Where does the humidity go in a super-sealed building?

I am wondering deeply, and this question makes me doubt all wall designs.
Where does all the humidity go in a super sealed structure ?
Let’s assume that a residential house has an almost perfect water vapor barrier setup
and or is very tight ( my personal example is an ICF house ), what happens to all the daily generated humidity by the occupants ??
I understand that nothing is completely vapor diffusion proofed, but if slow enough,
would the humidity level rise without stopping ?
I am asking this because of the following situation …
I have a large ICF ( quadlock) house, on which there is a flat roof terrace,
and i have to re-build the small exit house on top of it because my carpenter helper didn’t
do it properly ( all sheating got damp, some rotten wood supports etc… many many air leaks )
And i need to commit to a certain design, so i am afraid that i would actually need some excess humidity to get out, and if i go with a reflective inside insulation and or another design that would “seal” even more the vapor, there would be no way for it to get out by diffusion fast enough.
Is that worry founded ?
Do we need some walls to be somewhat permeable so we can exchange humidity levels with the outside ??
i hope i am making sense somewhat !
thanks for your time all! superb website!! 🙂
GBA Detail Library
A collection of one thousand construction details organized by climate and house part
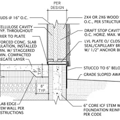
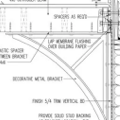
Replies
Does your house have mechanical ventilation? That's what you need.
Hi David, thanks for the quick reply!
my house has bathroom and kitchen fans that output directly outside
and i have a Venmar 3100 that is yet to be installed
http://www.venmar.ca/45-air-exchangers-hepa-3100.html
how does it remove the humidity ?
What climate zone are you in? How big is the house? What rooms is the Venmar serving, and which are exhaust and which are supply?
In most heating climates, the outdoor air is fairly dry during heating season, so ventilating (removing) indoor air and replacing it with outdoor air removes humidity. Out with the old, in with the new. You don't need to worry about diffusion through walls. Just make sure you have adequate ventilation.
..."I understand that nothing is completely vapor diffusion proofed, but if slow enough,
would the humidity level rise without stopping ?" •• That is why you want walls that are fairly vapor open, on both sides if possible. A little in, a little out.
thanks all for taking time to reply
i am personally in 6-7 ( east on Montreal )
my ventilation setup will be on the recirculating system for the Venmar.
I heat with electrical infloor and i've installed a recirculation system that mixes up most of the air the house .. my house is fairly on the large side
roughly 1.6ksq ft per story times 3 .
but please let's take it back to general situation
houses get rid of excess humidity mainly by exchanging air with outside in cold climate ???
( be it from leaks and or ventilation )
i thought that we would want diffusion to make the "passive" part of it nah ??
Here in Quebec province, people have been installing poly sheets behing sheetrocks for quite some time ...
alot of houses do have mold/rot problems ...
now since approx 10 years, the "higher quality" houses are build with a reflective vapor barrier
behind the sheetrock... which also seems to serve as thermal break from the studs
but personally, i do not like the idea of "sealing" humidity from neither sides ...
Let's assume please for an instant, a theoritical setup .
Small house, that was 100% sealed ( no leaks ) with a correct vapor barrier ( <0.1 perm ) from the inside. Would ventilation to outside suffice to get rid of the daily inserted humidity ??
Would it then require "more" ventilation to be able to keep the same level as a non perfectly sealed similar house ??
What about using dehumidifiers even during cold season ?
They generate heat as byproduct, which is not really any loss of energy during winter time nah?
Jin,
First of all, I disagree with John Klingel. There is no necessity for walls to be vapor-open.
Your question illuminates a common misconception: the idea that somehow we should design walls and ceilings to remove humidity from the house. People have the false impression that it is desirable to encourage leaks through walls and ceilings, as if the walls and ceilings were supposed to operate as some sort of magic, automatic dehumidifier. This is nonsense.
In winter, the outdoors is cold and dry. The indoors is warm and relatively humid. This is normal and desirable. Indoor conditions are different from outdoor conditions. We need a thermal barrier to separate the two conditions.
