Will minisplits work in all floor plans?

I’m researching the details of building a new house in central KY, zone 4a. This will be the house that lasts for the rest of our lives (hopefully 50+ more years). I had assumed that GSHP were the “no-brainer” HVAC choice, but from the looks of things, it isn’t that simple. I’ve been reading some amazing things about the potential of mini split systems.
My question is this: Aside from getting your house as well insulated and tight as possible, do you need a certain floor plan or construction feature to make mini-splits work? Does the foorplan need to be open without many walls and closed rooms? Will this only work with smaller square footages? In other words, can I take a traditional, 2-story, “normal” house plan (3k-4k sq. ft.), wrap it up with R30 walls and R60 attic, and get good results with some mini split units, or do I need to build a house with a specific floor plan?
Also, what is the contingency plan if the mini splits weren’t getting the job done? What if the bedrooms were too hot and humid in the summers? Or what if parts of the house were too hot or cold? It would be a major pain at that point to try and go back in and install ductwork.
GBA Detail Library
A collection of one thousand construction details organized by climate and house part
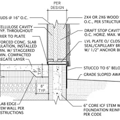
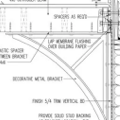
Replies
Clay,
Any heating and cooling system needs to be designed. That principle applies to a conventional forced-air system hooked up to a furnace and a split-system air conditioner, and it also applies to a minisplit system.
Start by performing a room-by-room heating and cooling load calculation.
Once you know your loads, you can start designing your system, using a combination of ducted minisplits and ductless minisplits.
There are lots of articles on this topic on the GBA site. I suggest you start with this article: Rules of Thumb for Ductless Minisplits. Don't forget to investigate the links, including the links found in the "Related Articles" sidebar.
Thanks Martin. Where does that step fall in the planning process? We have not settled on a house plan yet, so we are in the very early stages of all of this. I wanted to see if picking certain house features would exclude mini splits from the realm of possibilities.
Thanks for the links. I have been trying to read everything I can get my hands on. I need more time in the day! Haha.
Clay,
You can't perform a room-by-room heating and cooling load calculation until you have settled on a plan.
However, you should hire an architect or designer who understands green principles, so that you end up with a house that is compact, with as few bump-outs and ells as possible.
To understand some basic principles, read this article: Green Building for Beginners.
To read a humorous blog by Greg Labbé, filled with many examples of hideous homes that can serve as examples of "what to avoid," see Pastiche Architecture.
Thanks, again, for the links. Just when I think I have read most of the applicable articles on this site, I find (or you point out) another rabbit hole to tumble down. The first few paragraphs of "Green Building for Beginners" are scary accurate!
Oh, and do you make recommendations for architects/designers? If so, do you have any in the Central KY area?
Clay,
I too live in South central Kentucky! FWIW Here are my thoughts. Minisplits need help dealing with rooms that have the doors closed! Conventional ducted forced air heat pump systems can easily keep even the rooms with closed doors close to the same temperature. Unfortunately available forced air heat pump systems have abysmal energy efficiency whenever it's cold outside , many resort to a COP of 1 resistance heat at temperatures below 20 f. While the low temperature minisplts are still running a COP of 2 well below zero f. I plan on solving the puzzle by using the air handler (with ECM for energy efficiency) portion of a conventional system ducted to all the closed rooms & the perimeter of the house with a low temperature minisplit. I'll dedicate a closet to the minisplit and air handler. Return air will flow through the ceilings to the top of the closet, the air handler output will go to ducts below the floor. The air handler will be "slaved" to the minisplit with it's power controlled by sensing the current drawn by the minisplit. the minisplit will have a remote thermostat located in a hallway.
If you're worried about the floorpan or door status interfering with the units' ability to heat or cool the house, there's always a ducted mini-split heat pump, which is still going to be more efficient than a conventional ducted heat pump. And you'll likely only need one, which may save you money compared to a multi-split system with several indoor heads.
