Need advice for insulating an attic and crawl space of an addition in Region 5 and using area for storage

Live in the region 5, Poconos / northeast Pennsylvania. There was an addition put on my 1968 cape cod style house, with a sunken living room with a fireplace, over a crawl space that is adjacent and accessible from my full basement. Then there’s a 2 car garage next to that, on a slab. There is a pulldown staircase in the garage, and then there is a fairly large vented attic that run over both the garage and the sunken living room. With the fireplace chimney coming up between the 2.
I’m looking to convert this attic into a long term storage area and want advise on the best approach to insulate and convert this into a storage area. Also want to encapsulate and insulate the crawl space and use this for storage as well. And want to keep the garage clear so we can park our cars in there, and will have shelving and a work bench around the perimeter for various tools and dirty projects. I want to eliminate risk of CO and other gases infiltrating the home.
I’m ready to tackle this project myself. Let me know what else you need to know about the area and I’ll provide the requested info. Presently there is R-19 fiberglass batting above both the living room and the garage. I can either leave this or remove it, I don’t really care. Whatever is best.
GBA Detail Library
A collection of one thousand construction details organized by climate and house part
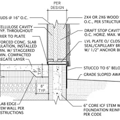
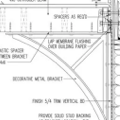
Replies
Ryan,
You haven't asked any specific questions yet.
Here is a link to an article on crawl spaces: Building an Unvented Crawl Space.
Here is a link to an article that explains the first steps needed for addressing attics: Air Sealing an Attic.
Here is a link to an article about the most common types of attic insulation: Blown-In or Loose-Fill Insulation.
Martin,
I read the 3 articles. Here are some specific questions.
For the crawl space, I'll be leaning towards 3" of closed cell spray foam on the 3 exterior walls (including the one against the attached garage slab). The wall adjacent to the full basement I assume only needs 6" or so to attach the poly barrier to the wall? Your article mentions bringing the poly up to 3" below the top of the walls, but if using closed cell spray on the walls, it isn't necessary to go this high, correct? Just 6" or so up the wall, enough for the spray foam to adhere and hold it in place.
Presently there is a hatch opening between the full basement and the crawl space. Does this provide sufficient air exchange for the crawl space? Or would I still need to add a passive vent up to the living room above? I don't have any HVAC system presently. Using a coal stove for heat, and the house has an attic fan combined with opening basement or 1st floor windows for cooling. However this summer I disconnected that and just put in a few window A/C units. So not sure how I can meet any air exchange recommendations.
With regard to the attic, would a blow in product be advisable, if I am going to cover it with a subfloor for storage? My understanding was that it would compress over time, and so I hadn't really considered using it. However, the fact that it fills in nooks and crannies is certainly a benefit over fiberglass batts. Would it be advisable to use a type of rigid foam board over the existing joists and leave the fiberglass in there? And then install subflooring over the rigid foam board? I'm looking for something I can do myself that ideally doesn't require the rental of a large machine.
There's not really any penetrations in the ceiling of the living room addition. However there are wood beams that I believe are more decorative than real, and the drywall is installed between them. And there is also some crown molding in all the edges which I'm not sure how well sealed the drywall is behind it. But other than that there are no penetrations in the ceiling itself.
Ryan,
Q. "If using closed cell spray on the walls, it isn't necessary to go this high, correct? Just 6 in. or so up the wall, enough for the spray foam to adhere and hold it in place?"
A. Yes, that's right.
Q. "Presently there is a hatch opening between the full basement and the crawl space. Does this provide sufficient air exchange for the crawl space?"
A. It's hard to say. I would advise you to install a hygrometer and monitor the crawl space RH and see what happens.
Q. "With regard to the attic, would a blow-in product be advisable, if I am going to cover it with a subfloor for storage?"
A. Your subfloor needs to be installed on framing (joists). If your existing joists aren't deep enough to hold as much insulation as you want, you can add additional joists above the existing joists (usually at 90 degrees to the existing joists). However, before doing this, check with an engineer to make sure that your joists are properly sized for storage. You may need an engineer to specify the size of the needed joists and how they should be installed.
Once you have the right cavity depth, you can blow in insulation on top of the existing insulation, followed by a plywood subfloor.
I guess the idea that was proposed to me of laying 4" of rigid foam board on the joists and then OSB over that is not advisable? I was told that XPS is rigid enough to support.
Alternatively I could lay new joists perpendicular to the old ones. Would it be that much better to blow cellulose in then it would to lay R30 batts perpendicular in these joists? It would save me from having to hire someone or renting a cellulose blowing machine.
It may be tough to bring an engineer on site to ask that question. My father in law is a commercial construction foreman, maybe I can just ask his opinion. Are there any sources or guidelines I can use to establish how much weight a particular load bearing assembly can hold?
Does it matter why type of subfloor I use? OSB or Plywood? 1/2", 5/8", etc?
Thanks.
Ryan,
Q. "I guess the idea that was proposed to me of laying 4 inches of rigid foam board on the joists and then OSB over that is not advisable?"
A. You are correct. It is not advisable, because the top of the joists will dig into the rigid foam. Your idea would only work if you first installed plywood or OSB on top of the joists, followed by a layer of rigid foam and then another layer of plywood or OSB. That's an expensive and labor-intensive way to proceed.
Q. "Would it be that much better to blow cellulose in then it would to lay R-30 batts perpendicular in these joists?"
A. Yes, the blown-in cellulose would almost always perform better than fiberglass batts. But if you really want to avoid renting a cellulose blower, you could install batts instead.
Q. "Are there any sources or guidelines I can use to establish how much weight a particular load bearing assembly can hold?"
A. For a rule-of-thumb approach (rather than an engineered approach), you can use span tables. (For example, here is a link to a simplified span table.) Caveat: this simplified span table ignores differences arising from wood species and lumber grade, so it's not a foolproof approach. But it will give you information on whether your joists are wildly undersized or in the ballpark of reasonable. The span table shows, for example, that 2x6 joists spaced 16 inches on center should span no more than 9'10".
Q. "Does it matter why type of subfloor I use? OSB or Plywood? 1/2", 5/8", etc?"
A. Any one of those suggestions will work for attic storage.