Why install foam on the exterior side of a wall as opposed to the interior?

I am a builder in North West Montana (about an hour from the Canadian boarder). I have installed foil-faced poly iso foam to the interior side of walls (just under the drywall) with success for years. It seems a lot easier to deal with the thermal bridging from this side of the wall then the exterior – fewer things to go wrong. Why is there such a push to move the foam the outside?
I am familiar with Joe Lstiburek book Cold Climates and only partly understand the idea of a condensation plane. The book goes into detail on the idea of the sheathing (OSB or Plywood) as being the first condensing surface. It talks about the importance of keeping this surface warm and above the dew point. As I see it however, vapor doesn’t need a surface like OSB or Plywood to condense on, it will be perfectly happy to condense on fiberglass or anything else which is below the due point. It seems like what is far more important is to keep the warm, moist air out the wall no matter where the foam is. Any thoughts?
Also, in my area, I have been seeing far more closed cell foam being used. Recently, I was in a house where the contractor sprayed 2 inches of foam in the 2×6 walls and then added an R-13 batt over the top. (A similar version of this was done in the cathedral ceiling using 4” of foam). No vapor barrier was installed under the drywall because the idea was that the true vapor barrier is the foam within the wall (or rafter). I can’t say for sure what is wrong with this design, but something doesn’t seem right to me about this. Thoughts on this?
Thanks, Mark
GBA Detail Library
A collection of one thousand construction details organized by climate and house part
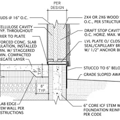
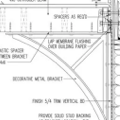
Replies
Mark,
You're right that the moisture in warm air will condense on any solid material that's below its dewpoint, but the amount of moisture that can collect on tiny glass fibers is infinitesimal and the water vapor will disperse throughout the vapor-open fiberglass batt.
condensing surfaces are solid membranes that literally stop the water vapor because of a sudden change in vapor permeance. If that condensing surface is cold enough to be at or below the local dewpoint and also made of a hygroscopic material, then we have not only condensation but moisture accumulation - and that's the real problem.
Sheathing, typically made of plywood or, more commonly today, OSB, are perfect condensing surfaces, as is the backside of plastic housewrap if moisture makes it that far. So the theory which has gained popular support is to keep the exterior sheathing above the dew point by the use of exterior foam insulation and, at the same time, reduce thermal bridging from the sill to the rafters without interruption at rim joists.
One problem with this approach, as you probably intuit, is that exterior foam is often a wrong side vapor barrier. This may not be much of an issue of the thermal envelope is very air tight and the wall can dry to the interior. But it can easily become a problem if there is any air leakage (by homeowner action, for instance), or uncontrolled indoor humidity, or if there is ever an exterior leak through the foam board (bad flashing or failed tape joints, for instance).
Since, in a cold climate, most vapor drive is from the inside out, drying to the inside may not be sufficient to reverse any potential wetting of the sheathing or framing. The wall could accumulate moisture all winter and, since the sheathing is now maintained at a warmer temperature, it could be in the growth zone for mold (tests have confirmed this).
Your instincts are correct. Walls and roofs perform better and are more durable if they can "breathe" or dry in both directions, as well as safely store moisture until they can dry. That's why hygroscopic insulation, like dense-pack cellulose, is preferable to any kind of foam. And, in a cold climate, rigid foam is more appropriately located on the inside, where it can serve as air and vapor retarder.
The simple answer is that installing foam on the outside makes the foundation wall available as a thermal mass during air conditioning season. Installing the foam on the inside would solve a world of problems but would be best done in a heating dominated environment like yours. While I understand the desire to install fiberglass inside of a closed cell "flash" coat, I share the feeling that this arrangement could end in tears since it represents a "wrong side vapor barrier" for you. Simply put, try to keep an open diffusion to the outside. If you have to choose, place your foam in the inside surface. Don't forget the flame spread requirements of this assembly and give extra attention to soil drainage.
Tony Olaivar- BPI Professional, HERS Rater Lanz Heating and Cooling
The OP wasn't talking about foundation walls, and inside thermal mass is at least as important in a heating-dominated climate. Massive foundation walls should have insulation either on the exterior (unless in termite country) or midline (such as the ThermoMass wall system).
My first thought was that the outside is easier to get a continuous thermal break & R value. Inside that is more of a challenge?
Mark,
Your method can work fine. I have also built homes with polyiso under the drywall, so I know that such homes can perform well.
However, there are two possible problems or drawbacks:
1. With interior foam, there's no easy way to address the rim joists. With exterior foam, you just continue the foam over the rim joist areas and partition intersections.
2. Your method raises a new problem: the "cold OSB" problem (or its somewhat less scary little sister, the "cold plywood" problem). If you use diagonal board sheathing, you don't have to worry about this problem.
For more on the cold OSB problem, see How Risky Is Cold OSB Wall Sheathing?
Martin,
How do you balance the "cold OSB" problem with the "foam vapor retarder" problem created by the foam plastic sheathing applied to the exterior of a wall?
Tom,
I'm not sure what you mean by a "balance."
But if a wall with exterior foam sheathing is designed properly, it will dry to the interior. Moreover, the sheathing (or the interior surface of the rigid foam) will always stay above the dewpoint temperature, so there's no reason to believe that moisture will accumulate inside the wall.
By what driving force?
If there is exterior foam insulation and an air gap or fully ventilated rainscreen, then there will be little solar radiant drive.
If the only remaining drive is vapor pressure, then the wall cannot dry to the interior unless the interior vapor pressure (or relative humidity, if the temperature is constant) is significantly less than inside the wall cavity.
In a tight house with mechanical ventilation, the indoor RH will likely remain at a relatively constant 40% or so, and in the summer the RH will almost certainly rise. If the inside summer temperature also increases, then the vapor pressure drive is still from inside to out.
There will be some inward thermal drive in the summer but, limited by the vent gap and continuous insulation, will it be enough to dry the walls?
And what happens if there is ever even a small external leak from driving rain or an ice dam or an internal leak from a sweating or leaking pipe?
The simple answer is that a cold climate house should be able to dry in the dominant moisture migration direction - inside to out - and a resilient and durable house is one that can dry in both directions and safely store excess moisture until it can.
Otherwise it's like believing we can dam up a river to control flooding and discovering (as did the Army Corps of Engineers) that it only limits routine flooding and instead results in occasional catastrophic floods.
You can't fool Mother Nature.