Zone 6 exterior wall insulation question

My location is zone 6.
My timber frame is enclosed with an on-site wrap and strap assembly, the studwalls of which are full dimension 2×5 @ 24″o.c. The exterior of the assembly is insulated with 2.5″ xps, taped and caulked.
My plan was to have dense pack cellulose installed in the cavities behind intello web, but because of some concerns with bulging I’ve gotten some advice to consider open cell foam, which the cellulose installer I’ve been working with offers.
My question is, given the current assembly details is this a viable alternative?
Thank you, Daniel
GBA Detail Library
A collection of one thousand construction details organized by climate and house part
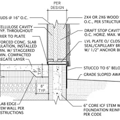
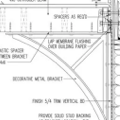
Replies
Hi Daniel,
The short answer is yes, you could use open-cell spray foam in your walls. But many green builders prefer cellulose to any foam products, when possible, as it is one of the most environmentally-friendly insulators.
I'm curious, what's the bulging concern all about in these walls?
As I've come to understand cellulose installation can have a tendency to bulge a small amount, but if sprayed to the correct pounds per square ft. it will be a minimum that rolling will further minimize. In my case, at 24" centers the bulging can be a bit more challenging to minimize. Of the installers I've gotten quotes from, two recommended installing the sheetrock and then drilling holes and blowing cellulose. I won't be doing that. The installer I'm likely hiring never suggested that approach, but when I asked for his opinion admitted that bulging could be more of a hurdle than usual due to the 24" o.c. The timeline for the sheettrock install might further complicate matters: just two of us installing and 1/3 of the total wall space gets wood paneling which will slow things down more yet. Open cell wouldn't present any of these potential issues.
Given my wall assembly and my climate zone there are no moisture considerations/issues?
Hi Daniel.
The specific vapor permanence of open cell spray foam depends on its installed thickness but it is generally vapor-open enough to allow drying in both directions.
Damp sprayed cellulose doesn't bulge.
None of the three installers in my area that offer cellulose will damp spray.
Using 5/8” drywall instead of the more common (for residential use) 1/2” will greatly reduce the chances of bulging between studs, especially with 24” stud spacing. 5/8” drywall also gives you a stronger, flatter wall and better sound deadening.
Bill
Daniel,
I am pretty sure that both cellulose jobs I am aware of were damp fill on the walls. Both used 5/8 sheetrock. One I am sure had bulging to deal with. In any case, with 24" stud spacing I would go with 5/8" regardless of insulation choice. When you say wood paneling, are you talking plywood like products or 3/4 lapped boards. If you try to fight bulging with too thin paneling, the bulges will win every time. Lighting will skim and reveal the humps be they ever so slight.
I would add that 2.5" of exterior xps sounds on the edge of best practice to keep the dew point far enough out for CZ6. For open cell foam to be safest, I would have put more foam outside. The more amenable cellulose will still be vapor open to the inside and buffer any risk of water vapor load on the back of the outside skin. Being timber frame may enhance the buffering , I am not up on the behavior of that type of build. I would be a little suspect of the moisture passage by open cell foam, the foam will not behave like cellulose.
>"I would add that 2.5" of exterior xps sounds on the edge of best practice to keep the dew point far enough out for CZ6. "
---------- and-----
>"My understanding was that 2" of xps was on the edge of best practice for a 2x6 framed wall.
Your understanding is mistaken.
Chapter 7 of the IRC calls out R11.25 MINIMUM for a 2x6 wall in zone 6:
https://up.codes/viewer/connecticut/irc-2015/chapter/7/wall-covering#R702.7.1
At 2" XPS is labeled R10, but only warranteed to R9 @ 20 years, and will eventually hit R8.4 (the same as EPS of the same density) when the blowing agents diffuse to near-zero. At full depletion of the climate-damaging HFC blowing agents 2.5" of XPS runs about R10.5. It's only warranteed to R11.25 @ 20 years (= 90% of labeled R).
