Would 2″ exterior foam board + standard interior poly put my eastern Ontario house at risk?

My wife and I will be building our house next year. I’m in the research and planning stage and first order of business is to determine our insulation strategy. We’ll be building in eastern Ontario (near Ottawa) which sees average winter temps of around -13C (7F). I’ve recently come across the dew point calculation method posted last year by Martin. I was thinking of going the route of 2” XPS foam board with rock-wool cavity insulation on a 2X6 wall. Here are the calculations (assuming 70F and 35% humidity, therefore giving us a dew point near 40F):
Temp delta = 70F – 7F = 63F
Interior Insulation ratio = R-22 / (R-22 + R-10) = 0.6875
Sheathing temp = 70F – (63F * 0.6875) = 26.69F
Which is obviously not enough. Going to a 3” foam still gives a lowly sheathing temp of 32.54F. Even a 4” XPS leaves me needing more (or dropping interior insulation levels). With this in mind, what is the common thought on going with a 2” XPS foam (not moving the dew point out of the wall space) and having a standard interior poly vapour barrier. From what I can tell, the Dow Cladmate foam board has a vapour permeance of 3.5 for 1”. Assuming a linear perm rating of 1.75 for 2” foam, would I realistically be putting our house at risk? Are there better interior cavity insulations than rock wool for my situation?
Thanks for the help,
-Mike Goulet
GBA Detail Library
A collection of one thousand construction details organized by climate and house part
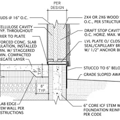
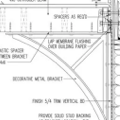
Replies
Is interior poly required in your area? Many folks are avoiding it, preferring to do a bang-up job of air sealing. If you will ever use an air conditioner, poly inside can be problematic. Are you familiar w/ alternative methods of "sealing" your walls and NOT using poly? BTW: I'm not familiar w/ that dew point calc method. Do you use the R value of the insulation, or the whole wall? With 2x6, those figures will be a bit different.
Mike,
Here's an article that discusses these calculations: Calculating the Minimum Thickness of Rigid Foam Sheathing. I'm not sure whether you are in climate zone 6 or 7. If you are in climate zone 6, you need a minimum foam R-value of R-11.25. If you are in climate zone 7, you need a minimum foam R-value of R-15. In either case, I think 2 inches of polyiso would work. (Depending on how you calculate the R-value of the polyiso, 2 inches of poyiso might be only R-13 -- but I think that's close enough to keep you out of trouble.)
I would skip the interior poly. I know that in Canada, some building inspectors insist on interior poly. If your building inspector is like that, I would invest in MemBrain. Because it looks like poly, they usually will OK its use.
John: Interior poly is still the defacto standard in my area and something my "older school" builder seems to think is a given in wall construction. I recently had a chat with the local chief building inspector and he says they don't see many builders stepping away from it (since they deal with minimum code tract builders most often), but said that if I can prove that the dew point calculation works and have documentation regarding the sheathing's ability to act as a vapor barrier, that they would accept it. The calculation was done based on 2X6 walls (with R-22 Roxul cavity insulation).
Martin: I believe I fall smack dab on the line of zone 6 and 7, however even though average winter temps are about 7F (-13C), it is not rare to get a cold snap of -20F. With this said, I'd rather play it safe. Typically for polyiso, I stick with the ajusted value of around R6.5 per inch. But even at R-15, I fail to see how this would work given the dew point calculation.
Dick: Yes. What I meant was, for that particular calc, would one enter the R of the insulation, or the R of the whole wall, taken as an assembly. I would assume one would use the R of the wall, "averaged" for studs, but was not sure if that concept was sort of built into the equation.... or fudged in, generally ignoring the studs. Thanks for the thorough run-down of the method, though. Cheers. j
John, there isn't any magic to calculating steady-state temperature profile across a wall assembly. Of course steady state never really exists, as outside temperature is always changing, but for wall analysis purposes the assumption of steady state is useful. Given that, the rate of heat transfer through each layer of the wall must the same, or there would be increasing or decreasing heat content and thus temperature in the different layers. Since that heat transfer rate (Q, per unit area) is given by:
Q = U*dT = dT/R
where U is the heat transfer coefficient, and equal to 1/R, and dT is the temperature difference across that layer having that R value, then first the heat loss rate Q is calculated from the overall temperature difference and the overall R of the assembly. We are talking about a piece of area where the R is uniform perpendicular to the direction of heat flow, so that would be center of cavity; more on that below.
Since the overall R is the sum of the R values of the layers, and Q is constant for all the layers, then for one layer the temperature difference is found from:
Q = dTL/RL = dTO/RO
where the "L" and "O" refer to layer and overall, respectively. Solving for dTL we get:
dTL = dTO *(RL/RO)
meaning, simply, that the fraction of the overall temperature difference that is across the layer is the ratio of layer R value to overall R value. Thus, to use Mike's numbers, with R22 inside and R10 more outside, the dT across the inner layer would be 22/32 = 0.6875 of the overall dT (63 degrees), or 43 degrees, giving 70-43 = 27 degrees at the boundary.
The temperature profile through a wood stud, wood sheathing, and finally that external foam can be calculated the same way, although the profile will be different than through the two insulation layers. There will be a lower temperature drop across the wood stud than across the inner insulation layer, because the R of that wood is a smaller fraction of total R of that slice of wall assembly.
However, this analysis has ignored heat transfer parallel to the inside and outside surfaces. In the immediate vicinity of the framing, since the temperature profiles across framing and inner insulation layers are different, there will be some heat short-circuiting from insulation to wood. In most cases this can be ignored for purposes of calculating worst case temperature at the sheathing layer, because it will be colder at the outside of the inner insulation layer than at the outside edge of the more conductive wood stud.
Martin,
I'm bringing this back up because I re-read the article that you linked to in your original response. This just leaves me a little bit more confused on what to do... if I base myself solely on the dewpoint calculation, R-15 on exterior walls isn't close to satisfying the test for a class III vapour retarder. However, if it's based on the table found in the the IRC supplement, it says I'm fine. Which one should I trust and follow?
Mike,
I'm confident that the values given in the table in my article will keep you out of trouble. Those values are based on dew-point calculations.
I can only assume that you have made a mathematical error in your dew-point calculations, but I don't have time now to check your math.