Zip Wall, air gap, and unprimed cedar shingles

Hi All,
I am about to build an 1800 sqf home right on the coast in RI. The general framing plan is 2×8 studs 24″ oc with 1/2″ Zip.
The insulation will be 1.37″ closed cell foam right up against the sheathing then high density fiberglass bats. Should be about r30.
(I understand this insulation and framing combo is not exactly logical. Its a compromise between several parties its not changing.)
Siding is unpainted cedar shingles over 1/4″ obdyke cedar breather.
My concern is solar driven moisture wetting the OSB zip wall. Building Science Corp recently published an article describing how solar driven moisture can rot OSB siding. I believe that zip wall is sufficiently permeable to allow drying,and the obdyke breather is a good start. I am slightly concerned that the sheathing will stay very cool and therefore damp because of the thickness of the walls and have no way to dry inward.
Do I need a larger air gap?
I had also been considering using a felt paper WRB as cheap insurance, but I am coming around to thinking this is unnecessary and will only prevent drying.
Thanks for your thoughts,
Thorson
GBA Detail Library
A collection of one thousand construction details organized by climate and house part
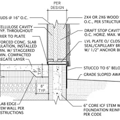
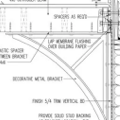
Replies
Here is the article FYI
https://buildingscience.com/documents/building-science-insights/bsi-061-inward-drive-outward-drying
The linked article indicates a min rain screen air gap of 1/4" which matches your 1/4" obdyke cedar breather. I don't see an issue. Besides its the gap in the cedar breather that allows the OSB to dry. That's why we have the gap to begin with.
IMO felt paper wwould be an unnecessary expense.
The ZIP is OSB but with an outer water resistive barrier layer. I think that would protect against vapor drive (assuming the joints are taped) without felt paper. Are spraying 1.37 inches because of the 2 by 8 framing? That seems like a pretty specific metric. How did you calculate it?
How does one even install ' ...1.37" closed cell foam..." , anyway?
And what purpose is it intended so serve here?
At 1.37" the vapor permeance of most closed cell foam would meet Canadian code definition of a "vapour barrier", or the technical definition of a Class II vapor retarder. Any drying toward the interior is significantly impeded (even though it's not a particularly risky stackup in RI.)
"I understand this insulation and framing combo is not exactly logical. Its a compromise between several parties its not changing."
The insulation specifications are really going to have to change, since there is no way to do a quality installation as-described. To be clear...
...2x8s are 7.25" deep, so with 1.37" of closed cell foam you'd be left with 5.88" deep cavity for the "... high density fiberglass bats...".
Since standard high density R21 fiberglass batts have manufactured loft of 5.5", it isn't sufficiently thick to fill the cavity, (it will leave a 3/8" nominal gap) and there WILL be voids & convection paths, unless a thicker batt is installed. unless the batts were 8.25" high density R30s, which would be a total PITA to install, which is a very high compression.
If you're committed to 2x8 framing with flash'n'batt approach, install a nominal 2" of closed cell foam + high denstity R21s to fill the remaining 5.25".
Mind you, there is as much polymer in 1.37" of 2 lb foam as there is in 5.5" of half-pound open cell foam or 4" of 0.7lb foam. Installing 4" of 0.7lb foam would leave 3.25" for batts, and you could use R15s.
But there is more polymer in 2" of closed cell foam than a full cavity fill of half-pound foam, and only slightly less than 7.25" of 0.7 lb foam (~ R30).
At 7.25" even 0.7lb open cell foam is 5-8x more vapor-open than 1.37" of closed cell foam- the sheathing can dry toward the interior, yet sufficiently vapor tight that in conjunction with standard latex paint on wallboard it's probably going to be moisture safe in a RI climate. A WUFI simulation of the north walls might be necessary to test that thesis- coastal RI is the very warmest edge of zone 5A. In zone 4A the IRC doesn't require vapor retarders other than latex paint, and it's probably not going to be necessary here either especially with air-tight cavity insulation such as open cell foam.
Or, worst-case, one could use a variable permeance membrane type smart vapor retarder between the wallboard & cavity foam. If the sheathing ever reaches rot-levels of moisture, the smart vapor retarders become vapor open, allowing the moisture to dry toward the interior. That's a cleaner-better installation, and probably cheaper too. Many 0.7lb foams can be safely installed at 7-8" thickness in a single pass, but not all. Check the vendor's specs.
