Region 5 below grade basement insulation techniques with intention to finish

I’ve probably read most or all of the articles on the subject 5-6 times over, but am still left with many questions as the advice can quickly change as the circumstances do, and it’s difficult to keep track of all these factors.
My goal is to finish my below grade basement in 18301 Region 5. Cape cod style home built in 1968. 954 sq ft basement.
Standard 16×8 block wall, ranging from 81.5″ high to 84.5″ high on the side with the sump pit. Slab appears to be about 1.5″ thick. Very minimal gravel under the slab. The outside of the block wall appears to have been painted with a black waterproofing paint. I don’t know if any other water management measures were taken on the exterior, but I don’t believe so.
Block wall does not appear to be topped with capstone block, just standard block with holes at the top. I only know this because every 176″ on center, the builder doubled up the block towards the interior to provide stability, and the part of this top layer that is inside the basement has the holes going through.
Then there was a metal termite barrier added on top of the block wall which extends out an inch or 2 into the interior. Then a very thin layer of fiberglass and then 2×8″ sill plate, and then 2×10″ band joist and floor joists. Presently there is fiberglass insulation in the floor joists (and craft faced on both sides oddly), though I intend to remove this mainly as it’s full of mouse droppings. I’m actually considering adding fiberglass back in the joists here but only for a measure of sound absorption between the floors, and I would just use unfaced fiberglass, somewhere between R-19 and R-30.
I have gutters along the exterior which underground pipes carrying the water away. Grading is fairly well done. There does not appear to be any water that comes in through the walls, and the floors also pass a moisture test (taping plastic to the floor does not result in any condensation bubbles).
There are also 5 windows along 2 of the walls, the openings measure 32″ wide by 14.5″ high.
I do have a mildly high radon level, and so I intend to have a contractor install piping and a fan (likely requiring an exterior penetration, unless we find a way through the interior walls and put the fan in the vented atttic and through the roof.
I would like to finish the entire basement, and am trying to decide on the best method to insulate/air seal as well as choose on flooring. I am also trying to take into account electrical receptacle box locations.
I had initially considered method (A), framing 2×4 studs 1″ off the block, and spraying with Lapolla 4G closed cell, 3″ – so 1″ continuous layer and then 2″ into the stud wall. Providing around R-19.5. However, I do not love the “permanence” of the installation. In case I ever needed to inspect or address a problem with the wall.
I then considered (B) a 1″ continuous layer of XPS, caulked at the gaps, and then taped, and framing over that, and then either cutting in additional XPS to the stud bays, or installing Roxul mineral wool.
Though I am also considering (C) a 3″ continuous layer of XPS, with 1″ furring strips and drywall screwed into the furring strips. However, I believe this method would require surface mounted electrical boxes which I’d rather avoid. OR, I could cut into the rigid foam board just where the electrical boxes – I think I’d still retain enough of a layer to keep my air sealing intact.
I believe regardless of the method chosen I will spray 3″ of closed cell on the band joist, wrapping down to connect with the XPS. I may end up using a DIY kit for this rather than hire a contractor. I was just going to install a drop-ceiling in the basement so that I have access for running wires in the future. I know the drywall is a sufficient fire barrier to cover the XPS on the wall, but since this would end at the bottom of the floor joists, I am not sure if I would be required to do anything more to protect against the top of the XPS and the closed cell on the band joist, if I am just installing drop tiles and not drywall on the ceiling.
I am seeking opinions on my stated options for insulation taking into consideration ease of install, costs, ability to maintain and access as much of the house as possible, and overall effectiveness. I like XPS over PolyISO as PolyISO loses R-value in colder temps. And I like XPS over EPS as it has a higher R-value per inch. My understanding is that I would not have a vapor barrier at all. Would this be OK, or would I need to add one? Much of what I’ve read seems to suggest it doesn’t really matter as half the year moisture will want to dry to the exterior and half the year to the interior. But I still want to make the best choice here. Also take into consideration that I already have foundation coating painted on the exterior of my block. Exterior insulation isn’t an option in my situation. I’d like to maximize my interior living space, ideally have access to run wires and receptacles in the walls, and optimize my energy efficiency and air sealing.