For an 2-story house you'd probably still need at least two zones (upstairs & downstairs) even with mini-splits, whether ducted or ductless.
No mini-splits do much better than a COP of 2 at sub-zero temps, at any modulated output level. (Most are a bit under 2 at -5F.) , But they can be into the threes at +15F if sized optimally, breaking into the 4s at outdoor temps of 40F. Sized correctly you can nearly meet or sometimes beat typical GSHP efficiencies (if not absolute best-case GSHP efficiencies) in a zone 4A climate. If you spend the difference in upfront cost between a GSHP and a couple of mini-splits on rooftop solar it's often a better investment. GSHP costs vary all over the place, but so does the quality of GSHP system designs. A mini-split is a pre-engineered "system in a can", with far fewer ways to go wrong (though truly creative installers are able to invent new ways to screw it up every day! :-) )
With modest to moderately sized high-R houses most HVAC equipment is ridiculously oversized for the loads, but there's a reasonable range with mini-splits. A typical 1.5 ton cold climate mini-split (ducted or ductless can deliver something like 20,000 BTU/hr @ 15F, which covers the heating load of most pretty-good houses at that temp. A tight 3000-4000' code-min house might have a heat load north of 35,000 BTU/hr, but if you pick a shape that's easy to air-seal that doesn't have a lot of thermally-bridging corners & bump-outs, slapping 2-4" of foam on the exterior of that house, an energy heel roof truss that allows 18" of fluff in the attic and using U0.25 or lower windows gets you down to the 20K range, at which point a couple of 3/4 tonners (one per floor) will have plenty of capacity at your likely outside design temp.
A 2x6/R20 16" o.c. code min wall with typical siding options comes in at about R14 whole wall. To hit your nominal R30 whole-wall goal takes 4" of EPS or 3" of polyiso on the exterior. That reduces the wall losses by a bit more than half that of code-min construction. A code-max window in zone 4A is U0.35. Dropping that to U0.25 cuts window losses by almost a third. The performance difference between a code min R49 and R60 in the attic isn't much, but the difference in cost isn't much either.
DO pay attention to the foundation insulation. Code-min for zone 4A is R10 continuous, but you'll want at least R15. Pouring the foundation with R20-R22 insulating concrete forms (2.5" of EPS on both sides) is not insane. If you design it right you can have the sheathing foam for the framed wall slightly proud of the ICF foam to get a continuous thermal break at the foundation sill. In termite country you'll want to use metal flashing at the transition between the ICF foam and the foam/sill above & or Z-flashing if the housewrap is between the foam & sheathing, but the foundation sill will still be warmer & drier than if the foundation had no exterior insulation and the thermal bridging will be less.
Dana, thanks so much for the reply. This helps me greatly.
We really like the Federal and Georgian architecture of the historic homes dotted around our state, and would love to build a house that looks like it has been around for a long time. This means a simple rectangle or square footprint and a simple gabled-end roof or hip roof design (no valleys, or changes in pitch, Martin :) ). It also means thick exterior masonry walls and deep window sills, which means going with a thick, insulated wall and outie windows will fit right in. I'm trying my best to ditch the idea of chimneys on either end of the house, but it has been tough. I know they are terrible from a heat loss perspective, but there is something about a hearth and mantle in the living room and twin chimneys on the exterior that just completes the "home" feel. I've even wondered about putting in dummy chimneys and mantles that are totally for show, even though I know that sounds silly and wasteful.
The only deviation from the simple rectangle/square footprint would be a mudroom or transition space between the house and attached garage (from an "historic" standpoint, I'd love to detach the garage, but I don't see that passing the practicality test).
However, even though we want the house to look like it has been there for 200+ years, we realize that we no longer live in the 1800's, and building a house that is viable in the present as well as the future is something equally, if not more, important. We want a modern house on the inside with a historic house veneer. If we can make this work, we will get the best of both worlds. If it won't work, however, I want to know early in the design stages so we can figure out what has to be compromised.