If you encourage the flow of vapor from the interior through your wall and ceiling assemblies, you are courting disaster. The idea is to keep the warm, humid air inside, and to leave the cold, dry air outside -- without encouraging the flow of heat, air, or vapor through your wall or ceiling.
What happens to the indoor humidity? It just is. It isn't supposed to go anywhere. The higher humidity is a function of the fact that the indoor air is warmer (and therefore able to hold more moisture) and that human activity generates moisture. The moisture is supposed to stay put.
Of course, it's possible that the indoor humidity is TOO high. This isn't because it builds up every day in an additive fashion; it's just because the residents have too many houseplants, take too many showers, cook too much pasta, and store too much firewood in their basement. The normal way to regulate high indoor humidity in the winter is to operate the ventilation system. That brings dry outdoor air inside, while exhausting some of the humid indoor air.
Of course, if you are operating a humidifier, or you store a whole winter's worth of firewood in your basement -- don't do that.
It depends on what "... fairly vapor open..." means, doesn't it?
A wood-sheathed wall in a Montreal climate is susceptible to wintertime moisture accumulation in the sheathing if there isn't sufficient vapor retardency on the interior, or sufficient insulation on the exterior side of the sheathing to keep it's average winter temp above the dew point of the conditioned space air. The higher you allow the indoor humidity to rise, the bigger the problem.
IIRC, Canadian building codes for wood sheathed timber framed wall assemblies require either:
a: A Class-I vapor retarder (usually polyethyene sheeting) on the interior side of the cavity insulation
or
b: sufficient insulation exterior to the wood sheathing that the sheathing does not drop below 5C at the 99% outside design temperature with a 20C interior temp.
Both will work, but both are more severe than need be, and a good wall design can be more protective of the sheathing without a severe vapor barrier OR that much exterior R, a case where codes interfere with good design.
With interior poly you can end up with condensation on the poly in an air conditioned building in summer, leading to puddling and floor rot at the bottom of the studwall, even in a Montreal climate. (This is more likely in stucco or brick clad buildings than with wood or vinyl siding.) The amount of exterior insulation necessary to meet the 5C sheathing @ the outside design temp is insanely high, and if the spec were relaxed to 5C sheathing at the January binned hour AVERAGE temperature, the sheathing would load up slightly during the coldest nights, but release that moisture during the warmer days without damage or mold risk, using only latex paint on wallboard as the interior vapor retarder.
The 99% design temp for Montreal is -24C, so about 65% of the total R value at center-cavity would have to be on the exterior to meet code without interior poly (!). But the January mean temperature is about -16C, which would relax the exterior R to about 40% of the total R.
A a concrete example of what that means, to meet the letter of the code with a design temp of -22C without the interior poly a 2x4 wall with R15 rock wool between the studs would need R28 of insulation on the interior (~12-13cm of rigid XPS or iso!), but the sheathing would in fact be fine with just ~R10 on the exterior (5cm of foam).
If one were required to put up interior poly with only R10 foam on the exterior it would be in danger of trapping moisture in the studwall, since the drying capacity in either direction is too restrictive.
My take on the OP is that this is an ICF house, not stick-framed...
David: you are correct, but i like to keep my questions general so others can benefit from the info :)
And yes my house is all IFC except that small room for the roof exit ( ~15X~18' ) that is stick framed
( currently already rotten :p )
A few questions arise in my head from reading your replies.
- What about when DEW point is INSIDE a FOAM sheathing ?? what happens then ?
does the vapor condense within the foam and then seep out ??
would it behave differentely in EPS than is XPS then ??
Martin: thanks for your time
- i thought that exchanging humidity to help dry walls etc through diffusion was a + and not a con ??
- what about open walls design such as what mr Thorsten Chlupp demonstrates on this tube :
https://www.youtube.com/watch?v=HrtUtNb3jmI
My fear is that nothing being perfect, what happens when a sealed wall
( lets assume poly or reflect insu on the interior ) leaks and get humid ? will it drie up ?
What about using no sheathing behind the framing wood and jumping right to EPS foam ??
