Zone 4 Build–Bottom to Top

Hello all
I am building a new home in the mountains of western NC, Zone 4. Four seasons there, lots of rain. We will be building on a 31% grade with one main level and one lower level(for some reason they hate to call them basements there!). If you don’t mind, I would like to start at the bottom with my proposed build and work my way up. I wanted to get this all figured out before I go to the architect and builder.
1) Footing will have a capillary break–likely Henry CM100. I hope we can do a slab for the basement vs. a crawl space. If slab, then I plan on 2″ of dense foam board(XPS vs. EPS, and what type of EPS?) underneath and between slab and foundation. Should it be termite resistant foam? Any recommendations on a strong moisture barrier–i see good comments about 15mil Stego vapor barriers?
2) Poured basement walls with peel and stick at junction of wall and footing, either sprayed waterproofing or peel and stick up the outside of the wall, dimpled drainage board outside of that. Two inches of closed cell spray foam on interior of basement walls making sure to seal area around slab perimeter thermal break. Regular 2×4 walls inside of that +/- roxul for sound purposes.
3) Closed cell foam at rim joist
4)Walls will be staggered stud on 2 x 8 plates. All walls and sill plate will be EPDM gasketed along with Contega HF sealer. I plan on 2″ of closed cell foam on the plywood sheathing(stops any worry of condensation) then dense pack cellulose to fill the rest of the space. Plywood sheathing, Solitex Mento housewrap, battens for gap, then cladding. Peel and stick at wall to foundation junction, as well as over top of wall.
5) I would prefer a conventional vented attic, in which case I will have the perimeter spray foamed, then pile on the cellulose. If I have a cathedral ceiling, I would sheath it in plywood, then add a nailbase layer of at least R-15 and then R-34 of open cell foam underneath. If the outer foam is thicker, I will make the inside insulation thicker to keep that 31%/69% outside/inside insulation ratio. Where do I put the peel and stick in such a situation? On the inner sheathing, the nailbase board or both?
That’s my initial plan subject to modifications. I would appreciate all comments. Thanks!
GBA Detail Library
A collection of one thousand construction details organized by climate and house part
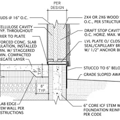
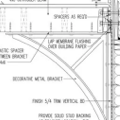
Replies
1: For basement slab foundations, in your climate 2" of 1.5lb density Type-II EPS is adequate for non-heated slabs, but 3-4" make sense if the slab is being used as a radiant heating radiator. Termite resistance can be important in high infestation areas, but measures other than using only treated foam may be used. (copper clad plastic sill gasket materials at the right locations can be effective.) Using the same 2" of EPS between the slab edge & foundation walls, with copper clad sill gasket under the interior studwall & wall foam on all the way to the foundation wall, should work. (Using copper flashing in this location would work, taking a small thermal performance hit from the thermal conductivity of the thicker copper.)
2: Using only sprayed closed cell foam for insulating on the interior of basement walls can be expensive, and (in most cases) comes with a high environmental impact from HFC blowing agents. Even a half-inch foil faced rigid polyiso provides sufficient dew point control for up to R15 of rock wool in a studwall (but 3/4" or 1" is even better.) Polyiso is blown with very low-impact pentane as the blowing agent, and foil-facers are dead-easy to air seal with purpose made foil tapes.
3: An inch of closed cell foam to seal & protect the sill & band joist is enough dew point control for up to R23-R25 rock wool or fiberglass.
4: Staggered studs on 2x8 plates is not buying a very high performance assembly for the money, complexity, and wall thickness.The 2" of closed cell foam is both more expensive and less green than 2" of polyiso. A standard 2x4 wall with 2" of foil face polyiso (on either side of the wall would be higher performance at a thinner wall thickness, even if it meant adding 1x4 furring on the interior for mounting wallboard.
5:The peel 'n' stick membrane goes on the structural roof deck, which should be part of your continuous "all six sides of the cube" defined primary air barrier.
Kevin,
I think your wall design is a little odd. Here is a link to an article on walls: How to Design a Wall.
If your attic is vented, you don't need any spray foam. You just need raised-heel trusses and plenty of cellulose. (Of course, you need to finish air sealing work before you begin insulating.)
@Dana -- I will look into the copper clad sill gasket. I think I read about that with the BSC guy talking about voracious Australian termites. The foil faced polyiso is a good idea for the basement wall. is there an adhesive specially made for this?
@Dana and @Martin--I spoke with the builder and architect about various walls, insulation, thermal bridging, etc. Both hesitated on exterior foam. The architect did his own house that way, and he would not do it again. He said the noise from expansion and contraction is terrible. His words, "It moves." The builder is more concerned with details and ease of install. The staggered stud wall was a compromise, allowed ease of construction, allowed me to use plywood sheathing(i would really rather not use OSB anywhere), and had a high R-value. The spray foam was to combat cold sheathing issues. I saw it detailed here https://basc.pnnl.gov/resource-guides/double-wall-framing#quicktabs-guides=1 and at BSC ( https://buildingscience.com/documents/enclosures-that-work/high-r-value-wall-assemblies/high-r-wall-double-stud-with-spray-foam-wall-construction ) as reasonable ways to avoid any condensation issues in thick walls(the example is double stud wall, but the same principle holds.)
