Which wall assembly is better in your opinions?

I have some clients that are asking me to review my wall assembly design for their home. My plan is to frame 9″ double stud walls with blown in dense pack cellulose insulation. They are wondering if it would be cheaper or make more sense to frame a single 2×6 wall with blown in dense pack cellulose insulation and 1″ of foam on the exterior sheeting. Any thoughts…. I will add that their concerns are value, energy efficiency, cost and carbon footprint. I have the perspective R- values at R-33 for the double stud wall and R-25 for the single 2×6 wall, guessing that the thermal bridging of the studs is not totally eliminated by the foam.
GBA Detail Library
A collection of one thousand construction details organized by climate and house part
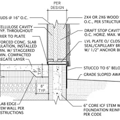
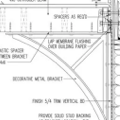
Replies
One question I would ask is, why 9" and not 12"? A lot of people seem to shoot for that and an R-40 value. Another is, if you go with 1" of foam on the outside, is it enough? I don't know what climate you're in.
My preference, rational or not, is to not use the foam, so I would be going with the double stud wall and cellulose. The thermal bridging becomes a non-factor, the assembly is permeable both ways, you can use organic materials and skip all the pesky foam chemistry questions, frame with 2x4 instead of 2x6 (lighter/faster although yes there are twice as many sticks), eliminate any issues of siding/trim fastening and window depth, and avoid showing your clients a dumpster full of foam cutouts headed to the landfill.
In remodel situations, with walls in place, foam outsulation makes sense. In new construction, you can get around it easily.
I think that question is best answered with a specific climate in mind. In addition, I suggest a review of the location of the air-tightness layer and the vapor retarder since they play as important a role as the insulation. So, in what climate zone is the project located?
Thanks David, the 12" was my plan but the clients wanted to lose less floor space. Another builder told them that the latter method would save a lot of time and money, but I don't necessarily agree. I would love to hear more thoughts........
Sorry guys, the project is in zone 7.
[Later edit: Sorry; the project is in Zone 4C.]
For someone unfamiliar with double wall framing, it would be a bit quicker to do single walls (of course) but I bet it isn't that much quicker, and "a lot of time and money" does not seem accurate to me. I wonder if Dan Kolbert or someone else who has done it will ring in. And obviously the up-front emphasis on saving a lot of time and money often leads to a lower quality product for the rest of their lives.
Are you going to be submitting a firm price for your proposal, vs. a firm price from the other guy? Or, is this a situation where it's T&M and the guy who says "save a lot of time and money" enough times gets the job... whether or not it's true?
Thanks David. The other builder was just hired as a consultant to ease the clients minds that I was in fact using the best methods to get them the best efficiency for the dollar. I don't have any competition on this one, but I do have to lock in the number as a bid. I have personally priced out the insulation cost, and counting the cost of foam, the 6" wall costs more by $400. Plus, there is a bit of labor to install the sheets, and the complications it can cause with vapor and siding application/ waterproofing. The FSC 2x4 is .33/LF instead of the 2x6, which is .52/LF. Taking the lumber into consideration, which is about $400 more for the 2x4, it seems to be a wash. Let's not forget about the labor and trouble of the foam installation.
Does anyone think I am missing something?
Matthew,
I'll echo David's suggestion to go with double frame and boost the thickness to ~12". The cost of framing is roughly the same, cellulose is cheap and the R value far exceeds the 1" foam scheme. You can sell the potential to get either better thermal comfort relative to energy cost, or lower energy cost, especially in a climate as cold as zone 7.
In fact your climate seems too cold to stop at 1" foam. See Calculating the Minimum Thickness of Rigid Foam Sheathing
I don't think you're missing anything, but I would revisit the foam thickness and revise the cost and R-value numbers, along with the possibly greater difficulty of installing thicker foam and dealing with window depth and siding/trim attachment through thicker foam (i.e. you might be able to use nails straight thru 1" foam, but with 2" or more you are using screws or even adding battens).
As David guessed, I vote for double wall. It's pretty quick and easy building the second wall, you can use 2x4's for the exterior wall, and you avoid the use of all that foam. We've found exterior foam to be tricky to detail, time consuming, and you still need to figure out how to attach your siding.
You do need to figure out how to deal with bridging at your rim, rafter overhangs, and your ridge, esp. if it's a structural ridge. But I really see less and less reason to use foam above grade in new construction.
I just had the same configurations among those I priced out with the builder I want to use, Matthew. An interesting difference: the double-stud/cellulose package comes out to about 10% additional by his figures. He also suggested I switch the exterior insulation for Dow's SIS.
Another difference: our climates are so radicall different, like the others I would wonder if there was enough thermal barrier there.
I hope you'll let us know what they/you finally decide.
Joe
I will let you know what they decide. Thank you all for chiming in and will continue to look for more comments here........
I know where I stand.
O.K. I screwed up the Zone calculation, the project is in Zone 4C/ on the edge of the Marine/ Dry line. With this info any other thoughts?
The owners need to factor in the loss square footage with the 9" and 12" options.
On a basic 1,000 sq ft book they will lose 6% of their area with the 12" wall.
Most buildings are measured for permit, tax value etc by the outside of frame method so they will be paying 6% more for the part of permit based on sq ft and the portion of property tax based on sq ft.
If you ask me Richard, we have to make choices: A little square footage, or a lot of Energy Savings?
Matt, not a choice between Size and energy savings. Where you put insulation can affect both permit costs and property taxes. Locally both permits and to a certain extent, property taxes are based on size. Both measure outside of framing dimensions. So exterior foam is not within the "taxable" square footage, but thick walls are.
Where I am they count porches and patios outside as well, I don't think it is a strong argument. Either you want to be cheap wherever you can, or you want to build with lots of insulation. When they come out with thin high R-value insulation, then we'll be talkin, until then more is better and thicker too.