Dana : i understand the dew point principle to push it outside of the wood sheathing
and i have no problem with thick exterior insulation
in fact, before i started reading about walls and insulation a few months ago,
i did not understand why we are still insulating within wall cavities and not all exterior
What do you guys think about the "PERSIST" type of setup in regard to humidity management ?
Dana do you really think it is possible to get condensation within walls from exterior during summer because of ac ?? please explain how that can be ...i thought condensation required much cooler than 20c to happen within reasonnable humidity levels ??
Jin,
Q. "What about when the dew point is inside foam sheathing?"
A. Most foam sheathings are vapor-impermeable -- so vapor doesn't get "inside" of them.
Q. "Does the vapor condense within the foam and then seep out?"
A. No.
Q. "Would it behave differentely in EPS than XPS?"
A. EPS is somewhat more vapor-permeable than XPS. But if you are installing enough EPS to insulate your wall -- as you would with an ICF wall or a SIP wall -- you really won't get much vapor traveling through EPS.
Q. "I thought that exchanging humidity to help dry walls etc through diffusion was a plus, not a minus?"
A. Well, if your wall is wet, you want it to be able to dry in at least one direction. That's very different, however, from deliberately encouraging water vapor to enter your wall during the winter! Certainly no builder wants his walls to get wet on purpose.
Q. "What about open walls design such as what mr Thorsten Chlupp demonstrates?"
A. Vapor-open walls like those built by Thorsten can work very well. But even Thorsten doesn't design walls to be deliberately leaky. The idea is for any wall to stay dry -- but if it ever gets wet, you want it to be able to dry out in at least one direction.
Q. "What happens when a sealed wall (let's assume poly or reflect insu on the interior) leaks and gets humid? Will it dry up?"
A. Maybe, maybe not. Polyethylene is risky in most climates. I don't recommend that you build your wall with polyethylene.
Q. "What about using no sheathing behind the framing wood and jumping right to EPS foam?"
A. As long as you brace your walls, that can work. Here's more information: Four Options for Shear Bracing Foam Sheathed Walls.
Q. "What do you guys think about the PERSIST type of setup?"
A. It's a good system. More information: Getting Insulation Out of Your Walls and Ceilings.
Q. "Do you really think it is possible to get condensation within walls from exterior during summer because of AC?"
A. Yes. More information: When Sunshine Drives Moisture Into Walls.
In a masonry clad house a considerable amount of dew & rain moisture can be stored in the masonry, and gets released at VERY high rates when heated in the sunlight, which can raise the dew point of the air in the cavity well above 20C even with a 2-5 perm vapor retarder (such as roofing felt) between the masonry & sheathing to slow the rate of humidity transfer. But without poly to block drying toward the interior the stud cavities will run much drier, and as long as the daily average humidity transfer into the stud bay isn't faster than it can be released through the gypsum & paint, it stays dry (and it does, even in hot damp swampy places like Louisiana or Florida.) This is much less likely to happen with wood clad structures, but not impossible.
When the temperature of some point within the foam drops below the dew point of the interior air NOTHING happens, because the foam isn't air-permeable at a rate that matter- even over the course of a year or two of sustained cool temps it won't accumulate sufficient moisture to make a difference in it's performance.
It's possible to build without structural sheathing if you cut in cross bracing to handle the racking loads, and there are several advocates of that approach from a cost-savings point of view.
It's good to have at least some drying capacity in at least one direction, and when there is a code-required vapor barrier in the stackup that direction is defined for you, for better or for worse. The problem with placing the vapor barrier on either the interior or the exterior is that in most areas the drying direction that is most optimal changes with the season and with the stackup of the structural & insulating materials within the assembly. As long as it has at least 1perm of drying capacity it can dry reasonable quickly, but if it's too vapor-open to the point where susceptible materials take on too much moisture over the course of a season you can end up with mold issues.
Wow ok thanks all for info ... brings up much more questioning .. but i'll take some time later to have my brain process all the info and come up with new questions !!!