"The standard double-stud wall concept can be improved through the use of closed-cell spray foam (ccSPF) installed directly against the exterior wall sheathing. The remainder of the framing cavity is filled with loose-fill fiber insulation such as cellulose or fiberglass. This is described as a hybrid insulation strategy (Lepage, Schumacher, and Lukachko 2013). In this example, high-density spray foam provides increased air sealing and moisture protection, decreasing the risk of wintertime condensation on the interior side of the exterior wall while less expensive cellulose provides additional R-value."
So I was trying to find the happy medium. Perhaps I will revisit this with the builder.
As for the roof, if the peel and stick goes on the sheathing layer closest to the rafters, do the roofers then just use roofing felt on the nailbase? Could they do another peel and stick layer? Taped seams? I really don't want any leak issues up there. My current house built in 2004 has had pipe penetration flashings fail(rubber is no good--only lead in the new house!) as well as leaks from poor chimney flashing.
Interior polyiso is dead easy if you plan for it, with no structural or wind loading issues to deal with.
Foam board construction adhesive is a standard product, made with solvents that don't compromise polyiso or polystyrene foam board.
Closed cell spray foam on the interior doesn't combat cold sheathing- it only makes it colder, and limits drying capacity toward the interior. Closed cell foam is a class-II vapor retarder, and while it prevents excessive moisture accumulation in the sheathing from interior moisture drives during the winter, in your climate zone that's only an issue when there isn't sufficient drying capacity toward the exterior. But if you're building using high permeance Solitex Mento on the exterior along with a vented gap between the sheathing and siding you have PLENTY of drying capacity toward the exterior, and don't need the low permeance foam. The back vented siding over plywood or OSB sheathing fully meets the IRC chapter 7 definition of "Vented cladding over wood structural panels" . That's even good enough even for zone 5A, and PLENTY good for zone 4A. See Section R702.7 in the code:
https://up.codes/viewer/int_residential_code_2015/chapter/7#R702.7
https://up.codes/viewer/int_residential_code_2015/chapter/7#R702.7.1
If anything, adding the 2" of closed cell polyurethane reduces the drying capacity of the assembly as a whole, by reducing the drying capacity toward the interior.
It would cheaper, more air tight and FAR greener (using less total polymer, and no HFCs) to just do the whole thing with 7.25" with half pound open cell foam, and skip the dense packed cellulose.
It's greener still (but may be more expensive than open cell foam) to air seal the framing to the sheathing with polyurethane caulk and go with just dense-pack or damp sprayed cellulose alone, paying a bit more care about air sealing the wallboard.
Both OSB and CDX are "smart" vapor retarders, that become more vapor open when the assembly is damp. When the sheathing is dry its less than 1-perm, whereas interior latex paint is 3-5 perms. The higher permeance of the paint keeps it from trapping moisture in the wall during the cooling season, even though some moisture diffusion will make it through the sheathing. But the assembly can dry in both directions. You DON'T want to use foil or vinyl wall paper, or polyethylene vapor barriers, since that would cause moisture to accumulate during the cooling season.
If interior foil faced polyiso is used it only drys toward the exterior since the foil facers block vapor diffusion. The only condensation concern then is in the summer, if the there isn't sufficient R value in the polyiso to keep the exterior side above the dew point of the outdoor air in an air conditioned house, but unless you're keeping it 45F inside that takes less than an inch of polyiso.
Using standard #30 felt on the nailbase as an underlayment for the shingles is fine.
Kevin,
Q. "The architect did his own house that way, and he would not do it again. He said the noise from expansion and contraction is terrible."
A. I have no idea what the architect is talking about. (Nor do I know if the architect did his own installation, or whether he depended on a contractor, or what the contractor did wrong.) All I know is that I live in a house with exterior foam, as do hundreds of GBA readers, and I have never heard of terrible noises from expansion and contraction (unless you are talking about metal roofing, which is an entirely different story from exterior rigid foam).
As Dana Dorsett accurately explained, closed cell spray foam on the interior side of the sheathing doesn't address cold sheathing issues -- all it does is to create an air barrier and vapor barrier to prevent indoor humidity from accessing the cold sheathing. (An approach that, admittedly, works, at an environmental cost.)
Q. "If the peel and stick goes on the sheathing layer closest to the rafters, do the roofers then just use roofing felt on the nailbase?"
A. That would work.
Q. "Could they do another peel and stick layer?"
A. I don't think it's a good idea to overuse peel-and-stick, since peel-and-stick is a vapor barrier, and since peel-and-stick complicates the lives of roofers when it's time to re-roof. Limit your use of peel-and-stick to situations where it's needed. If your roofing is properly installed, you don't need to plan for leaks.
Q. "My current house built in 2004 has had pipe penetration flashings fail (rubber is no good--only lead in the new house!) as well as leaks from poor chimney flashing."
A. Unfortunately, it sounds like your house was roofed by an ignorant roofer (a fairly common figure on most job sites). Take the time to find a roofer who knows what he or she is doing -- someone who understands flashing.
