Which foam boards for zone 5 over sheathing of 1974 house

Gentlemen;
I have read thru many of the articles on adding 2-3 inches of foam over wall sheathing. All very good articles by the way. But I see different types suggested and get confused.
Originally I was going to go with EPS, but nobody in my area handles it.
I can get the EPS with the poly coating,Insulfoam being one brand.
I am comfortable with how to do it thanks to you guys on this site.
So should i use poly coated EPS? XPS? or Polyiso ?
The house, Zone 5, 2×4 raised ranch, fiberglass insulation between studs with poly stapled and taped and sheetrock , latex primer and paint.
If I have to, i will take down the sheet rock and remove poly and reinsulate. But would prefer not to.
Thank you
GBA Detail Library
A collection of one thousand construction details organized by climate and house part
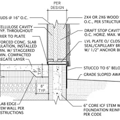
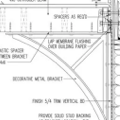
Replies
Opinions differ. POLY SHOULD GO in my book. UNLESS u can open it up a good bit in each and every stud bag by stud bay by ripping holes in it.
The only one to avoid is XPS. It has a much highter global WARMING potential. EPS OR POLYISO AKA ISO.
eps does better in colder climates but you can also use iso with eps over it in extreme cold. I'm in zone 4 and we use iso alone good bit
Interior poly is fine in colder climates. The assembly you are suggesting is very common around me (Ontario and Quebec) and there are no issues with it.
The one suggestion I would make is to go with permeable foam insulation, use either unfaced EPS or permeable poyiso (IKO enerair). This would allow for a bit of extra drying towards the exterior.
The amount of insulation you are installing is more than sufficient for condensation control in Zone5, the only moisture that will make it into your wall is from bulk water leaks, which would need attention anyways.
In zone 5 the IRC calls out a minimum of R5 on the exterior of the cavity insulation & structural sheathing in a 2x4 framed wall to provide adequate dew point control a the moisture susceptible sheathing. More is always better of course. At 2" any foam board will do.
But the environmental damage of XPS is about a full order of magnitude higher than EPS, due to the extremely high global warming potential of the HFC-soup blowing agents (main component of which is HFC134a, roughly 1400x CO2e @ 100 years.) EPS and polyiso are primarily blown with much lower impact hydrocarbons, predominantly variations of pentane (about 7x CO2e @ 100 years.) In the case of EPS most of that blowing agent leaves the foam while it's still at the factory where it is recaptured, not vented to the atmosphere. See:
https://materialspalette.org/wp-content/uploads/2018/08/CSMP-Insulation_090919-01.png
As the HFC leave the XPS via diffusion over decades the foam loses performance. The typical warranty is for 90% of the labeled-R @ 20 years, but it doesn't really stop. At full depletion the performance of XPS is identical to that of EPS of the same density, or about R4.2/inch for the typical 1.5lbs per cubic foot nominal density "Type-II" XPS sold as insulating sheathing.
Most of the plastic or foil faced foam are true vapor barriers, with a vapor permeance comparable to that of 6 mil polyethylene sheeting. Putting it on the exterior of a wall with interior-side polyethylene sheeting creates a moisture trap. With 2-3" of foam on the exterior that's not necessarily a disaster- the average temp at the sheathing will be high enough that any residual moisture can eventually (over years) stabilize, but it becomes a serious problem if there is any bulk water incursion from mis-lapped or leaking window flashing, etc. While re-mounting and re-flashing the windows with extreme attention to detail can get you there, stripping the interior side vapor barrier might be necessary for some people to sleep peacefully.
While using unfaced 1.25-1.5 lbs density EPS would have more than an order of magnitude more drying capacity than a foil or polyethylene facer, it's still going to be a Class-II vapor barrier @ 3" , which would meet the Canadian code definition for "vapour barrier". But it would still be some more resilient to bulk water incursions even if the interior side polyethylene sheeting was left in place. But standard interior latex on wallboard has 3-5x the drying capacity of 3" of unfaced EPS.
Reclaimed roofing EPS taken off commercial building re-roofing & demolition projects is usually unfaced 1.25 lbs density "Type VIII" goods that run about R4.15/inch, and will often be 1/4-1/3 the price of virgin stock foam. Most will have a large selection of 2lbs density fiber faced polyiso too, (which is fine if the interior side polyethylene has been removed.) Searching your local craigslist for [ rigid + insulation ]will often find local & regional foam reclaimers. eg:
https://hartford.craigslist.org/search/sss?query=rigid+insulation
https://cleveland.craigslist.org/search/sss?query=rigid+insulation
https://chicago.craigslist.org/search/sss?query=rigid+insulation
https://denver.craigslist.org/search/sss?query=rigid+insulation
https://saltlakecity.craigslist.org/search/sss?query=rigid+insulation
https://reno.craigslist.org/search/sss?query=rigid+insulation
https://bend.craigslist.org/search/sss?query=rigid+insulation
Gentlemen; Thank you for the knowledgeable answers!
The options I have for local distributorsl, which is 50 miles away. Is polyiso with a foil face and Insulfoam which also has a foil type face.
My thought at the moment is remove all siding and tar paper, prep the siding joints, poly caulk and tape. Move the the windows out to the required depth, build bucks and flash with a good type of tape. 2" of foil faced polyiso and 3/4 straping. Between each strapping add a sheet of 3/4 foam and then vinyl siding over that. I need a solid backing behind the vinyl. With the snow buildup on 2 sides of house for most of the winter it needs to be solid. Also a typar type of membrane over the sheathing prior to foam.
Then watch/check at later dates for any moisture in the fiberglass insulation. I have to replace sheetrock in one bedroom.
Hopefully that makes some sense. If not , I appreciate any responses.
General advice: when using anything other than unfaced EPS or mineral wool, I'd go one zone higher for the R value. Failure of IRC minimum exterior foam walls has been documented.
>"General advice: when using anything other than unfaced EPS or mineral wool, I'd go one zone higher for the R value."
That's good advice, but not needed in this instance, since even 2" of ANY foam board on a 2x4 wall would meet/beat the IRC's R7.5 minimum for 2x4 framed walls in Zone (5+1=) 6 (and 3" would deliver even more margin.)
Thank you gentlemen. I value your comments tremendously!