My interior finish was supposed to be aluminum sheets clipped in some special aluminum extrusions i designed ... this material ( acp ) is probably very close to 0% perm and will be pretty much sealed with the clipping system
and i am supposed to use it on 12mm plywood .. so bracing can be done with the plywood
any problem with using the plywood inside of the framing ?
Dana : here it is pretty easy ( country side ) to do as one wish, as no inspector ever came to visit my house and i doubt it will ever happen ...
so no vapo barrier and only retarders, with large insulation to move the dew point out on the exterior would be a better solution than using vapor barriers ??
Yes- moving the dew point out beyond the wooden sheathing with exterior insulation and using only standard latex paints gives the wood a reliable 2+ perm drying path, and presents no winter moisture buildup issues- it's a reliable way to build. Interior poly works, but has summertime issues, and works best when there is a rainscreen gap between the siding and the sheathing to guarantee good drying capacity to the exterior. But when you start putting foam on the outside of an assembly with interior poly the overall drying capacity gets compromised, and if you don't have at least 0.5 perm in at least ONE direction the assembly isn't very resiliant.
No walls are perfect, and most houses will experience a significant wetting event behind the siding (or several) in it's first 50-100 years (or even chronic minor wetting from mis-lapped or gaps in the flashing, etc.). If the wall is built such that it can dry it tolerates those events. If it can't dry quickly enough, it becomes a problem. At 0.5 perms it's not drying very fast under any circumstances- I like 2+ perms better, but the stack up has to be such that it won't load up too much seasonal moisture through that 2+ perms.
Putting the plywood on the interior would provide about the same structural rigidity as putting it on the exterior. The aluminum panels are about as close to 0.000 perms as you can get, and would be a code-compliant vapor barrier.
But air-sealing will still be important, and if you have exterior foam that is too vapor-tight you'd still have a moisture trap. You could use very-permeable high-density rock wool on the exterior, but it's more expensive than EPS/XPS/iso and dramatically heavier, presenting it's own challenges if you go high-R on it. At ~100mm EPS is still between 0.5-1 perm and would be OK, or you could use fiberglass-faced roofing polyiso which runs between 0.5-1 perm at any thickness, so long as it's only one layer. With XPS you'd have to stop at ~50mm, or R10.
Martin: I don't generally disagree w/ you, as I think you generally know much more than I. However, I will continue to favor walls that are "fairly vapor open" as I have never heard, read, nor reasoned that it can be harmful to be so. It's just less risky that way, imo, in case stink happens that we don't plan on. If anyone can provide info as to why to avoid being "fairly vapor open", please advise. Cheers.
John,
Jin Kazama began this thread with a series of questions about an ICF house. The walls of an ICF house are not very vapor-open. Nor, for that matter, are the walls of a SIP house.
In general, as long as these walls don't have significant air leaks, they perform very well. This type of wall proves that there is no fundamental need for a wall to be vapor-open. With an ICF wall or a SIP wall, the dry air outdoors stays outdoors, and the humid air indoors stays indoors. That's as it should be.
Jin's question -- "I am afraid that I would actually need some excess humidity to get out, and if I go with a reflective inside insulation and or another design that would 'seal' even more the vapor, there would be no way for it to get out by diffusion fast enough" -- implied that Jin thought that walls should act like dehumidifiers, to help lower the indoor humidity of the home. My answer addressed that misconception.
Walls can be vapor-impermeable and perform very well indeed. The way to lower the indoor humidity in winter is with ventilation, not by designing a wall to be so vapor-open that the indoor humidity is invited into the wall assembly. The latter method is a path to disaster.
Martin: you understood my questionning well.
I knew that ICF ( from reading around ) walls are pretty imperm, so i seriously wondered as to where the excess or additional ( from ideal % ) humidity had to do.
But now i understand that the mech ventilation is there for that,
so i will try and design my roof room walls without thinking about it "breathing" through diffusion.
That said and cleared, what do YOU think about PERSIST walls then ??
What about using 2X6 ( i need it for strength because roof is flat and snow loads ..i take no chance for a few bucks ) with a plywood exterior + all around peel and stick + exterior EPS
should i look for using 3.5" of ROXUL in the divisions, that would probably leave the sheathing/membrane hot enough to move out the dew point ??