For flooring, I have debated between just painting an industrial grade epoxy on the entire slab, or a combination of epoxy, and ceramic tile or vinyl applied directly to the concrete. I’m leaning towards the comnbination, mainly to avoid the excessive prep work required for epoxy, and the need to do the entire thing in one shot to get a consistent finish.
Thanks,
Ryan
GBA Detail Library
A collection of one thousand construction details organized by climate and house part
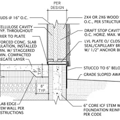
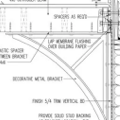
Replies
Ryan,
There is no evidence of water intrusion, correct? Would you okay with installing rigid foam over the existing slab?
No evidence of water intrusion is correct. I am not fond of adding any thickness to the floor as I am about 6'1" and from the slab to the joists at the shortest part of the basement is already about 6'10", and I am planning to add a drop ceiling - though I would install it as close to the joist as possible to the joists - just enough for PEX and electrical wires to pass over, and probably use a soft fiberglass tile or something similar that could easily be installed without any clearance needed above.
I should clarify. On the worst rain storms I did at one point see some dampness on the block wall, but I identified blockages in the gutter pipes which I believe were the cause of this. Once I cleared out the underground gutter pipes which carried away the gutter water, and now that I keep the gutters clear of leaves, I haven't seen any further dampness issues.
Based on personal experience with past three houses. Sounds like you have a "dampness" barrier on the exterior rather than water proofing. In my current house it looks like the contractor sprayed asphalt then a fiberglass mess then some kink of bituminous material about 1/8" thick followed by 4" of rigid foam insulation. If you don't have a moisture problem, I would not touch the exterior.
For the interior, if I followed you correctly, you have bare concrete block walls - good! Bare walls is what I had in this house though the foundation is reinforced poured concrete with a brick pattern. I put another vapor barrier in the form of DryLok Extreme (think paint) two coats followed by two coats of SW highly reflective paint. The floor I painted two coats SW concrete and deck paint (third house for the floor paint). Unless you are in marvelous physical condition, I do not recommend DryLok. That brick pattern was really hard to paint because the surface was so uneven. Use Thoroseal in its place and FOLLOW the directions; it is applied with a white wash brush. The directions say to moisten the wall ahead of your application. If you don't you just might lose your shoulder applying it!!! It sticks.
Then it depends upon what you expect to use the basement for. I was going to use the space for an office and since I am cheap I did nothing for the ceiling. And yes, my desk is three commercial folding tables. I had a large carpet from our other house so I just laid it on the floor. My grandchildren love to play down there. No smell of raw concrete, no dust and dry.
My first inclination was to stud out the walls, use Roxul bats since it is below grade and then mold resistant sheet rock. Never got done.
Ryan,
Q. "My understanding is that I would not have a vapor barrier at all."
A. Foam insulation is a vapor barrier (or more accurately, a low-permeance layer). Three inches of closed-cell spray foam has a vapor permeance of about 0.6 perm. Three inches of XPS has a vapor permeance of about 0.3 perm. According to the old definition of a vapor barrier, any material with a vapor permeance of less than 1 perm is considered a vapor barrier.
If you were thinking about interior polyethylene in your wall assembly, you are correct that it is not a good idea. For more information on all of your questions, see this article: How to Insulate a Basement Wall.
"I like XPS over PolyISO as PolyISO loses R-value in colder temps. And I like XPS over EPS as it has a higher R-value per inch. And I like XPS over EPS as it has a higher R-value per inch."
A couple of misconceptions here:
XPS may not lose R over cooler temperature, but it loses performance over TIME, and permanently! It will eventually fall to pretty much EXACTLY the same performance of EPS of similar density, "lifetime warranty" statements not withstanding. That performance advantage is only temporary. Do you really think anybody is going to submit a claim in 40 years when it fails to meet the "90% of labeled R" warranty terms? (Neither do the manufacturers.) Assume that averaged over the full lifecycle of a house it's performance of R4.5/inch AT BEST (the warranty specification) but really in the trailing years it's better to assume R4.2/inch not more, the same as EPS would be on both day 1, and on day 25,000.
In your stackup the BELOW grade performance of almost manufacturer's polyiso will exceed that of XPS inch for inch pretty much 100% of the heating season, and ABOVE grade 90% of the heating season. And if you use Dow Thermax it will exceed the performance of XPS inch-for-inch 100% of the time.
