Foam sheathing insulation on basement block walls

Building a new home in Syracuse NY. We will have two bedrooms in the finished basement (not walk out but large egress windows). I want to use foam sheathing on the concrete block walls – primarily as a vapor retarder but also for it’s insulating value. I have read differeing opinions on the ideal permeability rating for foam in this situation. BSC says to keep it permeable but I have read elsewhere (here maybe) to use impermeabile. I have my eye on 1″ XPS because Lowes has it in stock.
What do people recommend? Thanks
GBA Detail Library
A collection of one thousand construction details organized by climate and house part
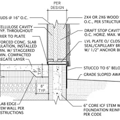
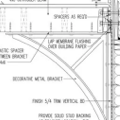
Replies
David,
Syracuse, New York is on the border between Climate Zone 5 and Climate Zone 6. In those climate zones, the 2012 IRC requires basement walls to be insulated to a minimum of R-15. To achieve R-15, you'll need at least 3 inches of XPS or polyiso, or about 4 inches of EPS.
So your idea of using 1 inch of XPS won't work.
Of these three types of rigid foam, polyiso and EPS are more environmentally friendly than XPS.
For more information on this issue, see How to Insulate a Basement Wall.
In your post, you mentioned that Building Science Corp. used to advise builders that interior rigid foam on basement walls needed to be vapor-permeable. Eventually, Joe Lstiburek admitted that he was wrong about that. To learn more about the history behind this piece of advice, since retracted, see Joe Lstiburek Discusses Basement Insulation and Vapor Retarders.
This reclaimer in Buffalo has 3" polyiso for $26, which is thick enough to hit R15 even when derated for climate.. .
https://syracuse.craigslist.org/mad/5837554222.html
see also:
https://albany.craigslist.org/search/sss?query=rigid+insulation
https://utica.craigslist.org/search/sss?query=rigid+insulation
The $26 price point is a bit more expensive than reclaimers in my area- it usually runs $15-20 here, but it's a competitive market with multiple reclaimers, but it's WAY cheaper than box-store XPS.
Strap it to the wall with 1x4 furring through-screwed to the wall (at least 24" o.c. or tighter), using 5" masonry screws. (You may have to order them online or find a hardware store that carries them, since the box stores typically only carry shorter TapCons.) The wallboard can be fastened to the furring. Keep the bottom edge off the slab to avoid wicking ground water or summertime moisture adsorbed into the slab from the air. A 1/2" gap is plenty.
This is exactly how I did my poured concrete foundation ~9 years ago, in a house where the footings are below the water table and the moisture content of the concrete is higher than average. When demolishing a portion to move some drain plumbing several years later (on the wettest side of the house) there were no indications of moisture issues. A CMU block wall with empty cores has less wicking potential than poured concrete, but if the cores were filled with concrete itt's comparable.
As long as you have at least a foot to 18" of unpainted above grade exposure on the foundation and reasonable surface drainage the moisture content of the foundation sills will be fine.
If you use an EPDM sill gasket between the top of the foundation & the sill and it will be fine, no matter how wet the CMU becomes.
If insulating on the exterior of the block wall, use reclaimed EPS/XPS (also dirt-cheap) and derate it to R4.2/inch for it's true long term performance after the blowing agents have all dissipated. Due to the thermal benefits of the CMU when it's inside the thermal boundary of the wall you can do fine with just 3" (R12.6, fully derated) , even though it's not quite R15 from a labeled performance point of view. (An R13 mass wall meets code even for above grade walls in zone 5 when half or more of the R is on the exterior. When it's below freezing outside even 3" of EPS will be performing better than R13.)
Thanks for the replies.
Martin - My plan is either to use the foam plus fiberglass. Or just foam in a sufficient thickness to meet code (or better).
DD - thanks for doing that leg work for me. I had no idea that there was a market for that stuff used.
There is some good detail information (like air sealing of basement foam) here.
I retrofitted a house near Syracuse 10 years ago. I put 2" of XPS on all basement walls. Some walls I just applied drywall directly through foam using tapcons. Some walls I furred out with wood studs and drywall, and some walls I filled stud cavity with fiberglass batts, typically where there was not backfill against wall. Half of the basement was below grade. I never had a moisture problem. Having studs gave me room to run power and data/coax.
In Oneonta there's is a foam reclaimer named Hickory Street Rentals. His name I said John. He advertises on Craig's List. He delivers in a large flatbed trailer for a small fee. I sourced 2.5 inch thick EPS sheets to do the whole outside of my house, plus a some nice 3 inch high impact XPS for under my covered porch slabs. He gets these off of the many many refrigerated warehouses and giant warehouse buildings that are torn down such as those on old military bases, old industrial parks and the like. I was very pleased with his business fairness and honesty. All the scrap pieces went either against the foundation under grade or up above my attached porch ceilings against the house wrap.
Thank you. I am going to let the builder use new materials in the finished portion of the basement and I will use reclaimed stuff in the (larger) unfinished section after we close.