Will this wall assembly last 50+ years and a detail question.

The goal is to make this insulation last 50+ years in climate zone 5, at 8,500 ft. in Fremont County Colorado (high altitude desert).
The envelope (from the outside in) is planned to be:
Concrete Fiberboard planks
Rainscreen
Tyvek Commercial D wrap
1/2″ Plywood taped and rolled (Yes, there is a slight risk, but it is a dry climate).
It is a 12″ deep 2×6″ loadbearing exterior framing with a non-loadbearing 2×4″ interior double stud wall.
The insulation plan is:
A bead of spray foam around the edge of each stud bay, then immediately press in 2″ of recycled EPS rigid foam board using a bay-sized brace made from 2x4s and plywood to hold it until the foam finishes expanding, then 6 inches of recycled Polyiso with spray foam around the edges until the stud bay is filled. First vertically until the 5.5″ bay is filled and then horizontally offsetting seams until done.
The EPS is there because it doesn’t shrink, and it will insulate the Polyiso (hopefully) enough to prevent the blowing agent from liquifying in cold weather. The spray foam offends me, but it is a small amount and will serve both as an adhesive and as it expands should fill any gaps or other air infiltration around the edges.
This will leave the interior 2×4 stud wall empty and I may or may not put some fiberglass in that space after electrical, plumbing, and fresh air exchange ducting are complete.
The logic is that it is way cheaper than spray foam, should last longer than fiberglass or dense-pack cellulose, avoids most moisture problems I can think of, uses recycled insulation and creates an air barrier that should be very effective. It is more labor intensive, but I am semi-retired and have a limited budget.
Should the horizontal seams of the Polyiso facing the interior be taped?
Why wouldn’t this insulation last 50+ years?
GBA Detail Library
A collection of one thousand construction details organized by climate and house part
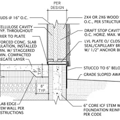
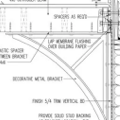
Replies
"The logic is that it is way cheaper than spray foam, should last longer than fiberglass or dense-pack cellulose"
I'm curious about this statement. My experience is that fiberglass and cellulose last forever unless they're disturbed. Usually their disturbed by construction, often the initial construction of the building. Rodents would be the other major cause of damage.
I don't see this assembly being any less prone to damage. If the plumber needs to make room for a pipe he's going to hack away the insulation.
Mhenson,
As a general rue of thumb if you don't see an assembly being used, either by the production builders around you, or the high performance ones who's work often features here on GBA, there is probably a good reason for that.
Cut & cobble in an insulation choice of last resort, not something you want to include in a new build. https://www.greenbuildingadvisor.com/article/cut-and-cobble-insulation
The main advantage of double walls is being able to get whatever depth of permeable insulation you want by adjusting the gap, while not having to use more framing. I don't see much sense in either only insulating the outer one, or using an insulation (foam board) that is best run continuously on the inside or exterior of the studs to reduce thermal bridging.
As DC said, there is no reason to believe that either fibreglass or mineral wool batts will deteriorate during the lifespan of your house.
My advice would be that rather than inventing a novel wall assembly, you choose one among the ones that have been successfully built, which suits your needs, and closely mimic it.
Piling on to Malcolm's good advice above, I've been in your position where it's really tempting to make things better than everyone else's standard procedure. "Oh, I'm doing the labor so it's really not costing that much more..." "Those other guys are hacks and I'm going to do it sooo much better..." "I'll appreciate this on a cold night..."
REALITY CHECK. It doesn't make that big of a difference. It takes way longer to do than you can ever imagine. That time costs money. That time (and money) can be better spent elsewhere.
I'm not saying to build a cheapo production house. Far from it. Build a high performance home that you are proud of, but you really need to question some of the ideas and even goals that aren't backed up by experience and data. There is a diminishing return in R value above a certain thickness for your climate. That's why we don't build homes with three foot thick walls. We could, but at what cost? What benefit?
The double stud wall exists because it makes a well insulated wall simply. It doesn't depend on unproven methods or require more complicated tools and techniques than what a typical builder can handle. There's no reason to complicate it.
