Zone 6: A straight forward and affordable wall assembly… does it exist?

Zone 6 and for a year we’ve been researching options for wall assemblies for a future home. Admittedly, still feeling just as confused. What I have learned is that there’s no such thing as a “perfect” wall and if there were, it would be beyond what our budget would allow and local contractors have experience in (ie. requiring exterior insulation like rockwool that’s 2-4” thick).
So, my question… Is there a wall assembly for zone 6 that won’t break the bank and is straight forward for contractors inexperienced with the green building and design? Currently, we’re looking at three options but would really appreciate any guidance and refining to choose the wall we will ultimately build. As a note, condensation and moisture leading to mold is the number one things we want to avoid as a family member is highly reactive to mold.
Assembly Option 1: Vertically hung black corrugated siding, Coravent rain screen, uninsulated zip sheathing, 2×6 walls, dense packed cellulose, vapor smart barrier like intello, drywall or plaster, paint.
Thoughts: The main concern here would be cold sheathing and condensation in the wall. Also some concern that the Zip would not allow enough drying to the exterior and may be best swapped for plywood and a self adhered WRB.
Assembly Option 2: Vertically hung black corrugated siding, Coravent rain screen, insulated Zip R6 sheathing, 2×6 walls, dense packed cellulose, vapor smart barrier, drywall or plaster, paint.
Thoughts: This assembly would meet the 20+5 insulation recommendations for our zone but would also limit drying to the exterior more than the previous option. Maybe the interior smart membrane prevents this from being an issue?
Assembly Option 3: Vertically hung black corrugated siding, coravent rain screen, uninsulated zip sheathing, 2×4 double stud walls with a 3” gap – or – 2×6 walls with 2” horizontal strapping, dense packed cellulose, vapor smart barrier, drywall or plaster, paint.
Thoughts: We have not yet quoted this option and there is concern of the double stud wall and added insulation cost. Even though the insulation is better inside the walls, unsure if the cold sheathing could still cause issues. If budget allows there would be the option to add the insulated Zip R6 but again you have the drying concerns and possibly the percentage of exterior insulation to interior being thrown off requiring a higher ZipR product.
I feel at this point we know just enough to be dangerous and are stuck in analysis paralysis. Any guidance would be greatly appreciated.
GBA Detail Library
A collection of one thousand construction details organized by climate and house part
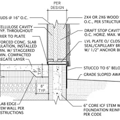
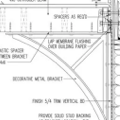
Replies
Emil,
#1 was until recently the standard wall in zone 6 - but usually sheathed with either OSB or plywood. The Zip is the same perm as those except it doesn't open up as much as plywood when damp. But barring water intrusion into the walls, doesn't experience either condensation or wet sheathing problems - especially when coupled with a rain-screen. It's problem-free wall, but doesn't even meet code minimum levels of energy performance in most places now.
#2 Slightly less forgiving due to the low amount of exterior insulation, but is probably the most common wall now in eastern Canada, and performs well.
3. Both are good options limited only by budget. Double-stud walls with cellulose and rain-screens simply don't experience moisture problems with their sheathing - unless you add exterior foam, so the Zip-R should be off the table.
In terms of assemblies that are straightforward and have pretty good performance, you might also consider framing with 2"x8"s. What I've started calling an Akos wall.
I love the 2x8 idea! I can see this being very straight forward for the builders while also giving us the added insulation. What are your thoughts of doing option 1 with the 2x8 walls and switching out the wall insulation for rockwool’s R30 product? Maybe even 24” OC to save a little on materials? Would this still be a quality assembly that would prevent any moisture issues and condensation in the walls or should we stick with dense packed cellulose?
2x8 would work just fine. This is pretty close to your assembly but with R28 batts:
https://effectiver.ca/calculator/wall.php?id=10795
Montreal is about Zone 6.
You want the 24OC not just for cost but thermal performance. The wider stud spacing reduces the thermal bridging of the studs so you get slightly higher assembly R value. Win/win on both cost and performance.
