Insulating Basement – Southern Part of Climate Zone 4

I live in Northwest Arkansas, Climate Zone 4 not far from the climate Zone 3 border. Most people don’t have basements around here, so no one seems to know what’s best for this climate.
We live on a very steep slope and converted our crawl space into a Walk Out basement (10 foot ceilings in basement). In the conversion, the guys did a wonderful job with wall that is mostly underground (upper part of slope). They put in french drains and treated the backside of the wall with tar like substance. I’ve had zero moisture in the basement, it’s actually very dry and comfortable, of course it’s only been about 4 years but we have had some major heavy rain in the area and still we have been perfectly dry.
Now I’m finishing the basement, I did not put foam board against the concrete walls because when we started we felt it was so dry we didn’t need to do that, this website now has me second guessing myself. I don’t want to take all my framing down now, so what do I do? I was going to put fiberglass bat insulation wrapped in plastic in the 2×4 wall cavities, will that be enough? Most people use those plastic wrapped fiberglass bats in their crawl spaces around here.
If that isn’t good enough, I have a few other options:
#1 option could be to fill the 2×4 cavity with foam board before putting the fiberglass bats after?
#2 spray foam the 2×4 cavities in the walls?
There is a natural small gap between the 2×4 walls and the concrete walls due to the concrete walls not being perfectly smooth. Yes, I did use Pressure Treated on my sill plate, not the other studs though.
Finally, what do I do with the concrete block wall that is on the low side of the hill (walk out part) that is not holding back dirt, can I treat that one differently than the wall that is exposed to the earth (underground)?
I know, a lot of questions…I appreciate everyones advice!
Pierre
GBA Detail Library
A collection of one thousand construction details organized by climate and house part
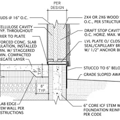
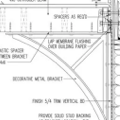
Replies
Pierre,
Building codes require basement walls in your climate zone to be insulated with a minimum of R-10 continuous insulation or a minimum of R-13 insulation if the insulation is installed between studs.
Now that you have installed stud walls, you can't easily install continuous rigid foam. So your only real option (assuming you don't want to dismantle the framed walls) is to use closed-cell spray foam.
Using fiberglass batts would be a bad idea.
Here is a link to an article with more information: How to Insulate a Basement Wall.
The amount of moisture wicking up from the footing into the foundation walls will vary, and it's always obvious.
Whatever you do, installing plastic on the interior side would be a real mistake, since it traps the studs on the groundwater-moisture side of the vapor barrier.
The relative risk with fiberglass really depends, in your climate. There is the potential for wintertime condensation events on the above grade portion, but the concrete can take it, and if there is reasonable drying paths to the interior the risk could be pretty low. But the fiberglass will also wick moisture from a damp foundation out to the wallboard. Even a half inch of foam can do a lot to mitigate both ground moisture and wintertime condensation moisture issues.
Current IRC 2015 code min for zones 3 & 4 is R13 + R5 continuous insulation for above-grade framed walls, which would still be a reasonable to apply even below grade, yielding generous dew point margins.
https://up.codes/viewer/utah/irc-2015/chapter/11/re-energy-efficiency#N1102.1.2
1.5" of EPS or 1" of polyisocynurate would be the best bet. A layer of 1" XPS would meet the letter of code, but it loses performance over time, eventually falling to about R4.2 after several decades as it's climate damaging HFC blowing agents dissipate out.
Thanks Martin & Dana!!
Martin, if you are recommending Spray Foam, will that protect my wood 2x4 regular pine walls from mold, my bottom plate is pressure treated? Again, my basement is a walkout on one side, so do I have to spray foam the concrete block walls that are not underground?
Dana, I wasn't going to install plastic, I was just going to use the insulation that comes lined in plastic by JM. It is supposed to protect the fiberglass insulation from collecting moisture. People often use it in crawl spaces in this area. The ends of the bats are actually not sealed in plastic so air still circulates throughout the bats so it's not a vapor barrier. I could cut a piece of foam board and place it on top the pressure treated bottom plate to prevent it from wicking up the fiberglass bats?
Your thoughts?
Pierre,
Q. "If you are recommending spray foam, will that protect my wood 2x4 regular pine walls from mold?"
A. Probably, as long as your foundation isn't plagued by water entry, and as long as the interior air isn't unusually humid.
Q. "Do I have to spray foam the concrete block walls that are not underground?"
A. All of your exterior walls need to be insulated. That's a code requirement. Because concrete block walls can wick moisture, and can also get damp from the exterior, using closed-cell spray foam for these walls is a better choice than fiberglass batts.
