Cannot persuade neighbor not to use fiberglass, so what is the best of the bad choices?

Had a question on insulation, actually trying to guide a neighbor who is also finishing basement and we are buying items together to get some discounted prices.
What we differ on is reason for basement; we are doing for personal use and he is doing for sale of house in spring/summer. Hence while I have decided on xps for wall insulation he has decided [for cost savings] to leave existing blanket pink fiberglass insulation then to frame in front and then new pink fiberglass batts.
I initially tried to discourage with no luck so now trying to make best of it. Did suggest not to have double vapor barrier and therefore he should slit or remove the existing VB once framing done and then VB over new batts.
But then read online how it is advised that fiberglass insulation not to touch cement walls.
Would I be wrong to suggest to neighbor:
Leave EXISTING blanket pink fiberglass insulation WITH VB [no slits and not remove] then frame in front and put new fiberglass batts WITHOUT VB and then drywall?
My reasoning, please advise if makes sense, is that the existing insulation is minimal R whereas new batts about double R so better the new batts are against the plastic VB [of old insulation] then against cement walls; hopefully less chance of moisture/mold. Or am I totally illogical?
Thanks!!
GBA Detail Library
A collection of one thousand construction details organized by climate and house part
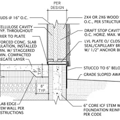
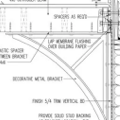
Replies
George,
I think that your neighbor is making a mistake. Any polyethylene layers in this assembly (I assume that we are talking about insulation installed on the interior side of a basement wall) can trap moisture. Moisture can come from the concrete side of the assembly, and moisture can come from the interior (as water vapor that can condense on cool polyethylene). Depending on the season and the temperature profiles, there are many scenarios that can lead to moisture accumulation if your neighbor includes polyethylene in this wall assembly.
My advice is simple: remove all of the existing fiberglass batts and the existing polyethylene and put the materials in a Dumpster. If your neighbor wants to insulate basement walls on the interior, he should use rigid foam or closed-cell spray foam.
Here is a link to an article with more information on this issue: How to Insulate a Basement Wall.
Have you guys looked into reclaimed rigid insulation? Maybe the cost savings of going with recycled foam would help get your neighbor on the right track.
XPS among the least-green foam insulation choices due to the HFC134a blowing agent used. EPS or polyiso are blown with pentane, which is far more benign. (Less than 1% of the global warming potential of HFC134a, and in many or most cases the bulk of that pentane is recovered and burned for process heat at he manufacturing site, turning it into CO2 and water, which are even more benign.)
In a reasonably dry basement with no flooding history it's reasonable to use a combination of rigid foam against the concrete, with a fiberglass or rock wool insulated wall to the interior side of the rigid foam. This must be done without an interior side vapor barrier to avoid trapping moisture inside the studwall- only unfaced or kraft faced fiber insulation, and no polyethylene sheeting, vinyl or foil wallpaper, only standard latex paints. If the slab is not insulated from below, an inch of EPS between the bottom plate and the slab is recommended as a capillary and thermal break.
The amount of wall foam necessary to make this a moisture safe assembly depend on climate. If you used the IRC chapter 7 prescriptives for wood-sheathed above grade walls for your climate zone, it would be sufficient for basement walls as well.
http://publicecodes.cyberregs.com/icod/irc/2012/icod_irc_2012_7_sec002_par025.htm
In most of the northern US climate zones code-min for basement walls would be the equivalent of R15 continuous insulation. That could be 3" of polyiso, 4" of EPS. In zone 5 that could be either 1" of polyiso or 1.5" of EPS and a 2x4 studwall with R13-R15 batts, but in higher zones it would require a bit more foam (and it would beat code-min performance). In zone 6 that could be 1.5" polyiso or 2" of EPS, in zones 7 & 8 it could be done with 1.5" of polyiso or 2" of EPS, plus a 2x3 studwall and compressed batts.
http://publicecodes.cyberregs.com/icod/irc/2012/icod_irc_2012_11_sec002.htm
Hi Martin, Totally agree with your suggestion however neighbor not going to stay at house for long time before selling so can not convince otherwise.
For my part, happy to see that local hardware store has xps on sale.
Back to neighbor, since can not change his mind, is there a lesser of evils:
* Leave existing VB then frame then batts then drywall?
* Remove existing VB then batts then VB then drywall?
Thanks much.
P.S. Your approach on how to insulate joists very good and just about to finish that today!!
Where are you located OP?
George,
I have tried to provide useful advice for your neighbor. I really wish your neighbor good luck.
The polyethylene and fiberglass batts are not appropriate for insulating the interior of a basement wall. It really would be best if your neighbor started from scratch.
George: Polyethylene clad batting of the type used in metal buildings had a brief surge in popularity as basement insulation a couple of decades ago, but it's track record over the long haul has been generally poor, with lots of failures and unintended mold-farms. Covering it up with new fiber insulation won't fix anything, it will only make it worse.
You still haven't hinted about your climate zone / location and it might actually matter, changing the particulars of what works or doesn't.