Basement wall assembly

We are building a house with a daylight basement (three sides below grade), and though the soil is good, rainwater doesn’t drain very well. We have a perimeter drain in, connected to an interior drainage pipe around the garage (which is a few feet lower than the basement level). We unfortunately did not implement a capillary break between the footing and the foundation wall, though we do have a drainage mat and waterproofing on the exterior of the wall.
We currently have fiberglass batts (R21) specified for the walls. I’d like to add 1″ of XPS between the wall and the fiberglass batts to minimize condensation/adsorption, though the walls need to dry in and we are sitting in the middle of rain and cold weather (20-40 deg F). With the fiberglass batts, we would use dehumidifiers and fans to dry in before installing them, though apparently the foam would need to go on the wall right away so that framing could be then built over it.
Should I be concerned about the 1″ of XPS (~1.0 perm rating) not allowing the concrete to dry to the interior before the fiberglass batts and wall coverings (3/4″ drywall) are installed? The builder is specifying that the XPS be attached to the concrete walls with expanding foam (no tape).
Thank you!
GBA Detail Library
A collection of one thousand construction details organized by climate and house part
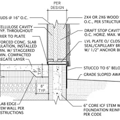
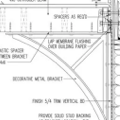
Replies
Mike. It would be helpful to know your location. You will want to install enough rigid foam or spray closed cell foam to keep moisture from condensing on the interior wall. Martin has a detailed article here: https://www.greenbuildingadvisor.com/blogs/dept/musings/how-insulate-basement-wall. XPS is not the most environmentally friendly choice, and you may want to consider other options. (FYI. Reclaimed foam is much cheaper than new product.) If you use rigid foam, it is important to tape all seams and seal all edges.
If you are building a tight house, you may need a dehumidifier to accelerate the drying out process. What are you doing to ensure good air quality for the home's occupants?
Thanks Steve! We are in the pacific northwest (marine 4C according to the map?). That is good to know about the taping and sealing of the edges. We may be able to switch to EPS or a recycled product, and I'll ask about this. For the air quality, we are looking at doing a "Central Fan Integrated Supply Ventilation" (needs an energy-efficient ECM blower): https://www.greenbuildingadvisor.com/blogs/dept/musings/designing-good-ventilation-system. I'd ideally like to do a separate HRV type system, but due to budget that option is less likely.
Mike,
You noted that your concrete walls "need to dry in." In fact, they do not. The concrete walls will be wet for the next 200 years, because the soil is damp, and the walls will never dry. They don't have to dry, because concrete can stay wet for 200 years without harm.
Ideally, you will insulate these concrete walls with rigid foam, and you will give up on your idea of using fiberglass batts. If you install a stud wall near the concrete walls, it's best to leave the stud bays empty, without any insulation in them. To learn why, read How to Insulate a Basement Wall.
Hello Martin. Thank you for your response! We will have a 1" air gap between the wall and the wood framing where we are likely to place a continuous layer of foam, though that will only get us to R5. Our local codes require R10 and my architect and builder would like to be closer to R21. Would placing more layers of foam between the studs work well (instead of the fiberglass), or what would you recommend to get the R value up to an acceptable level? If we were to move the 2x6 studs back to create more room, we would lose interior space in a room that we want to keep the size it correctly is. Thanks for your guidance!
Why not use 2x4 studs to make 2" more space for foam?
Mike,
Your approach will work, although I prefer to keep fiberglass insulation out of basements. If you want to go with an all-foam solution, just switch from 1 inch of continuous rigid foam to 2 or 3 inches of continuous foam.
If you don't want to lose the interior space, you'll need to install some type of insulation between the studs -- or switch from a stud wall to vertical 1x4 furring strips.
Mike:
Rigid foam is available in many thicknesses. You can also install multiple layers to achieve a target r-value. Remember, the foam is attached to the concrete. If you are finishing the basement, the inner wall serves as an attachment point for the drywall and as a chase for wiring. In my basement, I used 1.5 inch metal studs instead of standard dimensional lumber.