( R14 it is i believe )
If water would ever to get inside a persist wall, by leak or accident,
and i'd install a plywood on the interior side + my aluminum finish, would it dry ???
since it should be near room temp
I am pretty sure i can safely design the walls and this small flat roof section
to make sure water never enters and stays out of the membrane
else i could use only the EPS on the studs and get something like 0.5 perm total to the outside
so it could eventually dry during summer days if required ?
This room sites at ~40' high on my flat roof, so it is very well exposed to direct sun all day long
except for the north-east facing side.
Martin: Agreed. I think we are on the same page, just different paragraphs. RE: "...Walls can be vapor-impermeable and perform very well indeed. ...not by designing a wall to be so vapor-open that the indoor humidity is invited into the wall assembly. The latter method is a path to disaster." But vapor impermeable on both sides, I don't think, is advisable. Hence, my reference to "fairly vapor open", implying that drying should be allowed to happen in one direction, if not both (ex: Thorsten's). As for being so vapor open that you invite vapor in, agreed, though I don't see how a person could do that with a "normal" (whatever that means??) house with sheet rock and paint. Maybe w/ wood inside and no kind of moisture retarder? Dunno, but that concept sure needs to be kept in mind, and thanks for pointing it out. That is why you get the big money.
Hey guys, i would be tempted to try out something.
Please let me know if this is ok.
Would try to do it with 2X6 + plywood for bracing and attachment
all around peel stick "a la " PERSIST
then 2 layers of my 5" EPS foam ( i've got enough i'm pretty sure )
and lastly 1" ISOCLAD product just to have something to tape correctly and would double
as water layer.
I was just looking at some euro passivehaus and some have used up to 14" of EPS with succes .
I wonder though about the walls details.
I would but this foam directly into the flat roof foam layers
and i'd do the same for the small roof on top.
Would need to figure out how to properly set windows,
but i wanted to give them a 45degree sunshade treatement so i might be able to get pretty close to that if i set the windows 6-7 inches inside and i do a small detailed overhang in the finish !
Jin,
Q. "What do YOU think about PERSIST walls then?"
A. My answer is the same as the first time you asked me that question. You may recall that I answered, "It's a good system." I also provided a link to an article I wrote on the topic. If you read the article, you should be able to tell that I am a PERSIST fan. Here is the link again: Getting Insulation Out of Your Walls and Ceilings.
Jin,
I wouldn't attempt to try to attach 10 inches of EPS to the exterior of a wall with long screws. I think that 8 inches of foam is a reasonable limit.
Anyone following GBA for the last several years knows that there has been a lot of debate on whether or not building assemblies should be vapor permeable.
I think Martin's message has been consistent throughout these debates: either option can work. It depends the climate, the design, the build quality, and the details. (Correct me if I am wrong Martin!)
As more evidence that vapor impermeable assemblies (and exterior foam sheathing) work, Building Science recently released an update on their Vancouver Test Hut. If you haven't seen it yet, you can find the update here:
http://www.buildingscience.com/documents/reports/rr-1207-vancouver-field-exposure-facility/view
Jin, if you want 10" of foam, get 10" SIPS panels and build the roof exit structure out of them... walls and roof.
Hi Jin,
Interesting post.
It sounds/looks like your house is still under construction....
and Perhaps you are still working on the interior finish.
Are you saying that your flat roof-deck is 40 feet high and the rotten/leaky "exit-penthouse" is even higher than 40 feet above the ground?
How about posting a photo of the outside of your house that shows the entire height.
and another interior photo of one of your "extra-cold" windows that shows more context (from floor to ceiling)....
Further to the Building Science report mentioned in post #22, I note that in multiple places toward the end, in the discussion of performance of the various wall assemblies, there is the comment regarding the sheathing temperature going below the dew point of the interior air: "This is not a durability problem unless interior air reaches the surface of the sheathing." Wouldn't this be an argument for providing a well-detailed inside air barrier in a cold climate, even if there is an outside air barrier?
Definitely.