Dana, you said, "If you spend the difference in upfront cost between a GSHP and a couple of mini-splits on rooftop solar it's often a better investment. " This is exactly my thinking. Why spend $20k-$30k on GSHP when I could spend that same amount (or less) on mini splits and solar? This approach not only sounds like it uses less energy than GSHP, but adding solar to the equation makes the difference in energy use that much greater. I don't think I am off in thinking that the price difference between a couple of mini splits and a GSHP would buy enough solar to put a huge dent in my total electric usage, not just covering the heating and cooling usage. That seems like a much smarter investment. Plus, I will have enough land that I could set the arrays out in the back yard and add to it as needed. I've seen on the internet where arrays were built on the roof of a pergola. It looked great and could be a fun DIY project.
If you want a chimney, you could always put it in the center of the house, rather than one at each end, basically turning it into a masonry heater and a useful heating appliance.
Thanks for the reply, Nate. A central chimney is characteristic of northern architecture. Southern Georgians and Federals (with which we identify here in KY) have chimneys on the ends. It may seem like a silly thing to make the distinction, but around here it would stick out like a sore thumb.
With brick veneers there is a huge thermal bridge to contend with at the top of the foundation, with no really great solution. Think carefully how you are going to deal with that, since it will undercut the performance of a high-R house. One approach is to build a 12" step-down on the exterior side of the foundation with the brick and foam extending a food below the foundation sill or installing a foot of aerated autoclaved concrete (AAC) insulating block between the top of the concrete and the foundation sill, with interior side rigid insulation going all the way up to the top of the AAC. If you do nothing and just plant it all on top of the foundation you'll have an R1-R2 stripe of concrete & brick at the bottom of your R30 wall, and above your R15-R20 foundation.
With thick foam & brick veneers there is also the issue of finding appropriate brick-ties that can handle the length, which can be a real cost adder. Deeper commercial ties are probably what you'd need to manage 4" foam.
Even better than AAC for that situation is Foamglas, which is marketed as a thermal break for brick ledges and has double or more the R-value of typical AAC block. Insulating firebricks could probably work too if an especially gun-shy inspector is worried about the load-bearing capacity of foamglas.
Thanks again Dana. I am somewhat familiar with the step-down idea. We like the idea of a stone veneer foundation, and our builder mentioned a step-down below the top of the foundation to rest the stone on.
A foot of AAC block might be close enough in appearance to stone to serve the same purpose. However, for that to look right, the concrete should not be seen, so the grading would have to come all the way up to the AAC. Something tells me that is a no-no?
Brick & stone veneers are pretty dense and will exert fairly high psi pressure- you may have to use a denser AAC to support the veneer(?), compared to supporting the house where the load distributed by a 2x6 or wider sill plate. I've only heard reference to AAC supporting the foundation sill as a thermal break for the foundation sill (and not the veneer) in these assemblies, but I have no first-hand experience with it. Poured concrete can handle quite a bit more pressure than AAC.
AAC is extremely vapor-permeable, but has less capillary draw than poured concrete, and I believe it's fine to use at or below grade. (With the usual foundation waterproofing below grade.)
So if I understand you correctly, you were suggesting the AAC to sit on top of the poured concrete wall but behind the brick? The if so, I misunderstood.
A quick search brought up this article from BSC regarding insulating slabs. http://www.buildingscience.com/documents/insights/bsi-059-slab-happy
Figure 4 (halfway down the page) shows some sort of insulating block sitting as the foundation for the veneer, but it does not mention what that block is.
So... how much of a fatal problem is this? Enough to scrap the idea of brick veneer? Are there any alternatives? Live with the R-1 stripe in the basement and add some insulation under the floor joists to compensate?
