Why do contractors not want to consider heat pumps as primary heat source?
One contractor told me that oil is more efficient than a heat pump. The MassSave guy told me that oil is “not bad” and initially said that wood was a fossil fuel, though he did correct himself when I looked kind of shocked. No one, including MassSave, has mentioned insulating the apparently totally uninsulated basement, though they suggest tearing up half the floor in the attic to add more insulation.
GBA Detail Library
A collection of one thousand construction details organized by climate and house part
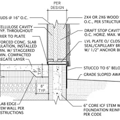
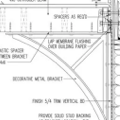
Replies
Remember none of these people have much training in comprehensive building science. Even MassSave just works with the menu of solutions they have. They have limited training to select off that menu.
If you want a heat pump. Get an engineer or energy specialist to design a system including a Manual J and duct system. Then have contractors bid the exact design.
I don't think MassSave is currently insulating basement wall, but they may do basement rim joists. They definitely blow cellulose anywhere they can, which can be good or bad. Tearing up your floor, air sealing the ceiling, and adding more insulation probably makes sense.
>"The MassSave guy told me that oil is “not bad” and initially said that wood was a fossil fuel, though he did correct himself when I looked kind of shocked. "
Clearly there are no rocket scientists wasting their carreers as MassSave auditors, eh? :-)
The subsidies for different weatherization efforts change from year to year, and the auditors are expressly discouraged from making recommendations that go outside of the program. They used to subsidized some amount of unvented roof insulation, now it's attic floor-only, so that's all they're allowed to suggest for attic insulation. Even if they happen to know more about it (some do), they can't go off-script.
Ripping up the attic floor and installing a second set of joists perpendicular to the existing joists to accommodate R50 then replacing/re-using the floor decking is still usually a lot cheaper than insulating at the roof deck, and still worth taking the subsidy on.
MassSave will currently subsidize insulating and air sealing the band joist and foundation sill with a couple inches of closed cell foam, which is also worth it. If you go ahead and insulate the interior side of the foundation on your own dime and there's access to spray foam the band joist on down to the top of your wall insulation they'll still subsidize that.
If you have a heating history with the old boiler, run a fuel-use based load calculation on some wintertime fill-ups to sanity check any other load calculations. It's not hard, and it's a measurement of the homes performance where-is-as-is at the state of air sealing & insulation there was at that time. To see how that's done, look here:
https://www.greenbuildingadvisor.com/article/out-with-the-old-in-with-the-new
All oil boilers are oversized for all normal-sized insulated houses. Compare the burner size to your fuel-use load calc. Oversizing is not your friend.
Thanks for all the input. None of the contractors did a load calculation. My oil boiler is supposedly 83.5% efficient. Last winter we used 2.96 gallons of oil a day for a 45 day period for which the HDD was 1423.5. The outdoor design conditions chart says the 99% temperature is 6 for a town near where I live. The walls are 2×4.
The windows are mediocre but double-pane. The smallest bedroom is only about 99 square feet, and the largest only 121.
A gallon of oil is good for 138,000 BTU/hr source fuel, so at 83.5% only 115,230 BTU/gallon goes into the heating system.
The ~3 gallons/day x 45 days is 135 gallons, over 1424 HDD is 0.095 gallons/HDD, or ( x 115,230 BTU/gallon =) 10,947 BTU/HDD. In a 24 hour day that would be (/24=) 456 BTU/degree-hour.
So when it's +5F outside (Worcester's 99% temperature bin) and a presumptive heating/cooling balance point of 65F (the HDD base temp) you'd have 65F - 5F= 60F heating degrees, for a implied design load of 60F x 456 BTU/degree-hour= 27,360 BTU/hr.
At Framingham's +6F design temp it would be 59 heating degrees, and an implied design load of 26,904 BTU/hr.
When it's 0F outside (both Lawrence & Springfield's 99% design temp) you'd have 65F heating-degrees for a design load of 29,640 BTU/hr .