See the chart on p2 of Dow's bit of marketing fluff (where they claim to have beaten the cool temp derating issues with Thermax):
http://msdssearch.dow.com/PublishedLiteratureDOWCOM/dh_098a/0901b8038098a015.pdf?filepath=styrofoam/pdfs/noreg/179-00263.pdf&fromPage=GetDoc
The temperature scale is the mean temperature through the foam, not the outdoor temperature. Your deep subsoil temps are in the 50s, but near the surface the temps will decline a bit over the winter. When it's 65F in the basement even when the soil temps a foot or two down hits 40-45F toward the end of the winter, with R15 in the stud bays the mean temp through the foam will still be near the peak of the knee in the generic polyiso curve, delivering better than R5.
The mean outdoor temperature in your ZIP code is ~30F even in January, so even in JANUARY 1" generic polyiso would still be averaging over R4.5, which is about what you would get out of EPS, or fully fully depleted XPS.
https://weatherspark.com/m/22901/2/Average-Weather-in-February-in-East-Stroudsburg-Pennsylvania-United-States#Sections-Temperature
If you were living in central Quebec there would be an argument for not using Brand-X polyiso in this application, but not in PA 18301.
Thanks for the comments. Dana, that's exactly the kind of insight I was hoping someone would find reading my proposal. I'll call around on the Thermax, not sure I can find that specific product but I can definitely switch my plan to polyISO over XPS.
Of the options / strategies I described, would you give your blessing to the self installed polyISO over closed cell lapolla 4G sprayed 1" continuous and also between studs to a 3" thickness total, with drywall installed on the framing?
The self-installed polyISO would be 3" continuous as described, with furring strips installed vertically, nailed or screwed in to the block. Then drywall into the furring strips. Wires would go in the gap created by the furring strips. Electrical boxes would either be surface mounted, or carved into the drywall and EPS. (leaving at least some continuous layer behind). It seems the thermax only comes in 1" or 2" sheets, not 3", so I'd need to double stack them. Does having 2 stacked foil layers cause a problem?
Alternatively, I could install only a 1" continuous polyISO layer, with 2x4 framing, and R-13 Roxul installed in the cavities, with drywall installed on the frames. Electrical boxes cut into the drywall, installed on the framing.
Do you like one of these options over the other by a wide margin? Or would either option be about equal? I think the first option gains me about an extra 1" of living space based on 1/2" thick furring strips, but I end up with a wonkier receptacle installation solution. I may need thicker furring strips.
There's no issue caused by screwing or nailing into the block wall, yes? And I don't need to apply anything to the block wall first? I'm less fond of adhesive.
Is any caulk suitable for sealing gaps, or is there a particular kind that is recommended?
Ryan,
Q. "Does having 2 stacked foil layers cause a problem?"
A. No.
Q. "There's no issue caused by screwing or nailing into the block wall, yes?"
A. Not as long as you use fasteners designed for concrete blocks.
Q. "I don't need to apply anything to the block wall first?"
A. No, as long as your block wall shows no evidence of water entry.
Q. "Is any caulk suitable for sealing gaps, or is there a particular kind that is recommended?"
A. Either polyurethane or silicone caulk would be better than latex painter's caulk. Seams between panels of foil-faced rigid foam are best sealed with foil tape.
If double layering the polyiso you can save a few bucks by using Thermax for only the exterior inch, which would keep the interior 2" on the sweet side of the derating curve for cheaper polyiso pretty much all the time.
The inch of polyiso + 2x4/R15 studwall is usually cheaper than a full 3" of virgin-stock foam and 1x furring with long masonry screws. For 3" foam + 1x furring the screws need to be longer than what the box stores carry. Routing the electrical and hanging electrical boxes is also easier in a framed wall. If going that route, put an inch of EPS (any density) under the bottom plate of the studwall, extending all the way to the foundation, so that neither the cut edge of the polyiso or bottom plate can wick ground moisture from the slab. That also keeps the bottom of the bottom plate closer to room temperature, and less likely to take on summertime moisture from the room air than when resting on a cool slab.
Notch the BOTTOM of each stud to allow routing the electrical on the bottom plate. That makes the batt-fitting easier and more perfect, avoiding the need to split the batts to accommodate wiring without creating voids or compressions.
