so they are easy to adapt and renovate. If your house is still in use in a hundred years, it will undoubtedly be because it has been extensively modified to meet the demands of people living in the 22nd century. I don't think a few sheets of plywood will have made much difference to whether this occurs or not.
Aside wrt longevity -
Building longevity in indeed an interesting topic. Even assuming that a building is durable and pleasing to look at and live in, owners and tastes are inevitably going to change. If the building can be built in layers that are relatively disentangled, the short-term surfaces can be changed readily while the long-term parts of the structure and site stay unchanged. Malcolm’s design goals sound like the Open Building concept that I’ve seen described by Tedd Benson, among others [e.g., Fine Homebuilding, Andrew Dey, Nov 2006]. I think “Open Building”, along with durable details (sufficient overhangs, good flashing, etc.) are about the best we can hope for; 300 years unchanged isn’t going to happen.
Thanks Malcolm and Andrew for your comments about durability vs change. I had not heard of the Open Building concept. Modularity and adaptability make a lot of sense.
If I was building for other people, I think your attitude is the right one. You cannot assume too much about future owners and every building has to have compromises.
I do have a background worry, though, that we are somewhat planning for only the wealthy people of the future. The luxury of being able to significantly remodel your house every 30 years may not be available to all of our descendants.
I thought I would resurrect this topic from a while back. RDH has now published two summary documents following up from the research linked in my original post. There is also a related sheathing treatment lab study. The level of detail in these studies is really amazing and I am hugely appreciative that BCHousing funds such things in our province.
https://www.bchousing.org/research-centre/library/building-science-reports/asphalt-shingle-roofing
https://www.bchousing.org/research-centre/library/building-science-reports/field-evaulation-roof-sheathing
https://www.bchousing.org/research-centre/library/building-science-reports/mouldy-sheathing-treatments
They reinforced a few points raised before: In the winter, vented roof sheathing in the PNW gets wet from outside air condensing (or sorbing) on the underside, even with zero contribution from interior air, and even with "unrestricted" ventilation.
They answered my initial question with a surprising result (to me): Inserting a thermal break (drainage mat) between the roofing and the sheathing actually made things worse! The conclusion was that the reduction of heating (drying) during the day was more significant than the reduction of radiative cooling at night.
To me, this seemed to imply that radiative night-sky cooling might be less of an issue than just plain ambient temperatures (below dew-point) in a PNW winter. If anyone reads the results in a different way, I would be interested in other interpretations.
There were a few wood treatments that showed promise. The cost for most of them isn't clear, but the Kilz primer would not be a huge expense if a homeowner was willing to do the labor of painting the plywood, perhaps even before it went up on the roof (if the geometry was not too complex).
While there was no perfect solution, I was happy to see such a good study done on this lingering question!
John,
Thanks for the links, and I too feel very indebted to BC Housing for the support they give us through their research. I think your take on it is spot on. The ambient conditions here in the PNW mean wood is wet for much of the year. That generally is only a problem that need addressing for areas close to grade, and roof sheathing. Hopefully soon a factory installed treatment will be available that will mitigate the problem with sheathing, but it still doesn't seem to be a problem we urgently need a solution to.
The question of gaps under roofing seems settled here in the PNW, but I wonder how climate specific that is? In somewhere hot that still had significant condensation from night sky radiance, I wonder if the heating from a roof built with a gap might outweigh the wetting? Fortunately for us, that's someone else's problem.
Good point about the radiative cooling being a very climate-specific issue. Martin's article that discussed the wet roof insulation in Arizona was eye-opening.
In my particular case, we are planning large overhangs which will amplify air pressure at the soffit. (Well, I say planning, but we are about 2 years later and still in our planning process.) That pressure also comes with wildfire risk for ember entry into attics through the soffit vents. I note that California now requires closeable soffit vents or ones that automatically shut from heat.
I was mulling installing the closable soffits, since it would be easy enough to use a pole to close them in July/August if it looked like a very hot dry summer. This got me thinking that I could also close them from November to March, to avoid the worst of the ambient winter moisture. Regular dry season sunshine would then (hopefully) dry out any residual moisture that had collected in the winter.
Vents:
https://www.youtube.com/watch?v=b6QLMtHxAxI
My only caution is that the ridge vent would not get closed, and it might depressurize the attic when the soffit vents were closed. Our code allows us to overweight the vents up to 75% to the bottom, so the "suction" effect may not be too bad if the ceiling was well sealed?
Even if this worked, closeable vents would only work for a motivated homeowner. For the long-term we need more automated solutions.
John,
Where are you building? I have a feeling I've asked before and forgotten.
I don't know much at all about wildfire protection. I'm relying on being in the fog zone of the Island and having clear-cuts forming a barrier. We did have one about ten kms away last year, so hopefully my complacency doesn't come back to bite me on the ass.
This seems like a good guide: http://www.californiachaparral.com/bprotectingyourhome.html
Thanks for the link! Anything with Jack Cohen is bound to be very good.
On a similar theme, this is another California site I have liked:
https://ucanr.edu/sites/fire/PrePost/Building/eaves/
As for venting, this video was thought-provoking:
https://www.youtube.com/watch?v=nd3p6ai_c-Q
I am about 40 minutes away from you, on the Saanich peninsula in the Doug-Fir/Arbutus zone (we chatted on the phone a couple years ago). A little drier, I think. Having family that saw 100 acres burn in the interior a couple years ago, I am very cautious of wildfire even in our mostly-rain-forest. This time of year, it is hard to ever think anything would burn here.
However, with trees (and park that will never be trimmed) all around our site, I figure it is like an earthquake: A matter of "when" not "if." There are plenty of old fire scars on the older trees, if you start paying attention.
I do remember the fire out your way a while back. We had other friends up-island that were close to the Maple mountain fire, as well. Perhaps that will excuse my preoccupation with the opposing questions of moisture and fire...
(Sorry to not see your message for a couple days)
John,
Sorry - I remember now.
I think my complacency over fires is probably a coping strategy. We are on a heavily treed lot that would be next to impossible to protect. Sometimes when those winter wind storms come through and I hear the trees falling nearby, I dream of relocating my house to a nice safe Costco parking lot.