Would 2×8 studs filled with dense-packed cellulose and 2 in. rigid foam over the sheathing work in Zone 5?

I’m located in climate zone 5 (Portland, Maine).
The 4 inches of foam that people seem to like over 2x6s seems quite a bit more troublesome from a detail point of view. Sure, 2x8s would cost more, but cellulose is a lot cheaper and more environmentally friendly than foam.
In a related question, what about solid wood sheathing, which is more environmentally friendly than OSB or plywood? Could one get it tight enough with taped housewrap?
GBA Detail Library
A collection of one thousand construction details organized by climate and house part
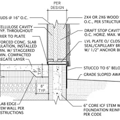
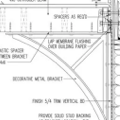
Replies
Kevin,
Q. "Would 2x8 studs filled with dense-packed cellulose and 2 in. rigid foam over the sheathing work in Zone 5?"
A. Yes. But Portland, Maine isn't in Climate Zone 5; it's in Climate Zone 6.
To learn about these calculations, read Calculating the Minimum Thickness of Rigid Foam Sheathing.
To get a precise answer to the question, "What is the minimum thickness of exterior rigid foam installed on a 2x8 wall in Climate Zone 5," you would need to use the calculation method described in this article: Are Dew-Point Calculations Really Necessary?
To get a back-of-the-envelope idea of the minimum R-value of the foam for a 2x8 wall, you could do it based on percentages. The standard recommendation for a 2x6 wall with R-20 (nominal) insulation between the studs in Climate Zone 5 is to install R-7.5 foam. So the ratio of exterior to interior foam is about 27% to 73%. For a 2x8 wall with R-26 (nominal) insulation, you would need (roughly) exterior rigid foam with a minimum R-value of R-10.
For Climate Zone 6 (Portland, Maine), the ratio of exterior to interior foam is about 36% to 64%. For a 2x8 wall with R-26 (nominal) insulation, you would need (roughly) exterior rigid foam with a minimum R-value of R-14.6 (equal to about 3 inches of XPS or polyiso).
If you install board sheathing, there are several ways to address airtightness. You can follow the Airtight Drywall Approach; you can use spray foam (in a flash-and-batt system, or by itself); you can use taped exterior rigid foam; you can use a liquid-applied water-resistive barrier (WRB); or you can use a taped housewrap. If you try to use a taped housewrap as your air barrier, I would choose one of the European wraps, not a conventional U.S. housewrap.
Going with 3" foam instead of 1.5" represents a big cost cost jump-and adds a lot of fastening issues. What is the potential consequence of using 1.5" foam and let in bracing instead of sheathing?
Martin J
Martin,
Taking the OSB or plywood sheathing out of the equation doesn't change anything, because 1/2-inch OSB or plywood sheathing has negligible R-value.
But why would anyone want to frame a wall with 2x8 studs in the first place?
Kevin,
Do you want to be energy efficient or not? Maine gets cold. Put 2 staggered and taped layers of 2 in. (or more) polyiso all around and get it done. I did just that (over the existing 1 in. of eps) on a retrofit in Maryland. I'm living in that house. It's 19 degrees out going down to 7 tonight, and it feels great inside. My single 12kbtu minisplit has been off from 10AM to 5PM, with the help of a brilliant sunny day with snow on the ground and plenty of south facing window area.
After a year or so of experiencing this house, I would consider that 5 inches of foam over 2x4 fiberglass to be minimum for around here. I would certainly consider it minimum for Maine.
As for "fastening issues," that you mention, I can tell you from experience that it's not a big deal. I drove hundreds of 7 in. long Fastenmaster Hedlok screws into studs all around the house. With a little care, I was surprised how few missed the studs.
Sounds like you did it right Sonny! How did you attach the siding? I brought up the 1.5" foam and no sheathing for 2 reasons-most projects simply cannot afford 5" of foam, Hedloks, window extensions and the furring for siding. 1.5" of foam fastens quickly and some siding can go right over. This is a system that may fit conventional budgets. I know the computer models call for more foam.
My speculation: on the few coldest nights, a bit of condensation may form on the warm side of the foam. With no sheathing to absorb it, the cellulose does, and slowly, safely dries it to the inside.
Martin J
Martin J. and Kevin, sorry, I was responding to the wrong person.
Anyway, Martin, you certainly are correct about the price and ease of 1.5" foam. If I were doing it again, I would still want the wall R value I have (about 40) but might go with double wall, cellulose and a thinner foam for thermal break. I wouldn't give up the R40 walls, though, even for MD. I'm sitting here again with brilliant snow-assisted sun providing my heating today, and once in a while go out to listen to the beautiful music of all my neighbors' central heat pumps running.
I think the extra cost of superinsulation or passiv house is worth it., and I think society is (slowly) coming around. The sun is the source of all our energy and I get a lot of it direct-from-the source that sends no bill.