See below for information regarding how inward drying on basement walls reduces the risk of liquid water. On the other hand, many basement walls will be fine without such additional insurance.
http://www.nrel.gov/docs/fy13osti/55802.pdf
Jon,
The 2012 document you linked to cites Lstiburek's 2000 book, Builder’s Guide to Cold Climates, as the source of the information. In the 16 years since Lstiburek published that book -- the one with the mistaken information that basement walls need to dry inward -- Lstiburek has reversed himself.
I explain some of the history of this controversy, and the happy resolution of the controversy, in this article: Joe Lstiburek Discusses Basement Insulation and Vapor Retarders.
As I said the last time this controversy arose: If you have liquid water entry through a basement wall, there is no way that switching from a vapor-impermeable insulation to a vapor-permeable insulation is going to stop the water entry problem. The water is still going to come in... in some cases, faster than ever.
On this issue, Aldrich cites his own research, which hasn't been reversed.
You write that Lstiburek's original recommendation "was due to a concern that imperfections in the foam installation might allow some warm interior air to contact the cold concrete, leading to condensation."
This is a different source of moisture than Aldrich tested - any reversal regarding this isn't relevant to Aldrich's findings.
Jon,
I know Robb Aldrich pretty well. I just left a message on his cell phone. When he calls back, I'll report what he has to say on this issue.
Sounds like a good idea, although any researcher reversing his position should publish it - not via some verbal conversation that is then hearsay.
Thanks so much for your advice guys. The lumber drop has taken place, and so unfortunately we don't have the option of switching to 2x4s or anything smaller. Our builder needs to have the walls go in pretty quickly since the framers are starting next week, the lumber is here, and by the time the house is closed in, HVAC will be well under way, so delaying the building of the studs until later isn't an option. My plan right now is to try to procure 1" of XPS from the subcontractor, or better yet from a recycled source, and install it myself before they put in the R21 Fiberglass. It could be difficult to fit it behind the framed wall, so if anyone has done this before and has cautionary tales, that would be much appreciated. Another thought is to ask the insulation sub how much raw foam he could provide in exchange for not doing any insulation in the basement, and I can cut each piece to fit between the studs (perhaps 3" / R15).
One question for you Martin on the topic of concrete needing to dry in. I'm not concerned about the concrete itself, though am thinking that getting a good amount of the water in the concrete out with dehumidifiers and fans for a month or two could be a good idea, especially since we likely will unfortunately have fiberglass in the wall assembly. The concrete will be fine, though I'm concerned about the water coming out of the concrete, attempting to dry to the interior, and soaking the fiberglass. Am I thinking about this incorrectly?
Finally, in the US Dept. of Energy publication Jon provided, it says, "In very cold climates, however, care should be taken to limit condensation risks on the surface of the foam. A frame cavity R-value much higher than the foam R-value could lead to foam surface temperatures below dew point temperatures under extreme conditions. Designers may chose foam R-values higher than fiberglass R-values, or simply forego framing cavity insulation entirely."
Is this something I should be worried about in western washington state, with only 1" of R-5 XPS next to R-21 Fiberglass?
Mike,
The rigid foam needs to be attached to the concrete wall before the 2x4 walls are framed. You aren't going to be able to slip the foam behind the 2x4s once the walls are up.
Q. "I am thinking that getting a good amount of the water in the concrete out with dehumidifiers and fans for a month or two could be a good idea, especially since we likely will unfortunately have fiberglass in the wall assembly. The concrete will be fine, though I'm concerned about the water coming out of the concrete, attempting to dry to the interior, and soaking the fiberglass. Am I thinking about this incorrectly?"
A. The concrete is going to be damp forever (although you're right that it will be most damp right after it is placed). Trying to dry the concrete with a dehumidifier is a fool's errand. In houses without interior rigid foam, the concrete walls can contribute lots of water to the interior air for decades -- because these walls are in contact with damp soil, and therefore always damp, and therefore always evaporating inward.