Q. "I was just going to use the insulation that comes lined in plastic by JM. It is supposed to protect the fiberglass insulation from collecting moisture. People often use it in crawl spaces in this area. The ends of the bats are actually not sealed in plastic so air still circulates throughout the batts so it's not a vapor barrier."
A. I don't advise the use of these batts. They can trap moisture between your concrete block walls and the insulation. When you are insulating a below-grade room, you usually don't want any polyethylene in your wall assembly. Nor do you want any fiberglass batts in your wall assembly.
Ok, you've convinced me, I will be doing closed cell spray foam on the walls. I have one final question, I found a local company that uses Icynene foam. Do you have an opinion on that type, will that be good for my application? Thanks again for all your great advice.
Pierre,
For years, Icynene only sold open-cell spray foam -- so for many contractors, "Icynene" is shorthand for "open-cell spray foam."
These days, Icynene also offers closed-cell spray foam. Just make sure that you're getting the right product before you agree with your contractor's plan.
Thanks Martin! When the sales person came over we spoke about open and closed cell Icynene, but he was very clear that he would be using closed cell in my installation. After he left I was doing some research on reviews of Icynene, and most talked about it being open cell, so that's why I asked your opinion. The other thing I found, is that Icynene is made of isocyanates, a petrochemical...I was wondering how safe that could be long term. Is there another spray foam chemical/compound that may pose less risk after installation or that you prefer?
Icynene's 2lb density closed cell foam (MD-C-200)is blown with HFC245fa, a powerful greenhouse gas. Icynene has two "semi-open" 2lb foams (MD-R-200, and MD-R-210) blown with water that would be appropriate here. Both run about R5/inch (compared to R6.6/inch for the HFC blown version) so you'd need a full 2" to hit a code-min R10 continuous, not 1.5" with the HFC blown foam.
At 2" the MD-R-200 would ~2 perms, MD-R-210 would run ~0.8 perms. Either would be fine in this application at 2", but if going for an R13+ R5c.i. the more vapor-tight MDR-210 would be preferred.
http://www.jsjfoaminsulation.co.uk/docs/ICYNENE-MD-R-200-Specification-Sheets.pdf
https://www.icynene.com/sites/default/files/downloads/ProSeal%20Eco%20MD-R-210%20Technical%20Data%20Sheet_August%202013.pdf
All polyurethane and polyisocyanurate foams are made with iscyanates. If the mixture & temperatures and substrate temperatures are within spec during installation the health risks are very low. Most foam blowing equipment has reasonably precise mixture and temperature controls (adjustable by the installer), so it's really up to the competence of the installer. Get references.
Ok Martin, I'm down to 3 different installers in the area, here are their products as closed cell options...
Heatlok XT vs Profoam 11-033 vs ProSeal (MD-C-200v3)
My wife is really, really, really worried about these chemicals being introduced to our house. Of course she's seen some horror stories in spray foam installations on the internet, and is worried. So is there a preference in terms of quality and the low risk to chemicals/VOC in the house. We do have very young kids. We would definitely leave the house for at least 24 hours (maybe 48) while they apply the product and we let the house 'air' out. So which would you lean towards?
As you mentioned, the installer is very, very important and when it comes to that side of the decision, I think by far the Heatlok installer would be the most 'professional' of the three, they only do Spray Foam (no drywall, gutters, etc) and have been doing it for 23 years and do ~25 jobs/week and do installations for most of the big builders in the area.
Although, he did disagree with your recommendation, he said in this area he almost exclusively installs open cell (Demilec Selection 500) even in basements for multimillion $ homes. Having said that, he said he has no issues doing whatever product we want, but is surprised in my situation that I need closed cell.
So what are your thoughts??
Pierre
I was reading more about spray foam and found a quote on page #2 of this article:
http://www.ecobuildingpulse.com/products/product-review-spray-foam-insulation_o?o=1
"Because of the open cell structure, open-cell foam allows some vapor to pass through, making it a good choice in hot, humid climates, and under roof sheathing, such as in conditioned attics, where water vapor caught between insulation and sheathing could promote wood rot."
We have very high humidity where we live, it's probably 4 solid months in the summer. And even in the winter we have a very damp cold, that goes right through your clothes, so wouldn't this mean that open cell would be better in our area. Or is that only for the upper levels of the house and in the basement closed cell is still the way to go?