Clay,
Assuming you have a basement, the solution is simply to insulate your basement walls on the interior. In How to Insulate a Basement Wall, I wrote, "If you plan to install brick veneer on your above-grade walls, interior basement insulation makes more sense than exterior insulation." If you click the link and look at Image #4 on that page, you'll see why installing rigid foam on the exterior of a basement wall is incompatible with brick veneer.
Thanks Martin. I read that article (and all 129 comments) just a few hours ago, actually. :) I remember reading that statement and taking comfort in a clear choice for my situation, however I thought that since I plan to use exterior insulation on the above-grade walls that that still created a path for the heat to escape. Looking at Image #2 of that same article, and envisioning how brick veneer and exterior foam would be different, helps me see the continuous layer of insulation, I think. With my wall, you would move back the wall and floor assemblies, put the brick on the outside edge of the concrete, followed by the insulation, then the wall and floor assemblies as drawn. The insulation for the above grade walls are thick enough to completely isolate the basement wall from the inside.
The thought just hit me. Geez, this is going to have to be a pretty thick foundation wall, correct? The foundation wall is going to have to be wide enough to span the brick veneer, the rain gap, the exterior rigid foam, the sheathing, and the 6" frame wall. I'm not going to be able to let the exterior foam hang out over the foundation like I see suggested on some articles because there will be no way to support the brick veneer.
Also, Martin, I read one of your articles today (there have been too many and I can't find it again), I thought it was in the comments of your "How to Insulate a Basement Wall" article, but I can't find it now, where someone asked about why not just insulate the ceiling of the basement instead of the basement walls and floor. You mentioned a couple of reasons, one being that the ducts for the downstairs HVAC is usually routed through the basement. What about situations where there is no ducts in the basement, as in the case of a minisplit system?
I'm sure the other reasons make enough of a case to still insulate the walls, but I can't find that comment.
Also, I guess if I went with a HPWH, you would say that the cost savings in insulating yourself from the cooler basement (in the winter) would be offset by the lower efficiency of the HPWH operating in a colder basement and the lack of cooling benefit from the cooler basement in the summer?
Clay,
There are several issues here.
First of all, ducts are not the only issue. Most basements also including plumbing, including hot water pipes -- and it's good to have plumbing inside of the conditioned space of your building. (In Vermont, if you insulate the basement ceiling but not the basement walls, it's pretty easy for your pipes to freeze. That's probably not true in Kentucky -- but it's still a good idea to keep your pipes indoors.)
Second, many basements have a water heater. Water heaters belong indoors, not outdoors.
Third, it's difficult to do a good job insulating a basement ceiling, because all of the penetrations make the insulation work awkward. It's usually easier to insulate the basement walls.
Fourth, most homeowners (these days) occasionally visit their basement or use it for storage -- and they don't really want the basement to be cold in the winter.
Of course! Frozen pipes aren't usually a concern for us in KY but if you remove the furnace from the basement (in the case of a mini split) you'd be taking a big risk. Once again, thank you so much! The advice here is invaluable. I'm going to get a membership to say thanks!
Clay,
NOT ALL BRICK has the same issues!
My house will have a brick veneer exterior but it will only weigh 7 pounds per square foot and be supported by the wood walls, not bearing directly on the foundation. The trick is "thin" brick or adhered masonry. The actual brick used are about 1/2" thick. They can be applied much like ceramic tile to stucco or glued to a fabricated substrate ( I'm using a substrate by Ambrico called EZ-Wall).
There is no thermal bridge issue with "thin brick.
The most cost effective insulated foundation is called PWF, Made of pressure treated lumber (wood foundation graded) using no concrete in the footings or walls. very rare in Kentucky, I've only found one source for the materials.. .
..
Hi All,
I'm starting to narrow down a floor plan and would like you all to take a look and let me know if this 2nd floor layout would be too chopped up for a ductless mini split.