This inward drying is undesirable. The faster you install the rigid foam, the better.
Q. "Is this [condensation on the cold rigid foam] something I should be worried about in western Washington state, with only 1 inch of R-5 XPS next to R-21 fiberglass?"
A. No. But the document you cite describes the risk I'm talking about, and the phenomenon is one reason that I advocate the all-foam approach. In Climate Zone 4, one inch of rigid foam should work.
Hello Martin,
Thanks very much. I'll do it. One final question if you have the time. We originally had a 1" air gap specified between the 2x6s and the concrete wall. The foam will go in this space. Do I need to back the studs up at all so that there is a gap between the foam and the wood? I'm assuming no, though just want to be sure we don't soak and rot the wood by putting it in direct contact with the foam. Thanks again. I appreciate it.
Mike,
Q. "Do I need to back the studs up at all so that there is a gap between the foam and the wood?"
A. No.
Great, thanks.
Jon,
Robb Aldrich called me back today. After our phone conversation, he sent me an e-mail. Here is what he wrote:
Basement insulation can be a tricky topic.
I think it’s fair to say that several research efforts (by University of Minnesota, BSC, and SWA) found that basement walls that had somewhat permeable insulation systems were drier than walls with impermeable insulation (e.g. faced polyiso). And I’m referring to the moisture in the concrete and/or the space between the concrete and insulation. This makes sense; it’s pretty intuitive.
The question then is: does it matter if the wall is wetter? If this space between the concrete and polyiso is prime space for mold growth, does that matter? Maybe not. If this space is truly sealed from the interior of the basement and there is no communication, then maybe these nasty, moldy conditions don’t matter. For good thermal performance, it’s also quite important that air movement behind the polyiso be eliminated.
In some of our research, we were “lucky” enough to have a window well leak significant amounts of water into our test basement. This got us thinking about longer term durability and bulk water events, so we dumped some water in our walls. We found that the insulation systems that were somewhat permeable dried much faster after bulk water intrusion – again pretty intuitive.
In the guidelines referenced in the discussions (http://www.nrel.gov/docs/fy13osti/55802.pdf), we listed 4 criteria for interior basement insulation systems (p. 12):
• Insulation is directly in contact with the basement wall; i.e., there is no channel for air movement between the insulation and the concrete.
• The assembly is air sealed so that basement air (and the moisture in it) cannot move into the insulation assembly.
• No moisture-sensitive materials are in contact with the concrete walls or floor (this is often addressed by building codes).
• The insulation system is somewhat permeable to water vapor.
I think the last bullet may be of least importance, but I still consider it. The first insulation system we show is polyiso adhered directly to the concrete, but we show the insulation stopping 6” from the slab (p. 15). We (and others) found that this can allow the wall to dry much more quickly. However, we also say that this gap may not be appropriate in some cases (e.g. codes prohibit it, you have hollow CMUs). In the ccSPF system we show (p. 21), there’s virtually no vapor permeability (and we reiterate how critical other aspects of moisture management are!).
My own house may be a good example: a 1950’s cape in Connecticut; full, unfinished basement; and hollow CMU foundation. I applied rigid foam all the way to the floor. If I had left a gap, convective loops in the hollow cores would make the insulation pretty useless (I actually did some crude tests to check this). IF, however, I had poured concrete walls, I would have left a ~6” gap to allow for better drying and recovery from bulk water (which still happens once in a while – that’s another story).
So I still consider insulation permeance, but I don’t know of folks having consistent problems with impermeable insulation systems. More people are going with lots of rigid foam or spray foam, and I haven’t heard of major problems. It’s always a balancing act: risk, efficiency, durability, comfort, resiliency… No silver bullet. But I don’t really see major risks in the initial system proposed – seems pretty similar to the system on p. 19 of our guidelines.
"...better drying and recovery from bulk water.." - seems clear that he still believes that where feasible, drying provides an advantage.