Ah yeah so any idea on how one can attach 5" of EPS to another 5" of EPS ?
the one i have doesn't have any embedded clips so i need a layer of something in between ?
i guess that wood is out of the question :p
WOW again , will try and answer each as briefly as possible.
Martin: I had seen your article on PERSIST before getting on the forum here,
it is how i found out this site :) ( was searching google for exterior insulation wall designs )
But, i didn't notice both first time that YOU did this article on the PERSIST! :)
Would there be anything that i could use in between the 2 5" EPS ?
I really want to use the foam i already have ( and already paid for ) and if i can't use 10" of it,
i'll have to settle for using a single 5" layer + something else
I do have access to fairly cheap screws and hardware, and i can easily get screws up to 15" ..
but they won't hold the weight, only tension holding ..would need to have the foam "sit" on something else ..and this could be possible since it needs to be connected onto the roof insulation boards ( fireston HD recoverys ... iso laminated on 2 sides with FG )
Anyhow if you approve of the PERSIST method or any derivative, this is what i am going after then,
as i've always thought insulation should be outside and not wtihin walls ...
Also will make it much easier and faster to do the air sealing for me :)
Daniel: i've only been browsing here for a few weeks, but thanks for the link ... i believe that any research results are worth reading as there is always much to gain from using other's experiences.
exemple, i've only recently learned that there isn't much energy efficiency to gain by going from a well built R20-R30 walled house VS an regular ICF cosntruction if air leakage is similar
( i really thought that the mass of the concrete would've have a much larger impact .. )
if i had none all i know earlier, would've probably installed another 2-4" of EPS on the outside of the house before the cladding
David : i do not have access to SIP, and as much as i wanted to get equipped to built SIP walls for my next projects, i am slowly moving away from the idea as i do not believe that having a structural OSB at the exterior of the house is a very good idea at all anymore ... looses way too much strength once even only humid for a small period of time.
If it was up to me, we'd only use concrete and metals for building structures :p
John Brooks: yes the floor of the roog terrace is at ~40ft high and the roof exit room sits on top of this ( approx 50ft at highest point )
The house have been in the work for 4 years now ...it took me approx 2 years to plan and purchase everything , we have been living in it since july of 2011 ( almost a year and a half now )
But i do not wish to turn this thread into a personal one,
as i believe it could be informative to everybody ( that is why i asked for a general quetsionning at first ) i'll join a few quick pics ( may not be all actual ) and if the ower of the site permits
( i haven't read the rules completely and you are interested, i could start another thread that discuss my project ...and related problems :p ) thanks for the interest !
Dick Russell: my thought also !!
from all my recent reading, it seems that 90% of problems are due to air leaks providing a path for humidity to get to the cold parts ... why isn't everyone trying to envelope the building with some stick wraps already ??? seems obvious that sealing in between intricate details makes it much impossible to reach perfection.
Jin,
It's a little hard to answer your questions when they occur in a long post with many different questions on many different topics. I urge you to post just one or two questions at a time.
In your original question, you wrote, "I have to rebuild the small exit house on top ... because my carpenter helper didn't do it properly (all sheating got damp, some rotten wood supports etc... many many air leaks)."
It seems to me that you are living in a house with elevated humidity. You also have air leaks on your top story which led to predictable results.
I strongly urge you to take the following steps:
1. Hire a home performance contractor to perform a blower-door test. If possible, use that opportunity to perform blower-door-directed air sealing. Find your air leaks and fix them.
2. Take steps to lower your indoor humidity levels. Buy a few more hygrometers to monitor your indoor RH in several locations, and to verify that your current readings are accurate. To lower your indoor humidity at this time of year, ventilate! Run your bathroom exhaust fans until conditions inside improve.
Holy stack effect Batman!
Thanks again Martin for taking some of ur time to reply.
Sorry for the mixed up on the thread, wanted to reply to as many poeple as possible
as they took some time to post on the thread.
so,
1- I will hire someone to do a blower test ( BTW how much does the equipment to do this kind of test runs for ?? i have many projects in the next few years and could probably benefit from this )
When i am done with the different problems. I still have 2 doors to make/install and many different leaks on the top room and the windows ... would not be worth it yet ! but i will for sure!!
