Where to spend time and money on cathedral ceiling?

I am putting an addition on my own home and feel like I have absorbed enough information from here to be dangerous! With so much information I feel like I have gone down a rabbit hole and cant see out.
Our house was built in the 1960’s and has 2×4 walls with paper faced batt insulation, 1×6 sheathing, stucco exterior and 2×8 rafters (2/12 pitch) with batt insulation, cathedral ceilings and 1×6 sheathing and strip venting along soffits only. The mechanicals and windows were replaced throughout about 8 years ago. We are in climate zone 7. We are on relatively tight budget, and will be self performing alot of the work.
The addition will be 6×18 and will enlarge the master bedroom and provide space for a master ensuite. The new construction will be 2×4 walls, tyvek drain wrap and 2″ of exterior XPS insulation with 3/4″ strapping and fiber cement siding. The ceiling assembly is 2×8 rafters to match existing and avoid increasing total height due to property bylaws which would require more engineering/permits to avoid. It is designed as a bulk fill 7″ closed cell spray foam unvented assembly (Cathedral ceilings need an effective R28.5 for code here so interior strapping would likely be required) . Plywood would be used for the sheathing and rockwool R14 cavity insulation. Foundation will be a frost wall with 2.5″ of exterior XPS. These assemblies seem to give us the most cost effective way to meet code.
I have received alot of push back on the ceiling assembly as lots of people want to avoid unvented ceilings and the risks involved. This assembly will also need to be engineered for the city to allow this to be done.
So my questions are:
-Is this the best option? Given that the remainder of the house is still only at a maybe R20-24 ceiling. Would this money being spent on spray foam be better off spent on bringing the remaining roof assembly to code by doing an overroof over the new and old together? The total roof area is 700 sq ft vs the 100 sq ft for the addition.
-Would something like standing seam metal on strapping be an effective way to minimize any issues with the unvented spray foam ceiling.
-If going the spray foam route should I convert the entire existing roof assembly in the master bedroom into the unvented portion as well? The interior ceiling will be removed anyways so in theory it makes sense however the amount of spray foam required is definitely cost prohibitive.
-Since we are replacing some portions of the exterior cladding, do we continue exterior insulation further and insulate the walls better because we are already doing portions of it? This would be alot less work, then completing an overroof.
-Finally do we just keep it simple and plan on doing the new portion as designed (Because it will be less time and money) and tackle the remainder of the house another time from above and outside when/if the funds and desire may be there to do it all.
Thanks in advance for your help!
GBA Detail Library
A collection of one thousand construction details organized by climate and house part
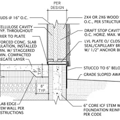
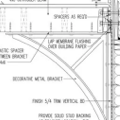
Replies
7" of spray foam between rafters is going to have it's performance significantly undercut by the thermal bridging. But 7" does fit into a 2x8 rafter bay without adding strapping. In zone 7 at least 60% of the total R of a roof has to be outside the first condensing surface. With 4.5" of HFO blown closed foam you'd be at R31-R32, which is sufficient to accommodate up to R20 of high density rock wool or high density fiberglass, which would add another 4.5-5" . That fits in a 2x10 rafter bay.
But rather than 2x10s, let's see what we can do with the 7.25" depth of a 2x8:
Since it's only a 6' span, will it make it structurally with 2x4 rafters? If yes, adding 3" deep foam edge strips on the underside of the rafters screwed & glued into place with 1x strapping brings it to the same depth of a 2x8, and the gyprock can hang on the strapping. If that's too awkward, 2x6 rafters with 1.5" foam edge strips & strapping gets you there, still more than doubling the R-value of the framing fraction. This approach has been dubbed "Bonfiglioli strips", detailed here:
https://www.finehomebuilding.com/membership/pdf/9750/021250059.pdf
With a 7.25" deep cavity 4" of closed cell foam (R24 for brand-X HFC blown goods, R28 for HFO blown foam) and 3.25" of compressed batt (R13-ish, if compressing an R14) gives you at least R37 at center-cavity, with at least 63% of the R-value exterior to the foam/fiber boundary for dew point control.
With 1.5" polyiso (R9) Bonfiglioli strips on 2x6 rafters the framing fraction is about R16-R17, which should meet the R28.5 "whole assembly" performance numbers. If they will allow 3/4" asphalted fiberboard for the roof decking it'll add at least another R1 to the whole-assembly numbers if it turns out to be marginal with plywood. (Asphalted fiberboard is extremely moisture tolerant compared to plywood too.) With 3" polyiso Bonfiglioli strips on 2x4 framing the framing fraction would be R22-R23, and it would exceed R28.5 whole-assembly performance.