If a ductless model would not work, what about a ducted mini split? How do ducted mini splits work in an attic with 16-18" of blown insulation on the attic floor? Do you just run the ducts on the floor of the attic and then cover them up with the blown insulation? WHat about the unit itself? I assume it has to sit above the level of the insulation?
What about normal HVAC in the attic? How does that work with blown insulation on the attic floor?
Ideally a ducted unit would be located inside the PRESSURE boundary of the house, not just buried in the insulation layer, since air-sealing the ducts, air handler, and sealing the register boots to the pressure boundary (often the ceiling gypsum, in your configuration), would have to be PERFECT, and remain perfect forever. Any leakage of the ducted system outside of the pressure boundary of the house would drive outdoor air infiltration, increasing the load. Also, the ducts would have to be insulated with fairly thick air-permeable insulation to avoid condensation on the ducts under the fiber insulation in summer.
A ducted mini-split is very low- profile and the ducts could be as well. A horizontal service chase under the air barrier can be a reasonable solution. This can be done with 1/2" OSB on the underside of the structural joists or truss chords detailed as an air barrier, with framing underneath that to support the finish ceiling below the OSB. This means the framing of the upper floor needs to be taller to accommodate it, and the necessary depth of the chase for the ducts & mini-duct cassette needs to be known a-priori.
Fujitsu's mini-ducted units only take 9.5" of space, and (unlike most) are allowed to be mounted vertically, in a wall/chase.
http://www.btureps.com/fujitsu/fujitsu-literature/2014-rlfcd-rlfcc-brochure.pdf
Figuring out the cassette placement and it's condensate drain in a location where it's easily serviced is an important consideration. Mounting it in a wall or at the top of an accessible closet space works, and allows you to use thinner, narrower profile ducts in any ceiling service-chase or soffit approach to duct routing inside the pressure boundary.
Thanks D Dorsett. How centrally located does the unit need to be? If it doesn't have to be right in the middle, I would imagine the laundry room would be a good place since the condensate drain would be close to an existing drain. Plus, the unit would be somewhat removed from the bedrooms in case noise was an issue. I am planning for 9 foot ceilings on the 2nd floor, so I assume I could always drop the ceiling in some areas to get the ducts under the attic.
I also have some extra room in the linen closet off the master bedroom, but I would be worried about the noise of the unit being so close to our bedroom, plus the condensate would have further to go, although the master bath isn't too far away.
From the looks of things, if I had the unit in the laundry, I could drop the ceiling in the kids bath, the central hall, and even the linen and kid's closet on the other side of the hall. I could run the supply ducts above the kids bath out to the central hall, and then straight over to above the linen closet and Kid #2 closet.
ETA: Or, if it needs to be centrally located, I assume I could put it in the top of the kid's bath closet. That would allow me to still have a drain close by.
It doesn't need to be centrally located, but there are limitations to how many miles of duct can still work. Not all vendors' mini-ducted units have the same amount of blower capacity, and duct friction has a direct effect on as-implemented efficiency.
The floor plan attachment isn't accessible, so it's hard for me to guess if the laundry room location would work, but it probably does. Like anything else, designing it rather than hacking at it makes a difference, starting with the room-by-room load numbers...
Oops. Sorry. I didn't even check to see if the file uploaded correctly.
Here is a link to cloud file. https://onedrive.live.com/redir?resid=9DEE0D7D08E081E6!1328&authkey=!ANHx1h-nl5BUhX8&ithint=file%2cpdf
Basically, the house is 44' wide and the laundry room is against the exterior wall. Fortunately, the laundry room sits in the middle of the house front to back, and I should be able to run a straight line from there, across to the other side of the house. The supply to all the rooms can be just a short run off the main line.
Looking at the floor plan I'd hazard that the top of the closet in the M. Bath might be optimal for routing both ducts and condensate drain. It may depend on just where the outdoor unit is best positioned, and the length limitations of the refrigerant lines.
