Help with retrofitting Roxul ComfortBoard / ComfortBatt in existing structure

Hi,
I need help with my basement insulation project. I am very new at this kind of work so please be forgiving.
I started the project some time ago with the intention of using sray polyurethane foam on the concrete walls and the ceiling joists. So I built a 2 x 3 structure 1 inch away from the concrete wall and was looking to get a contractor to spray foam. But then I realized that the foam is not so green and that the EPA investigates its possible health effects, so I kept researching on the topic and I have to say that what I read scared the hell out of me. So I decided to ditch the PU option and look for something else. I found out about the combinaton of roxul comfortboard and comfortbatt which is the option I like the best for ecological and health concerns. My idea was to detach the walls from the floor and ceiling and to install comfortboard on the concrete, reattach the wall on the comfortboard and then put some comfortbatt between the studs. But comfortbatt are made for 2 x 4 not 2 x 3. So my question what is my best option:
– Replace 2 x 3 by 2 x 4 and do the work all over again? Maybe I could keep some of the 2 x 3 for my interior walls but I don’t have as much interior walls.
– Nail 2 x 1 on my 2 x 3 to make them 2 x 4? I guess this is not a good idea since the 1 x 2 may curve differently than the 2 x 3 and this will leave air gaps everywhere in the structure which I think is not a good idea?
– Use some other insulation technique? I don’t like the PU option because of the chemicals inside and the same goes for rigid foam and their fire retardants.
I live in Quebec, Canada so it’s a pretty cold climate and I am seeking an insulation with an R value of 14 or more.
Please help. Any suggestion is appreciated.
GBA Detail Library
A collection of one thousand construction details organized by climate and house part
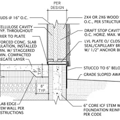
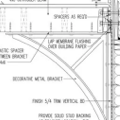
Replies
Guillaume Dumont,
Salut et bienvenu.
You don't want to use mineral wool insulation to insulate your basement wall, because mineral wool is air-permeable. It will allow warm, humid indoor air to contact the cold concrete, leading to condensation and possible mold.
Your choices are rigid foam (EPS, XPS, or polyiso) or spray polyurethane foam. More information here: How to Insulate a Basement Wall.
Thanks Martin,
I do understand that, but shouldn't a polyethylene film over the studs make a sufficient vapor-barrier as indicated in the DIY videos of roxul (see http://diywithroxul.com/en-ca/diy-videos/insulate-interior-foundation-basement-wall.html). The government energy efficiency website states that it is ok to insulate with fiberglass or mineral wool as long as it is covered by a vapor barrier (http://www.efficaciteenergetique.mrnf.gouv.qc.ca/en/my-home/helpful-advice/insulation/). Your GBA link says that I am better off with just the rigid foam.
This seems to be contradictory. Would you say that having a poly film works in theory but often fails in practice?
Guillaume,
You are correct that many online resources give bad advice on methods of insulating the interior of basement walls. This information dates back to methods used in the 1970s and 1980s, and these online resources haven't kept up with recent building science research.
I would ignore the video from Roxul. It's no surprise that the manufacturer of Roxul is promoting its products for a wide variety of purposes, even some that aren't a good idea.
L'autre document -- «Isolation des Fondations » -- décrit des méthodes anciennes. ("Lorsqu’on isole avec un isolant fibreux ou tout matériau susceptible d’absorber l’eau, on doit le protéger avec un «pare-eau». Cette première membrane (par exemple un polyéthylène ou un papier 15 lbs, posé avec du mastic) n’agit pas comme un pare-vapeur, mais prévient la migration de l’humidité qui se dégage du béton.") Ça ne marche pas.
The concrete is still cold, even if the concrete is covered with polyethylene or #15 asphalt felt. Moisture can condense on the cold surface, whether it is concrete or cold poly. Moreover, interior polyethylene on the interior side of the Roxul can never be airtight enough to prevent interior moisture from reaching cold surfaces. Interior poly just prevents the stud bays from drying out, ensuring the growth of mold.
Maritn,
Ok it makes more sense now. Thanks. If I were to remove the stud wall and install rigid foam on the concrete wall and then install back the stud wall over the foam, how would I attach the foam to the concrete. The method I know of involves using furring strips. I have seen in the post you linked to (How to insulate a basement wall) that I could use Hilti IDP fasteners. Does this work as well as furring strips for keeping the foam well fitted on the concrete with no air space? On the other hand, is it advisable to install a stud wall over furring strips to allow for easier electrical work?
Guillaume,
Q. "If I were to remove the stud wall and install rigid foam on the concrete wall, and then install back the stud wall over the foam, how would I attach the foam to the concrete?"
A. You can use foam-compatible adhesive or special fasteners. In addition to the Hilti IDP fasteners, you might consider using Plasti-Grip PMF fasteners from Rodenhouse. (You can read more about Plasti-Grip PMF fasteners here: New Green Building Products.)
Q. "I have seen in the post you linked to (How to insulate a basement wall) that I could use Hilti IDP fasteners. Does this work as well as furring strips for keeping the foam well fitted on the concrete with no air space?"
A. The furring strips should be attached with Tapcons or a similar concrete screw.
Q. "Is it advisable to install a stud wall over furring strips to allow for easier electrical work?"
A. It's certainly easier to run wiring in a 2x4 wall than in the gap created by furring strips.
Guillaume,
I can only second Martin's comments. With foundations, you really only have three options: closed cell spray foam, foam board properly installed and air sealed or no insulation at all! Do not use air permeable insulation. Period.
You do not detail your concerns about spray foam but if my experience is any guide, they probably center on out-gassing and/or lingering smells. I long since lost count of the number of basements we have insulated with spray foam and from time to time we have a client who shares your concerns before biting the bullet. To date, they have all been glad they used spray foam. Yes there is some initial odor but that is true of almost any new product you put in your house.
Before you tear down your walls and start over, I would suggest that you find a reputable and experienced foam installer in your area and talk to some of their clients with similar project. Ask for samples of their foam, both freshly sprayed and aged, then judge for yourself.
Good luck with your project.
Thanks for your input Torsten.
Initially it was health concerns that pulled me away from this option. I have read horror stories (the kind you find on the internet when you look deep enough) of families having to leave their homes because spray foam made them hypersensitive to chemicals. I know that this represents a very small proportion of all SPF installations but still I am not sure I can take the risk (I guess I have a very low risk propensity). From my readings I think that in most situations these problems were caused by wrong installation because people went for the cheapest installer instead of a reputable one as you suggest. But since I realized, from this discussion, that none of the available options are completely safe from health point of view, my concern towards SPF has turned into an economical one. I am still evaluating the costs, but the SPF option is much more expensive then the rigid foam one if done as a DIY even if it means tearing down my walls.
Thanks for your advice, maybe I'll try what you suggest.
If I may ask another question:
I have a furnace which was installed very close (the closest point is around 8 inch from the concrete) to basement concrete wall. Since all basement insulation are flammable and that the specification is that I should not have any combustible material within 24 inches of the furnace what are my options here? My first idea was not to put any insulation there but this might be to radical since there has been an inch thick foam board there for almost ten years and maybe more (the furnace was changed in 2003 but the previous one probably had a similar setup). And the foam did not appear to have suffered from heat.
Thanks again this website is such a valuable source of information.