Advice on Insulating Unvented Attic – 1884 Home in Zone 4A

I hesitate to ask a question on this topic knowing how many other threads exist. I hope my question is OK. I have spent considerable time on forums such as these and read many articles on sites like Building Science. I am struggling with making the right decision on the insulation.
I am going to unload on the details for reference – I hope it isn’t overkill: 1884 home, about 1400 sq ft of attic floor, air handler for heat pump that feeds heating and cooling to 2nd floor below, two stairways – one walking right up to door to attic and other much smaller with door at 2nd level), currently invented, no existing insulation in floor or elsewhere, somewhat complex roof line (see attached a Google sketch), 7 small windows, heavy pine floors, and 9″ rafters. Roof will be replaced (felt, shingles) as part of the upcoming work.
The house has a cooling/heating heat pump (the one in the attic and another air handler in the cellar) but there is also a oil boiler steam system throughout the house for heat. The cellar (about same footprint as attic) currently has moisture issues. None of the downspouts drain away from the foundation (stacked stone and brick in places) and there is very little grade around the home. The floor is earth with some areas parged stone or brick and some dug out earth with staked stone. At present there is fiberglass batts in the joists and a poorly installed plastic vapor barrier under stones. It is not vented and has one HVAC return open and two supply vents open in the cellar.
Our plan for the cellar is to correct outside draining, creating venting, replace fiberglass (with barrier towards upper floor), close off HVAC openings, and airseal where possible. I add this detail because I read with interest another long post where someone pointed out the problem with creating an airtight attic assembly while having moisture problems elsewhere. The walls appear to be a mixed bag due to some past renovation. There is probably more plaster than drywall and maybe 40% of the walls have some form of insulation. It seems the current vinyl siding was installed over the old wood siding. With the exception of three old windows at the attic level, all other windows were replaced within the last 5 years.
So, the reading I have done suggests an unvented attic is a reasonable approach. Plus, there is one section of the attic we could see finishing down the road (the section where the main staircase comes up). Otherwise, in the mean time, we would surely be using it for storage. I’m struggling with the idea of spray foam. I suppose mainly due to costs but also just because the more I read the more I get confused. Three spray foam companies recommended open cell with two offered closed cell as an option. They all seemed convinced open cell was the ticket. One also gave an estimate using a combination of rigid foam board with foil against the underside of the roof in combination with fiberglass and FKS.
We can’t do everything – the budget won’t allow. We do know from past owners the heating and cooling bills were crazy. With zero insulation and handler in the attic it makes sense. It seems like putting money into the attic insulation makes sense. I get the argument over open cell versus closed cell as it relates to roof leaks. But without insulation above the roof deck, and despite this being a retrofit, it seems open cell doesn’t provide the recommended vapor impermeable barrier for an unvented attic. Perhaps I am reading things incorrectly.
There is part of me that is interested in the idea of using rigid foam (e.g. Thermax) as the barrier and then in combination with fiberglass. I read the recent build science article comparing the two approaches (attic floor versus roof) where they used rigid foam in that manner. But I have not seem many other articles covering this approach. I sense it may be just as expensive given the cost of rigid foam board (w/foil). I suppose my questions are not well focused or a bit open ended. But I am curious to know if anyone has struggled with similar questions with similar circumstances. For example, if using spray foam, is closed cell the answer? Assuming I correct moisture issues in the cellar, given the age of the house and other possible infiltration areas, am I asking for trouble to insulate the attic? From a cost and effectiveness perspective, is the rigid foam/fiberglass/FSK covering approach worth looking into?
Again, sorry for the length. I know when I read other posts with similar questions it is really helpful to read the discussion. Thank you.
GBA Detail Library
A collection of one thousand construction details organized by climate and house part
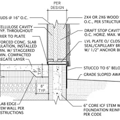
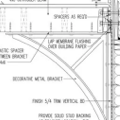
Replies
Historical,
I don't have time today to address all of your questions, but I will start with your basement plan.
You wrote, "Our plan for the cellar is to correct outside draining, creating venting, replace fiberglass (with barrier towards upper floor)."