If using reclaimed roofing polyiso the 3" foam + furring option may come in cheaper, but you're still stuck routing out cavities for electrical boxes, etc.
Thank you both for the comments.
Dana:
Great info, thanks. I will follow your advice and lay a 4.5" wide 1" layer of EPS against the slab adjacent to my block wall. How crazy do I go with caulk? Do I need to lay a full bead of caulk around the entire slab as I go laying EPS, and then another bead on top of the EPS before I lay the bottom plate. Then more caulk between every building material that butts up to another building material?
So looks like I will end up with a 5" wall. 1" polyISO (I'l try and track down the dow thermax for this). Then my 2x4 stud wall. Then in the stud cavities, is Roxul OK, or would it be that much better if I used 2" of cheaper PolyISO here.
If I've already caulked and taped the 1st 1" layer, is it necessary to continue doing that with subsequent layers? IE caulk around the polyISO I cut out for the stud cavities. Or has the air sealing requirement already been met at that point so any further would be redundant. (obv for roxul it wouldn't matter).
I assume I would still use pressure treated on my bottom plate or would it no longer matter over 1" of EPS. The stud wall I was planning regular wood.
Then I would either buy a kit, or have my foam contractor come in and spray 3" of closed cell around the band joist, and down to form a bond with the 1" dow thermax. Any thoughts on if this remains a fire hazard above my drop ceiling? Would I need to spray an intumescent coat over it before I install the drop ceiling?
Finally, I assume I should notch the bottom center or bottom towards the rear of each stud for the wires, not towards the front of the stud.
Martin:
Let's just say one year I am late clearing out the gutters a few years from now, and there is a heavy storm and surface water pouring out the side of the gutter builds up and dampness comes in through the block (not a steady water flow, just one nights heavy rain surface water dampness intrusion. Is it ok if the foam gets a little damp one day, and can dry out without long term problems? As long as I deal with the issue quickly and don't let it continue. Or if it gets exposed to moisture is the product ruined, not to mention creating mold spores. I mean I've inspected my block quite a bit after living here a few years, and I've done a slab moisture test, but I know problems can develop - it's part of why I'm afraid to spray closed cell against the block and inside the studs.
Thanks again!
Re this question "So looks like I will end up with a 5" wall. 1" polyISO (I'l try and track down the dow thermax for this). Then my 2x4 stud wall. Then in the stud cavities, is Roxul OK, or would it be that much better if I used 2" of cheaper PolyISO here." nevermind that question as you actually answered that by suggesting to route the electrical wires on the bottom to avoid splitting "batts". so either/or would be suitable. Either R-13 or an additional 2" of cheaper polyISO in the stud cavities. I'll prob go with whichever is cheaper, though the roxul seems like it would be easier to install and less messy than cutting the polyiso to size for each cavity.
Batts are definitely easier cavity fill than cut'n'cobbled foam board. With the thermal bridging of the framing the addtionional thermal performance afforded by the high R/inch foam is pretty small too:
https://www.greenbuildingadvisor.com/sites/default/files/images/Stud%20wall%20table%20for%202x4%20wall%20-%202.preview.jpg
https://www.greenbuildingadvisor.com/articles/dept/musings/installing-closed-cell-spray-foam-between-studs-waste
http://www.finehomebuilding.com/2017/07/10/closed-cell-foam-studs-waste
So I've tracked down a supplied of Dow Thermax and it's not too bad - about $18.75 per sheet in 1". They did have 2 models, one was about $1 more expensive, but the guy didn't know what the difference was (and I've forgotten the difference in model).
Just to confirm, it doesn't matter if it's faced or unfaced (that may have been the difference.... or it may have been white vs silver).
I'm planning to adhere it to my block wall with 4 vertical beads of Dow Enerfoam, and use Green Glue Sealant between all joints, and then seal the joints with the Dow Thermax Foil Tape.
Underneath against the slab I will have 1" thick, 4.5" wide strips of EPS, which will go under the Thermax and also the 2x4 stud wall.
Does the bottom plate need to be pressure treated since it will be resting on 1" of EPS? Do I need to use any more of the green glue sealant when laying down any of the stud framing, or drywall? Or is the sealing I am doing with the Dow Thermax layer all that is needed (there shouldn't be any air getting through.... or is it better to be thorough?)
