Wind bracing when using XPS

I would like to build a workshop using 2×4 studs on 16″ centers. I can get 1 1/2″ XPS at half its cost , enough to do my exterior walls. I want to create a thermal break from the studs, but I am concerned about wind bracing my walls, because of the 1 1/2″ between the sheathing and the studs.
Would there be any advantage to using the XPS on the interior, covered with 1/2″ drywall? The wall system would be from inside to outside: drywall, XPS, 2×4 studs, batt insulation, sheathing, Tyvek, 3/4″ battons, then wood siding. Would this work?
GBA Detail Library
A collection of one thousand construction details organized by climate and house part
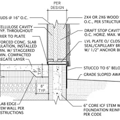
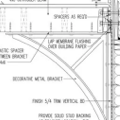
Replies
Mike,
Foam sheathing is best installed on the exterior of a building, where it can reduce thermal bridging through the rim joists.
The four main bracing options are:
Traditional 1x4 let-in braces;
Steel strapping with a T-shaped cross-section (Simpson TWB strapping);
Plywood or OSB sheathing at corners only;
Inset sheer panels
To read more about bracing foam-sheathed walls:
https://www.greenbuildingadvisor.com/green-basics/rigid-foam-insulation
http://www.xpsa.com/tech/FSC%20Bracing_Techniques_How%20to%20Guide_v1.2%20FINAL.pdf
Mike,
The answer would depend on your climate zone and configuration of the shop. When Martin says "foam sheathing is best installed on the exterior", he's considering only its thermal break benefit at the rim joists, which is a very small part of the thermal envelope and perhaps nonexistent if the shop is on an insulated slab.
In a heating-dominated climate, it's preferable to allow the house to breathe to the outside. In a hot, humid climate it's best to make the exterior less vapor permeable and leave the interior vapor-open.
It may simplify construction and give your nearly the same thermal break advantage to install the XPS on the interior (as I just did to retrofit an old farmhouse) and strap it horizontally for the drywall. You will have to extend outlet boxes to the drywall surface, but that's often easier than aligning the exterior WRB, windows and flashings to exterior foam board.
Unless you're in a high rainfall area on an exposed site with inadequate roof overhangs, I would advise skipping the rainscreen, which also makes weather barrier integration more challenging, creates an opening for insects as well as a fire path to the soffits and roof. Simply backprime the wood siding and use solid color stain instead of paint for a durable low-maintenance finish.
Mike,
You mentioned batt insulation, by which I assume you mean fiberglass. While rigid foam board solves one of the problems with fiberglass, it's propensity to convective losses, it doesn't solve the most common one: rodents turning it into a tunnel maze and then chewing on the foam.
I would suggest considering cotton batts. More money but more density, more R-value, more fire-resistant (with the borates), more sound attenuation, and far more insect and rodent resistant. I just installed blue jean batts in the farmhouse. They're a bit difficult to cut but fit nicely and are a pleasure to handle.
Robert
Where Is it more likely to have moisture condensation within the wall cavity... with foam on the inside or foam on the outside? Specifically in New England in the coastal area where humity is often high.
JR,
I know you asked Robert, but I'll offer my opinion (which probably differs from Robert's). The answer to your question is, you are more likely to have condensation in your wall if the foam is on the interior than if the foam is on the exterior.
Here's why: if the foam is on the exterior, the inner face of your OSB or plywood will be warm -- too warm for condensation to occur. If the OSB has no foam on top of it, it will be cold.
If you choose to install interior foam, you should use the Airtight Drywall Approach to limit the exfiltration of warm, moist interior air into your stud cavities. Another way to help protect your OSB sheathing is to install a vented rainscreen behind your siding. A vented rainscreen helps damp OSB to dry out.
JR,
Martin answered your question, but the question - and hence the answer - is far too narrow to be meaningful.
First, condensation within the thermal envelope is a problem only if:
1 - indoor humidity is uncontrolled by spot and general ventilation
2 - the walls are open to air movement
3 - the condensation surface is vulnerable to moisture (such as OSB)
Since good building and responsible living practices require indoor humidity control and an air-tight assembly, the primary route of water entry into the structure is almost invariably external leakage (all building exteriors will leak at some point). And this bulk leakage - through roofing, cladding, doors, windows, flashings, failed caulking, etc.) can be considerable.
So it become essential to durability that the thermal envelope be allowed to dry. While the "warm sheathing" approach may prevent the unlikely occurrence of condensation from the interior, it will reduce a wall's drying potential while at the same time maintaining the warm conditions that are conducive to the growth of mold and decay organisms (studies have proven this).
From both your answer and Martin it seems as though there is a delicate balance between having a tight shell to prevent air infiltration and at the same time allowing the building to breathe. As I try figure out the best way to incorporate good building practice(s) into my addition project it seems like there are many things to think about...while also trying to stay within a budget. An additional problem Im having is incorporating the requirements for living in a 110mph wind zone and the use of much more framing lumber to meet this requirement.
What I have settled on is using dense pack cellulose between my 2x4 stud cavity with rigid foam insulation on the inside, and using a rain screen on the outside to assist in keeping the shell as dry as possible.
I greatly appreciate both you and Martin for your dedication and committment to this website, it has been a wonderful resource for me...
JR
JR,
It seems that one of your statements is based on a misunderstanding. You wrote, "there is a delicate balance between having a tight shell to prevent air infiltration and at the same time allowing the building to breathe." In fact, both goals are easily met without any "balancing" or trade-offs.
The word "breathe" is misleading, so I usually avoid it. Most people use the phrase, "a wall needs to breathe" to mean "a wall needs to be vapor permeable so it can dry out when it gets wet." They don't usually mean, "a wall has to be leaky, with air blowing through it."