1. Don't add basement vents. Basements (like crawl spaces) should not be vented.
2. Don't install any fiberglass batts in your basement.
3. For more information, see:
How to Insulate a Basement Wall
Building an Unvented Crawl Space
Martin, I very much appreciate your response and willingness to provide any feedback. I have read with interest the various articles about basements. I am going to find a couple pictures of the cellar to show the situation. I have questions about how to approach an unvented cellar /basement. But I'll post pictures to help explain. Thank you!
I attached a PDF file with some pictures. I wish I had better ones on hand. So, as it relates to the cellar, here are my concerns. First, the property has poor drainage. There is no doubt some changes can be made to the downspouts and there are needed repairs to the existing windows at grade. For example, one of the largest sections of the roof drains down to the lowest point around the house. However, I worry because the back of the house has so little relief and the current grade is within 6" of the siding / top of the foundation. So I don't know if having moisture in the cellar is something that just can't be avoided. At the same time, perhaps the idea that venting will help is a falsehood.
For additional reference, the cellar has a sump (for the water heater and water softener), an electric water heater, well pump / pressure tank, oil boiler, and HVAC that serves the1st floor above. The "newer" and larger section of the cellar (~22' x 40') has near vertical walls (parges brick/stone). The older section (~ 20' x 25' ) looks as if it was dug out in the past to put in the oil tank and boiler (that vents through a chimney). The existing cellar windows were covered up and HVAC was opened up with one return and two supply vents. The earth floor appears to have a plastic sheeting with a few inches of small stone.
Another area of concern are bugs - there has been past termite and beetle damage and minor areas showing white rot. Just going down into the cellar it's obvious it's moist. I went down one day when the A/C was running and I could have wiped a cup of water off the uninsulated metal ducts. The moisture is my biggest concern going into this house. Both because of the obvious issues in the cellar but also because of how that moisture might impact our efforts in the attic.
I have learned so much from this forum and the building science articles. I truly appreciate any help and information. And I hope the detail I provided helps someone else in a similar situation.
Historical,
There is no cheap way to fix an old basement like this. The right way is expensive.
While changing the grade on the exterior of a home is often expensive, it is important to do what it takes to get the grade to slope away from the foundation. That may require installing a new swale on the uphill side of your house.
The basement will require a lot of work. It may be necessary to remove some dirt to lower the grade or even up the floor. Once that's done, you'll probably want to install 6-mil (or thicker) polyethylene on the floor, followed by a concrete slab.
The fiberglass batts belong in a dumpster. You'll probably want to insulate the existing stone foundation walls with closed-cell spray polyurethane foam.
It looks like you have a rusting furnace flue in the photo. There may be safety concerns related to your existing heating equipment.
Your basement may also need an interior French drain system leading to a sump with a sump pump.
If all of this work is discouraging or daunting, you may want to call a local basement expert.
Thank you for the feedback. I am going to talk to a contractor with experience in older homes about some of the required repairs or approaches. I think that is good advice. Based on a few conversations, all agree that some redirection of rain water outside is critical. And given there are gutters that simply dump water at the outside of the foundation, we have some obvious places to start. On the boiler, the plan is to replace that boiler flue and reline the chimney. I agree that is an issue. We will also be removing the fiberglass (and now perhaps not replacing) and of course the old (asbestos) pipe wrap will be removed (by an asbestos contractor).
In one of many threads I read elsewhere, referring to a similar type dug out cellar area, someone raised a concern over putting a vapor barrier over the soil that effectively forms a knee wall for the stacked stone foundation. The thinking was that covering the soil might increase moisture content and weaken the soil supporting the foundation. Is there any validity to this?
And is there any validity to the idea that insulating from the inside could take away the heat previously provided to the foundation mass and thus increase the likelihood that there is heaving on the outside of the foundation? I have seen it suggested that these old foundations rely on the warming from the cellar to moderate cold temperatures on the outside of the wall. Or perhaps in zone 4 it isn't a likely issue?
And I thought the attic was my only problem.. :/
Value of home, now and after spending $_______?
Budget $_______?
Reason for renovation verses sell and purchase desired end product?
I see $100,000 of DIY work to get to a C level. It would cost as much as new construction or more to make a modern low energy low maintenance home using a qualified contractor.
I have recently completed such a project. It is a specialty and wouldn't have just any contractor attempt the project.
Get contractors out to suggest options. We have dug out cellars and even raised homes and added new foundations. Existing stone foundations can be can be added to by stepping inward while digging down. Or convert to clean dry crawlspace.