With more data on thermostat settings that can be fine tuned a bit, but that's the order of magnitude you're looking at.
The smallest oil boiler burners that work with US #2 oil is 0.6 gph, which at 85% efficiency comes in around 70,000 BTU/hr, more than 2x oversized for your likely heat load.
A 3 ton heat pump solution with a cold-climate type compressor would have you covered with margin eg:
https://ashp.neep.org/#!/product/25915 (multizone compressor, mix of ducted/ductless)
...or...
https://ashp.neep.org/#!/product/25352 (fully ducted with a small cassette type air handler)
After insulation & air sealing up grades reduces the load, a 2.5 ton (or maybe even a 2-ton) modulating cool climate heat pump may be more optimal.
https://ashp.neep.org/#!/product/25351
https://ashp.neep.org/#!/product/26173
For sanity checking purposes, how many square feet of fully conditioned space?
How many square feet of basement (assuming the boiler is in a basement, not a garage or some other mechanical room)?
Thanks for your detailed reply! There are 912 square feet of conditioned space. The basement is also 912 square feet. About 450 of that is finished, but we just use it for storage. Although there is a separate zone in that 450 sq ft room, the heat has not worked for years, but it is warmed somewhat because the oil boiler is in the adjacent, unfinished space.
That MassSave stuff aside, I think the main problem is that northern contractors simply are not up to date on the cold weather performance of heat pumps, so they assume it won't work in the climate. They don't have incentive to know either, as heat pumps are not something they've had to deal with. That should change over time.
There are PLENTY of contractors in Massachusetts that are fully up to date on what you can do with cold climate heat pumps. (Unfortunately many of them are too willing to stoop to gross oversizing in lieu if proper load calculations, which is why it's better to have a qualified third party run the numbers before soliciting proposals.)
Even MassSave offers subsidies for cold climate heat pumps, and 0%/7 year financing for a complete heating system if it meets minimum efficiency specs.
Sorry, I didn't mean to imply no knowledgeable contractors were available. There certainly are plenty, but that sort of knowledge is still not common among contractors in general. Or am I simply out of date on that front?
General contractors in my area are definitely NOT on top of cold climate heat pump capabilities, but nearly all mechanical contractors & HVAC pros installing heat pumps are- especially now that they're being subsidized by the state programs.
"Heating & Plumbing" contractors who mostly install boilers but somehow got into mini-splits when the price of #2 oil was north of $4/gallon and climbing usually don't get it and would rather sell you something they're comfortable supporting, (such as another hydronic boiler.)
Experience has taught me to not trust the installers to correctly size the things, even if they run a pro-forma Manual-J. Ductless contractors are sometimes clueless about which heads & cassettes are compatible with which compressors too, but I suspect that's getting better.
There are dozens of competent Mitsubishi installers in MA, where they own a lion's share of the market. (Their regional contractor training and design center is in MA.) Trane is now installing Trane-branded Mitsubishis in MA too, as well as their other heat pump offerings. Once you have a good idea what the load numbers are and have it sketched out in black & white, if Mitsubishi is a vendor you're comfortable with there are usually at least a handful of contractors within a half hour drive of any MA location. Plug in your ZIP code here:
https://www.mitsubishicomfort.com/get-started/contractors
Fujitsu has a comparable contractor-finder (but fewer contractors per square inch in MA. :-) )
https://contractors.fujitsugeneral.com/
My own strategy has been (and continues to be) to run the load numbers of the "after building upgrades" condition of the house, come up with a couple of plausible solutions using the equipment specs and engineering manuals online, then solicit bids or counterproposals from local contractors. YMMV It's worth listening to objections or alterntives from the installers, but that doesn't mean they're always right.
This is really helpful info, since I have some grandparents in MA that could really use a mini split (they've been relying on window units for AC). Looks like they have a lot of contractors nearby, two in their town alone! Thanks