For example, when an old-time carpenter says, "I don't like to use a plastic vapor barrier because a wall needs to breathe," he's talking about vapor permeability, not air leakiness.
So there is no contradiction between having a tight shell to prevent air infiltration and "allowing the building to breathe." Walls can be very air tight and still be highly vapor permeable.
Martin
I appreciate your responses, having learned the craft from "old time" carpenters much of my thought process is based on the vernacular of old school.
Based on my response #7, do you feel that my plan of attack will achieve the goal of having a tight shell to prevent air infiltration while being highly vapor permeable (if I may use your choice of words...)
JR
JR,
Your wall design will work, but your description does not include air barrier details. It's up to you to make the wall as airtight as possible.
I suggested that you use the airtight drywall approach. The means using gaskets or caulk between the drywall and your bottom plates, as well as between the drywall and top plates. You would also need to buy airtight electrical boxes with gasketed flanges.
Alternatively you could establish your air barrier at the wall sheathing, using peel-and-stick tape to seal your sheathing seams (or the Zip system).
Either way, there are lots of other air leaks and penetrations to address -- between your bottom plates and the subfloor, at wiring penetrations and plumbing penetrations, at the interface between your walls and ceilings ... and so on.
So, when you ask, "Will I achieve a tight shell?" my answer is, "Maybe. It's up to you."
Martin
As long as I know what to address and how to address the specific area I can follow your advice. One follow up question...if I were to use a peel and stick tape would I not need to address the drywall side of the wall? What tape would you recommend in that regard?
Many thanks...
JR,
If you establish an air barrier at the wall sheathing, it isn't necessary to make your drywall air tight. But be careful of transitions: if you draw your air barrier on your section drawings, you should be able to trace your air barrier all the way around the conditioned space without lifting your pen from the paper. At each transition (foundation to floor framing, floor framing to wall, wall to ceiling, etc.), you'd better have a good plan to make the transition air tight.
To get details on how to tape wall sheathing seams, read:
"Airtight Wall and Roof Sheathing."
I would have to respectfully disagree with this statement.
In a heating-dominated climate, where the potential for condensation is from exfiltration of warm, moist air into the thermal envelope, the most effective place to create an air barrier is on the inside (stop the moisture at the source).
Relying on the exterior skin as the air barrier could lead to problems if air channels on the inside and within the thermal envelope weren't carefully sealed. For instance, if electrical boxes and bottom and top plate electrical penetrations weren't properly sealed, there is a high probability of the most dangerous type of air movement, called channel flow. Channel flow is where warm, moist air enters the wall at one point (often a low electrical box) and exits at a distant point (often an open hole in the top plate), typically due to stack effect pressure differences or interior positive pressure from unbalanced mechanical systems.
This gives the moist air a long flow path to cool and condense over a large surface area, in spite of an air-tight exterior sheathing layer.
So either an interior or an exterior air barrier location requires the same level of care in air sealing cracks and penetrations, and in either case the drywall (or interior skin) should be as air-tight as possible.
Robert,
To paraphrase, you say the "warm sheathing" approach creates conditions that can lead to mold and decay organisms. Can you please post some links or references to the studies that you mentioned? Thank you!
Robert,
1. You will notice that I recommended to JR that he should establish his air barrier on the interior, using the Airtight Drywall Approach. On that issue we agree.
2. I advised him that if he chose instead to establish his air barrier on the exterior of the sheathing, he didn't need to include ADA details. Here's my reasoning: air in always equals air out. If there is no air leaving the wall cavities because an air barrier has been established, then no air will enter the wall cavities.
3. In your example, you speculate what would happen if there were an open hole in the top plate. Obviously, I agree with you: if there are open holes in your top plate, it's easy to imagine air entering the wall cavities through the electrical boxes. But if you are building a house with holes in your exterior wall top plates, you're building a house without an air barrier. Seal the holes! If you decide to include holes in your envelope, all bets are off.
This is the primary study, which concluded: "The presence of thermal insulation on the exterior of a wet stud cavity (due to construction deficiencies) tended to increase the duration of warm conditions at the bottom of the wet stud cavity, reinforcing the need to minimize water entry into the stud cavity."
http://www.nrc-cnrc.gc.ca/obj/irc/doc/pubs/nrcc47066/nrcc47066.pdf
The Florida Solar Energy Center also did a 10-year simulation of roof systems in cold and hot climates, deliberately introducing a roof leak in year three. Their conclusions were similar: non-breathing assemblies that get wet don't dry out. http://www.astm.org/DIGITAL_LIBRARY/JOURNALS/JAI/PAGES/JAI102057.htm
My point, Martin, is that we have to be very leery of simple answers (which is what most of the building industry is seeking).
It's very easy to assume that, with an air-tight exterior, far less attention has to be paid to interior air-sealing details. And you reinforced that perception by stating that the interior drywall did not need to be airtight with an exterior air barrier.
While the air-tight drywall system is not popular because it requires extra attention to detailing during all phases of construction - that's its great strength. Attention to detail is what defines the difference between a durable structure and one that only appears so.
Robert,
What is wrong with "simple"
Of course attention to detail is important .. no matter where we choose to air seal.
It seems to me that the advantage of sealing at the exterior is that there are fewer penetrations, intersections and "nodes".
John,
I'm all for true "simple". In fact, my design goal is always "simple and elegant".
But the "simple" answers that almost all builders are looking for are far too often "simplistic", because they fail to factor in the ramifications and consequences or fail to comprehend the big picture.
Yes, air sealing at the exterior is "simpler", but it makes sense only if the air we're trying to seal out of the thermal envelope is originating from the outside. Building a moat around a castle (or a fence at the southern border) is useless if the enemy is within the castle (or in DC and Wall Street and the BP corporate headquarters).