Poly under slab and over sill ?

We are building a super tight insulated house (passive inspired). My Q is does the 10 mil poly that we will put under the slab have to run up the interior basement walls and over the sill. Our house has a full basement, the concrete exterior has been waterproofed, insulated and back filled. Our sill seal will be acoustical sealant, EPDM gasket and PT sill. I understand the poly is a vapor barrier and the concrete is the air barrier. I have had a hard time finding info on the web about full basement as opposed to slabs. I was planning on taping the poly to the basement walls 1-2 feet above the slab but now am second guessing whether I need it over the sill. I understand concrete wicks moisture so it might for the cost just make sense to run it up over the sill to isolate the concrete completely. Thoughts ? Thanks so much !
GBA Detail Library
A collection of one thousand construction details organized by climate and house part
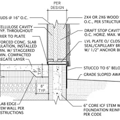
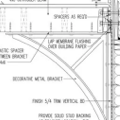
Replies
Where is the thermal boundary? Is your foundation insulated to the exterior, interior, or are you insulating the floor? If it's the walls then how are you insulating them?
What is the extent of the waterproof treatment? Does it extend above grade? Is there a capillary break between the footing and wall?
The devil is in the water management details and without knowing what's been done it'll be tough to recommend what to do. Returning the poly completely up the wall is not typical and in conjunction with what I assume is asphalt foundation coating on the exterior could be detrimental to the foundation curing.
Matt,
Asphalt coatings have been used for many years in the northeast region. I do not recall ever hearing that this "damp proofing" process has harmed any foundation. If you have any documentation you could share to support this I'd be interested in seeing this. What is known to harm foundations is water, freeze thaw conditions and or a poor concrete mix combined.
I'm assuming J Smith is using a waterproofing material based on her comment. I am surprised 10 mil is what your using under your slab when there are proven 20+ mil membranes which are far more puncture resistant and some have gas phase control. Typically the thinner membrane is used on the walls. Typically a double faced tape designed to hold your membrane in combination with a polyurethane caulk and mechanical fasteners are used to lock the membrane to the foundation walls.
On another note, considering how tight your planning your home do not forget the passive radon system in your design.
If your truly interested in waterproofing and membrane materials may I recommend to you to contact PROSOCO... http://www.prosoco.com/
Paul Grahovac, LEED AP
Technical Leader
Building Envelope Group
R-GUARD Air & Water Barriers
PROSOCO, Inc.
3741 Greenway Circle
Lawrence, Kansas 66046
(785) 830-7355
(888) 376-3417 fax
[email protected]
Here's a good resource for green design published by the EPA...
http://www.epa.gov/region1/greenbuildings/residential/pdfs/guide08.pdf
Jocelyn, I'm very curious what answers show up here because this is a detail I've also been thinking about for a while now. Several conditioned crawlspace plans show the floor poly run continuously up the concrete stem wall before interior insulation is installed. If this was applied to new construction, and the under slab poly was continued up and over the top of the concrete wall before the floor is framed, then this poly could be later sealed to the exterior sheathing to form a darn-tight air barrier connection, and complete vapor separation from the concrete foundation walls. I'm not sure if there are any disadvantages, but I look forward to reading others' thoughts.
Richard,
I was queasy writing that sentence and you proved me right to worry. It was just my neurotic nature coming through. My concern is that applying impermeable coatings to three sides (possibly four) of a concrete wall before it has fully cured could theoretically lock in an undesirable moisture content. But I'm a little out of my depth and just encouraging Jocelyn to proceed with some caution as she's making decisions on important details during construction and not before.
Is concrete harmed by being excessively moist? My understanding is that it is not. It does fine underground and underwater all the time.
delete.
Jocelyn,
Q. "Does the 10 mil poly that we will put under the slab have to run up the interior basement walls and over the sill?"
A. No. For more information on insulating basement walls, see How to Insulate a Basement Wall.
Matthew,
Q. "My concern is that applying impermeable coatings to three sides (possibly four) of a concrete wall before it has fully cured could theoretically lock in an undesirable moisture content."
A. It's good for new concrete to stay damp or wet for as long as possible. Slow curing is better than fast curing, and concrete continues to gain strength as it cures, for at least a year. There is no downside to keeping concrete damp. Concrete can stay damp or wet for a century or more.
Matthew,
My comment was not intended to be interpreted as though "water" through normal use is harmful to concrete. Issues arise when water is not managed, poorly mixed (to much water added to mix), improperly reinforced for it's intended purpose.
The link below may help with a better understanding of water management.
http://www.extension.umn.edu/Environment/housing-technology/moisture-management/moisture-in-basements-causes-and-solutions/
I also concur with Martins statement.
"It's good for new concrete to stay damp or wet for as long as possible. Slow curing is better than fast curing, and concrete continues to gain strength as it cures, for at least a year. There is no downside to keeping concrete damp. Concrete can stay damp or wet for a century or more."
OK ! Thanks for all the feedback. Martin if I understand it correctly I should NOT run the vapor barrier up and over the sill bc I have insulation on the exterior and interior-this could lead to mold problems. Should I just tape the poly up the wall a bit from the slab ? For the sill detail we plan a line of acoustical sealant, then the EPDM rubber gasket, then the PT sill plate. Is this ok ? I see in so many images of passive houses built on slabs that poly run up and over the sill edge completely isolating (vapor wise) the concrete from the house. Like this video http://www.finehomebuilding.com/design/articles/passive-house-build-part-two-air-sealed-mudsill-assembly.aspx I don't see anywhere where the sill sits directly on the concrete with sealant and gasket in between. Should there be more of a separation ? THANKS !
Jocelyn,
You can terminate the polyethylene at the bottom of the concrete wall if you want. You can also run the poly all the way up to the top of the wall if you want -- although that is unnecessary. Either way works -- the concrete doesn't care. The concrete doesn't have to "breathe."
The important thing is to insulate the concrete wall with an adequate thickness of rigid foam or closed-cell spray foam.
You always need to have a capillary break between the top of your concrete wall and your pressure-treated mudsill. Most people use foam sill seal (a type of gasket) at this location. Sill seal is a good capillary break, but it isn't always airtight -- so it's good to supplement this sill seal with caulk or Tremco acoustical sealant.
An EPDM gasket is another excellent type of capillary break at this location.