I attached my vinyl siding in the usual fashion using roofing nails, through one-by strips or 3/4" ply at the corners, that are attached with the Hedloks. After 2 summers and winters, there is no waviness or any problems at all with the siding, even though you usually don't have to search too long to find problems with vinyl siding installations. I did end up filling in the spaces between furring strips with 3/4" foam, because I just didn't trust the vinyl to stay straight over the open spaces, and because none of the vinyl manufacturers want to accept any unbacked vinyl (see a blog that was done here at GBA about this---I forget what it was called)
Martin H. and Others - Thank you for your responses. The reason I'm considering 2x8's, is that I like the simplicity of double stud dpcellulose walls, but nervous about moisture , esp. on north wall. So the 2x8 allows me to build in a very straight forward way , using mostly cellulose for environmental and cost concerns, and 2" of foam would mostly protect the sheathing. After reading about moisture testing on 12" dense pack walls, and they seem to do o.k.( sheathing reaching 20-30% on the north wall only, in Feb. and Mar. but drying by May when it gets warm.), I'm thinking that the exterior insulation recommendations may be overkill. And these plastic foams are very unfriendly from an embodied energy point of view. By the way , the southern coast of Maine is more like a "Zone 5.25", that is, it's significantly warmer than 10 miles inland, and cooler in the summer, ( though really cold this week, coldest it's been in 4-5 years). The maps don't get that kind of detail on them, for understandable reasons. I am an osteopathic physician, who designed and built passive solar and super insulated buildings up to the mid 1980's, before going to medical school in 1987. My homes then were 2x6 with european vapor barriers, then 2x3's laid horizontally, shot through with screws, and all the wiring and plumbing in the 2x3 space. V.B.taped to all windows and doors , between floors, and all penetrations. What a time consuming job! Anyway, I am lucky enough to love my new( now 22 years!) work, and I try to stay up on building info.In short, I want a R40 wall system that is environmentally and "embodied energy" friendly, and more cellulose seemed reasonable. Unfortunately, the more cellulose you use between the studs, the more foam you need on the outside, at least from the tables. But what about those nicely performing thick wall cellulose only houses?
Kevin,
Q. "The more cellulose you use between the studs, the more foam you need on the outside, at least from the tables. But what about those nicely performing thick wall cellulose only houses?"
A. Those nicely performing thick-wall cellulose-insulated houses get damp wall sheathing every February. They perform well because the damp wall sheathing dries out in April.
If you install thin rigid foam on the exterior side of the sheathing, you reduce the ability of the sheathing to dry to the exterior. Now the sheathing won't dry out in April. It will stay damp.
The only way that exterior foam can reduce the risk of rot is if you make the rigid foam thick enough to keep the sheathing above the dew point in winter, so it never gets damp in the first place.
Here's my advice for anyone considering the installation of exterior rigid foam: make it thick, or don't bother.
Martin - Thank you for that succinct answer. You are very generous with your time and knowledge, and I appreciate that. I have read many of your articles, and they are always informative. You are also very patient with all the folks who do not have your level of expertise. I'll probably go with 2x6's and 3" - 4" of foam to approximate R40 walls. The simplicity of the detailing still makes double wall dense pack an attractive option. If I did the latter, I think I'd avoid OSB, and use plywood or wood sheathing, which can be had for reasonable $ in Maine. Thanks again. Kevin
Kevin, here is a link to a project that used 2"x8" walls which was used to illustrate a blog here on GBA this summer. No idea how it will fare over the long term.
http://www.bernhardtpassive.com/construction/
Isn't the wood sheathing the issue? It's the sponge that will hold the moisture and rot. If it is not there, I think that a small amount of moisture may condense to the inside of the foam, on the few coldest nights and later melt and absorb back in. Wasn't the condensation moisture in the cellulose all along? The borates will prevent mold while it's condensing/drying/migrating-it is very good and absorbing and releasing small amounts of moisture.
I am making a few assumptions-normal good building practice and interior humidity levels. No interior moisture retarder. A good dense pack cellulose install. Basic stuff.
In fact, going to 10" of cellulose may even be better as it is a pretty effective air barrier at that thickness.
I achieve that by strapping as Kevin did in the old Tenoarm days.
But following the tables usually puts the price of foam out of most budgets. Beyond 1.5 or 2" is a lot more expensive. Doubling it much more than doubles the cost due to fastening and extension issues. So people do not use it. You can upgrade from wood sheathing to foam for a small cost increase and a big performance jump.
Yes, it is better to place the dewpoint inside of 5" of foam. But it is so cost prohibitive and outside of the realm of normal construction practice that it is not even considered by most designers.
It is a shame to not get the huge benefit of the solid thermal break of continuous foam, and an R40 wall if the moisture is managed by a well designed assembly.
Martin J
Martin J.,
The same amount of moisture will accumulate in the wall assembly every winter, whether you choose to install thin rigid foam over OSB or just thin rigid foam without any OSB. In either case, the moisture has to find a way to dry or it will eventually cause rot.
Actually with thin EPS no OSB/ply sheathing the most susceptible component (the sheathing) is absent. OSB sheathing runs about 1 perm, which is too vapor tight to dry on it's own, and is damaged when wet. An inch of Type-II EPS is about 3 perms, which is about as vapor open as standard latex paint, and EPS is not damaged or functionally impaired by wetting. But at 3" it would run about 1-perm, and there is a risk of accumulating moisture in the cellulose unless one used a "smart" vapor retarder on the interior side (at more material expense & detailing labor).