Will also try to get someone with a thermal camera at the same time, and do it during winter time so we can pinpoint all of the problem areas at once.
2- I know the RH was way too high during the last 2 winters and that might have accelerated the problem with the roof room. we poured more than 200 bags of mortar to level the floors 2 years ago just before winter time , and last year was our first real heating year ..
Still it is unnaceptable and i will settle for nothing less than near perfection ! ( hahaha ).
The rooftop room had a 1/4" X 4" long space under the patio door where u could see outside
( was right under the roof membrane.. u can imagine what it did )
luckily the steel deck was unnafected yet by the situation .
Martin should i start a different thread for the questionning about this room and connections to other planes ?? can we start personal threads or does it need to be of general interest ?
Lucas : please explain your comment, i am not familiar with this expression !!
( my engrish is shabby in the expression department )
Jin,
Lucas is exclaiming that your building is very high, so that a leak on the top story creates an above-average stack effect.
L'origine de cette blague est une émission de télévision des années 70, "Batman."
Martin: i'm sorry but i still don't understand the "above average stack effect " part ! ahaha
Do you speak french ??? I'm too young to have learned anything form the old Batman TV series ...
i'm more of the Transformers generation !
Jin,
Oui, je parle français. Le "stack effect" est l'effet de tirage (qu'on appelle aussi l'effet de cheminée). Voici une explication: Étanchéité : comment se produisent les fuites d’air?.
Une explication en anglais: The Stack Effect: When Buildings Act Like Chimneys.
Jin, here is another article (in English) about stack effect
http://www.buildingscience.com/documents/published-articles/pa-air-leaks-how-they-waste-energy-and-rot-houses/view
not only is your house extremely tall ...
it is also possible that the Neutral Pressure Plane is extremely high in your house (IF the majority of leaks are concentrated near the penthouse)
Jin,
Excusez moi pour la blague deroutant...
Et pour mon mauvaiz francais - ca fait trops long temps depuis que j'ai eu la chance de pratique.
Lucas,
Thanks for the link. Did you notice in the video (at about 1 min 49 sec. or 1 min. 50 sec.), Robin exclaims, "Holy waste of energy!"
Martin,
No, I tuned out after the first minute.
How apropos!
Lucas: ahahha ok i got it now ..i'll remember that one! Votre francais n'est pas si mal dutout mon cher!
Martin: May i ask where u learned french in such a perfect manner?
Je crois que vous l'ecrivez meme mieux que moi, je trouves ca louche !!!!!! haha
About the stack effect, that may explain why this year we are having a very bad draft all through the second floor that wasn't there last year ... but now the front door doesn't leak much on the first floor
and 90% of the house leaks are probably on the roof room, so the "plane" should be approx right on the second floor if it is an average of all leaks distribution !!!
Anyhow, taking care of this is done only by pluggin air leaks right ?
Which should be something i'll work for in the coming months ...
Back tot he PERSIST walls
What should i be looking for in the "peel stick" membrane for it to work properly ??
So many to choose from .
MARTIN: what if if would be to stack the 5" EPS layers with some strips of my ACP material ( 3mm thick ) and have it touch ground all around ??
OR isn't there anything we can use in between insulation foams to help stack it up on walls ??
Jin,
Q. "What should I be looking for in the peel & stick membrane for it to work properly?"
A. You should be looking for an airtight installation. Most rubberized asphalt membranes are similar, but products from Grace (like Ice & Water Shield) are the best known.
Q. "What if it would be to stack the 5-inch EPS layers with some strips of my ACP material (3 mm thick) and have it touch ground all around?"
A. I don't recommend that you try to build a sandwich. As I wrote earlier, I think that 8 inches of foam is the practical maximum for site-built SIPs for your wall (in other words, for thick foam attached with long screws). If you want thicker foam, just buy SIPs.
Q. "May I ask where you learned French?"
A. Mon père était professeur à Beyrouth au Liban de 1963 à 1970, et j'y suis allé à une école française.