Zone 5 building envelope question

Building a new construction home for immediate family in the Chicago suburbs. Home is about 3600sf plus basement. With ultimate protection against mold/rot in mind and researching this site as well as chatting with numerous product salesmen for hours on end there’s still some unknowns. Here is the building envelope from the exterior side:
1. Brick veneer
2. 1″ space for drying
3. 1.5″ rockwool comfortboard to keep sheathing warm in winter
4. WRB. 2 options here would be
– better vapor permeability with products such as Mento 1000, Delta vent s, Siga Majvest 200, Another option is Tyvek stuccowrap with its small air cavities to increase the drying potential with comfortboard being pressed against it. Before applying any of these the idea is to tape all plywood seams for air.
– self adhered products such as Adhero, deltavent sa ect.. Adhero is only 11 perms (which seem too low) and deltavent sa is about 50 perms (proc B). Majvest 500 is about 24 perms. Due to numerous brick ties this self adhered option was recommended, but is it necessary?
5. .5″ cdx sheathing
6. 2×6 wall filled with rockwool
7. Would you recommend doing a vapor retarder here since rockwool is unfaced? If so would you go with Intello or membrain or something else? Worried a bit about summer humidity which is really high in these areas. All these options are costly and budget limited, but will do whatever it takes will keep the walls dry.
8. 5/8 Drywall
GBA Detail Library
A collection of one thousand construction details organized by climate and house part
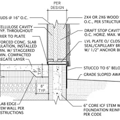
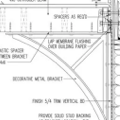
Replies
Since you are asking for ultimate, use fully adhered WRB and taped Intello on the interior. And if possible, more exterior mineral wool.
Some info on WRB perms here (I'd use 20+ perms).
Deleted
Would you go without the vapor retarder? If so, would it be better then to go with a more or less vapor permeable wrb?
Code requires a vapor retarder. You could use paint, but Intello is "smarter" and makes a good interior side air barrier.
IECC 2021, which will be adopted soon by Illinois, will requireR20 in cavity + R5 continuous exterior (or about an R22 for total assembly if you go the U-Value route). So your proposed assembly will be a code compliant wall. I’d go above code, if it’s financially feasible, increasing the thickness of the exterior insulation or considering a polyiso (unless you have embodied carbon priorities).
I’m told self adhering WRB is almost always better than mechanically fastened.
People also seem to really like the intello smart vapor barrier on the interior face of the stud. Service cavity if you can so that you do not penetrate it.
Hope this helps!
-Scott