Which Weather Resistive Barrier behind new masonry?

I’m coming up on a project involving cladding Structural Insulated Panels (SIPs) with a full-thickness veneer natural stone wall. So, from the outside in, it will be stone – 1″ gap – WRB – 6.5″ SIP panel.
Question: Which WRB is preferable?
Context: I am in northwest Ohio.
The following page on this site’s Product Guide lists a number of products, but links only to manufacturers’ info: https://www.greenbuildingadvisor.com/product-guide/cat/water-resistive-barriers
Of course, each manufacturer claims their product is superior. SIP manufacturers specify 30-pound building felt. My masonry supplier suggests one of the high-tech things. While I’m inclined to go with the traditional felt, some sources claim it disintegrates in less than a century, and I’m hoping the WRB maintains its integrity for at least that long. Is there enough data on the new products to support their use as a long-term WRB? What about synthetic felt? I fully expect to layer the WRB shingle-style, and not rely on tapes or mastics of any kind.
Wisdom of the crowd is greatly appreciated!
GBA Detail Library
A collection of one thousand construction details organized by climate and house part
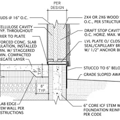
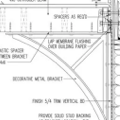
Replies
Andy,
First, a warning: you are choosing a particularly risky combination of cladding materials and sheathing materials (stone veneer over OSB). Many homes with these materials have suffered problems with rot. You'll need impeccable workmanship to succeed with this plan.
Inward solar vapor drive and water leaks put this type of wall at risk, so you'll need to be sure that you have a good air gap with ventilation openings at the bottom and the top of the wall. It is essential that you prevent mortar from clogging this air gap. The safest way to proceed is with a three-dimensional plastic drainage mat enclosed on both sides by a WRB. This mat would be installed between the stone and the SIP.
Needless to say, all penetrations, including windows and doors, must be very carefully flashed.
I think it's a good idea to start out with #30 asphalt felt to protect the SIP. From there, you could install the plastic drainage mat, followed by at least one more layer of WRB -- your choice.
More information here:
All About Water-Resistive Barriers
Stone and Synthetic Stone
Martin,
I knew this plan might be risky, and your feedback is making me reconsider. Most of the articles on this topic deal with thin masonry veneer and stucco, which has its troubles--I was hoping to avoid some of those by going with full-thickness masonry and the air gap.
The NAHB article referenced at "All About WRBs" acknowledges that components of the WRB may not be durable, and also points out the problem of intrusion at fasteners and brick ties.
An additional concern is the brick ties themselves--not only is there no underlying structure behind the OSB cladding for attaching them, but if they are a possible moisture entry point then they will assuredly fail if 1/2" OSB is the only thing they're hanging on to.
If my first priority is durability, would you STRONGLY suggest changing my masonry-over-SIP plan? Although I have masonry ledges in my foundation, it's not too late to switch cladding.
Andy,
Q. "If my first priority is durability, would you STRONGLY suggest changing my masonry-over-SIP plan?"
A. Yes. I would never install stucco or stone veneer over OSB.
Just a tough...I saw this stone veneer system where the stone sit in a 2" thick EPS panel. Would that be safer due to the EPS reducing inward wapour drive? http://enduramaxwallsystem.com/
Martin, with much anxiety I have made the decision to stick with the original stone plan, and lean hard on the word "impeccable" when I detail the rainscreen.
(Marc, I have the foam system you describe, and decided against it for all the same reasons that I am not doing synthetic or thin veneer. Might work for some people, though...)
Just to be clear, I am installing full-thickness natural dolomitic limestone veneer, sitting on a 6" masonry ledge, that ranges in thickness from 3-5 inches.
Martin, all the drainage mat details I see online are specifically for stucco or veneer stone that's adhered directly to the wall. I will have capacious and irregular space behind most of my wall, with only a few nubs here and there coming close to the rainscreen. The only danger of mortar plugging the space would be the droppings at the bottom, and there wouldn't a u-shaped mortar catching mat or just a 2"-thick mat do the trick? Can you just say a little more about the rationale for your suggestion of using full-wall coverage of drainage mat, along with a second WRB on top of that? Seems like that's perfect for stucco or thin veneer, but somewhat redundant for my application. Just sayin', I don't know!
Is there a WRB product, superior to 30-pound felt, that is more self-sealing and therefore less likely to leak around brick-tie fasteners?
Advice of any kind is greatly appreciated.
Liquid applied WRBs will seal around masonry ties, but most of them are fairly high-permeance- too permeable to use behind masonry (but look some up, and read the specs, eh?)