I'm planning to use R-15 Roxul in the stud cavities, and notch the bottom for my wiring as was suggested. However, the R-15 I see in stores is actually 48" so I'd have to stack 2 batts. In this case does it matter if I just run the wire straight across at 48" so it nestles between the batts? Also, does it matter if the Roxul is faced or unfaced, particularly if the Dow Thermax will be either foil or white faced). You mentioned the cut edge of the Thermax being on the bottom against the EPS. But does it matter - can I put the factory edge against the EPS, and then the cut edge above? This way, the Lapolla 4G spray foam that I am installing against the band joist (3" minimum) and wrapping down to touch the Dow Thermax will cover it.
I will put 1/2" drywall on the stud wall then. And a drop ceiling. Just wondering if there are any fire hazards here? 1" dow thermax connecting with Lapolla 4G against the band joist. 1/2" drywall provides a barrier to the basement, but there wouldn't be much of a barrier above the drop ceiling - the thermax and Lapolla 4G will all be exposed to the air above the drop ceiling.
Lastly, I have done a moisture test on my block walls - using poly and tape. And passed. But what if there is ever any temporary water intrusion - perhaps due to gutter failure or something else. Assuming I catch it quickly. Is it a problem if moisture was to temporarily come in - not much, and not for a long time. Will it dry to the outside? Or will my wall assembly need to be pulled out and re-done in that portion? Remember I also have that black stuff on the exterior of my block wall. It would likely take a long time to even notice if something like that happened. I'd likely have to wait for evidence of staining, odor, or even water seeping out somewhere.
Thanks,
Ryan
Ryan,
Lots of questions.
Here's the basic principle: Finishing a basement is risky, because it's hard to be certain that you won't have water entry problems. Water entry ruins finishes. That's why lots of builders avoid basements. It's a strong argument in favor of putting all finished rooms above grade.
So, it you have decided to finish your basement, that means you've accepted the risk of water entry.
Before installing interior insulation on a basement wall, you want to do everything possible to convince yourself that you have solved all water entry problems. Only you know if you are being honest in your answers to that question.
Even if you've done your best to address water entry problems, there is still a risk.
Ryan,
Q. "Does the bottom plate need to be pressure treated since it will be resting on 1 inch of EPS?"
A. No, it doesn't have to be pressure-treated.
Q. "Do I need to use any more of the green glue sealant when laying down any of the stud framing, or drywall? Or is the sealing I am doing with the Dow Thermax layer all that is needed (there shouldn't be any air getting through.... or is it better to be thorough?)
A. You want to prevent warm interior air from contacting the cold concrete. That usually involves sealing the seams in the rigid foam, as well as the perimeter of the rigid foam at the base of the wall, the ends of the wall (right and left), and the top of the rigid foam near the floor joists. If you are aware of any cracks that allow interior air to contact cold concrete, seal the cracks with caulk or tape.
Ryan,
Q. "In this case does it matter if I just run the wire straight across at 48 inches so it nestles between the batts?"
A. You can do that if you want.
Q. "Does it matter if the Roxul is faced or unfaced?"
A. No, it doesn't matter.
Thanks Martin. Yes I always have tons of questions before doing a project.
Thermax always has facers, sometimes one of the facers is white rather than shiny-aluminum.
With an inch of EPS as a thermal and capillary break, the bottom plate of the studwall does not have to be pressure treated.
Can you even get rock wool with facers? Most or all rock wool batt goods sold in the US are unfaced, and that's fine. Batts with foil facers should be avoided. Paper facers are just putting more mold-food in your sub-grade wall, not great, but not a problem as long as there is no bulk water incursions. (Paper facers won't trap moisture the way foil facers can.)
Why Green Glue rather than foam board construction adhesive, a compatible polyurethane caulk, or can-foam? Are the solvents in Green Glue even compatible with polyiso? Butted up seams of foil faced polyiso are sealed well enough with any high quality foil tape with temperature rated adhesive, such as Nashua 324a (sold widely in box stores), or the Dow Thermax tape, of course, no goop in the butt joint required.
Most inspectors will give band-joist-only foam a pass on fire hazard, but if you put 3.5" of rock wool between the joist bays and (tight to the) spray foam it's that much safer.
