Zone 6 Wall Assembly – Exterior Insulation Behind Sheathing

I’m planning on building this fall in Zone 6 and haven’t quite nailed down our wall details. Locally, it’s now common to use closed cell spray foam in a 2×6 wall. Insulators generally won’t spray more the 4″ since it is enough for air sealing. That’s great but I’d like more insulation than just 4″. So here is my plan for the wall built with 2×6 normal framing.
LP Smartside
1/2″ rainscreen
Tyvek
5/8″ sheathing (plywood/OSB not yet determined)
2″ XPS – SM exterior insulation
2″ closed cell cavity insulation
3.5″ R12 Fiberglass bat cavity insulation
1/2″ drywall
Will this work well? Are there any ways to improve it? Is there a better option for exterior insulation?
GBA Detail Library
A collection of one thousand construction details organized by climate and house part
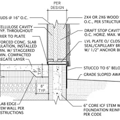
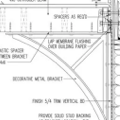
Replies
That wall assembly should perform alright, with an actual whole-wall value just under R-30, using aged values for the foam and not reducing for plates and beams, only for studs. The problem is that while reducing your energy bills, your assembly pollutes the atmosphere with the heavy greenhouse gas emissions of XPS, and likely from the spray foam as well, unless your market is one of the few that has switched to HFO-blown spray foam. The energy savings will never recover the environmental damage. There are many ways to get R-30 performance without using such polluting materials. The simplest for you might be to swap out the XPS for EPS or polyiso, with slight dimensional changes.
However, using three different types of insulation in a 7.5" space is sure to be more expensive than limiting yourself to one or two types, requiring fewer trips around the house. Double stud walls with cellulose insulation have low embodied carbon and perform well if built properly. With offset studs, in 7.5" you could get about R-25, or thicken the wall to 9" to get R-30.
Or frame the wall with 2x8s and wrap the exterior with 1.5" of EPS or mineral wool to get R-30. EPS is relatively vapor-open at that thickness so there should be no moisture accumulation concerns, especially if you add a variable permeance membrane at the interior.
Thank you for your reply. The most common new construction methods here insulate with either spray foam and no exterior insulation, or an inch of foam over the sheathing with 5.5" fiberglass bats. No building codes are applicable as of yet. The majority of builders have only ever built with 2x6 traditional framing. My goal is to build a good quality home that performs better than what the local standard is while keeping it simple enough for local builders to not feel overwhelmed. I should also specify it's going to be a 5000 sq ft oceanfront property with lots of glass.
I could probably swap the XPS for EPS. Though I am set on the idea of spray foam as an air barrier. 2x8 construction is unheard of here. As is many other modern building materials and techniques.
Right now my only other option I'm considering is to scrap the R12 bat and just use 4" of closed cell spray foam plus 2" of XPS/EPS inside of the sheathing. Which I don't know if it makes sense but I think some thermal bridging of the studs would be better than just cavity spray foam alone?
I am sure your local builders are also not familiar with placing XPS between studs and sheathing. Just because something is common or not inspected doesn't mean that's the way it should be done. In fact, the opposite is often true. Even if building codes (aka the worst house you can legally build) are not enforced, they are still a good baseline to follow. (The IRC code that most of the US uses requires wall bracing, which you are not providing.)
Closed cell foam in the wall cavities is gaining you very little thermal performance and decreasing the ability of the wall to dry in the event of water infiltration. I have worked on a lot of coastal homes and water infiltration is an issue. My worst-performing projects included closed cell foam. There are simpler, cheaper, more effective and less polluting ways to provide airtightness--simply taping the sheathing will do the same thing that spray foaming the framing cavities will. In fact it will likely work better.
The builders are familiar with an inch of exterior insulation. Wall bracing? The entire house is sheathed and spray foamed. Does that not add to structural integrity? How is the system I'm proposing any different from ZipR?
The sheathing on the outside provides a solid surface for installing windows. While 2" of foam does add structural issues with hanging the cladding and windows, can this not be offset by a nailing pattern similar to ZipR? And once the spray foam is in place will that not tighten up everything? My neighbors that have all built in the last few years have only closed cell foam as insulation.
