Why not place for insulin between osb and studs
I am building in Northwest ohio, zone 5. I am building 2×6 walls 24″ oc with the cavities filled with open cell spray foam. There will be 7/16 osb on the exterior with a tyvek type wrap and furring stripe to allow air drying under the siding. I haven’t seen any mention of using thin foam sheating between the osb and studding for a thermal break. It seems that the osb would dry to the exterior and underneath the foam would dry to the interior. I am probably overlooking something obvious and would like ideas on this.
GBA Detail Library
A collection of one thousand construction details organized by climate and house part
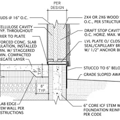
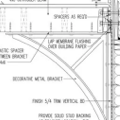
Replies
The sheathing is structural, keeping the walls from twisting and racking in high wind. Putting insulation between the OSB and studs requires doing the engineering analysis.
There are commercial products (eg Huber ZIP-R ) with insulation pre-laminated to OSB that will meet the structural requirements if you follow the manufacturer's fastener type & spacing requirements.
In zone 5 you would need at least 1.25" of rigid polyiso or 1.75" of Type-II EPS (2" of Type-VIII EPS) between the OSB and studs for dew point control at the open cell foam/rigid foam boundary to be able to get away with standard latex paint as the interior vapor retarder.
Put EPS outside of the exterior sheathing. This:
1) is better structurally
2) keeps the sheathing warmer/dryer
3) prevents excessive wetting of the OSB from the exterior
If you don't want to do this, then I'd put the EPS on the interior side - it's better structurally.
I just designed a home addition near Cleveland using Huber's Zip-R9 insulating sheathing. One advantage is that any insulation will work on the interior; there's no reason to use spray foam, which doesn't insulate any better than cellulose, mineral wool or fiberglass, and the sheathing provides airtightness if detailed properly. By not using spray foam, the home is more easily renovated in the future, and petroleum is put to better use.