You may be mentally overestimating the amount of noise these things make. At low speed (where it'll operate most of the time ) even a 1.5 ton inverter-drive mini-split is quieter than your refrigerator. It's nothing like the air handler noise of a typical ducted hot air furnace or central-air.
"You may be mentally overestimating the amount of noise these things make. At low speed (where it'll operate most of the time ) even a 1.5 ton inverter-drive mini-split is quieter than your refrigerator. It's nothing like the air handler noise of a typical ducted hot air furnace or central-air."
Wow. OK. Yes, I was totally overestimating the noise. We have a brand new furnace in the basement of our current house and I knew that that would not be acceptable in a nearby closet.
Thanks for the help!
No - a mini split does not require an open floor plan. In the ideal situation, the house will be very well insulated and very air tight, so that the heat loss from each room is minimized. When that occurs, less heat escapes from individual rooms whether the doors are open or closed, so less heat is needed to maintain the set temperatures. I've installed mini splits in a four bedroom 2nd floor of a home, with one unit in the hallway and the second in the MBR suite. There have been no complaints, but I doubt this client has monitored the exact temps of the rooms, and I believe they are leaving the doors open during the day. I've also installed three in my not-so-superinsulated old New England farmhouse and have been extremely happy with them. I'm very sensitive to sound & will say we rarely notice the units.
Bob- if you look at the layout of the upper floor with the rooms-off-of-rooms approach to laundry being off the kid-bath, and the walk- in closet being off the master bath, I think you'd agree that a mini-duct makes more sense than a wall-coil at the top of the stairs on this one.
https://onedrive.live.com/view.aspx?resid=9DEE0D7D08E081E6!1328&ithint=file%2cpdf&app=WordPdf&authkey=!ANHx1h-nl5BUhX8
With a mini-duct cassette at ceiling height or vertically mounted in the M.Bath closet with a grille through the wall into the stairwell hall, the hall can be the common return, using partition-wall cavities as jump-ducts for the return paths of the adjacent rooms. With a lowered ceiling in the stairway/hall to route the supply ducts it should be pretty easy for the main rooms.
A soffited duct path along the partition wall of the big walk-in closet to supply the laundry room (and the walk in closet), with the laundry room's return via partition walls thorough the kid's bath would work. The return for the walk in closet could be a partition wall cavity jump-duct into the M.Bath closet that houses the mini-duct cassette. The kid's bath does not need it's own supply duct, since it has conditioned space on all sides except the ceiling, which is a high-R ceiling. The design heat load of the kids bath is less than the amount of heat being emitted by one living-breathing human. The return path may require a grilled door on the kid-bath closet, with a partition wall jump duct into the common stairway hall.
The return for the Master bedroom may need to be partition-wall jump-ducts first into the linen closet, then to the common stair/hall way.
Even though traditionally the duct registers would be located by the windows, in a higher-R house like this and with better than code windows there is no good rationale for doing that. Keeping the duct runs as short as possible is key to maximum efficiency. With the supply ducts near the ceiling level, as long as the return grilles are located either on the far end of the room &/or at the floor the amount of short-circuited flow would be pretty small. With the mini-duct cassette located in the M.Bath closet the longest run will be to the nearest corner of the Kid #2 bedroom, which looks something like 10 feet if you running it on the diagonal.
Thanks for the response, Bob. This is good to hear.
We are still tweaking the floorplan, and have made a few minor changes (moved the bath, added a hall, etc.). I think we are getting pretty close to the final product. See attached below. (Sorry about the trouble with the attachments earlier. Didn't know PDFs wouldn't upload.)
Ok, now that you've changed it all, swapping the location of the master bath and the walk-in closet...
Looks like locating a mini-duct cassette in the corner of the big walk-in nearest the bathrooms (for proximate access to plumbing chases for the condensate drain) would make the most sense.
A non-ducted version wouldn't be able to heat the master bath even if you left all the doors open. As drawn the walk-in doesn't need it's own supply duct, and if there are no window in the laundry area it doesn't need it either, but a very modest amount into the kid-bath would still be good idea.