For the sheathing ZIP/OSB/CDX will all work fine with your corrugated cladding since it is self venting.
The insulation can be any fluffy product, dense pack cellulose is the greenest option plus it tends to make for better sound isolation.
Emil,
It would yield a well performing wall from both energy and moisture perspective.
Some thoughts I had on your approach overall:
A) A wall assembly does not HAVE to dry in both directions. It is considered safer if it is able to do so, but it is not absolutely necessary.
B) The problems about interior air condensing on the cold inside of the sheathing drops dramatically when you install an interior (preferably smart) vapor barrier. Since all of your designs have that installed you really shouldn't be worried about this issue. The vapor barrier will stop humid indoor air from reaching the sheathing, and your WRB on the outside will stop humid outdoor air from reaching the inside of the sheathing.
I don't think I would do exterior insulation AND an interior vapor barrier - I would be worried it would not allow enough drying to the inside in this case.
Matthew,
"I don't think I would do exterior insulation AND an interior vapor barrier"
Definitely a good idea if you have thick enough foam, but if you go with less, the interior vapour-barrier is what keeps the wall safe:
https://www.greenbuildingadvisor.com/article/rethinking-the-rules-on-minimum-foam-thickness
Have you read this article?
https://www.greenbuildingadvisor.com/article/how-to-design-a-wall
What are your goals for this house?
In most places zone 6 option #1 would not be code compliant at R20 but a very safe wall.
What is the appeal of Zip+R for you? I don’t see paying a premium for something that weaken the building.
Is Zip +R6 allowed in zone 6? Seems like Zip+R12 would required with a 2X6 wall at R20.
Option #3 is great but tends to be expensive.
Consider asking for bid of option #1 with R12 of exterior foam.
I like the 2x8 idea.
What are the local production builders doing to meet code? That will be the low cost option.
If the real goal is the lowest cost of ownership build a BEopt model of the house enter the cost for all the options and let the math pick the winner.
https://www.nrel.gov/buildings/beopt.html
Be sure to find the BEopt training videos on YouTube.
Walta
Currently the code in our area only requires a 2x6 wall with R20 or more insulation. It does not require exterior insulation but does require an interior vapor barrier. This is why the smart vapor barrier is planned in every option. Our codes are not up to date with current recommendations yet. We like the 2x8 option too as it looks like rockwool has a R30 product that would fit in this space. If we did the 2x8 recommendation, we would essentially be building option 1 just with a thicker wall.
The reason I was trying to include zip sheathing is because it’s a product our builder uses all the time. I was hoping if we used their sheathing preference, it would still have drying ability (as long as we don’t use the insulated version) and because the builder is familiar with it, the seams would be taped appropriately and we’d have less mistakes to watch for. I could request plywood and a self adhered WRB but if it’s not something they do often, the concern was mistakes being made.
I like My Zip sheeting but I do not see the value in Zip+R product.
The real question is what are your goals.
Rockwool is another premium priced product that I fail to see the appeal. Ok the R value per inch is 12% better. But it is batts and the installation is never perfect. Damp sprayed cellulose fill every gap with a greener product.
My wild guess is if you built the BEopt model the walls with over R20 would recover the higher cost but a lot of that depends on how much extra your builder needs to charge because it is above code and unusual.
The BEopt model will help when you pick windows, HVAC and attic R values
Walta
Lot of good options here. Our team has two preferred “pretty good wall” assemblies:
Starting from exterior:
1) siding, 1x3 rain screen battens, 2” mineral wool, mechanically fastened WRB (vapor open), CDX with taped seams, 2x6 filled with wood fiber, smart vapor retarder, interior finish
2) siding , 1x3 battens or drainable WRB (vapor open), cdx with taped seams, 2x6 exterior wall, 2x4 interior wall (staggered layout from exterior wall), blown in wood fiber or cellulose, smart vapor retarder, interior finish.
Option 2 can be thickened for more r-value but our budget version is 9” thick.