A better approach would be a 1" shot of closed cell spray polyurethane foam, which will get you down to the 0-2 perm range, sufficient to dry into to a masonry cavity or rainscreen, but fairly resistant to the intense peak moisture drive of sun on dew & rain soaked masonry. It'll add about R6 to the stackup and add some structural rigidity, but your primary purpose for using it here is to protect the OSB from moisture degradation.
Dana, that is an interesting proposal. Cost would seem high, but Martin's suggestion above of a drainage mat and a second WRB doesn't seem any cheaper. As far as anyone else would care to weigh in, does this sound like the best possible solution?
If sun-driven vapor drive is the primary issue here, and budget is straining, would it make sense to add additional protection on the southeast and southwest walls only?
Like so many details, it's so tough to figure out the *right* thing--or the *best* thing. Of course, I'm getting conflicting advice from my masonry supplier, who insists I won't have any trouble with his 1950's-era approach.
As for the other approaches, would I just do drainage mat in the bottom 18" of the wall? Bottom half of wall? Entire wall?
Is there a WRB that is marginally self-sealing, like Grace/IWS but with an acceptable perm rating?
Thanks for ongoing help.
Andy,
Q. "Is there a WRB that is marginally self-sealing, like Grace/IWS but with an acceptable perm rating?"
A. Yes. I is called Cosella-Dörken Delta-Vent SA. Click the link to learn more. I think it is expensive.
Martin, thanks for that lead. A quick google revealed one quote of about $1.15/sq.ft. for the Delta-Vent, which puts it in the same ballpark as the other options here.
But let me clarify about the "self-sealing" thing. I'm worried about the brick ties. The Delta-Vent is self-adhering, which eliminates fastener holes for putting it on, but I still have to put screws through it to attach the brick ties.
Wait: might this be my solution: a combination? Use Delta-Vent to eliminate WRB fasteners, then use the more expensive and bulky spray foam in a spot application just over each brick tie?
That is NOT a rhetorical question... looking for an amen, or at least more feedback. Thank you all!
Delta-Vent is rated at 30-50 perms, which isn't exactly going to be protecting the OSB from the high moisture drives of the masonry unless you give yourself a ~2" cavity between the WRB and the stone that's vented at both the top and bottom for maximal convective purging. Something that permeable can dry much more quickly than the inch of foam solution, but it'll also HAVE to be able to dry quickly, which means the rainscreen cavity has to be substantial to handle it.
Delta-Vent is not any cheaper than a flash-inch of closed cell foam either. A flash inch of foam is in the buck-a-foot range, installed, and it's self-adhering (it's basically puffed up Gorilla Glue.) While there's something of an art to it, it doesn't take a Michaelangelo to get, a flash-foam job that is fairly smooth & consistent in depth. A 1/4" variance in depth doesn't mean much here- as long as the thin spots are at least a half-inch thick it'll work just fine as a vapor-retardent semi-breathable WRB.
OK, Dana, that Delta-Vent is too permeable--even Tyvek is down around 17, and we all take that as too permeable for a masonry-cavity WRB.
I'm using 2-part spray foam now to seal the gaps in my Structural Insulated Panel system, so it's a product I'm familiar with, and I betcha I could achieve a Michelangelo effect with it.
You're proposing I use this as the only WRB, instead of the 3o-pound felt or any other product. You say it has adequately low perm to protect my OSB and seal up my brick tie fasteners. But is 0-2 perms not TOO LOW? A bona fide visqueen-esque barrier? Or is it OK for this location?
Anybody else care to weigh in on this idea?
Andy, in your question you state "...some sources claim it disintegrates in less than a century, and I'm hoping the WRB maintains its integrity for at least that long." Yet then you specify an OSB SIP panel behind masonry? I would suggest you reconsider the strategy. You can strive to achieve 100% adherence to a "perfect" solution (air gap, WRB, poss SPF) but its unlikely you will. Its not to criticize your workmanship, its just the reality of how things go. I imagine you've read: http://www.buildingscience.com/documents/insights/bsi-029-stucco-woes-the-perfect-storm
And if your thinking 100 year durability, I'd look at a different design. Martin's first post was good advice.
Zero perms is too low, but ~1 perm nominal is neither too high nor too low, it's minimal class-II vapor retarder. Even at 3" thickness closed cell foam has about 10x the drying capacity of 10 mil poly.
At 6 mils Visqueen is about 0.05 perms, more than an order of magnitude lower permeance of a flash-inch of 2lb polyurethane, which is a "dries never"' scenario. We're not going anywhere NEAR that level of vapor tightness.
And yes, as long as it's protected from ultraviolet light, closed cell polyurethane will be a long lasting weather resistant barrier all by itself, far superior to #30 felt in this application. On a rooftop you'd have to coat it with a UV-protective paint/ballast, but if the solar UV ever gets strong enough to burn it's way through 3-6" of limestone methinks we're already toast, eh? ;-)
Sal (msg #12), you are absolutely right. On a number of levels I have been gut-wrenchingly dispossessed of the notion that my project will be "perfect:" Had I navigated to this depth in the WRB question a year ago, I would have changed course and dropped either the SIP or the masonry.
