Retrofitting double wall house – best approach?

Hi folks – long time reader – first time poster:
We’re currently retrofitting a duplex in Wisconsin (zone 6B, near 7A). The ultimate goal is reduce air infiltration, improve insulation, and establish proper water barriers. The original builders used almost no flashing and air sealing wasn’t done, so I intend to remove the siding and exterior OSB to find and fix any water damage that exists. The fiberglass batting will be removed, and the original windows and doors will be replaced as well.
I would like to use the “greenest” materials possible (chemical sensitivities are a concern, as is carbon impact), but would like the improvements to last for as long as possible and not require significant rework in the future. Amendments and improvements will be done one wall at a time over the next year.
The structure ABOVE the foundation has offset double walls (~10” from drywall to OSB). From
inside out, the layers are:
A) Drywall
B) poly sheeting (unsealed, doesn’t wrap windows)
C) fiberglass batting in 2”x4” conventional wood framing (24” on center?)
D) 3” gap (the tops of the walls are open, so air flows far too freely)
E) second stud wall w/ fiberglass
F) OSB
G) vinyl siding
BELOW the foundation, from inside out (above the foundation), the layers are:
A) Drywall
B) poly sheeting (again, unsealed)
C) fiberglass batting in conventional wood framing
D) Foundation (unsure of thickness)
E) 1 or 2 layers of 3/4” blue foam sheeting – below grade, so information is limited
The ATTIC has blown cellulose, but again, no sealing was done. I’ll seal as well as I can following techniques I’ve seen here and then add more cellulose.
I have a plan in mind, but I thought I’d ask open-ended questions first. What insulation materials and scheme would be best above and below the foundation level? What about the air barrier? How important is sub-grade insulation for the foundation (I’d have to dig it up…)? How do I avoid water condensation in my new wall?
GBA Detail Library
A collection of one thousand construction details organized by climate and house part
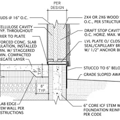
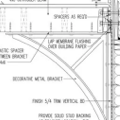
Replies
Erik,
If you plan to "remove the siding and exterior OSB to find and fix any water damage that exists. The fiberglass batting will be removed, and the original windows and doors will be replaced as well," then you've answered your own question. It sounds as if you already have a plan.
If you do the work you describe, you should perform as much air sealing of your walls as possible, and then insulate your walls with dense-packed cellulose.
Below-grade walls should be insulated on the interior with rigid foam or closed-cell spray foam, following the advice in this article: How to Insulate a Basement Wall.
The attic floor should be air-sealed following the advice in this article: Air Sealing an Attic.
Good luck.
If the studs of the two studwalls are aligned, it would be possible to staple blowing mesh from the interior stud to the outer, which would make it possible to properly dense-pack insulation in there. Without side barriers it's tough or nearly impossible to get consistent density. Either 3.5lb cellulose or 1.8lb fiberglass would be suitable here. Pull the MSDS sheets on the potential products for potential chemical sensitivity issues.
Cellulose is greener by a good margin, but fiberglass would be somewhat higher performance, and greener than most foam solutions.
The interior polyethylene is a 2- edged sword, blocking all drying toward the interior, and since it's not air-tight, it makes it an even bigger problem. Go ahead and yard it out, air seal the gypsum using whatever it takes working from the cavity side, and paint the cavity side of the gypsum with "vapor barrier latex" primer. The vb latex is a Class-II vapor retarder, and will dramatically reduce the rate of moisture migration into the cavity over the winter, but gives it at least some drying capacity toward the interior.
It's worth getting quotes for open cell foam in lieu of fiber insulation, which would also simplify the air sealing process, and may be cheaper than dense-packed cellulose or fiberglass, but comes with a different set of chemical issues to sort out. Open cell polyurethane is the greenest of any foam solution.
OSB is a class-II vapor retarder on the "wrong" side of the assembly. If you can stabilize the walls with let-in bracing or plywood shear panels on the ends of wall sections, using fiberboard (eg Celotex) or exterior rated gypsum (eg DensGlass ) for the majority of the sheathing gives the assembly an order of magnitude higher drying capacity, making moisture accumulation far less likely. If you went with 3/4" fiberboard it adds another ~R1.5 of whole-wall performance beyond where it would be with 1/2" plywood or OSB. It's possible to use fiberboard as structural sheathing using the manufacturers' recommended fasteners & spacing, but it's still a lot more flexible than OSB, which is why bracing or shear panels to improve the overall racking force rigidity might be preferred to relying solely on the fiberboard as the structural sheathing (especially if your local inspectors are unaccustomed to it.)
