Batt Insulation or Mooney Wall With Blown-In Cellulose

In reading GBA, I see a lot of attention paid to minimizing thermal bridging. One such technique is the Mooney wall, which, as I learned here, is 2x2s installed horizontally against 2×4 framing to create a 5.5″-deep wall with less thermal bridging than a 2×6-framed wall.
So, I’m going to insulate a 12.5′ x 8′ wall, which is only 100sf. The insulatable area is even less, because I’m installing 24sf worth of windows, and about 7sf of headers.
To install insulation into a Mooney wall, my understanding is my only option is blown cellulose, and renting a machine is a big expense and hassle for only 69sf or so of wall. If I attach the 2x2s to the 2x4s vertically, I could just install 5.5″ batts and be done with it, but I’d have more thermal bridging.
So, those of you who are serious about thermal bridging, if you were in my place, would you rent the machine to avoid the thermal bridging for a single small wall, or would you just accept the thermal bridging and install batts?
By the way, before anyone mentions, I’m aware that my headers have to be only 3.5″ deep, and if I go the batt route, I can glue 2″ of foamboard insulation to the headers. If I go with batts, then I do indeed plan to glue foamboard to the headers.
GBA Detail Library
A collection of one thousand construction details organized by climate and house part
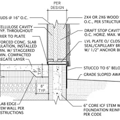
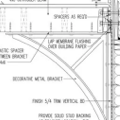
Replies
Now that I've already hit Send, I realize that I could keep the existing 3.5" deep insulation, and cut 2" thick rigid foamboard to install between the Mooney sections. I presume that's what most of you would do?
The home improvement store will rent you a low-end machine for free if you buy enough bags. Not ideal for dense-packing because of the lower power, but for one wall... On the other hand, I doubt this project will require "enough bags".
PS: 2x2's, 2x3's, 2x4's all work here.
PPS: You could also try a Bonfiglioli wall setup, where you fur out the 2x4's with 2" x 1.5" strips of EPS, which get screwed through.
I wouldn't recommend using a low-power rental blower. It can't install insulation densely enough to avoid settlement over time.
For such a small area, I'd use batt insulation. The box stores sell it all the way down to 2 1/2" thick R8, which could compress down to 1 1/2" without issue. The insulation product data sheets sometimes have a chart telling you how that will translate to installed R value, if it matters.
Jason, actually a rental blower does work for dense packing. See this thread @ 3 in the comments section: https://www.greenbuildingadvisor.com/article/borrowing-a-cellulose-blower-from-a-big-box-store
I still stand by that. However, unless one is OCD and just can't restrain oneself I wouldn't attempt it for just 100sq ft. The labor cost and the physical cost of the insulweb, the roller, and the stapler is just way too much trouble for such a small area. I'd find another way.
Thanks. I'd always thought that compressing batts reduced their effectiveness, but I just looked it up and it's not a problem. e.g., Compressing a 5.5" batt to 3.5" gives you less R-Value than the 5.5" is rated for, but it gives you a little *more* R-Value than a standard 3.5" batt.
Check around the local lumber yards, if you are in an area where exterior continuous insulation is required, Zip R6 might be a stock item. This is 1.5" thick, you can rip strips to go over the existing studs than install 2x6 batts. Much easier to screw drywall into the OSB on the Zip than dealing with long screws through foam.
Thanks all for the replies. I had another idea: A plane of 1-inch foamboard over the 2x4 studs, then 1/4" drywall on top of that. (Take that, thermal bridging.) I have some 1/4" drywall left over from another project, so this would be a good way to use it.
Correction: As per IBC 2603.4, rigid insulation must be covered by at least 1/2" gypsum for fire protection, so for me, that means 2 layers of 1/4" drywall. And I might as well add furring strips over the foamboard to make it easier to attach the drywall.
Batt insulation is a great product. The typical lackluster install is only reason why batt insulation gets a bad wrap around here. However there's no reason why a homeowner is not capable as performing a Grade 1 install of batt insulation. It just takes patience. Your foam strip idea on the interior face of the studs is a good one.
> I see a lot of attention paid to minimizing thermal bridging
Which is almost always misplaced. The focus should be on whole wall R value. And moisture performance.
So I'm leaning towards:
(1) The 3.5" cavity from the original 2x4 framing, already filled with fiberglass batts
(2) 1" of rigid insulation
(3) 1x2 furring
(4) Two 1/4" gypsum layers
The question then is what to put between the furring strips, because there's a 3/4" gap there. I Googled and got conflicting answers about whether the airspace would be a decent insulator. So, I'm thinking of cutting and cobbling 3/4" rigid insulation there, because there's no question that that will insulate.
Why two 1/4 layers instead of a single layer of 1/2"? And why the furring instead of just attaching the drywall with 2-1/4" screws? It seems like you're making a lot of work for yourself.
Earlier I'd mentioned that I have some leftover 1/4" drywall that I can't ever imagine being able to use for anything else. (I'm a homeowner, not a contractor.) And it's already in the upstairs area where I'm re-doing the wall. Doing 1/2" would mean buying it and hauling it upstairs.
I guess I could attach the gypsum without furring strips. How would the rest of you do it, furring or no furring?