Exterior foam wall assembly without interior polyethylene

I am building a Net Zero home in Edmonton, Alberta Canada and plan on using 6″ of EPS or XPS rigid foam on the exterior of a traditional 2×6 wall sheathed with OSB and filled with Roxul batts resulting in about an R-40 wall.
The building code here calls for polyethylene on the interior and a maximum 1/3 rule for insulation on the exterior however the recommendation on this site is at least 4″ of exterior rigid foam and no poly for a wall like this(I assume my climate zone is 6). How can I convince the city to accept my design and how can I ensure air tightness without poly?
Thank you.
GBA Detail Library
A collection of one thousand construction details organized by climate and house part
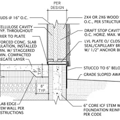
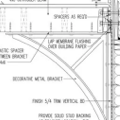
Replies
You are in climate zone 7.... like me (Kenora Ont)...
My building plans (4" exterior EPS with fiberglass batts in the 2 x 6 studs) were accepted by the city (of Kenora) with membrain instead of poly with an engineers stamp.
Sheffie,
It might be worth looking at the relevant sections of you code again before settling on a wall assembly. Unless Alberta has recently modified the NBC, the code doesn't call for poly on the interior and I haven't seen a 1/3rd exterior insulation rule.
The building code does want the wall to contain a vapour barrier, but that can be a variety of materials, and can be located anywhere in the wall as long as it is designed not to encourage condensation.
The best way to convince your building inspector is probably to show them what the code actually calls for.
Here is a link to another thread addressing this problem:
https://www.greenbuildingadvisor.com/community/forum/building-code-questions/59781/poly-and-canadian-building-codes
> a maximum 1/3 rule for insulation on the exterior
Are you sure this isn't "minimum"? Maximum makes no sense - even 100% exterior foam is a reasonable design.
Tim, did you do a blower door test to determine air tightness? One of my goals is to be under 1 ACH, but not sure if it'll be achievable without poly.
Sheffie,
Hardly any of the projects published here on GBA which have exceeded 1 ACH have used an air-sealing strategy based on poly. The main strategies are using the sheathing layer, foam, air-tight drywall, or a combination of them.
Sheffie... I'm still building and haven't had a blower door test yet ... however I believe (like Malcolm has indicated) that poly is not a requirement for air tightness; rather attention to detail is...
Quote; The main strategies are using the sheathing layer, foam, air-tight drywall, or a combination of them.
Sheffie,
Malcolm Taylor is right: educated builders stopped using polyethylene as an air barrier back in the last 1980s. For more information, see these two articles:
Questions and Answers About Air Barriers
Airtight Wall and Roof Sheathing
Sheffie,
There are two issues here. One is whether the code requires poly (which it doesn't), the second whether using poly as an air or vapour barrier is a good idea. I'm a bit more equivocal about the latter than Martin.
In a climate with no cooling, where the insulation industry is set up to air-seal poly to a high standard and where the code requires a vapour barrier, it may still make sense from a practical point of view to use poly. A huge majority of the houses here in BC still do. The practice will no doubt slowly disappear, but in the meantime it works alright and does little harm.
However that pre-supposes conventional wall assemblies usually filled with batts. In your case the poly really does create a problem by limiting the drying potential of the wall and you should either alter your wall assembly so it can dry to the outside, or use a vapour-permeable interior membrane.
Malcolm,
It sounds like you and I are in agreement about whether Sheffie should use polyethylene on this wall assembly. Sheffie shouldn't.
About the larger issue -- whether the use of interior polyethylene in southern Canada still makes sense -- I'll just say that it's a complicated issue. We should note:
1. Even you note that the use of polyethylene should be limited to "a climate with no cooling." Those areas are moving north rapidly, as global warming advances and air conditioner sales increase.