I'll second Dana's plan.
Hi all,
Thought I would pop in here and give you guys an update. We have tweaked the 2nd floor plan a bit due to the builder's recommendation, so take a look at it (below) and let me know if this changes things. I doubt it does, because it hasn't changed that much, but you never know :).
Also, I received the heat/cool load calculations from our local utility company. I have it attached below in case anyone wants to look it over. I have no way of knowing how accurate it is. All this is way over my head. They came back with a total load of 38k btus for the whole house. I was hoping for less (after Dana threw out the 20k number), but I realize I've got a bigger house with bigger windows than most high-efficiency plans.
Still, if these numbers are correct, the utility company recommends a 2.5 ton heat pump for the 1st floor and a 1.5 ton for the 2nd. These are numbers that fall in line with the "1 ton per 1000 ft" rule of thumb estimate. I was hoping for better, but this is much better than my last house which was sized at 2 tons per 1000, and I think that was actually sized correctly because the A/C ran for hours at at time on the hottest days.
Would the 2nd floor still be a candidate for a minisplit? According to the load information, the upstairs has a heat/cool load of 15k/12.8k. My builder wants to put the 2nd Floor hvac unit in the attic and insulate a mechanical room to isolate it from the outside. I would prefer to keep everything below the ceiling plane, per what I have learned here at GBA. I've got 9' ceilings on the 2nd floor, so I have room to drop the central hallway ceiling and run ducts to the bedrooms. However, if I have to go with a regular air handler, I worry about the noise if it is located in the master closet (plus it would take up space). There is space in the laundry room for something, and it could be far enough away from bedrooms to be tolerable.
I guess the main thing I am looking for is confirmation to continue down this path. I would expect I will get a decent amount of skepticism from my builder and all the hvac subs in our area. They will be pushing for the traditional heat pumps because there isn't much opportunity for them to see houses insulated to this level. The last house my builder built was a super insulated passive house that had just one ductless minisplit for the whole house. He said the designer had to do all the hvac decisions on his own and pretty much the hvac sub just filled the order, shaking his head all the way.
It would be easy to say that I just need to forget the local subs and try to find someone in a bigger market that has experience with this, but I live in a small town without much access to a nearby big market, and I have friend (and future neighbor!) that is an HVAC sub. It's not that these guys are hard-headed and unwilling to learn new ideas, but its just that I have to know enough about what I am talking about to discuss the options with them and also feel confident in my own thoughts that this is what I need.
Thanks for everyone's time and advice so far!
The short form of the heat load calc has no insights, since it doesn't spell out the U-factors used in the calc.
If you subtract out the basement (which they assigned a heat load of zero) you have 3880' of fully conditioned space, and a total heat load of 38,600 BTU/hr @ +13F which is just shy of 10 BTU/hr per square foot. For 2-story house that shape, that's consistent with IRC 2015 code minimum assumptions on the building envelope.
That's also consistent with what I said about code min loads for houses that size back in response #7:
"A tight 3000-4000' code-min house might have a heat load north of 35,000 BTU/hr, but if you pick a shape that's easy to air-seal that doesn't have a lot of thermally-bridging corners & bump-outs, slapping 2-4" of foam on the exterior of that house, an energy heel roof truss that allows 18" of fluff in the attic and using U0.25 or lower windows gets you down to the 20K range, at which point a couple of 3/4 tonners (one per floor) will have plenty of capacity at your likely outside design temp."
Like many pro-forma heat load calculations done by HVAC contractors, it's likely that the utility company assumed code minimum.
If they also gave you the long form. let's have it.
Thanks, as always, Dana. Yes, I remember your comment from earlier, and it was bothering me that I wasn't able to get better results than what you spelled out as just a regular built house.
I talked with them about the extra insulation I was doing, gave them the window specs, and the air tightness goal I was shooting for. I guess that was all ignored. That's disappointing, but I guess the silver lining is that the numbers can only improve if they calculate it correctly.