It's fine to run the wires at 47-48" up from the bottom plate. You may want to still give the batt a shallow split to snug the wire into. The air-sealing obsessed will can-foam the wire penetration at each stud which doesn't take much time.
Thanks Dana.
I'm not sure about the rock wool facer, just wanted to be preemptive in case what I picked up had it - I will try for unfaced.
I chose Green Glue sealant because (I believe you) had mentioned using acoustical caulk for air sealing since it's flexible. Note that I wasn't planning to use their noiseproofing compound, but rather their sealant which is an acoustical caulk. I just read through their data sheets, but can't find anything about compatibility with PolyISO. I may have misunderstood where to use it. So the Dow tape is sufficient to air seal the Thermax boards together.
What about under the EPS? Was planning to use GG sealant there. Between the EPS and the Thermax? The only other really tricky spots are above the CMU pilasters. They're hollow, and the 2 length wise ones have beams resting on them. The others are just providing support to my block wall. I was thinking of filling in the tops of them in with a foam of some sort, maybe the Lapolla 4G, just to seal them off and connect them with the tops of the thermax and the band joist layer.
I think I originally intended to put the GG sealant around the drywall penetrations too, but then wondered what the point was if the thermax was already sealing the block wall from air exposure. The other place I intended the GG sealant for was for other areas of the house, to air seal from the attic between drywall joints, and around where stud bays meet drywall or sheathing...
I'd have no problem air sealing the stud penetrations - I presume I could just use something like a can of Great stuff. Again, I guess I just don't understand the point - if I've already air sealed the Thermax against the block wall, why would any further air sealing be beneficial? Happy to do it if there's a reason I don't understand what it'd be for yet.
I contacted both Green Glue and Dow to inquire about compatibility, and Green Glue responded first:
"Unfortunately the sealant likely won’t stick to the EPS so I do not recommend it for your application. I would suggest looking at another type of sealant- one that bonds with EPS should be the first criteria and it should flex over time to allow some joint movement. The EPS manufacturer might be able to point you in the right direction."
So whether or not it's compatible with the Dow Thermax, I'm not sure, but my plan also included using it between the EPS and the slab (and then the EPS and the Dow Thermax), and it won't work for that.
So.... I'm hoping to order all my materials today for this project and just wanted to confirm a few details.
Any suggestions on a product that's compatible with EPS and PolyISO? I'm having trouble finding answers on specifics there. Basically need something for under the EPS against the concrete. And then between the EPS and the PolyISO. everything else should be covered by the tape, and then closed cell foam up top. I'll foam up the penetrations in the stud wall for good measure.
With regard to great stuff, there are so many varieties - any reason to choose one of the specialty varieties over just the regular one, when sealing misc holes for air sealing?
Since I already bought the green glue sealant, I guess I can use it to seal my drywall seams? Again, I'm happy to do redundant sealing - just curious why further sealing would be beneficial beyond the initial sealing with the Dow Thermax against the block wall. Is it just because any sealing done is not likely to be perfect, so basically just for redundancy?
Thanks
Ryan,
Q. "Any suggestions on a product that's compatible with EPS and polyiso?"
A. Most lumberyards and hardware stores have tubes of caulk labeled "compatible with rigid foam."
Q. "With regard to Great Stuff, there are so many varieties - any reason to choose one of the specialty varieties over just the regular one, when sealing misc holes for air sealing?"
A. No.
Q. "Since I already bought the green glue sealant, I guess I can use it to seal my drywall seams?"
A. Drywall seams are sealed with paper tape and drywall compound (mud).
I'm having a lot of trouble with my local lumber yard and suppliers actually making any valuable suggestions. After many phone calls tracking down some Dow Thermax, it turns out what they ordered was initially RMax, then Dow Blue board, and then Dow Tuff-R. At this point, I'm considering the Dow Tuff-R. They've informed me that it performs identically to Thermax with exception of the fire barrier (which I don't need because I was going to use drywall. However, I had decided in my utility closets I would leave the Thermax exposed, so I'd have to re-think that....
My biggest question here is if Tuff-R is identical to Thermax for my application other than the fire barrier?
I also decided to order some Dow Enerfoam online which looks like it will work for EPS and PolyISO.
