Zip panels vs. liquid WRB

I was curious – what option might be more cost effective?
1.) sheathing with OSB and then using the Prosoco joint compounds and CAT 5 liquid WRB over the entire surface…
Or
2.) sheathing with zip system panels and then using the Prosoco products to seal the seams.
I saw the Hammer & Hand guys out in Washington use both of these techniques and it got me thinking. I’ve been a little apprehensive about using all the tapes to seal joints and flash around windows, as I’ve read about questionable adhesion over time compromising the airtight seal, and ease of installation issues. I like the foolproof nature of the Prosoco products especially around windows, but I’ve also seen the $500 plus price of the stuff for a 5 gal bucket. My first choice would probably be to go with option 1, but the possible cost got me thinking. Is there anything inferior about option 2? Is option 2 in any way a cheaper route to consider?
Our new house plan is a 2300 sq ft walkout ranch, so there is considerable wall area to deal with.
Thanks in advance for any insight.
GBA Detail Library
A collection of one thousand construction details organized by climate and house part
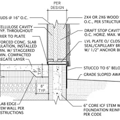
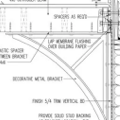
Replies
Brian,
I'm not sure of the answer, but a few minutes of calculations (after you call local suppliers for prices) should provide you with an answer.
Zip System sheathing is a system. The manufacturer (Huber) recommends that seams be sealed with Zip System tape. When you depart from the manufacturer's instructions, you no longer get any warranty support from the manufacturer. Moreover, failing to follow a manufacturer's installation instructions is (technically speaking) a code violation.
We've found the ZIP system to be less expensive in the long run because a) all the components are stocked by our supplier and thus, readily available, b) less weather-dependant, and c) doesn't require additional trade (WRB applicator). We use a combination of the ZIP butyl tape and ZIP Liquid Flash, which is a privately labled product made for Huber by Prosoco.
That said, there are very good arguments for liquid applied WRB.
Thanks for the heads up Martin. I definitely don't want to do something that compromises any warranty or goes against code. But I do like the idea of the zip liquid flash Jack. I'm glad you pointed out that they make a product that I can use in my option #2 approach. That's more along the lines I was thinking. I just am very leary of using tape. Issues with it getting dirt or sawdust behind it, or problems with it around corners or rough areas, or even wild temperature extremes affecting it.
I know I can probably get some prices to compare, but performance wise, what do you think Martin - would the zip sheathing properly sealed at the seams perform comparably better than if I covered plain OSB with the liquid CAT 5 from Prosoco?
Brian,
I used all sorts of tape, foam, goo and Prosoco products on the house that we built. I've repaired jeans with Pro Clima Tescon Vana tape which won't come off despite repeated washings. I've got multiple t-shirts and shorts that have Prosoco joint and seam sealer on them that won't come off despite 2 years of washing. You'd be happy with any of these high performance products, BUT they are expensive.
I don't think anyone knows what the lifespan of these products is since they are relatively new. The 2 main manufacturers of European high performance tapes (Pro Clima and Siga tapes) have been making them for quite awhile so we know a little more about their reliability.
That's why people who are really concerned about building a house to last for the long term build in redundancy in the air sealing with things like tape on the outside, a smart vapor retarder on the inside, caulking around the dry wall, etc.
And then the other question is, who is going to install these products? You've either got to be onsite during the critical air sealing steps in building your house, have a contractor who is highly motivated in installing things right, educate the hell out of the crew, or use something that is not too alien for the crew.
Thanks for the info Lucy. I do plan on working closely with our builder especially during the air sealing stage. The crew will be small in that it's going to be just him and his partner along with me and my dad. My goal is to have the outside sheathing as my air barrier, which is why I've been trying to narrow down the smartest way to do it for ease of installation and cost. I realize the products are new, but getting a clean surface for tape worries me.
I'm really glad to hear that the crew is small. I think that makes a tremendous difference in building a "Pretty Good House" or better. A framing crew comes in a slams it together so fast, you don't have time to catch mistakes. We (I say we, but I really didn't do the building) built my brother's house with a crew of 2-3 guys. It took a long time, but it is so nice and solid and quiet and efficient. My brother loves it.
And I really like the Prosoco stuff. It's is amazing. I have on my Prosoco Joint and Seam filler-dyed shorts right now. I'm pretty sure as product in a building it will outlive us.
Hello Brian,
I am aware this post is going on 1.5 years old, but we are building in Southwest Michigan and have the exact same question as you did in this post. We are curious to know what combination and product(s) thereof you decided on and what thoughts you have now that it has been completed and "aged" just a bit.
We would be delighted to hear from you and any thoughts you have! Thank you!!
-Leslie Q.
Hi Leslie - we ended up going with the zip system and tape. The Cat 5 over the entire exterior was going to be too expensive, running close to $5,000 for just the Cat 5. We did use Prosoco's joint and seam filler along with their Fast Flash for our rough window openeings.
Overall, we used a wide variety of products to air seal. We used a rubber gasket from conservation technology along with Tremco acoustical sealant for our mudsill. We also taped the exterior sheathing to our foundation wall using Siga Fentrim from Small Planet Supply. Our exterior sheathing served as our air barrier, and all seams along with nail holes were taped with Zip tape. Our windows were flangless from Klearwall and were taped on the outside with Siga Fentrim and sealed on the inside with Prosoco Air Dam. The slab edge along the basement perimeter was also sealed with Prosoco joint and seam filler. All penetrations including wires and pipes were caulked and gaskets were used from 475 building supply. In addition, we sheathed the underside of our trusses with OSB and taped all the seams with Tescon Vana from 475 building supply. We built a service cavity out of 2x3s to run wiring and for our low profile led cans.
All of this, with an air tight sump lid led to a blower door of 0.38 ACH. I'm not a builder, but it was thanks to the info on this site and the advice I was given that allowed us to achieve a Passive House level of air tightness.
Brian,
Well done! Great blower door test result.
-- Martin Holladay
Michael,
Thanks. You're right, of course.
Zip System tape is a re-labeled acrylic tape manufactured by 3M, but Huber likes to keep that fact quiet.
-- Martin Holladay
I know this is an old thread but Jack Miller mentioned Zip's butyl tape. I've heard this several times recently. Zip tape looks like butyl tape such as Vycor, but it's actually a polyolefin base (the same plastic used for rain screen material) with an acrylic adhesive. They add carbon black for UV protection. So it actually has more in common with Tescon Vana than with Vycor.
Zip 1.5 = Zip tape on all seams, but Zip Liquid flash on all horizontal seams BEFORE the tape...and of course the roller imprinted Z must appear EVERYWHERE or you make them climb up the ladder again the next day-anyone can supervisor to the extent.