Pierre
Pierre,
The position expressed in the quote you share is ignorant. Yes, open-cell spray foam is vapor-permeable -- meaning it allows water vapor to pass through it. But that doesn't mean it's a better choice than closed-cell spray foam in your climate zone.
When insulating a basement wall, you certainly don't want water vapor to travel through the foam from the damp side of the wall (the exterior) to the dry side (the interior). That's why you want closed-cell spray foam in this location.
When installing spray foam on the interior side of roof sheathing, you don't want to allow interior humidity to travel through the foam and reach the roof sheathing. Open-cell spray foam in this location causes all kinds of problems. To learn more about this issue, see this article: High Humidity in Unvented Conditioned Attics.
To reassure you about the dangers of spray foam: The vast majority of spray foam jobs are completed without problems. If you choose an experienced contractor with a good reputation, you shouldn't have reason to worry.
Pierre,
I see your preferred installer reps Demilec and I was wondering if he discussed their HFO product? It uses Solstice as the blowing agent, so very low GWP. While not relevant to your situation, it can also be applied in a 6.5" lift, so they claim you can get an R-49 in a single lift.
As always thanks Martin! He never mentioned the HFO version, just the XT version. My guess is they haven't used that product since he didn't mention it. Should I try to get him to install that version even though he probably doesn't have experience with it? And, based on your comments, are you suggesting I should go with the Demilec installer/brand versus the other installer/brands?
He actually responded to me this morning...btw, I referenced you as the Energy Consultant...
"We can get the HFO, but to be real honest you aren’t going to notice a nickel of difference on performance for the extra money you spend. I understand how energy consultants view r values, but both XT and HFO are a 2.17-2.2 density and will perform the same at 2” on your concrete walls. Again it’s more about proper installation and we have seen good adhesion and results with the XT. Always a difficult transition to new chemicals as you change the pattern, temperatures, pressure, etc.."
Your thoughts?
And thanks Jonathan Lawrence, oops just noticed that I wasn't just dealing with Martin anymore.
It's not about the ~R7/ inch compared to the ~R6.5/inch or whatever. The reason for going with an HFO blown foam has nothing to do with it's very marginal increase in performance, but quite a bit to do with the extremely high greenhouse potential of HFC245fa (~1000x CO2) compared to the very low global warming potential of HFO1234ze (<5x co2, for any variant of hfo 1234_ _ ).
It's highly likely that HFC245fa will be banned for this application within the next decade by international agreement in much the same way CFCs and HCFCs were taken out of foam applications by the Montreal Protocol. With any change in blowing agent there's a learning curve, but the manufacturers have been working it out for a handful of years, and it's now ready for prime time. It's not that difficult for the installers to read the manual and adjust the equipment accordingly, but some are just reluctant to move away from something that they have experience & comfort with and they know works, or to have to train the crew to set up the equipment differently, changing back & forth, etc.
It's easier for the contractors to "set and forget", adjust the equipment once, let the crews memorize the magic number, and just let the crews go at it with a cubic acre of foam before it has to be adjusted again. But it's neither rocket science nor is it time consuming to make the changes.
One true advantage of HFO blown foam for the installer is that it can be safely applied in lifts of 4" or greater, whereas most HFC blown foam is limited to about 2" before there are shrinkage and adhesion issues, even a fire hazard issue during curing. IIRC Demilec is claiming that you can install a full R49 (IRC code min for roofs in cooler climates) in one pass, which would take FOUR passes with HFC blown foam if doing it by the book. (Many will push the limits, and will install 3" or more a time, but there are quality and fire risks when they do that.) With HFO blown foam it's not a problem.
Pierre,
Glad to help. He really did miss the point of using the product, though. As Dana points out, a lot contractors like to"set and forget" so I am not necessarily surprised. I run into this issue all the time.
I did have chance to stop by the Demilec booth at ABX Boston last month and it was the first time I saw anyone marketing an HFO product. They did tell me that the cost of the raw material is slightly more expensive, but labor savings can easily offset that in applications that would normally require multiple lifts.
Thanks Dana, Johathan & Martin, I really do appreciate all the inputs!
I think it's imperative for the green building community to push for the rapid transition to HFO foam. We've been spraying LaPolla Foam-Lok 2000 4G for a couple years and really like it. I asked my lead foam tech at the time we switched, and he told me that the learning curve really wasn't all that steep--a conversation with our sales rep, a little tweaking of the reactors settings, and we were there. This biggest adjustment was getting used to laying down the thicker lifts, which in the long run saves time and increases yield.