BTW: You don't "place" a dew point in a wall, or anywhere else. Dew point isn't a location, it's a temperature- the temperature at which moisture in the air condenses. Since moisture content of the air will will vary, so will the dew point. The dew-point of the entrained air in a fiber insulated wall is never higher than the temperature of the sheathing in winter, since the fiber is extremely vapor permeable, and as the sheathing temperature drops to the dew point of the entrained air, it adsorbs that moisture OUT of the air, and into the sheathing (which is exactly the problem when using moisture-susceptible wood sheathing that isn't very vapor permeable itself.)
It's possible to build a decently thermally broken cellulose wall on 2x8 plates using 2x4's 16" o.c. for the exterior structural portion of the wall, and finger-jointed 2x3 studs 24" o.c., spaced and staggered to always miss the 2x4s. That way you always have R13+ of thermal break from just the cellulose at every stud, and a center-cavity depth of R26-R27. If you put an inch of EPS on the exterior the center-cavity value will run about R30 center cavity before deductions for thermal bridging. The most serious thermal bridging will be at the plates, but you'll still run well north of R25 for a whole-wall, probably close to R28, which is about about 2x that of a code-min wall. (Typical 2x6/R20 comes in at about R13-R14, depending on stud spacing/framing fraction. With advanced framing techniques you can sometimes hit R15 whole-wall.)
If you want to sheath the 2x8 stagger-stud wall with 5/8" fiberglass faced exterior grade gypsum (eg. GP DensGlass) and skip the foam you'd still be in the mid-20s for whole-wall R, and it would not collect moisture in the winter as long as the siding is back vented/rainscreened. (See: http://publicecodes.cyberregs.com/icod/irc/2012/icod_irc_2012_7_sec002_par025.htm Note the provision for zones 4-6 that reads " Vented cladding over gypsum." )
An R40 wall is great if you can afford it, but if that means you can only afford code-min windows rather than U0.20 triple panes it's a step down in whole-house performance. An R25 wall is nearly 2x code, and code min windows would dominate the heat load numbers even at R25. To get the whole-house performance up, it ALL has to move in rough proportion, with some bang/buck tradeoffs. Is R40 whole-wall with slightly better than code U0.25 windows cheaper & better than R25 walls and way better than code U0.18 windows? It depends a lot on the house design, and the actual costs of the goods. Sometimes the "right" solution is to just cut down on the total window area and use lower performance windows, concentrating more on south-window solar gain factors than an arbitrary U-factor, etc.
Using reclaimed roofing foam can take quite a bit of the expense out of the exterior foam approach- there are several vendors operating in MA (including insulationdepot.com, who will gladly ship to ME for a price.) On a deep energy retrofit I was involved with in MA a bit over a year ago we used copious quantities of reclaimed 3" and 3.5" roofing iso on the exterior of a three story 2x4 balloon-framed 1890s house to hit about R40 whole-wall. The cost of the reclaimed goods was about 1/4 that of virgin stock. Re-used foam is as green as it gets in the foam-biz on every front,. including environmental & financial- the net savings to the project of using mostly reclaimed rigid foam was well over ten grand in material cost.
Thanks Dana and Martin H and sorry to Kevin for hijacking his thread.
So do we have agreement that it is safe to place 1.5-2" of foam over 7 inches of densepack cellulose, with no wood sheathing despite the tables?
This gives Kevin a thermally broken mid 30'sR wall at a minimum of cost, easy fastening and detailing. Exterior is tight iso or extruded foam, taped and/or Tyvek, wall dries to interior.
Again, I am assuming normal good building practice.
You are right about dew point Dana-I was clumsily trying to say condensation would only occur when the inside foam surface was very cold.
"all we are sayin', is give foam a chance!" Let's not eliminate it if it works. It's an inexpensive way to get a huge benefit.
Martin J
Thanks to all for your input. Kevin Z.
Kevin - we've built several double-wall houses (11-12" walls) in Portland and environs without exterior foam. We haven't pulled apart the exterior to check on the sheathing in any large scale way but they seem to be holding up fine. There is also someone up the coast gearing up to panelize wall construction. I wrote a piece for JLC about one of our early projects - send me an e-mail if you would like a pdf of it. Search my name and you should get to our website easily, with a link to my e-mail.
Kevin: Thermal bridging is a huge but little understood (without doing a wufi analysis) way a home loses heat. If you really want to build an 8" wall, build two 2x4 walls separated by an air space. the interior wall does not need a 2nd top plate or any headers.
Dan: we've panelized our last two homes with mixed results, I like the concept and the benefits, but there are downsides.
Refining Bob's double studwall suggestion a bit, rather than two 2x4 walls, make the non-structural wall finger-jointed 2x3s 24" o.c.. With finger jointed studs you'll get better wall flatness even with the wider spacing, use less wood, and achieve a measurably higher R thermal break at the same wall thickness.