XPS Blowing Agents

Is there any update on the XPS industry’s conversion from using HFC-134a to HFOs, as was explained on GBA’s website a year and half ago: https://www.greenbuildingadvisor.com/blogs/dept/green-building-blog/friendlier-foam-insulation-way-eventually
Foamular’s marketing material touts a “Zero Ozone Depletion Potential” of its blowing agent since a blowing agent conversion in 2009, but it doesn’t say what the blowing agent is. And it doesn’t speak to the Global Warming Potential. That part is conveniently not mentioned. With only a rudimentary understanding of what these measures mean and how they differ, I find the marketing to be difficult to parse on these products.
I wish XPS would become an environmentally friendly option in all respects. After years in the curtain wall industry, I favor mineral wool batt and board insulation, but in detailing a cathedral ceiling in south east (zone 4) PA, I’m currently thinking of using several layers of EPS outboard of the structural roof sheathing, which will be covered with an intelligent air barrier. I’m concerned that mineral fiber would lose performance with wind washing if I don’t cover it. My concern with the EPS is that it seems more fragile. I’d like to use metal hat channels to create a 2″ vent space on top of the board insulation, followed by the roof sheathing and membrane. My concern is the EPS might not withstand point load compression at the anchor points.
I feel like I’m walking into a rat’s nest with my XPS questions, but its been so helpful to read these boards that I thought I’d ask.
GBA Detail Library
A collection of one thousand construction details organized by climate and house part
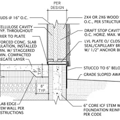
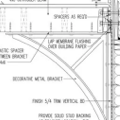
Replies
Type-IX EPS is at least as rugged as Type-II XPS, and usually cheaper per labeled R (despite being higher density, and more polymer per R). It's probably overkill for most roof applications though.
Type-II EPS is rugged enough for insulated concrete forms and walkable membrane roofs, and is one of the most commonly used insulating materials in commercial flat roof construction (along with 2lb fiber faced polyisocyanurate.)
Zero ozone depletion blowing agents aren't just a nice feature- they're the LAW! (Montreal Protocol.) Foam blown with ozone depletion potential agents would be contraband in North America.
There is no reason to believe that HFO blown XPS won't experience the same loss of performance over time as current HFC-soup blown XPS as the HFO diffuses out. With any1.5lb & higher polystyrene assume it will be no more than R4.2/inch at the end of the lifecycle of a house. The exception would be graphite loaded Type-II EPS, which should be better than R4.5/inch for life.
Regarding mineral wool and wind-washing - Martin H. did a blog post recently on that topic...
https://www.greenbuildingadvisor.com/articles/dept/musings/windwashing-exterior-mineral-wool
My understanding is that XPS sold in the U.S. is still blown with the high GWP blowing agents.
EPS, polyiso, and mineral wool are all preferable to U.S. XPS from a global warming perspective. That may change in the future, but it hasn't changed yet.
Some (all?) European XPS has made the switch, so the change is certainly possible, but I imagine that it won't happen until it is legally mandated.
As of 5 years ago something like 90% of all rigid foam in Europe was blown with pentane, though some XPS was blown with CO2. Since then there has been some movement toward HFO1234ze for site-sprayed foam, as well as some HFO1234_ _ and HFO1233_ _ variants in the XPS biz.
See also (from 2011):
https://www.epa.gov/sites/production/files/2015-07/documents/transitioning_to_low-gwp_alternatives_in_building_and_construction_foams.pdf
Thanks everyone for answering. The wind-washing studies on mineral wool were excellent. Reaffirmed my affinity for mineral wool. If you are willing to use a separate air barrier, and if the cost is reasonable, it seems like such a good choice, from a fire perspective, a production perspective, an ant perspective, from a vapor permeability perspective. I get that it may be harder to get a perfectly flat plane when attaching furring to create an air gap. But once it's done, it seems like a great performer.
As Dana says, if you want long-term better R-per-inch than EPS, get graphite loaded EPS, not XPS.
There's no good reason to consider any of the North American XPS until they change blowing agents, but since you were wondering about the blowing agent in the pink stuff, here's what I figured out previously:
Foamular literature claims their mix has a global warming potential (GWP) 70% lower than the pre-2009 HCFC blowing agent (142b), which had GWP = 2310. 70% lower would be about 700. On the other hand, the XPS industry association says that the GWP of the blowing agents their members use range from 740 to 1340. I suspect that the 740 is for Foamular, and Owens Corning is rounding the 68% improvement that represents up to 70%.
But whether it's 700 or 740 or even 500, that drastically worse than EPS and not worth considering using.
That was in a comment on this thread: https://www.greenbuildingadvisor.com/community/forum/energy-efficiency-and-durability/93206/xps-brands-dow-owens-corning-pactivkingspan
Hi Charlie, the XPS manufacturer's seem to be delaying the launch of a foam using HFO, or other low GWP blowing agents. The marketing of zero ozone depletion or ODP is not relevant since the blowing agents used for the past 10 years, such as HFC used in XPS, already address this. The GWP or global warming potential is what needs to be addressed by switching away from HFC BA.
Spray foam manufacturers, such as BASF, have had a HFO low GWP foam since 2017. See WALLTITE CM01.