XPS is the least environmentally friendly commonly used foam insulation. It's blown with high-impact HFCs, and loses performance over time, eventually dropping to the same performance as EPS of equal density & thickness. If you can spare the extra half-inch, use 2.5" of Type-II EPS on the wall sheathing, which is normally cheaper per labeled R than XPS, and doesn't lose performance over time.
To do it with a foam-over of the whole roof could be expensive. The 2x8 rafters probably half R19s in them. Filling them with 1lb density blown fiberglass drilling from the exterior would deliver about R27-R28, and it would take at least R45 of exterior foam to achieve dew point control at the roof deck. If you can yard out the batts and seal the rafter bays at both ends you could get an R28.5 whole-assembly compliance can be met with just 6" of Type VIII (1.25 lbs nominal density) roofing EPS and a nailer deck through-screwed to the structural roof deck with 8" pancake head timber screws. (Using EPS nailbase panel vendor specs for the fasteners & spacing usually works.) Using reclaimed roofing EPS can make that reasonably cheap- less than 1/3 the cost of virgin stock foam for the material itself. But that does raise the overall height of the roof, adding 7" of facia board, etc. which could run into pushback from other quarters.
Thanks for the advice Dana. The span of the rafters is over the 18' section rather then the 6 foot direction with a ridge beam in the middle. I feel this is why the engineer spec'd the 2x8's. I'm not sure if smaller could be used however with around a 9 foot span I think the 2x8 is probably minimum. I like the idea of using the flash and batt technique with the ceiling. This seems to be a great way to perhaps increase the total area being spray foamed and keep the same budget.
In regards to the over roof, I am torn between doing the over roof, which as you mentioned could be expensive or doing almost the same square footage of wall insulation which would be simpler and tie into the work being done a little better given that the work will be done over the winter. Then circle back to doing a over roof when the remainder of the house's shingles needs to be replaced in the foreseeable future.
Doing the spray foam route now on only the new addition part would be the most cost effective way to go to meet code I feel. Followed by the over roof at a future date to further insulate the entire home.
Would using the spray foam in portions directly under the roof deck interfere with doing an over roof in the future?
Would it be worth using the Bonfiglioli style furring strips on the underside of the rafters?
Thanks!
Bonfiglioli strips add depth, and reduces the heat loss through the framing, and will improve the overall performance. Whether it needs that upgrade to hit your minimum performance target depends on the target, the actual framing fraction, and the total stackup of the assembly.
Increasing the fiber-R depth also means increasing the spray foam-R to maintain the minimum 60% foam-R.
User 7191102,
First of all, can you tell us your name? (I'm Martin.)
Q. "Would something like standing seam metal on strapping be an effective way to minimize any issues with the unvented spray foam ceiling?"
A. What "issues" are you talking about? If your unvented cathedral ceiling is properly detailed, it won't have any "issues."
If you decide to use spray polyurethane foam, remember that you can still choose to vent your rafters. Just install site-built ventilation baffles (made of sturdy material) in your rafter bays before inviting the spray foam contractor to begin working. If you do this, you'll need soffit vents and ridge vents, of course.
For more information, see "Site-Built Ventilation Baffles for Roofs."
Hi Martin, my name is Chris. Thank you for your response!
When the plans were being drawn up the Architectural Tech determined that there would not be enough room for the ventilation channels and insulation. This is the reason why I believe he spec'd the bulk foam. I'm going to reach out to the inspector and get clarification if this will pass as you are now the second person that has mentioned this possible option.
Makes sense about the metal roofing, build it right to begin with and there should be no issues with roof rot. I just thought the gap would allow some possible ventilation as we do have issues with Ice damming in the existing house.
Chris -
Glad you are working through this and asking questions at the design stage.
I completely understand about rabbit holes, and especially on this topic. The building science of cathedral ceilings is apparently poorly understood, because even the experts are debating. It appears that there are many ways to create problems, and we only understand some of them. While there are a lot of cathedral ceilings out there that don't have obvious/discovered problems, it seems to be such a problematic design element that I think my half-serious suggestion to people pondering something other than a flat (and level) ceiling is to consider trompe-l’oeil and a good painter.
