Another basement finishing question

I recently purchased a home and would like to turn the area into a family room with a wet bar with porcelain tile floors. I am having trouble figuring out what the best way to do this.
Facts about basement area:
– Frame house with brick veneer built in 2006
– Climate Zone 4
– Utilized previously as storage / laundry room
– Semi finished
– 800 sq ft & 9 ft height
– 66% below grade
– Cheap carpet over the concrete slab as flooring
– Drywall seems to be directly affixed to the concrete (see attached picture)
– Semi detached house, 1 side is a shared wall with neighbor, 1 side is an egress to the backyard partially in contact with the ground outside, 2 sides with with direct contact with the ground
– Did not feel humid. Previous owner claims no water / moisture / mold issues.
– Not sure if there is external insulation or insulation below the slab floor
Questions on work that needs to be done::
– Framing walls / internal insulation / redo drywall
1- How should my framing be done? 2″ Rigid insulation followed by wood? Pressure treated wood on the bare concrete without insulation? Other suggestions?
2- I only need to frame on the 2 sides of the walls that come into contact with the ground outside.
Should I redo the shared wall and the egress along with this?
3- Do I use mold retardant drywall or regular?
– Set up floor for tiling
1- Should I insulate the floor prior to laying down tiles?
2- Will insulating with 1in rigid insulation with OSB yield good results?
3- Do I need to leave space around the walls?
4- Can use Liquid Nails to glue the foam to the floor and glue the OSB to the foam rather than use tapcons or other fastener?
Any other suggestions would be very much appreciated.
Apologies for the long post and thank you for your time.
GBA Detail Library
A collection of one thousand construction details organized by climate and house part
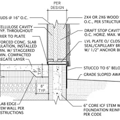
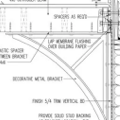
Replies
In zone 4 you'll be fine and would meet code-min performance with 1" of foam (any type) trapped against the foundation wall by a 2x4 wall insulated with unfaced R13s or R15s. If you use foil faced polyiso it will be easy to air seal the foam with a high quality foil tape, but keep the bottom edge of the foam off the slab or it can wick moisture over time. If EPS or XPS it can rest on the slab.
Installing an inch of EPS under the bottom plate of the studwall as a capillary and thermal break from the slab is preferable to using pressure treated, since it keeps moisture from wicking into the assembly, and keeps the temperature of the bottom plate above the likely summertime dew point.
It's not essential to insulate the floor as prep for tile, but it may have a long term benefit. If the basement never-ever has the "musty basement" smell even without mechanical dehumidification you can probably skip it. But 1" EPS (not polyiso) under a standard OSB subfloor would work just fine. You can't use Liquid Nails with foam board, since the solvents will degrade the foam, but there are specially formulated foam board construction adhesives out there that work just fine. Run the floor-foam and OSB all the way to the wall foam, and install the studwall on top of the OSB.
My local home improvement store only sells Faced EPS 1in R3.85 and Unfaced XPS in 1in R5 or 2in R10.
- Would the 1 inch work for both my walls and floor? If its EPS, do I need to remove the facing?
- For the flooring, do I need another vapor barrier or will the taped foam be sufficient?
- As I am unsure if there is external insulation, would this setup cause any issues if the house does have external insulation?
- Should I be concerned about moisture / mold issues between the foam and the concrete?
How about this product?
https://insofast.com/explore/basement-walls/
James,
Either EPS (with or without facings) or XPS will work, but green builders usually avoid the use of XPS (because XPS is manufactured with a blowing agent that has a high global warming potential). For more information, see Choosing Rigid Foam.
You are very lucky that you have a 9-ft. ceiling. If I were you, I would install rigid foam above the concrete floor, followed by a plywood subfloor and your tile.
For more information on insulating your walls and floor, see this article: How to Insulate a Basement Wall.
Taped EPS foam with facers would be a sufficient vapor barrier on the floor. The facers bond well to any number of construction tapes. Be sure to stagger the seams of the EPS with the seams in the OSB by a foot or so.
Thank you for all your help. It looks like I'll only be able to insulate the wall only due to budget concerns. Seems like most people here recommend EPS over XPS. Would 1 in of Faced Type I R3.8 EPS sold at the local big box store be sufficient for the walls? I'm somewhat concerned that the facing on the boards will cause condensation.
James,
In Climate Zone 4, the 2012 IRC requires a minimum of R-10 of continuous insulation for a basement wall. If you want a foam-only solution -- and that's the best way to do it, in my opinion -- and you are using insulation that is rated at R-3.8 per inch, then you will need at least 3 layers of the 1-inch EPS that you are thinking of using. Of course, if they sell the same product in 3-inch-thick panels, that would work.
Don't worry about the facings. Even if you stack up 3 layers of foam, there won't be any condensation on the facings. (The foam separates the cold concrete from the warm interior, so the inner face of the innermost foam will be warm. If it's warm, there won't be any condensation.)
If you want to go with Dana's suggestion -- a combination of 1 inch of rigid foam and some fiberglass insulation on the interior side of the rigid foam -- you can do that instead. But you still need at least R-10 or R-13 of total insulation.
A 2x4/R13 wall comes in at about R10 all by itself after factoring in the thermal bridging of the framing, but the inch of foam is necessary to keep the wood warm & dry enough year-round to fully mitigate mold risk. Even though the basement shows no signs of moisture, when you have insulation against the foundation the foundation will run cooler below grade, and without the foam the average temp at the stud edges next to the foundation may be below the dew point of summertime air in a zone 4A location. It doesn't take much- if budgets are tight you can get there with 3/4" EPS foam and R13 "contractor roll" fiberglass.
In my area it's possible to buy reclaimed and factory seconds foam for about 1/4-1/3 the price of foam at box-stores. Try searching your local craigslist for "rigid insulation", see if it comes up with anything. Deals on used-once roofing foam seem to show up in many locations, eg:
https://philadelphia.craigslist.org/mad/5540179346.html
^^That's about $20/sheet for 3" polyiso, which performs at about R16-R18. Virgin stock f.o.b. the local distributors in my area runs ~$60/sheet.
With roofing polyiso 2" (which is a common standard thickness) would get you to code min on it's own and you could skip the batts. But you would want to keep the bottom edge off the slab. Even if you don't run 1" EPS over the whole floor, putting some under the bottom plate of the studwall and under the edge of any polyiso used as wall foam.