While I am not new to building, I am new to building science. Like these things go, the more I learn about it, the more I realize I don't know, and as a newbie it can be frustrating to search for the "right" answer. This crowd-sourced forum (along with Joe Lstiburek's BuildingScience.com) comes closest to the authoritative voice that I need, and I'm grateful to those who weigh in at length to help folks understand.
I realize now--SIP construction is not the best substrate for full-thickness masonry veneer. It rather sucks. It's got other issues, too, some of which I knew going in. I'm TOO far in, though, to change course, and I still have other people chattering that it's not an issue if it's detailed correctly. My gut tells me that Martin's first post IS correct ( it's a "particularly risky combination"), and so is Sal's caution that WRB trouble is "just the reality of how things go."
So I'm proceeding (deep breath....) At this moment I figure I'll run with Dana's suggestion of the spray foam, which at this moment seems not only acceptable but rather effective AND durable. For what it's worth, Sal or Martin, or others, what do you think of that idea?
Andy,
Take a look at using Greenguard's DC-14 as the WRB over the sips. It is a1/4" thick fan fold XPS with drainage channels on both sides. It is right at 1 perm and qualifies as a WRB if the horizontal seams are properly lapped and taped. It should cost way less than spray foam.
Jerry, the DC-14 product, overtop of GreenGuard housewrap, seems like a reasonable double-duty "belt-and-suspenders" approach. Then, sealing fastener penetrations with GreenGuard Caps or a patch of GreenGuard butyl flashing, and bob's your uncle. At least, according to GreenGuard.
I take heart from Joe Lstiburek's words, in his 2010 article "Mind the Gap, Eh":
"So, can we make OSB work? Yes, get a good water resistant OSB, a non-perforated surfactant resistant housewrap and make sure you have a gap between the cladding and the housewrap/OSB interface. You now have 1950’s durability coupled with awesome energy efficiency. And a whole bunch of structural strength that you may or may not need. But is it real nice to know that if you need the structural strength the wall won’t rot because you have that gap on the outside of the OSB. Knock yourself out with whatever cavity insulation you want. The gap makes them all work – including SIPs. Nuff said."
I just have to work through his caveats: the housewrap has to WORK; the gap has to be functional. Oh, he advocates non-perforated housewrap. GreenGuard is perforated. Sigh. Tyvek, then?
Andy,
With BOTH Tyvec and DC14 you'il definitely have a WRB! My question about using both is which should be next to the OSB? Putting the Tyvec on the outside would assure drainage even if there were a spot with mortar plugging the gap behind the stone. I'm sure either way will work, but which is better?
Jerry,
Excellent question, great point about creating a protected drainage space, as Martin suggested early in this thread (he actually advocated *two* WRB's with a 3-d drainage mat in between.) Hope he or Dana jumps in with an answer (or an opinion). The Tyvek has a perm of 17, the DC-14 is somewhere around 2. At this point, my head is spinning, and I'm still leery of the cost of combining multiple products, which will cost more than a single flash coat of 2-part foam....
Our German partner, Pro Clima makes a membrane especially for this purpose (although they primairly use it over woodfiberboard), but the concept should be the same for SIPs (but I agree with Martin that Brick over OSB is still a tricky combination).
It has a perm rating of 8 - Restrict inboard vapor drive, but be sufficiently vapor open to let any interior moisture out. It is called SOLITEX FRONTA QUATTRO, not in stock yet, but http://www.foursevenfive.com will have in stock in the fall 2013.
Video explaining the principle of Humida membrane behind brickwork (in german, but images speak for themselves"
Sealing brick ties can be done with TESCON No.1 tape.
Floris, another interesting suggestion. Over woodfiberboard? Wow-even more optimistic than me. Unfortunately, I need something available sooner.
ONE FINAL SUGGESTION has been floated: a spray-on WRB (not the 2-part foam). It is the following product: http://www.tremcobarriersolutions.com/products/enviroDri.asp
Claims to be effective for exactly my application. Here's the spec sheet: http://www.tremcobarriersolutions.com/fileshare/sell/TBS0566EnviroDriSpecSheet.pdf
Anybody have any experience with this product?
Andy,
EnviroDri is a liquid-applied water-resistive barrier. For more information on that type of product, see Housewrap in a Can: Liquid-Applied WRBs.
I have written a review of EnviroDri. Here is the link: New Green Building Products — July 2012.