I realize drywall seams are sealed with paper and mud - but I always read how drywall joints need to be seealed because they are major sources of air loss. For example from above in an attic. Is this because of poor mudding? I had presumed that the mudding was not enough to prevent air flow through small holes. I'm a little confused about the best methods to air seal, then. Perhaps there is an article that I've missed?
Thank you.
Ryan,
Tuff-R is simply a brand of polyisocyanurate. All brands of polyiso perform similarly.
Thermax is also polyiso, but (as you evidently know) it is formulated differently, to pass fire safety tests. As long as you are covering the polyiso with drywall, any brand of polyiso is fine.
If you tape the seams of drywall with paper tape and mud, the seam is airtight. The reason that energy experts tell homeowners to crawl into their attic and caulk the gap between partition drywall and partition top plates has nothing to do with whether paper tape is airtight. The reason you caulk that crack is to prevent the air between the partition studs from rising into your attic.
OK, I thought Thermax was also formulated in a way (so they claim) which doesn't have as steep a drop in R-value as the temperatures drop. And I was wondering if Tuff-R had this same property, as their literature seems to suggest (minus the thermal barrier).
Ryan,
I have never seen any evidence that the Thermax behaves differently at cold temperatures than other brands of polyiso.
According to Dow's marketing fluff, they claim to have beaten the polyiso derating game:
http://msdssearch.dow.com/PublishedLiteratureDOWCOM/dh_098a/0901b8038098a015.pdf?filepath=styrofoam/pdfs/noreg/179-00263.pdf&fromPage=GetDoc
Dana,
Thanks for the link. The information sounds credible.
My guess is that they are using a Solstice LBA/pentane blend.
According to that link, it seems to only apply to their Thermax brand, not Tuff-R. I will try and call Dow tomorrow for confirmation.
Delivery came today including the 1" EPS - I'd asked for unfaced, but one side has foil and the other side has some kind of clear plastic. Wanted to ask which side should be against the slab, and which should have the PolyISO and the non-pressure treated 2x4 bottom plate on top of it? I'm using Dow Enerfoam adhesive sealant between both surfaces.
Thanks.
Ryan,
Unless one side of the rigid foam will face an air space, it makes no difference which way it is oriented. If one side is facing an air space, that's the side where you want to put the foil facing.
OK, thanks. No there's won't be an airspace.
I've acquired all the materials for this project. The Thermax I received is foil faced on both sides. It's actually a little more beat up than I was expecting. Wanted to see if there was any benefit to taping over any nicks in the foil face on either the concrete side or the roxul side?
It occurred to me that I am putting PolyISO (albeit foil faced) against a below grade concrete wall. However, I have a 1" layer of EPS between the cut edge and the slab. Just want to make sure I'm not exposing the PolyISO to any moisture issues via nicks in the foil.
Further, if the edges are a little beat up (not a lot), is the tape (I have the 3" wide thermax tape) going to be sufficient or should I perhaps spray some of the enerfoam I am using to adhere the boards to the concrete walls in between the pieces first? (laying each board in a vertical orientation, with 4 vertical lines of enerfoam along each board to adhere it - then framing a 2x4 wall (also on the EPS), which I will fill with R-15 unfaced roxul, then 1/2" drywall.
One other thing - I read an article on here recently which discussed using 2" EPS on top of the slab in the entire basement (followed by 2 alternating orientation layers of 1/2" plywood for subflooring, followed by a finished flooring. I simply don't have space for something like this. Am I making a big mistake by not at least laying 1/2" EPS, or even 1/4" fan fold XPS along my entire floor? I am struggling with headroom as is, so hoping just the 4.5" strip of EPS along the perimeter wall under the Thermax and the 2x4 stud wall is sufficient. Might mortar tile directly to my slab for flooring - or do an epoxy finish, perhaps with some throw rugs.
Cheers
I'd love if anyone had any comments with regard to the above. Thanks!
Don't sweat the nicks in the polyiso unless they're really huge, and going to be in direct contact with the concrete. It takes direct contact for moisture to wick into the polyiso- even a 1/16" gap is a capillary break. If you're concerned, tape over it with a high quality aluminum tape (the same stuff you should be taping the seams with.)