Attic. DIY is best cost. Still, budget is $____? $10,000 ? Vent, fiberglass, rigid foam then drywall. Contractor price triple. Spray foam quadrupal it. Get some quotes.
What about windows and walls? Natural gas heat source? Switching heat pumps to minisplits?
Are you living in this home with the asbestos mess and moisture issues?
AJ - I appreciate your comments. It's always worth putting things in context - specifically dollars. This house is a short sale and given the purchase price we "believe" it makes sense to make some investments like insulation and other corrective actions like the cellar/drainage. And, despite the attraction of it in my mind, I guess there is no economical way to insulate an unvented attic as compared to putting insulation at the floor level. The move to ccSPF is about 6K more. I guess it's hard to quantify things when trying to compare insulating the attic floor versus the roof line considering things like the stairways, HVAC, etc. We just want to make a reasonable dent in the heating and cooling costs. I see how doing the roof line make more sense. But would the attic floor insulation approach get me 80% of the way there? It's hard to know. When you mention the vent, fiberglass, rigid foam, and drywall, were you talking about insulating at the roof or floor? Thx.
I'll second Martin's recommendation for insulating & air sealing the foundation with closed cell foam as part of the "critical" list, every bit as important as air-sealing the attic.
The fiberglass insulating between the floor and the basement lowers the summertime temp in the basement, increasing the mold & rot potential just from humid summertime outdoor air, while doing next to nothing for stopping whole-house stack-effect drives from robbing heat all winter.
Stopping air leakage at both the top and bottom of the "stack" to block stack effect infiltration counts, and insulating the foundation is more effective than insulating between the joists, R for R. Even 2" of closed cell foam (about $2-2.50/square foot) gives you ~ R12 while nearly eliminating the air leakage at the foundation sill and between the stones.
Frost heaves propagate in the direction of heat loss, and as long as the basement is heated, there's zero chance of frost heave on the foundation. Even if you reduce the heat loss 3 orders of magnitude, the direction is still the same. Frost heaved foundations & slabs in zone 4A are somewhat rare even for unheated buildings, but are primarily an unheated barn sort of issue, where the heat loss in winter is from the ground upward, rather than from the basement downward. In zone 6 or higher you might have to think a bit more carefully about it though, and sometimes buried foam "wing" insulation around the exterior perimeter might be called for, but that's literally never called for with a heated building in zone 4.
In zone 4A, if you can put at least 2.5" of roofing iso or 4" of EPS (R15+) above the roof deck when you re-roof you can then safely fill out the rest of the R on the interior using fiber. See:
https://www.energycodes.gov/sites/default/files/documents/cn_unvented_attic_assemblies.pdf
This would thermally outperform an interior foam insulation job, since it thermally breaks the rafters. But if it is a complicated roof with lots of hips & valleys the scrap rate would be high. Using 2x furring over the foam long-screwed to the rafters &/or plank decking with pancake head timber screws (eg FastenMaster Headlok) 24" on center works, over which a non-structural half-inch OSB nailer deck can be applied for the shingles. Cor-a-Vent or similar vents + screening between the nailer deck & foam at the edges keeps critters from making the vent cavity into a condo complex. Use a membrane between the foam and roof deck for air-tightness, and use spray foam judiciously on the interior to seal up air leaks.
Reclaimed roofing foam from commercial re-roofing or demolition can be had at a fraction of virgin-stock pricing. If you can't find a local source, insulationdepot.com will drop-ship if you need a bunch of it, but there are minimum orders.
If you have simple roof lines this is far cheaper than any spray foam option for insulating it. DO use spray foam for air-sealing though.
Wrapping flues with unfaced R13 rock wool batts can provide the necessary clearance to combustible insulation while still giving decent R-value, but use sheet-metal for air sealing those penetrations.
Do Dana and Martin's cellar including water asbestos, boiler, duct redo, etc. $20,000 budget.
Do attic floor cellulose after all air sealing work. $5000 budget.
Pull trim on doors, windows and seal. Blower door check infrared scan home fix up leaks and insulation in walls. $5000
Then another $25,000 for updating appliances, kitchen and baths lightly.
Detail your planned work version 1.0 and price it. That's next.