Follow-up a month later, with a question:
I have nearly finished a total application of the StoGuard liquid-applied WRB. From here I will continue to follow SOME of Martin's advice from earlier in the thread:
"I think it's a good idea to start out with #30 asphalt felt to protect the SIP. From there, you could install the plastic drainage mat, followed by at least one more layer of WRB -- your choice."
So I've already substituted a 17-perm liquid-applied WRB for the tar paper, an expensive upgrade that feels more durable. I'm down with the plastic drainage mat to encourage drying. Question of the day is this: is it true that the fabric typically integrated with the drainage mats is NOT a second WRB, rather just a mortar-deflection layer? Should I instead install a plain drainage mat and then an actual WRB wrap? Or is there a drainage mat out there that comes with a bona fide WRB for an outside layer?
Thanks as always.
Martin,
Thanks. Those two articles point to the possible viability of liquid applied WRB's for my project. Unlike the suggestion of spray foam, they are designed for this use, and come with instructions and accessories to make it happen. Plus, it appears they'll come in at half the price of spray foam.
(It's also worth noting that the spray foam has very little tolerance for UV exposure, so it would have to be applied in stages, immediately before the stone is laid in front of it. The liquid-applied WRB, on the other hand, is rated for a 6-month exposure.)
Andy,
If you have applied a liquid-applied WRB, that will protect your wall sheathing. As you have correctly guessed, the main purpose of the WRB on the exterior side of the plastic drainage mat is to keep mortar out of the drainage gap. There are several available products on the market that integrate a WRB with a drainage mat. It's also perfectly acceptable to install the plastic drainage mat, and then any WRB you want -- whatever product you prefer.
Thanks, Martin. So a drainage mat with a simple mortar deflection fabric (not a WRB at all) is sufficient here, but.a drainage mat with an integral WRB (such as the HomeSlicker Plus Typar) may provide a smidge of extra protection.
With this assembly, how should the weeps at the bottom of the wall be detailed? Do they need to extend clear back through into the drainage mat through a slit in the WRB to ensure good airflow? In that case, is a mortar-catching device such as a thick mat still a good idea? My cladding is 6" thick to the sheathing, so I think I'll need two weeps end-to-end....
Andy,
At the base of your wall, you need high-quality flashing -- ideally stainless steel or copper -- that collects the water that runs down your WRB and conveys the water to the exterior at the weeps. You also need this flashing above windows, doors, and projecting roofs (like the roofs over bay windows).
Martin, I understand the need for a high-quality flashing. My question was about the inevitable mortar droppings clogging the air passages at the base: whether the WRB-mat-WRB combination reduced the need for a mortar-catching product; and how to go about detailing the weeps.
As for the flashing, the one I'm using is a composite 40-mil membrane called Textroflash, and they specify use of their proprietary stainless steel drip edge at the outer edge of the masonry, inserted below the outer edge of the flashing to "aid in egress of water". This drip edge is only 3" wide, so if I'm reading the spec sheet right, the manufacturer totally endorses their membrane product as the sole through-wall flashing, with only a wee bit of stainless visible at the base of the wall and tops of windows and doors.
http://www.h-b.com/images/installation/06TEXTROFLASH_install.pdf
I totally understand that a full stainless flashing would be better.
Andy,
For more information on weeps and flashing on this type of wall, I recommend the following article: Keeping Water Out of Brick Veneer. Although the article is (obviously) written with brick veneer walls in mind, most of the recommended details also apply to walls with stone veneer.
We too are planning a masonry over OSB SIP structure, and have reviewed as much of the pertinent literature on the subject. You MUST plan for a rainscreen type structure. Our solution, starting from the SIP face: WRM. 1x6 vertical battens, hot dipped galvanized nails, 1/2" Permabase fibre cement board, hot dipped galvanized nails, thinset,
Refer to: NTA Inc. "Guide to attaching sheathing and /or cladding through continuous foam insulation. also....
Laticrete MVIS systems,
also..,.. TRUFAST Ltd. monograph on nail/screw pull-out via a combination of dead load and negative wind forces (find out what the design wind speed is for your job site !) .
Hope this helps. Sincerely, Theo
Theodore Chabane and Andy: Men, how did you systems work out in the end? I am about to consider just such a system. Thanks.
William, it's done; whether or not it "works" is an open question for a few years from now. I'm very happy with how it turned out, but my appetite for risk in future jobs has diminished as a result of this project. Stone veneer is nice, but not THAT nice, and for THAT much money. SIPs have some wonderful advantages, but really, 1/2" OSB holding up a house? I feel confident of the "belt-and-suspenders" approach of two WRBs, integrated flashings and a generous air gap. I should have incorporated at least a BIT of a roof overhang, although that can be added. Martin and the GBA community deserve much credit for anything that "works" on this house, and I await the gentle "I told you so" for that which doesn't.
FWIW, I got LEED Platinum, but I'm too in debt to buy the plaque.