Zone 7 (Saskatchewan) — new four-season garage / workshop

Apologies if this has been asked before, I have read a lot of similar designs but have not found someone using this same assembly in a very cold climate. Here is the plan:
Exterior to interior:
5/8″ Fiber cement board siding (Hardie Plank)
3/4″ (1×4) wood furring strips (to hold insulation and act as vented rain screen)
3″ Mineral wool (2 layers of 1.5″ roxul comfort board 110, staggered seams). R=4.2*3=12.6
1/2″ Fiberglass gypsum (GP DensElement, with PROSOCO fast flash to act as ARB and WRB). R=0.5
5.5″ (2×6) wood studs with DP cellulose in cavity. R=18
1/2″ OSB with MemBrain (Vapor retarder and second ARB). R=0.6
1.5″ (2×2) wood furring strips (for electrical chase, this will be open without insulation)
1/2″ Drywall with latex paint
Total thickness is 12-7/8″ and an R value of 31.7. Sound transmission should be very low considering the mineral wool, DP cellulose, and drywall attached to furring strips. Did I mention this is a workshop in a residential area and I plan to make a lot of noise? Sound transmission is important to me which is one of the big reasons I want to avoid foam insulation, I need mass to dampen the sound. I don’t trust the durability of EPS or polyiso and XPS is not “green” enough for my liking.
Pros:
-Solid construction with 2×6 frame and OSB shear panels. OSB installed on warm side to prevent moisture and mold issues
-Good R value for northern climate and done with “green” building materials (I hate the over use of that word but you know what I mean).
-Wall can vent to the outside and inside (or is this a con in climate zone 7? We typically only vent to the outside)
-Exterior fiberglass gypsum is moisture and mold resistant and should be OK if it gets wet, can dry to the outside through the mineral wool.
Cons:
-Wall is fairly thick but I believe most energy efficient walls are.
-Likely more expensive than the REMOTE wall or double stud.
-Ratio of exterior to cavity insulation is low (41% exterior insulation), but does this even matter if the assembly can dry to the outside? I have read that 70 to 75% exterior insulation is ideal for foam insulation for climate zone 7, but this shouldn’t apply to mineral wool.
Questions:
1. What are your thoughts for the durability of this wall?
2. Would the MemBrain be required or would taping the seams of the OSB do the same thing for a air barrier / vapor retarder?
3. Any changes you would make to increase durability?
4. Any changes you would make to reduce cost?
GBA Detail Library
A collection of one thousand construction details organized by climate and house part
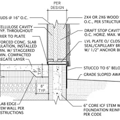
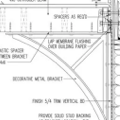
Replies
Craig,
Have you read this article? How to Design a Wall.
In that article, I answered at least one -- probably more than one -- of your questions. I wrote, "Mineral wool insulation can be substituted for rigid foam insulation on the exterior side of wall sheathing. One advantage of mineral wool over rigid foam: because mineral wool is vapor-permeable, it doesn’t inhibit wall sheathing from drying to the exterior. That means that builders can install mineral wool of any thickness on the exterior side of their walls. You don’t have to worry whether exterior mineral wool meets any minimum R-value requirement. (Of course, thicker insulation always does a better job of resisting heat flow than thinner insulation.)"
With MemBrain on the the interior, vapor permeable DensGlass sheathing, a 20+ perm WRB, and rock wool on the exterior with rainscreened siding it would take one heluva air leak to cause a wintertime moisture accumulation problem in that wall!
If you put a hot tub in the garage and leave the top open all the time MAYBE you'd overwhelm the drying capacity, but I doubt it.
Craig. GP is one of my marketing clients. Would you be interested in a possible case study for DensElement? The company is looking for opportunities to document its use in residential applications. Might be a win-win for you. Let me know, and I will put you in contact with the product team.
Just a thought, you can simplify the wall if you surface mount the electrical boxes and wiring. I'm doing that in my garage/workshop in Kenora. As an aside I'm building insulated "carriage house style" doors in front of the overhead 7x9 overhead doors to improve the insulation of that chunk of wall and help with air sealing...both of those are sore spots with an OH door... and my wife likes the look of the carriage house style door!