Two quick points. One is that if exterior foam is what makes most sense, except that you have people on your project team who are against it for strange reasons, it might be worse trying the idea of mineral wool boards on the exterior. In addition to not being foam, for people who don't like foam for whatever reason, it is best of both words for keeping sheathing warm and dry: it keeps it on the warm side of some insulation, and it allows drying in both directions.
The other is that I think that lead flashing is too toxic to be considered green, and copper is a better choice for masonry chimneys. But finding someone skilled in copper flashing is even harder than finding someone skilled in lead flashing.
I have seen many questions about rainscreens. If my house is wrapped in Solitex Mento and furring strips used, will I need any additional rainscreen? Seems like I would have a nice air gap for drying and a WRB for the water to run off of as is. As for furring strips, I see people cutting down pressure treated plywood to use. Does it need to be PT? 5/8"? 1/2"? 3/4"?
Kevin,
I'm not sure what you're thinking of when you use the word "rainscreen." But if you have a WRB and furring strips that create an air space between the siding and the WRB, you already have a rainscreen.
For more on this topic, see All About Rainscreens. The article explains why furring strips don't need to be pressure-treated.
A rainscreen isn't a material, it's a construction type that separates the siding from the drain plane (your Solitex Mento) with a vented air gap.
That type of construction is now required by code in cool rainy western British Columbia, but is a good idea in most areas that get a decent amount of rain. The air gap is an excellent capillary break, and with any amount of venting to the outdoors it speeds up the drying rate of any moisture blown through the siding, and evens up the drying rate of the siding itself, reducing warping/cupping and paint failures of wooden siding. It also meets the IRC definition of "Vented cladding" in chapter 7:
https://up.codes/viewer/int_residential_code_2015/chapter/7#R702.7.1
It does not need to be pressure treated. It's common to use 1x4 furring which delivers reasonable flatness and good fastener grip for the siding, but anything 3/8" and up (10mm, really) would meet code even in B.C.. Ripping OSB or plywood for the furring needs more fasteners for the furring to keep it from bowing. In order to provide sufficient structure for hanging the siding it needs to be through screwed in to the studs, not the sheathing. With 1x4 furring you can get away with timber screws 24" o.c., but with flexier furring it'll have to be much tighter to provide reasonable flatness.
I'd see if you can take another pass at your builder and architect about exterior foam. If they really really don't want to do it, then others in this thread have offered some alternative ideas. But exterior foam really isn't that weird, especially when it's not very thick.
Something like this seems like a very standard way to build a wall:
- Interior gypsum board
- 2x6 @ 24" O.C. with cellulose
- Plywood or OSB, seams taped (this is your primary air control layer).
- 1 1/2" polyiso or EPS (this is more than thick enough for your climate zone to eliminate condensation issues)
- WRB (solitex mento, tyvek, whatever)
- 1x4 furring strips
- Cladding
From my understanding, with only 1 1/2" of foam you don't have to significantly alter your window details, etc.
Mind you, at 24" o.c. spacing, in zone 4A even 2x6/R20 + R6 c.i. is a good enough wall to hit Net Zero Energy with a PV array that fits on the roof, now that typical residential PV uses 18-20% efficiency panels. See Table 2 of this document from back in 2009, when residential PV was in the 13-15% efficiency range, and cost 2.5-3x more than it does in 2017, and better class ductless heat pumps are now in the HSPF 13+ range, up from HSPF 10-11 back in 2009:
https://buildingscience.com/sites/default/files/migrate/pdf/BA-1005_High%20R-Value_Walls_Case_Study.pdf
The R25 whole-wall performance called out for zone 4 in that document is essentially Brendan Albano's suggestion. But with 18-20% panels the PV doesn't take as much free rooftop space. The 24" o.c. 2x6/cellulose + R6 continuous polyiso will come in somewhat ahead of R20, and with the technology (and cost) improvements of PV and heat pumps over the past 8 years
Where it's economical and easy, go ahead with the zone 4 recommendations in Table 2, even though with a well thought out (and BeOpt simulated) design you can probably still get to Net Zero Energy with the zone 3 row recommendations. Stay with R15 for the basement walls or even R20 if it's mostly above grade, and stay with 2" of Type-II EPS (R8.4) full coverage under the slab. A 2.5" + 2.5" EPS insulated concrete form might be cheaper & easier than hitting R20 fully inside the foundation walls, and would eat up less interior space.
If the architect or builder can't deal with an inch of exterior foam, most can deal with 1.5" ZIP-R sheathing delivering similar performance, but is easier for crews previously familiar with standard OSB or CDX sheathing to assemble properly.
Dana had suggested rigid foam edge strips applied to the framing on the interior side. He linked to a Fine Home Building article as well,but I can't find it. That might be more acceptable to a foam phobic builder.
Steve,
The Fine Homebuilding article is titled "Breaking the Thermal Bridge." Here is the link:
Breaking the Thermal Bridge.
The method is called the Bonfiglioli Approach. If you enter "Bonfiglioli" into the GBA search box, you will find several Q&A threads in which this approach is discussed.