2. In your province of B.C., the building industry suffered a catastrophic debacle called the "leaky condo crisis" -- a debacle that cause all kinds of repercussions, both political and economic. Most building scientists noted that most of the moisture that rotted these walls came from the exterior, and vented rainscreens (now required by code) have gone a long way to addressing this type of failure. But many experts also note that the use of interior polyethylene in BC contributed to the wet-wall crisis by limiting inward drying.
In a location as dry (as measured by dew point) as Edmonton there is effectively zero chance of inducing condensation on interior-side polyethylene even if the building is air conditioned, unless it's a walk-in refrigerator kept below 4C. The mean mid-summer outdoor dew point is about 10C for the most humid weeks 5 weeks of summer in Edmonton.
That's not to say that it's not good to have the capacity for drying toward the interior, only that it's not nearly as likely to create a problem as it is in more humid summertime climates such as the Ontario Riviera.
The 1/3-2/3 rule is that at least 2/3 of the R is on the exterior of the vapour barrier, which you would have, if you define the OSB sheathing as the vapour barrier. Dry 5/8" OSB has a vapor permeance low enough to meet the NBC definition of vapour barrier (= a permeance not greater than 60 ng/(Pa•s•m) when measured using ASTM E96, dry cup desiccant method.) see: http://osbguide.tecotested.com/pdfs/en/tb111.pdf
The 1/3-2/3 rule of thumb was never enshrined in code, but was used by some earlier mortgage financing requirements (back in the 1980s?) It sort-of works for most of Canada, but is not currently an explicit requirement anywhere that I'm aware of, but seems to have evolved into building lore. It shows up from time to time in NRCAN documentation as well, such as at the bottom of p19 (p11 in PDF pagination) of this bit o' fluff:
http://www.nrcan.gc.ca/sites/www.nrcan.gc.ca/files/energy/pdf/housing/Chapter2_e.pdf
But with R25+ foam insulation on the exterior of R23 Roxul even those who believe that lore is code should be satisfied.
Martin,
The issue is only complicated by convention, not building science. Currently buildings here are insulated and air sealed by the same subs, and the insulation and air-sealing is inspected at the same time prior to drywall. The end product is a fairly resilient and well sealed house - but I'm in no way arguing things shouldn't change, and alternatives take over. It's just that right now, taking into account the realities of the industry and approval process, it may not be a battle that is always worth fighting.
Thank you all for the feedback. I do not want to use poly and would rather use a product I'v seen used on a building by DuraBond, its an EIFS with a WRB product applied on the OSB (which is taped first) then the foam (which has drainage planes) is applied with a cement. The result looked great however I'm not sure how airtight it is, I'm assuming it would be if done right and had the foam layers staggered. That works great for the wall however how would the roof be done given I don't want a conditioned attic space? Ideally I can have the exterior and ceiling done then have a blower door test done to confirm air tightness before moving on to stud insulation, drywall etc.
Sheffie,
You're right that EIFS, properly installed, is a good system. Any system with a continuous layer of exterior rigid foam is an excellent approach, as long as the system includes good moisture-management details (and the EIFS industry has learned to provide those, after a few stumbles).
If you want to use a similar approach on your roof, you should read this article: How to Install Rigid Foam On Top of Roof Sheathing.
Martin, I read that article however I do not want a conditioned attic space, would I be able to use rigid foam on the ceiling for a thermal break then use blown cellulose in the roof like a traditional build?
I don't think there is value in using 10 or so inches of rigid foam when blown cellulose is so cheap here.
Sheffie,
There is no need for rigid foam or spray foam if you want a vented unconditioned attic. Just perform ordinary air sealing work on the attic floor (the top side of the ceiling) and install a deep layer of cellulose. For more information, see How to Insulate an Attic Floor.
In a location as cool as Edmonton, if you're going to skip the ceiling polyethylene it would be prudent to use air-tight ceiling gypsum, painted with a low-permeance "vapor barrier latex" primer. The air tightness is critical, lest you end up with frost/damp insulation along the exfiltration path, but vapor diffusion can count too, depending on just how well ventilated the attic is. (This is less of an issue in most US locations.)