Anyway, I hope I didn't come off as too harsh but sometimes I wish the more experienced builders were more harsh with me and my ideas when I was starting out and trying things that complicated the build for marginal improvements.
Well, that is sobering, but I do appreciate the insight and respect your experience. I did read the entire Cut and Cobble article. I have been researching this build for two years, most of my experience is rapid, to code, profit-motivated, single-family homes I am not an expert and a novice regarding the high-performance envelopes you build.
My first question is can someone please point me to where fiberglass and dense-pack lasted 50+ years everything I can find via many, many, Google searches and manufacturer's websites say I will be having to replace it in 20 or so years or even dense-packed it will sag and leave a gap at the top in 10 or 15 years. This was the primary reason I backed off of those products.
I built a large two-story three-car garage at my current home with 4 inches of properly installed exterior rigid foam. I hired a framing and finish crew (paid hourly), and they knew how to do it. Well sort of, I worked with them through the whole project to ensure the detailing was correct. It was so painfully hard, we didn't have very many communications problems, but they just hated the detail work and generally argued many of the assembly details I printed out for them from the Green Building Advisor detail library. Also the amount of rework because of the super long fasteners, and missing clearly marked studs or trusses. The building was completed correctly, it is cheap to heat and is exactly as advertised, but I decided I wanted little to do with exterior insulation in future builds. The double stud wall makes more sense to me and the framing and sheeting are easy. The thermal break is created by the double stud wall.
It isn't so much that I was trying to do it "better" than how it is generally done, but because I can get the recycled rigid foam for less than fiberglass R-value per sq ft. I have watched about 20 videos on how to dense-pack cellulose and am confident I can do it right with a small crew. When we did the garage a couple of guys on a table saw with a diamond blade (way better than the foam-specific blades I tried) could rip through many sheets of rigid foam and stay ahead of the guys installing.
This house will require only two sheets inside the stud bays a 2" sheet of EPS and a 3.5" polyiso. or 2.5" EPS and a 3" polyiso sheet. The rest will be full-sized sheets run horizontally between the stud walls and create a good thermal break.
If dense-pack will really last 50+ years would you recommend 2" of EPS on the exterior wall and then dense-pack in the 2x6" stud bays R36? Then dense pack again in the space to the drywall R62 (which seems like over-kill)or just run 3" rigid foam horizontally in the space between the stud walls for R51 and leave the stud bays of the 2x4" walls empty?
M Henson,
You wrote, "Please point me to where fiberglass and dense-pack lasted 50+ years; everything I can find via many, many, Google searches and manufacturer's websites say I will be having to replace it in 20 or so years."
Fifty years is nothing. My house is 44 years old, and every time I've opened up a wall, the fiberglass batts look fine -- dry and relatively pristine.
I can't imagine what event would occur to make my fiberglass insulation fall apart in the next six years.
Glass fibers don't rot. We have plenty of examples of glass vials (small bottles used to hold perfume) from the Roman Empire.
One other detail, my building inspector has approved, that if we fill the stud bays with rigid foam we are not required to install fire breaks in the stud bays which saves more labor and allows full-length foam sheets except around windows and doors.
What specific R-value are you trying to achieve in the walls?
I would be fine with R45, the biggest thing for me is the 50+ year lifespan. I guess with 1.5" or 2" rigid foam in the space between the walls it would be more cost-effective. I like the idea of leaving the 2x4" stud bays open because it makes electrical and plumbing a cakewalk. FYI I used Great Stuff for Windows and Doors to make insulation boxes for some heat transfer pipes and it makes stronger connections than the EPS itself.
I'm still not sure why you want to use rigid foam so badly. I understand that reclaimed foam is a good deal in R-value per square foot, but I doubt that it's cheaper than cellulose. A double stud wall filled with cellulose is easy to build and there are thousands of them in the Northeast that have been durable for years. Some of these were built in the 1980's, so yes, they can be durable for 50+ years. As mentioned earlier, so long as you keep them dry and rodent-free, they will be good indefinitely. And rodents are not just an issue for loose fill insulation - they are more than happy to tunnel into rigid foam as well. Not sure what insects you have up there, but termites and carpenter ants both love rigid foam.