Thanks for your comments everyone. I wish I could come up with a reason to install 1.37" of foam. but I can't. It's a typo. I meant to type 1.75" which makes it all better.
Dana: thanks for your comment. The insulation can change. The 2x8 framing is here to stay, and I think its a silly choice personally.
The closed cell foam seems to me like a redundant air barrier and that's part of the reason I am concerned about making my air gap bigger.
I will absolutely look into the open cell option, especially if the cost is similar.
Thanks,
Thorson
Three inches of open cell foam makes as-good or better air barrier as a couple inches of closed cell foam, and open would provide an order of magnitude better drying path.
Nobody will quote you closed cell foam in fractional inches, so you're looking at 2" of closed cell foam. A few miles up the Blackstone in MA that will run about $2 per square foot. The same $2 would buy you a full 7.25" cavity fill of half-pound foam (R27), but 0.7 lb foam would run ~$2.50 or a bit more per square foot for 7.25".
The cost is almost certainly going to come in UNDER the 2" closed cell + R15 batt solution, even if you allowed an additional 15-20 cents per square foot for a layer of 2mil nylon as a smart vapor retarder ( eg Certainteed MemBrain- probably not really needed, but could be cheap insurance) under the wallboard. The IRC prescribes a Class-II or tighter vapor retarder in zone 5A, so a smart vapor retarder might be necessary to meet the letter of code while still allowing high rates of drying toward the interior. But with air-tight cavity fill the risk is going to be low or non-existent unless you keep the house at a very high humidity level in winter. At 2" closed cell foam is 0.4-0.6 perms, but 7.25" of 0.7lb foam is over 15 perms. MemBrain is under 1 perm when the humidity in the cavity is low (which it will be during the winter, when the sheathing is colder than 40F) , but is over 10 perms at humidity levels that could support rapid mold growth. Intello Plus is a similar, more rugged and more vapor tight product, but also more expensive. Do NOT substitute cheap 4mil or 6 mil polyethylene here, either of which are less than 0.1 perms which is considered a true vapor barrier that effectively blocks all seasonal drying.
With either 0.5 or 0.7 lb density foam some vendors' products can be installed safely and well at 5.5" per pass without a problem, but 7.25" some products would be over the recommended limit per pass, others not. Consult the vendors, and NOT the installers. Contractors often take liberties, and going over the manufacturer's specified maximum depth per pass is both a quality issue and a fire hazard issue during the curing period.
Thorsen,
First of all, let's talk about your flash-and-batt plan. Flash-and-batt installations are regulated by the building code. In the 2012 International Residential Code (IRC), the requirements for flash-and-batt insulation in walls can be found in Footnote “a” to Table R702.7.1. (For more information on these code requirements, see Flash-and-Batt Insulation.)
The important requirements are:
1. The spray foam must be closed-cell spray foam, not open-cell spray foam.
2. The spray foam layer has to be thick enough to comply with the minimum R-value requirements established in Table R702.7.1 for exterior rigid foam on walls.
3. In your climate zone (Zone 5), that means that your spray foam layer needs to have a minimum R-value equal to 27% of the total R-value of the wall assembly. (For more information on this issue, see Combining Exterior Rigid Foam With Fluffy Insulation.)
Your plan to install about R-11 of closed-cell spray foam will therefore work. Your spray-foam layer will make up about 35% of the total R-value of the wall.
Now, to the second issue: Your concern about inward solar vapor drive. Your concern is baseless. For a major problem with inward solar vapor drive, you need a wall without a rainscreen gap and vapor-permeable sheathing. Your wall has a rainscreen gap, and your Zip sheathing has a vapor permeance of between 2 and 3 perms (which is low). So you will be fine.
For more information on inward solar vapor drive, see When Sunshine Drives Moisture Into Walls.
Thanks Martin. That is what I wanted to hear. To be clear I am not concerned about drive into the wall cavity as much as the OSB itself staying damp from the wet shingles and not having enough air gap to dry. I'm sure I'm just getting worked up for nothing.
I'm going to look into the open cell foam cavity fill option.
Thanks everyone for your generous comments! what an amazing resource