I will ask for a long form calculation, but I doubt they offer such a thing. This is just the utility offering the service for free, so I guess I was expecting too much from them.
I contacted the utility company and they said they took the higher insulation values into consideration when they ran the calculations, and they only offer the summary report listed above. Any further information need to be done with a licensed HVAC pro.
So, back the drawing board.
Well, I decided to see if I could figure out the manual J calculation myself. I found a nice free website called Cool Calc (www.coolcalc.com) that offers a pretty sophisticated calculator. There was a large learning curve for a novice like me, but after a couple of hours and a few attempts, I think I have a pretty good estimate. At least, it is an estimate that I like better. Whether it is accurate or not is another question.
I think I got the variables in there pretty good, but there was one variable, ELA (Effective Leak Area) that I am not sure what to plug in. They say that ELA = CFM50 / 10, but in the article, "Blower Door Basics", Martin says ELA = CFM50 / 18. Plus, I don't even know what CFM50 figure I should expect. I just made an educated guess (CFM50 = 500) and went on. I am a little nervous though, because that seems to have a big impact on the total load. Regardless of whether I put in an ELA of 27 or 100, the load is better than what the utility has calculated.
See the results below. This isn't a room by room load, but rather the entire structure. I also ran a report isolating the 2nd floor load, to attempt to see the loads on the different floors. So, below, the first report is the whole house and the 2nd is just the 2nd floor.
I'm cautiously optimistic that this is a more accurate report, and hoping that it is not just a self fulfilling prophesy, showing me what I hope to see.
Hey all, popping back in here with another update. I have used coolcalc.com to calculate the room by room loads. The software won't generate a single report with all the individual rooms listed, but it will let you generate reports for each room individually. Instead of attaching all those reports to this post (18 rooms), I have transferred the numbers to a single spreadsheet and attached it below.
I feel fairly comfortable with the outcome. I am obviously no expert when it comes this...not even close. However, the software was pretty detailed and I was able to fill it in pretty easily once I got the hang of the different screens. The only thing I am vague about is the ELA that I mention in the post above, and their max insulation values are a little under what I am using. For example, their max wall insulation is R21 between the studs and R6 on the exterior. I'm not sure why they stopped there, but I am using a whole wall value of R30. Also, the max attic insulation is R56 but I am using R60. I'm not sure how much those little differences will affect the final outcome, but it makes me feel like I am not underestimating the loads.
If these figures are correct, then I assume they are good enough for minisplits? If so, that leads me to my next question of zoning. The downstairs is pretty long from side to side and has two rooms (kitchen and den) that are right in the middle and have high loads. I could get a larger system to serve the whole downstairs but then I'd have long duct runs to the far ends of the house. Could I split the downstairs into 2 smaller zones, maybe with a multi-split system, and have one slim duct serving one side of the house and another serving the other side of the house? There will be sealed basement and crawlspace under the entire house, so running ducts will be easy. As it turns out, both halves of the house are pretty equal in terms of load (6k/8k & 6k/10k).
Also, I had a thought about the 2nd floor... Even though the load and the run distances for the 2nd floor are smaller, would it be a good idea to split it up into two zones also? The house is pretty easily divided with the master rooms in the rear and the kids rooms in the front. 10 or so years from now, the kids will be off to college and I wonder if we could get by with zoning those off or at least down to lower levels. The loads would be 6k/7k for the master rooms, and 8k/4k for the kids rooms and bath. For zoning a floor where you eventually plan to dial back 1/2 the floor, do you need to go with separate outdoor units or can you still multisplit those? I know you lose some efficiency when you have an outdoor unit sized for the whole floor and are only running one head. Just wondering about where that payoff is.
Obviously more zones means more equipment expense. Where do you strike the balance between efficient zoning and payback on extra equipment?
Thanks, as always, for the help!