In zone 5 the deep subsoil temps are typically in the low 50s, and in zone 5A the outdoor summertime dew point temperatures are in the mid to high 60s. Any amount of R you can put under a moisture-susceptible finish floor would be worthwhile, even if it's only 3/8" fan-fold or half-inch EPS. But if it's going to be ceramic tile, no-subfloor, and there won't be any thick throw-rugs, it matters a lot less.
Thanks Dana, this is exactly what I was looking for.
I was likely planning ceramic tile mortared directly to the slab in the living areas, and a cedar plank type floor in the sauna. And either bare concrete, vinyl tile, or epoxy in the utility areas.
I was considering a throw rug over the tile in one of the living areas. I'd consider a fan fold or even 1/2" EPS, but then how much underlayment would I need additionally as a tile base? Would just 1/4" durock over 1/4" fanfold (or 3/8?) or 1/2" EPS be acceptable for tile?
Ryan,
If using tile, consider first installing an isolation membrane. It is low-cost insurance against cracks.
Ah gotcha, I can see how that would be beneficial - does it float over the slab or get adhered to it in some way? Likewise if I used fanfold or 1/2" EPS over the slab, wouldn't that act as an isolation barrier in a sense? In that case though, I'd assume I'd need either 1/4" durock - or perhaps that orange stuff, though it's more expensive.
Ryan,
For the same type of useful expert advice on tile underlayment you would expect to get about high performance building at GBA, I'd take your question to:
http://www.johnbridge.com/vbulletin/index.php
Awesome thanks for the additional resource.
I would like to ask the fine users here - if I was to put 1/2" or 3/8" fanfold EPS on my basement floor over the concrete, then what would be my flooring options, and what would I need to lay over the EPS? Note that the bottom of my joists are only 84" from the concrete. And I was considering a small drop ceiling (2" to 3", to conceal wires and pipes. Alternatively if I drywall, I'd still need to drop it down a bit for wire chase and pipes. Either way, there's not much room to work with.
It's region 5, below grade, in 18301. And I've got 1" continuous barrier of thermax on the walls. in some places 3". And where there's not an extra 2", I have a 2x4 wall in front with R-15 Roxul. 3" of closed cell foam above it in the band joist. So I am looking to see what I should do with my floor if anything, and what my ideal flooring options are.
I'm considering ceramic tile, vinyl tile, cork, epoxy, throw rugs, etc. There will also be different rooms which would call for different floor types. Utility rooms likely either vinyl or epoxy. A wine cellar likely tile or some kind of wood. Sauna area would have cedar planks over either epoxy or the bare concrete. Bathroom and laundry rooms probably tile. Theater/bar area I would like tile, wood or cork, and some throw rugs. Etc.
Mainly trying to figure if it's worth trying to get a thin layer of 1/2" or 3/8" EPS over the entire basement slab and interconnecting varying floors on top. Or if it's unnecessary and not worth the lost headroom. I can't quite visualize how I would be able to finish the floor over top of it while maintaining a low overall profile.
Thanks.
Nice to see a fellow sauna (sow na) - if that doesnt make sense I take it back - fan. You fin? Me too.
I wouldnt worry or mess with it.
Floating cork-backed floor with rugs will work great if its dry, lvt with rugs works great if you dont quite trust your dampness potential. Tile will transmit all the cold your floor gives you.
Ill put carpet in a new poured basement all day long but would never trust carpet in a block basement without a perimeter drain catch system to a sump and zero indication of damp conditions.
Swede on my mom's side (last name Carlson actually). The coldness is what worries me about the tile, which is why I thought to put throw rugs in spots. Don't care as much in the laundry room, or even in the bathroom as I would like to be able to get them wet. Maybe in the bathroom I would put some kind of electric radiant warmers under the tile to have as an option.
I put a perimeter drain in my old house, but this one is much bigger and it would just be too much work I think. I haven't seen any moisture get in in the 3-4 years I've been here. The only times there's been any moisture on the block at all even is when I neglected to clean out the gutters and the water poured over the edge. I need to install one of those gutter systems to make it easier but haven't found one I like.
Ryan,
Only you can make the judgment call concerning the trade-offs. More R-value is better -- the only downside is the lower ceiling height. We don't know how tall you are.
When rugs or carpeting are installed on a basement slab that is poorly insulated, these floor coverings can lead to mold growth or musty odors.