The open inner 2x4 stud bays are convenient for utilities, but really only during the initial stages of construction. Once the rough-in is complete, the cellulose goes in just fine, stuffing the whole wall solid. I suppose having open stud cavities might make life easier during future rework, but I'm not sure that's worth all the trouble you're describing. If you just really like the rigid foam between the two stud walls, why not install cellulose in the outer stud bays to keep the polyiso warm, then do the clear runs of foam on the inside face. Tape the seams to act as a vapor retarder & inside air barrier. The do whatever you want in the inside stud bays.
FWIW, your high desert climate will make any wall system much more resistant to moisture damage than the same wall in a wetter climate. Even during cold winter weather, the very low humidity will help to dry out the walls to both sides, unless you operate humidifiers, then all bets are off.
I own a house built in 1976. It was insulated with fiberglass when new. Where undisturbed the fiberglass hasn't changed at all.
Thank you for the reality check. I will focus on dense-pack because it has properties that are more attractive to me than fiberglass. I will plan on filling the 2x6" stud bays first and over-pack them a little to reduce sag risk. This will also allow me to partially insulate the house before installing electrical and water lines. Then place another membrane on the 2x4" stud wall to fill the rest flush. The exterior will be done correctly and regularly inspected to avoid rodent problems. We have a bigger problem with chipmunks here than mice. There are lots more mice, but the cute/evil chipmunks are so tenacious.
Can someone tell me if running a taped and sealed peal and stick like Grace Ice and Water Shield at the bottom 12" or 24" of the Exterior CDX will be cost-effective additional insurance at repelling rodents/insects, just in case they eventually find a way behind the rain screen or would it be better to run treated plywood or? The walls are 10ft high plus the raised heal trusses. I will only be using stainless steel or urethane-coated fasteners on the exterior.
mhenson,
I'd caution against covering the bottom of the sheathing with an impermeable membrane that will inhibit drying to the outside. My approach is to stop pests at the cladding. A rain-screen gap means you can be more liberal with sealants around windows and other openings, as the materials can dry into the cavity. Rather than rely on insect screen, cover the bottom with perforated flashing. Something like this: https://www.menzies-metal.com/metal-flashings/perforated-j-channel-rain-screen-low-back/
If you absolutely want to keep rodents from gnawing, I find that a piece of galvanized j-bead on all exposed edges of sheathing is very effective:
https://www.homedepot.com/p/ClarkDietrich-1-2-in-x-10-ft-Metal-J-Bead-M401-10/311364897
However, the most important thing is ruthless air sealing. My observation is that rodents don't aimlessly gnaw at buildings. They look for openings and widen them, and what seems to attract them is drafts. They don't seem to attack cracks that are filled with caulk or spray foam, even though they could easily chew through it if they wanted to.
DC,
Akos shared an interesting tip yesterday: He embeds steel wool in spray foam he uses to seal holes.
I've had success with that, too. But I use either stainless steel or copper wool for longevity.
The air movement thing is real. Critters, mice especially, are attracted to cracks and holes with air movement, as it means they go somewhere. They will often ignore dead-end holes. Spray foam and caulk are the most important anti-critter measures, with screening and perforated metal providing good insurance.
The good news is that all of the normal air-sealing techniques also help to limit critter problems.
Once they figure out a hole goes somewhere they will attack it repeatedly, and foam and steel wool is a good way to get them to give up. I'm convinced they can smell where another rodent has gone before because they keep trying to return to the same places, even if you kill the ones that are living there now.
I looked at both products, Malcolm, I really like that design, but can't use the product because aluminum is incompatible with the fire resistant fiberboard we are using for siding. Maybe if I tape the edge to keep them from touching.
DC, how would I attach that j-bead and still allow air movement for drying and water drainage?
LOL, if there is one thing I have learned from you, Malcolm, Martin, and others on this site it is ruthless air sealing, followed by more detailed air sealing, and then cost-effective insanity air sealing.
LOVE, the steel wool spray foam combination for smaller penetrations!!