...
edit...
just another thought from a guy that is definitely not an expert... I am putting 4" EPS on the exterior of my home in Kenora...am planning on ripping 3/4 plywood (not G1S or even treated)... in place of the 1x4 furring... that gives better split control and can be ripped to any width you need... say at inside and outside corners where I'll need considerably wider furring
Tim, I like your idea for the carriage doors. Can you share some of your details? Basic 2x3 framed door with insulation? hinged with weather stripping to help seal up to the jambs? Then inside that, a typical insulated overhead door? I assume since most of these garages/workshops get used very infrequently, it really isn't a big deal to open/close 2 doors (well 3...2 carriage and 1 Overhead)
Steve: I might be interested at a later date. Right now I'm just working through the design and budget with construction planning to start next year.
Tim: I'm also interested to see the details of the carriage house doors. My garage would be large enough for 2 doors but i was thinking of just installing one and have the framing for a second just for future use. That would cut back on energy cost and capital cost since I only need the door to move tools and wood in and out. Plywood furring would be less prone to splitting I would change that. External wiring is also a good option since it is a work shop. I could forgo the smart vapor barrier and just install drywall over the OSB then use a vapor barrier primer on the drywall and make the drywall air tight. That would be fairly easy to do since there would be hardly any penetrations through the drywall and its a single story garage.
Martin,
I did read your article a while back and it was a good refresher, however I became a bit confused after reading what Roxul had to say in their design guide for comfort board 80. From table 1, they recommend an exterior:interior insulation ratio of 0.76 for T=-40C and 40 RH and state:
"If the sheathing layers are very vapour permeable (e.g., ROXUL COMFORTBOARD 80 over fiberboard or gypsum sheathing, and housewrap) then very little insulation value is required outboard of the stud bay. However, while these permeable layers can essentially eliminate vapour diffusion condensation risks with lower exterior sheathing R-values, the risk of air leakage condensation does not drop as much: air leakage may still deliver more water vapour to the back of the sheathing than can be removed by diffusion through the sheathing, and hence condensation could still occur and accumulate.
For important projects or situations in which the design team has little historical experience, investigation using widely available computer models such as WUFI Pro would be prudent if the necessary time and skills are available."
If you look at tables 2 & 3 in the design manual it looks like they recommend 5" of exterior insulation for climate zone 7. It sounds like Roxul still recommends keeping the exterior:interior insulation ratio high in case of air leaks in the interior air barrier but this sounds like an unnecessary safety if a good air barrier is installed with a vapor retarder.
Reading your other article on vapor retarders I could just get away with poly on the inside since i don't plan on having AC in the garage. If I was building a house with AC using this same wall system I would probably want a smart vapor retarder https://www.greenbuildingadvisor.com/blogs/dept/musings/do-i-need-vapor-retarder
Craig. You can reach me through my website at knappcommunications dot com.
Craig,
Surface wiring may simplify air sealing, but check your code - it means using different boxes and expensive shielded wire here.
Ryan; you are right these doors are not going to opened more that once or twice a day... my car lives outside, the ATvs and worksop are inside the garage.
2x6 framing as the garage is 2x6 (on edge to fill the void between the garage face and OH door (I'll dado a channel along the sides and top to allow the existing weatherstrip for OH door to remain. Then its a simple box with 1x6 pine trim on the front(design as you please there are a million ideas out there) glued and screwed to 1/2 plywood (its there for rigidity).. the ply is set back from the front face 3/4 inch..you can either dado a channel (I love to play in the workshop) or build some full length nailing blocks along the sides to secure the ply. I then filled the interior with EPS foam. I designed mine so I could build two 7x9 doors out of 3 sheets of 1/2" plywood. The hinges are 4 1/2 commercial grade ball bearing stainless (amazon) and when I'm done I'll add some decorative strap hinges (amazon).
I will add weatherstrip along the top/sides and bottom, the cter where the doors meet will be a barn/carriage door sliding bolt.
I'll see if I can hunt done the plans but they are dead simple.. mine are designed to be painted and I hope to have them completed in a week or two.
Ryan,
An article from FHB on insulated panels you might find useful:
http://www.farrellhomebuilding.com/Fine%20Homebuilding%20Final%20Article.pdf
Thanks Tim and Malcolm, those sliding doors are very intuitive. Getting a nice tight seal would be tedious. I think the carriage style doors would be more practical for a garage. It got me thinking, you could even incorporate a half width overlay to help seal things up, versus the big joint in the center of the opening.