P.S. This is not really directed at Chris, it just seems that cathedral ceilings come up over and over and over at GBA, and I don't see that there's a consensus solution that works with high confidence.
Thanks for all the information. Our building code (Alberta) requires a 2 1/2" vented airspace above the insulation. As we need to have this work inspected the city will not allow us to raise the peak height without going through further applications, reviews etc.
This would allow two possible solutions:
-Build vent channels and furr out the interior of the space. Reducing interior height by approx 1.5" (Currently the eaves have around 7' 6" clearance at exterior walls). Either by Bonfiglioli strips or 2x4 on side ran perpendicular to existing rafters 24" oc. Spray foam approx 5.5".
-Keep the un-vented assembly as is with approx minimum R33 ccsf
I am leaning toward just doing the un-vented assembly as doing the first option would effectively only do 1/4 of the house, max out at a less then ideal R value and reduce ceiling height. In the future when the shingles are due to be replaced (5-10 years) I will likely do an entire over roof at that point to bring the entire house roof assembly to current code and reduce thermal bridging.
I do have a couple follow up questions though:
-Are there any advantages I am missing to doing the vented approach other then saving a few bucks in the engineering plans/site visits for the un-vented portion? The reduced ceiling height/extra work/costs associated with the furring seem to bridge the gap, as well as potentially doing an over roof in the future seem to further make this option less desirable.
-With doing the un-vented approach in the addition portion. Is there any advantage to removing the existing batt insulation in the remainder of the space. And creating the un-vented assembly there now?
-At the time to do the over roof would I need to remove the batts in the existing ceiling? Could I not just seal the ends and leave the insulation in place?
-Is there anything else I can do now on this half of the house, to simplify the process or reduce replication at a later date for the over roof?
-Would using compressed mineral wool batts or semi rigid boards help with the thermal bridging of the rafters more then filling the available space with spray foam? Or is this a mute point with the end goal of doing an over roof?
-Are there any concerns with ice damming on a unvented roof? Or is the risk reduced by the closed cell spray foam
Chris,
Q. "Are there any advantages I am missing to doing the vented approach other then saving a few bucks in the engineering plans/site visits for the un-vented portion?"
A. If you have a vent channel, it's easier for roofers in 30 years to replace any rotten roof sheathing. That's the main advantage.
Q. "With doing the unvented approach in the addition portion. Is there any advantage to removing the existing batt insulation in the remainder of the space, and creating the un-vented assembly there now?"
A. Your question is unclear. Where, exactly, is "the remainder of the space"? Is this a wall or a roof?
Q. "At the time to do the over roof would I need to remove the batts in the existing ceiling? Could I not just seal the ends and leave the insulation in place?"
A. If you insulate your roof now using the flash-and-batt approach, you can later safely install rigid foam above the roof sheathing if you want, without changing the flash-and-batt job. I'm not sure what you mean by "seal the ends" -- if you are doing flash-and-batt, there usually aren't any vent openings at the soffits or ridge. If, however, you decide to do "flash-and-batt with a vent channel between the spray foam and the sheathing," then yes -- the ventilation openings ad the soffit and ridge would need to be carefully sealed when you install rigid foam on the exterior side of the roof sheathing.
Q. "Is there anything else I can do now on this half of the house, to simplify the process or reduce replication at a later date for the over roof?"
A. That's a broad question, and therefore hard to answer.
Q. "Would using compressed mineral wool batts or semi rigid boards help with the thermal bridging of the rafters more then filling the available space with spray foam? Or is this a moot point with the end goal of doing an over roof?"
A. If you are worried about thermal bridging through the rafters, there are only two ways to address it: Either install a continuous layer of insulation on the interior side of the rafters, or install a continuous layer of insulation on the exterior side of the rafters. If you are planning eventually to install a layer of exterior rigid foam, that will reduce thermal bridging nicely.
Q. "Are there any concerns with ice damming on a unvented roof? Or is the risk reduced by the closed cell spray foam?"
A. Of course an unvented roof can have an ice dam -- especially if (a) there are air leaks through the thermal envelope, or (b) the R-value of the insulation is less than minimum code requirements. For more information on ice dams, see "Prevent Ice Dams With Air Sealing and Insulation."
Thanks for your time answering these questions Martin!
We are adding onto the back of a 4 level split. Currently on the top level there are 3 bedrooms and 1.5 bath. We are going to be enlarging the master bedroom and adding a full ensuite bath.
