Dealing with multiple WRBs and air barriers with external foam board

Building a home on the edge of zone 4 & 5 (in zone 5) with avg 60″ annual rainfall and minimal snow. CA building prices are crazy (~$275/sqft by avg contractor in area), and this is our final home so want to maximize durability and longevity in a reasonably buildable green home. The buildable area on the lot is small, so need a thin wall to get the needed square footage while allowing a garage. Planning 2″ PolyIso over 2×4 framing and 7/16 OSB, then 1×4 rainscreen and stucco for the walls. Taping the PolyIso will create a good air and WRB, but based on GBA advice, I’m hesistant to rely on that for the long term. Seems like using Zip for the OSB and creating the primary air and WRB at that layer would be the best insurance, but not sure if having a second air & WRB at the PolyIso level is likely to cause issues. I’ve seen Martin’s great advice on whether housewrap should go in or out with external foam, but looking for GBAs advice for the Zip system in combo with external foam.
GBA Detail Library
A collection of one thousand construction details organized by climate and house part
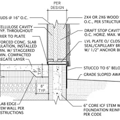
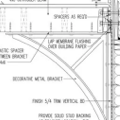
Replies
Mitchell,
Zip System plus exterior rigid foam works fine, with or without an additional layer of housewrap.
Huber has come out with a product that integrates Zip sheathing with a layer of polyiso. It's called Zip R sheathing, and it is available in a variety of thicknesses. Here is a relevant link: Zip System R sheathing.
In addition, you may want to read a GBA article on this type of sheathing: Nailbase Panels for Walls.
Check with local codes regarding seismic requirements before diving in.
Fatter grades of ZIP-R probably won't meet seismic code requirements in N. CA.
Just about any OSB can be used as primary air barrier, if caulked to the studs inside each stud bay. Some like to use construction adhesive or polyurethane caulk between the framing & OSB but that may make the wall too rigid for seismic spec in CA, making it more likely that the wall will walk off the foundation in a big 'un, in which case the fallback is to use an acoustic sealant (which is a bit messy- many people in the trades hate dealing with it.)
I'm not sure how to achieve a 1/4" rainscreen with 2" exterior foam, since 1/4" furring would be too floppy/bendy, and you probably can't just slap up 1/4" rainscreen mesh then long-nail metal lath for the stucco to the studs with foam that thick. (Or can you? Anybody have experience on that?)
A 2x4/R13 + 2" polyiso wall is about R20-R22 whole-wall, and about 7.5" from the exterior of the stucco to the interior paint.
A 2x6/R23 rock wool + 1" polyiso (or 1.5" ZIP-R) wall is at about the same performance, but an inch thicker.
Looking even further outside the box...
...a 4" reinforced concrete wall poured into a minimalist 2" + 2" EPS insulated concrete form with an EIFS exterior would be a lot more rugged, and may be quicker to build (but probably more expensive.) It's only ~R19 whole-wall, wall, but would outperform the 2x4 + 2" polyiso wall in your climate due the thermal mass benefits. ICF construction dead-easy to air seal, very moisture tolerant (if you get the window buck detailing right), nearly impossible to burn down completely during wildfire season, etc. With half inch gypsum tight to the interior EPS it's also ~8.5" from the exterior of the EIFS to the interior paint.
Thank you both for the options. The planned rainscreen is standard 3/4" thick 1x4s vs 1/4".
If we utilize the 2x4 stick framing option, I definitely prefer to keep the OSB next to the lumber to maximize shear strength and keep the assembly simpler. Just using ICF for the basement, and exterior foam on the main floor is already taking almost all builders in my area out of their comfort zone. GBA advice and reference articles have really helped provide the confidence and knowledge to build a more durable and green home.
At 2000' elevation in Nevada County most days do swing above and below optimal inside temp, so thermal mass advantages were key in deciding to use ICF for the entire walk out basement. I'd seen some recommendations to stay at 6" or wider with ICF to help avoid pour complications, but I'll definitely look at 4" thick ICF options closer now.
Is a rainscreen still highly recommended when using stucco over ICFs? Seems the concrete would be much more tolerant of occasional moisture that is able to dry to the outside.
Mitchell,
Q. "Is a rainscreen still highly recommended when using stucco over ICFs?"
A. No. To the best of my knowledge, there is no need to include a rainscreen gap when installing stucco over ICFs.
For the foundation you'll probably still want a fatter wall, but if it's only one story fully above grade 4" can work. Finding an experienced contractor is key to doing any ICF right, and the thinner the wall the more important it becomes. With ICF you don't have the luxury of being able to easily inspect & correct after the pour, and hidden faults aren't rare when dealing with a less experienced contractor. (Don't ask me how I know this... :-( )
If your contractor isn't comfortable with an 8" or 10" foundation wall, a 4" ICF probably isn't in the cards. But 4" concrete poured in forms with sheet EPS applied after the fact can still work.
Even further outside the box would be a 4-5" SCIP solution, where the EPS is a core for a reinforced shot-crete monocoque. You may have to hunt for a contractor with any experience, but it's even more fire-proof than ICF, and about as hurricane proof. (Even the roof can be done as a SCIP, continuous with the walls.) The interior concrete can be textured as the scratch coat for plaster, and the exterior for a hard stucco finish, saving some steps. This one was done in Vancouver WA:
http://www.oregonlive.com/front-porch/index.ssf/2013/07/to_save_the_trees_vancouver_ho.html
This one is in Hawaii (and complete thermal overkill for the climate, but nice! IMHO :-) )
https://www.concretedecor.net/decorativeconcretearticles/vol-11-no-3-april-2011/project-profile-hiilani-ecohouse-kukuihaele-hawaii/