I'm not here to argue about codes. It'd be great if they were enforced here. They aren't yet. I'm just wondering if this is a system that could work or are there major issues with it? To me, it is similar to ZipR. If it's too complicated, then my alternative cavity insulation is ccspf. I'm sure there are simpler, cheaper, more effective ways to build it but I'm trying to be involved with the build process. If I'm not, I'll end up with ccspf, no exterior insulation, r5 stem walls, and maybe r10 underslab.
Separating the wall sheathing from the wall framing means that instead of the sheathing directly providing lateral bracing, the nails have to transfer the load from the framing to the sheathing. Zip-R has gone through extensive testing, the foam is adhered to the OSB and they have specific nailing patterns required. Even with that, there is a limit to the lateral load Zip-R can handle: https://www.huberwood.com/uploads/documents/technical/literature/ZS_R-Sheathing_Installation_Manual-R3-12v21.pdf.
I'm not saying that what you propose won't work, just that it is not a code-compliant system. Since building codes represent the worst house you can legally build, even when they are not enforced, they generally provide a safe baseline for construction details. Most conscientious builders go beyond code when possible.
Spray foam is touted as providing shear strength but as far as I know it's not a code-approved system for lateral bracing and I have never seen tables or other calculations that show the lateral loads foam provides in different situations. I have seen many successful spray foam installations, and many failures as well. In fact right now I'm consulting on a failure, a house only a few years old that has extensive water damage and rotted sheathing. Spray foam didn't cause the problems, water and poor flashing techniques did, but spray foam prevents the wall from drying. (On that project, a significant portion of the foam has pulled away from the studs as well.) On another consulting project, a $2M+ house just a few years old, the spray foam did not cure properly and the owner is suing the builder to fully remediate the insulation and replace all finishes.
This is a site for green building discussions. I'll say it again: there is nothing green about filling your framing cavities with closed cell foam. Here's an article that explains why: https://www.greenbuildingadvisor.com/article/installing-closed-cell-spray-foam-between-studs-is-a-waste.
+1 on simplifying. If you want to stick with your design, note that the sheathing can be eliminated (check local requirements for racking). There is also open cell spray foam - good air sealing, insulating effect similar to other cavity fills.
Thank you for your reply, Jon. Open cell spray foam might be the answer for the walls. The choice of system really comes down to local tradesmen. There are very few builds here that would deviate from the local standard. I posted some examples in a previous comment. No codes are enforced but homes here are generally always sheathed. 1" of exterior foam is common when spray foam isn't used. Some newer homes are now done with ccspf but nothing on the exterior to slow thermal bridging. We've specified wood framed windows and that's unheard of here. I don't know any modern homes without vinyl windows within 50 miles. Jaws drop at the idea of wood windows. Same goes for WRBs. Anything but tyvek and typar are hardly every used. While my plan may seem a little more complicated written out, it's simpler for me to explain to the builder than specifying uncommon construction methods or materials.
Deleted
The spray foam in the cavity is barely budging the R value of the assembly. About the only job it is doing is air sealing. You can get that for way less money with taped sheathing.
If you go with 2" of polyiso (or 2" unfaced EPS + smart vapor barrier), it is enough for condensation control in your climate, you don't need any extra SPF in the cavity.
You can use your SPF money and spend it on a bit more air sealing or better insulation (HD fiberglass or mineral wool), either of which will make more of a difference.
EDIT. I just noticed that you want to put the foam under the sheathing. This won't work as the foam will compress. If you want this type of assembly look for ZipR, otherwise the foam needs to be outside of the sheathing.
Is this not the same as ZipR? Doesn't XPS have great compressive strength? My thoughts are now only is the spray foam air sealing, it adds structural rigidity to the exterior foam? Plywood on the outside makes it simpler to install windows.
Similar, but without the required testing. It would work fine - if you build the wall to meet code even if the plywood/OSB wasn't there.
Spray foam does glue things together well, but code won't accept that.
As long as you are bracing the wall by other means (corner brace, let in brace) and your area is not a high wind or seismic zone that requires full sheahting, you could do it. Don't know what trades will say about the non-standard assembly though.
Zip R is simpler without any of the structural issues.