So effectively we will have the entire master bedroom ceiling down (basically half the top floor). This is where my not so clear questions about anything else, future stuff etc. come in.
We want to make this 1960's house as efficient and comfortable as possible, but we are on a tight budget so we can't do everything at once.
I think I'm sold on the unvented approach for the new addition. Ideally then when the roof shingles go, we could do an insulated roof deck at that point.
However there still is the possibility that we dont go that route. So my gut tells me to balance the two. Remove all the insulation from the areas we open up and spray it to a code minimum. This is better then what was there and air seals the roof deck in case we never get around to doing part 2.
The remainder of the house would then still have fiberglass batt, so if we loose filled as Dana mentioned we would need around R45 exterior insulation. Or if we removed the batts and did code minimum R30.
-Would these amounts of insulation work over the spray foam portion as well?
-All the articles I have read say the rafter bays need to be completely filled and insulation indirect contact with the sheathing, if using exterior insulation. What happens in this air gap if it is left unfilled?
Chris,
Your questions are still vague, making them hard to answer.
Q. "Would these amounts of insulation work over the spray foam portion as well?"
A. What is "these amounts of insulation"? Do you mean "spray it to code minimum" or "around R-45 exterior insulation" or "code minimum R-30"?
Q. "All the articles I have read say the rafter bays need to be completely filled and insulation in direct contact with the sheathing, if using exterior insulation. What happens in this air gap if it is left unfilled?"
A. If you are combining exterior rigid foam and interior fluffy insulation, then the fluffy insulation needs to be in direct contact with the underside of the roof sheathing. If the fluffy insulation isn't as thick as the depth of the rafter bays, it can be tricky to figure out how to maintain the insulation in contact with the roof sheathing. But if you can jury-rig a method of keeping the insulation tight to the sheathing, go ahead and do it that way.
The air gap doesn't really cause any problems, but it can be a channel for air movement. So it's important to pay strict attention to air sealing at any penetrations or intersections of you want to avoid problems with hidden air channels.
Sorry for the vagueness, I swear these questions make sense in my head! Hopefully these are a little clearer.
-Can I remove the old batts and use R30 on the entire roof deck? Keeping in mind that a portion of the roof would have the R33+ closed cell spray foam under the roof deck.
-If I spray deeper then R33 under the roof deck with close cell foam, would I need to increase the rigid thickness accordingly on top or does this rule only apply for fluffy insulation under.
-Since you have said it is best to try and avoid the foam sandwich with rigid foam ontop and closed cell under. Am I better off then leaving the existing batt insulation untouched in the existing portion of the room for now as this technically doesn't need to be changed as it doesn't need to meet current codes. Then if we do the next step, either remove the batts or add on to them before doing the rigid foam above.
-Is it worth going through the effort in building site built channels and spraying to them? Is a 1.5" vent space and 5" of spray foam going to perform better in my climate then one with 5" of spray foam alone?
At the end of the day I want to build to meet or where it makes sense exceed code requirements for the addition now. Then try and improve the remainder of the house in the future. So anything I do now, I would like to either help future efficiency work or at least not make it more time/money consuming. For example if I spray the 2x8's full with spray foam now then find out I need to use R60 exterior on the roof to make it work I think that's backwards.
Chris,
In your original question, you described this as a roof with 2x8 rafters with a 2-in-10 pitch. That's a low-slope roof. You can't create a vented roof assembly with a low-slope roof, unless (a) the attic is deep enough to permit room for at least 6 inches of air space between the top of the insulation layer and the underside of the roof sheathing, and (b) you install one or more ventilated cupolas in the middle of the roof.
For more information on these details, see "Insulating Low-Slope Residential Roofs."
In your case, your only choice is an unvented assembly.
A sheathing sandwich (with rigid foam on the exterior and closed-cell spray foam on the interior) will work, as long as the roof sheathing is dry when it is encapsulated.
Thanks for your help Martin, yes it is definitely a low slope roof.
One final question. Does the thickness of rigid foam above the roof deck matter then if we use closed cell spray foam under the roofdeck?
Thanks!
Chris,
If you are planning to encapsulate your sheathing with rigid foam above and closed-cell spray foam below, then the thickness of the rigid foam above the roof sheathing is irrelevant.
The total rigid foam + closed cell spray foam is what's relevant for keeping any fiber insulation dry. The low vapor permeance of the spray foam protects the roof deck, the total R value exterior to the fiber is what keeps the fiber from collecting moisture over the winter.