Your opinions about best approach to hydronic piping in slab

Your own opinions on the pros and cons of each approach, please.
Consider a new house being built on a monolithic concrete slab on grade, with hydronic floor heat.
1. The floor heat piping could be placed with the rebar before the slab is poured. This is the more common approach.
2. The floor heat piping could be placed on top of the slab, then be embedded on an apx. 1.5″ topping slab. This could be poured gypsum underlayment if it’s going to get a different finish surface (tile or wood). Or it could be concrete if the desire is to have a finished concrete floor.
Here are my thoughts.
1. pros – common approach. 1 step approach.
cons – Piping embedded in slab requires that slab be broken up if repairs are ever required. Piping is placed early in construction when there is a lot of heavy work going on, on site, and may have more risk of damage. Piping placed under slab must heat entire slab thickness before reaching interior. This can be mitigated by tying the piping on top of the slab reinforcing.
2. pros – Piping can be installed much later in construction sequence, risking less damage. If ever piping needs to be repaired only the topping slab gets broken up. The primary slab below remains undisturbed. If a finished concrete surface is desired this too can be achieved later in the construction sequence, when it is less likely to be damaged by other trades. Piping near finish surface means faster response time.
cons – Requires a second concrete pour, the topping slab.
GBA Detail Library
A collection of one thousand construction details organized by climate and house part
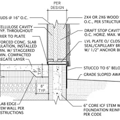
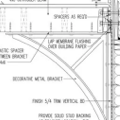
Replies
I think your response time will be pretty equal in all cases. Concrete doesn't insulate against heat traveling down with the topper slab. PEX is pretty tough stuff, it's pretty common to attach it to rebar or to the foam. I think the risk of damage is fairly low. More so, I have heard the risk of staples securing it to foam popping out during pouring is likely.
Too much money for no improvement in function for plan 2
I'm not a big fan of concrete slab floors in residences to begin with.
When it comes to under-floor heat, what's been learned is that comfort is maximized when responsiveness is maximized, which happens when heat capacity is minimized. If you're going to do something after the initial pour I'd be looking for a low heat capacity system that is thermally isolated from the underlying slab. I can't recall the name right now but there are systems that are foam slabs with channels cut in and a layer of aluminum, that would work well.
What are you doing for the finished floor?
Thanks for all your replies.
To DCcontrarian - Warmboard-R is a panel made to go over a fully supported surface and is consequently thinner and less expensive than their normal Warmboard-S which can span between joists. That would certainly be responsive and would easily allow for both tile and wood flooring. That one I happen to know off the top of my head, though I don't have actual pricing.
But since you mentioned it I thought I'd find a few others, in case anyone is interested.
Creatherm makes insulated, shaped panels, but without the aluminum facing of Warmboard.
Heat-Sheet is similar to Creatherm.
Both of these make panels reaching R20. So I suppose they could replace the usual foundation insulation if one detailed elsewhere appropriately. That would compensate for some of the cost
Another advantage would be that it would present a softer surface underfoot. That's something some people find uncomfortable about slabs on grade.
I wish I had the knowledge to do comprehensive cost comparisons but that's beyond me.
I vote for option 3: save a shit ton of money and skip the in-floor heating. Whatever benefits you'te imagining with it are going to be very minimal or non-existent in reality.
In a high-performance house, or one built even to current codes, the heating loads tend to be low. The heat output of a floor is determined by the temperature difference between the surface and the room air, so if the heating load is low the surface temperature of the floor needs to be low. I find that below about 78F you can't tell that a heated floor is heated, with a room temperature of 70F that corresponds to a heating load of 16 BTU/hr per square foot of heating.
A well-insulated, air-sealed floor will be close to room temperature. At room temperature, tile and concrete feel cold because they are highly conductive. My suggestion would be that comfort would be maximized by going with a less conductive surface, like wood, that also has some yield to it.
DC,
What about the solution Akos has proposed several times of just using radiant heat in very small areas - like the bathrooms and maybe the kitchen - where it would have to run hotter?
That's actually what I do in my own home, the only heated floors are in the bathrooms. And I use a multi-stage thermostat so that the other heat only comes on when the floor heat is running full on. In my mild climate there are long stretches in the winter when the floor heat is the only heat running in the whole house.
But it's a pretty decadent luxury. To run this way you pretty much have to have an air-to-water heat pump, which probably is going to cost 2 to 3 times what an air-to-air heat pump of equivalent capacity will run. Or a boiler, if you're not going all electric I guess. Resistance electric for the floors doesn't make sense because they end up being your primary heat source, resistance only makes sense for supplemental.
To elucidate further:
On my second floor, I have three stages of heat. There is tubing under the bathroom floors and in the ceilings of the bedrooms, and there is an air handler. I have a three-stage thermostat where the floors come on first, the ceilings come on when the floors can't meet the load, and the air handler comes on when the ceilings can't meet the load.
I log run times for each stage. For the winter 2023-24, December 1 to March 1, the floors were on an average of 17 hours 18 minutes a day. The ceilings were on an average of 54 minutes a day, and the air hander was on an average of 43 seconds a day. The longest runtime in any 24 hour period was 24 hours for the floors, 6 hours 27 minutes for the ceilings, and one hour three minutes for the air handler. The second floor is 1400 square feet and the bathrooms are a combined 300 square feet.
I believe this is the way to optimize comfort, the bathroom floors are toasty all winter long.
I threw in the runtime numbers because sometimes people will suggest just running resistance electric in the bathroom floors. That won't work, unless you're OK with the lion's share of your heating coming from resistance. And sometimes people will say, "just use the electric to take the chill off and have the other heat provide most of the heating." That's not how heating works.
DC,
Thanks!
Like DC, I use my bathrooms to provide heat to the second floor of our house in Zone 6 A. The floors are Warmboard-S with each room being its own zone. Bathrooms are 72F, where the bedrooms at 69F. Only during cold nights < -10F is there a call for heat.
I would only do in floor heating in the bathrooms or other tile areas, unless you are in a really cold climate. Be sure to run a heat loss simulation (such as LoopCAD) to determine your water temperatures. We heat our floors using a heat exchanger come off th e indirect tank.