Thank you for the additional feedback. While I have only spoken to a few roofing companies, none of them seemed to have experience going the route of putting rigid foam on top of the roof deck. I don't know if that is a product of this area or if I am just talking to the wrong people. The roof does have three gables and two chimneys. I don't know if that is considered complicated. One roof mentioned to me that the peaks and valleys might present problems. But they may just not be experienced in doing it. Can anyone comment on how much the addition of rigid foam on the deck adds to a typical roofing project. We have quotes in the 8-9K range (felt, shingles, etc).
Can anyone comment if using a combination of rigid foam board (iso) and fiberglass on the interior side is significantly cheaper than a ccSPF spray foam option? I guess a last layer such as SFK From the one building science article comparing approaches of weatherization (RR-1205) it seems like the cost of something like Thermax is as expensive and not so easy to install. But then it would offer a change for DIY. Has anyone taken this approach instead of spray foam?
Am I correct that is spray foam is chosen as an option on the interior that a closed cell foam is required in zone 4 to provide an adequate vapor barrier? That is my take away from all the articles i read. However, i don't know why three of the foam contractors I spoke to recommended closed cell. Most often the cited the roof leaking issue.
Lastly, I added a couple more helpful pictures of the cellar for general reference in this discussion. I think these two pictures provide a better sense of the layout. As a side note, we already have plans to have a asbestos contractor remove the pipe wrap. And I would welcome putting that fiberglass in the trash if that is the direction we go. :/
Foam-over retrofits of residential roofs are pretty much the province of performance-builders, not so much roofers. Many roofers are used to dealing with 1-2" of XPS as an ice-dam countermeasure, but they usually long-nail the shingles rather than applying a nailer deck. Some performance builders will skip the furring and just apply a nailer deck through-screwed to the structural wood, which is less work, but also less robust over the very long term.
Hunter Panels and Atlas et al make products with iso or EPS pre-laminated to the foam to make this easier, and they come in both vented & unvented versions. The material cost is higher, but the site-labor lower. If your roofer can't handle it, a GC probably could- there's no rocket-science or very much design work to going that route- just follow the manufacturer's instructions on fastener spacings & type, underlayments, etc. See:
http://hpanels.com/images/stories/pdfs/lit_prod_color/english/Cool-Vent.pdf
http://hpanels.com/images/stories/pdfs/lit_prod_color/english/H-Shield-NB.pdf
http://hpanels.com/images/stories/pdfs/tech_bulls/Fasteners.pdf
http://www.atlasroofing.com/tabbed.php?section_url=58
http://www.atlasroofing.com/tabbed.php?section_url=51
Whether it's cheaper to do a DIY version using reclaimed roofing foam & furring depends on your local labor costs and the confidence/experience of the builder, but it's not hard. Whether DIY or commercial panel edge details need to be designed for venting & drip edges, and to keep it architecturally appropriate, and in some instances flues will have to be extended by the thickness of the applied materials, etc.
Normally in retrofits there isn't already a re-roofing planned, which makes the over-deck foam a more expensive proposition, but since you're planning to re-roof this is one of those opportunity moments that only comes along every 25-50 years or longer. Once you re-roof taking it down to the roof deck & new roofing felt it'll usually be re-roofed as overlaid shingles the next time around.
With an interior perimeter drain and (if possible) a parge over the stone wall that basement can be insulated with 2lb foam. It's probably worth laying down R5 XPS foam and a 1.5"-2" rat-slab with 6-10 mil poly between the foam and the slab too. These people started out with a veritable SWAMP in their field stone foundation/dirt-floored basement and ended up in pretty good shape:
https://www.powerofaction.com/media/pdf/DER_CaseStudy_Belchertown_MA.pdf
(Scroll to the last page for some of the basement details.)
Even replacing the fiberglass with open cell foam or taped foil-faced iso won't make it as tight as doing the walls & band joists with closed cell foam, and it would put the boiler outside of conditioned space (so that the standby losses are truly lost, not accruing at all to the house) and make the basement colder & more mold-susceptible. See the Arlington MA deep-energy-retrofit example outlined here, that leaks more air than many code-min houses:
http://www.buildingscience.com/documents/reports/rr-1108-hybrid-foundations-retrofits-measure-guideline
Trying to air-seal the basement/first-floor plane is a fools errand- it ends up being cheaper & more reliable in the end to attack the problem at the foundation wall/sill.