XPS rigid foam board on interior and exterior of wood framed wall

Currently working on a new residence (climate zone 4A). The home is 2×6 exterior framed wall with 3/4″ XPS ridge foam board over 7/16″ osb, then Tyvek WRB over rigid foam. Exterior finish is brick. No question about this wall assembly.
However, this home will have an indoor pool attached to the main home. Attached is this wall assembly for the pool room. As you’ll see in the attachment, it is spec’d for the wall framing to be sandwiched between the 7/16″ osb, 3/4″ XPS foam board, and Tyvek. And brick on both sides of wall.
The pool room will have designated dehumidifier.
Is there an issue with having a WRB, XPS on both sides of a wood framed wall?
What are other possible issues with this wall assembly, if any?
Thank you
GBA Detail Library
A collection of one thousand construction details organized by climate and house part
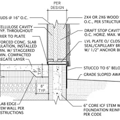
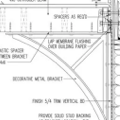
Replies
The answer will partially depend on if you are fully committed to limiting the interior dew point to recommended levels (typically quite expensive). Personally, I'd avoid OSB and XPS (fiberboard and EPS are better) and consider moisture proof ICF walls.
There's no point to having a WRB on the indoor side of the assembly- there is no wind-driven rain slamming into the interior side brick veneer.
If Z-flashing-taped at the seams the XPS could be the WRB (only needed on the exterior side.)
At 3/4", XPS (can the foam type be changed?) is fairly vapor permeable, about the same level as interior latex paint, which could become a slight issue if the dehumidification system fails. Replacing the interior side WRB with a true vapor barrier would probably be more protective of the interior & exterior plywood.
As drawn there appears to be a cavity between the brick and XPS, but it's not called out in the drawing with a specified depth, or whether it's ventilated to the exterior air with weeps at the bottom and vents at the top. The top of that cavity appears to be blocked on the exterior by framing, so as-drawn there is zero convective drying of the channel.
The roof assembly details need some work too. A broadsheet fully adhered layer between the t & g and the SIP panels would be a good idea, or there WILL be moist air leakage to the outer skins of the SIPs at the seams putting the exterior skin of the SIP at risk.. The most critical seam would be ridge, but the others matter too. It doesn't have to be an expensive roofing type layer, a vapor permeable fully-adhered WRB such as Blueskin VP 100 or Delta-Vent SA would do it without creating a moisture trap. A fully adhered housewrap would be like putting 4' wide sealing tape over your t & g, blocking indoor air's access to the SIP seams.