With ~0.5 perm paint on the interior and 5+ perm sheathing on the exterior drying into the air behind vinyl siding it's nearly impossible to end up with a condensation event inside the assembly, and it can dry in both directions. Leaving the polyethylene in place almost guarantees that you'll have at least some summertime condensation events on the poly if you air condition much under 75F (which some people do, though I'm not sure why.) If you use cellulose insulation the fiber itself would always wick and redistribute those events, but with fiberglass there's at least some potential for liquid water dribbling down to the bottom plate.
Foundation insulation is important, but it doesn't necessarily need to be on the exterior. With 1.5" of blue XPS on the exterior you have sufficient dew point control for the 2x4/R13 studwall, provided it extends completely above grade to the framed wall above, making the poly vapor barrier unnecessary. But if the foundation is not insulated above grade it's worth exploring what it takes to do that. With the poly vapor barrier on the interior the foundation will need to be able to dry toward the exterior above grade, so using rigid rock wool would be a better solution than foam, and you'll have to figure out how to protect the rock wool from the exterior with a cladding that vents to the exterior. The above-grade foundation insulation is far more important than what's below grade, and if it's only an R13 studwall on the interior side that's well below current IRC code minimums. Adding R8 to the exterior would bring it into compliance.
MARTIN – thanks for the reply! I have read those articles. The basement is finished, so adding foam on the inside would be challenging (impossible in some spots). What is the next best option, or are there clever ways to install the foam with the drywall already in place?
Regarding the walls, the plan was to dense pack the 10" cavity (packing triangular vertical columns made using air-permeable netting). My understanding is that the wall will then have an effective R-value greater than 30.
I was also considering adding a layer of foiled foam to the OSB, followed by an air gap (using furring strips), then siding. The addition thickness would impede air flow through the sofits, though I could add gable vents. I read the Calculating the Minimum Thickness of Rigid Foam Sheathing article which gave values for 2x4 and 2x6 walls, but given the thicker walls, I’m unsure how thick an exterior foam layer should be. Further, I’d prefer to use a low-GWP foam; that article provides advice, but it was written in 2010, I’m wondering what foams are currently available that would perform well in my zone. Is there an updated version somewhere? Do foams made nowadays have GWP ratings?
Aside, I liked the work done here, and much of it appears adaptable to our home.
DANA – thank you for the comprehensive and informative post. I will have to research some the materials and techniques you’ve mentioned and examine some of the features of our building. I will reply in detail tomorrow (hopefully).
Erik,
I recommend this article: Exterior Rigid Foam on Double-Stud Walls Is a No-No.
Martin,
Thanks again - missed that article. I'll have to search the site again using new keywords.
After processing both of your input and some further reading, this *Double Wall configuration* appears to be the ideal design. The rim joists on our home extend to the outer walls, which creates difficulty maintaining air barrier continuity. Would the mid-wall OSB air barrier still be the best plan, or could the barrier be established elsewhere with equal efficacy (i.e., is the mid-wall air barrier worth the extra effort)?
For the rim joist, would it be best to have them spray foamed (from the inside) or cut sheet foam to fit, seal/caulk it, and then continue with cellulose (something like this *example*? Regarding sensitivities, I’m primarily concerned about spray foam (off-gassing), but if the advantages are significant enough (aside from ease of install), I’d consider it.
The height of the cavity behind the basement walls, from floor to grade (just below the top of the foundation), is about 4’. Access into the cavities appears to be limited. Removing the insulation and poly sheeting from behind the gypsum appears feasible, but how could the painting/sealing be done on the cavity side? A roller on a stick would work - somewhat.
The inner studwall extends up to the second floor – unless there are windows, the bottoms of which are just above the foundation. As such, the cavities are divided, so it sounds as though the sealed cavities below the windows could be a problem. If I remove the poly, will this alleviate the moisture problem? Is rockwool the best option with the poly removed?
Aside, I plan to log the retrofit, on-line. This would allow critique and perhaps, direction for other homeowners with similar projects. Is there a good site for posting this type of information?