It would have been a lot greener to go with 3" of EPS or 2.5" of polyiso, either of which has about an order of magnitude lower CO2e footprint, and comparable or higher R-value over time. XPS is hands-down the least green insulation material in common use in the US:
https://materialspalette.org/wp-content/uploads/2018/08/CSMP-Insulation_090919-01.png
he eventual R10.5-ish performance (or even the R11.25 warranteed performance at 20 years) of 2.5" XPS would be pretty sketchy margin for 5.5"/R20 cavity fill if using only standard latex paint as the interior side vapor retarder, especially if going with open cell foam. which has essentially zero hygric buffering capacity. With only 5" /R18.5-ish cavity fill there's a hint more margin, but it's still pretty close to the edge. With open cell foam all of the wintertime moisture load would be carried by the structural wood, whereas cellulose will safely share/buffer & redistribute the wintertime moisture load with the structural wood without damage or loss of function. If open cell foam using vapor-barrier latex (~0.5 perms) would be cheap insurance, but with cellulose it wouldn't be needed.
Dense packed to 3.5lbs cellulose may ( but not always) put some bulge on half-inch sheet rock with 24" o.c. framing. But 5/8" or 3/4" wallboard would not have that problem.
Thanks Dana. I actually used all reclaimed xps from a link you had offered me several years ago when I was questioning my engineer's specs.
My question regarding the bulging isn't if the wallboard would bulge after installation but if the bulging would make installation a difficult challenge.
Deleted
Sorry to revisit this, but the numbers have been bugging me. If my 2.5" exterior xps is performing at r10.5 (its eventual low), that r value will offer at best barely the margin needed for protection against dew point moisture accumulation in my 5" cavity. My engineer had originally spec'd 2" of xps and a 2x4 cavity, and when I bumped the cavity to 5" is where I went wrong regarding dew point margin (2" xps at a low of r8.4 would have just exceeded the mimimum of 7.5 for a 2x4 wall).
Given these numbers it would **theoretically** make better sense for more than adequate dew point control to only insulate the cavities as much as a 2x4 wall would allow. My problem now is that I bumped up the framing, already installed the exterior foam and siding, and have to contend with marginal dew point control.
Just need to know that I'm understanding this correctly.
Wood paneling is 3/4" cherry and hard maple. And it's actually 5/8" blueboard that's going up for plastering.
"I would add that 2.5" of exterior xps sounds on the edge of best practice to keep the dew point far enough out for CZ6. For open cell foam to be safest, I would have put more foam outside."
My understanding was that 2" of xps was on the edge of best practice for a 2x6 framed wall. My studwalls are an actual 5" and I bumped the xps up to 2.5 after getting advice here several years ago regarding this issue.
Your input regarding needing more exterior foam for the use of open cell to be safe speaks directly to my question. At this point the house is sided, so no chance of adding additional exterior foam. So, given my climate zone and current assembly open cell foam would present moisture issues?
Deleted
Daniel,
I will risk raising the dander of Dana and say that you are likely not in much trouble. There will be relatively few days where you will be hitting the exact combination cold and vapor in the wall that results in significant moisture condensing out. Dana correctly pointed out that for the 5" wall thickness your balance relative to the exterior foam would put you just in "correct ratio". I don't usually fuss quite so hard over the 1/2" difference for the frame depth.
I used a huge amount of XPS on my build, albeit recycled. Someone else committed the crime against the world first and I kept it out a land fill. Karmic balance I guess. If it is any consolation (and a dark consolation at that), in the twenty years it will take to leak out your current 12.5R value, climate heating will probably have you in one lower CZ category. I have already seen a ten degree shift in winter temperatures where I am. I will be planning for air conditioning in my next build for a family member, who I hope will be in the home for at least 20 years. We were screwed climatologically over 30 years ago. I think a Mr. Hansen warned us. Exxon, Mobil, BP and many others have done more harm than you or I.
If you do anything, pack the 5" properly and make a bit of extra effort to seal the drywall and especially the board paneling. A smart vapor material behind the boards is one way. I would just use 3/8 drywall, taped, skimmed, and primed with PVA. Just check your detailing for interference with other surfaces and electrical box setting. I personally think the air tight drywall and electric boxes is wrong way round thinking. There shouldn't be air exchanging with the great outdoors behind your drywall. If you have done good air sealing on the skin under the foam, then you have already committed to a vapor open interior. If you don't have a koi pond in the middle of your living room, or raise bromeliads for a hobby, you can relax. The small gaps around fixtures and outlets are trivial in most contexts.