What’s the payback?

I read here over and over again the recommendation that a house should be built tight and ventilated. The house should also have insulation levels over what is required and what is typically done. I’m good with that if it makes sense. I’m sure someone has done some studies in various climates and calculated the savings and the simple (or not so simple) payback for the upgrades, but I’m not finding it. What makes sense?
My case, climate zone 5, new 2000 SF home, cheap natural gas. No AC. Colorado, lots of sun. Conservative habits, turn off lights, keep tstat low.
I’ve seen the recommendation here for R-60 ceilings, R-40 above-grade walls, R-20 basement walls, and R-10 basement slabs. What are the economics for going so high? I see here: https://www.greenbuildingadvisor.com/green-basics/insulation-overview, that the DOE recommendation is R 16-27 walls. Typical here is still just 2×6 with fiberglass (or foam) in the wall, no foam, or maybe 3/4″ on the outside, so that meets DOE levels.
What about air infliltration? What would a typical leakage level be? How tight can you build it and not add ventilation? What are the costs and savings for building tight, doing a blower door test, and adding ventilation? Are there some codes and procedures for building air tight?
Sorry, too many questions 🙂
GBA Detail Library
A collection of one thousand construction details organized by climate and house part
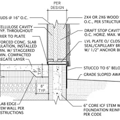
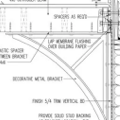
Replies
A code legal maximum air leakage for zone 5 under IRC 2012 or 2015 would be 3 air changes per hour @ 50 pascals. If there has been any forethought at all to air sealing during construction that's pretty easy to meet in most house designs, the exceptions being houses with crazy complicated framing, such as a house footprint with 20 corners and half dozen dormers on the roof. Typ would be 1.5-2.5ACH if they're paying attention, and don't build-in big thermal bypasses & holes such as unsealed band joists or skipping the wallboard behind bathtubs & cabinets, etc.
For insulation values, start here:
http://publicecodes.cyberregs.com/icod/irc/2012/icod_irc_2012_11_sec002.htm
Code min walls would be 2x6/R20 fiberglass in the cavity, not crummy low-density R19s. That's still a pretty low bar to hit. With only an inch of foam on the exterior of a 2x6 wall there isn't sufficient dew point control at the sheathing without interior side vapor retarders. If going with a skinny 3/4-1 inch foam, do not use foil faced goods on the exterior in conjunction with a 6-mil polyethylene vapor barrier on the interior, since it's a moisture trap, and there's insufficient exterior R for dew point control at the sheathing. It's "worth it" from a moisture resilience to install at least 1.5" of polyiso or 2" of EPS on the exterior, either of which is about the same cost as 1.5" XPS, but far greener due to unfavorable blowing agents with the latter. With that much foam you can skip the interior vapor retarder. The "whole-wall-R" of 2x6/R20 16" o.c. with 2" of exterior EPS or 1.5" of polyisocyanurate is about R24-R25. Going with R23 rock wool might be considered "worth it" from a higher fire resistance perspective in brush & forest fire risk zones.
A more resilient code-min wall would be 2x4/R13 + 2" of exterior polyiso, which has even more dew point margin. The whole wall R of that stackup is about R20-R21, and would not need an interior vapor retarder.
An IRC code-min continuous R15 foam is plenty for foundations. A minimalist 2" + 2" EPS insulated concrete form gets you there, and makes it easy to get a continuous thermal break over the foundation sill with 2" EPS sheathing on the above-grade walls.
Blown attic insulation is cheap. The additional cost of an "extra" 3-4" of fluff to hit R60 rather than R49 is cheap enough to be financially rational. Building with "energy heel" trusses deep enough to allow sufficient depth for R60 over the top plates of the walls is not a real cost adder, but you have to specify it.
From a long term perspective, with new construction it's good to consider the site factors and roof pitch orientation for rooftop solar PV, which is getting cheaper every year. In some areas PV + mini-split heat pumps is already cheaper than natural gas, but not in cheap gas areas. Designing for Net Zero Energy has favorable lifecycle enconomics if you presume that buck a watt solar will be available within the lifecycle of the house (highly likely before 2050, maybe even before 2030.) The approximate "whole assembly R" values that makes Net Zero a reasonably straightforward target can be found in Table 2, p10 of this document:
http://buildingscience.com/file/5806/download?token=GouEIX9Y
Note, that document was released in 2009, when cold climate mini-split heat pumps had an HSPF of about 10, and typical rooftop solar ran about 15% efficiency. Since that time cold climate mini-split efficiencies have moved into the 12s, and rooftop solar typically more often ~20% efficiency panels. You can cheat those whole-wall R values a bit and still hit Net Zero with an array that fits on the house, but cost-optimizing it requires a more sophisticated analysis.
If your up for it, you can use BeOpt (a freebie downloadable tool) for modeling the house performance using different insulation levels & prices to narrow down what's cost effective against your current & anticipated future fuel cost. Keep in mind that natural gas has been trading at historical lows since the fracking boom, but it really has nowhere to go but up, barring an unforseen comparable break through on gas extraction technology. Solar has been on a decades long "learning curve", dropping in price by about 20-25% every time production volumes double. In recent years the doubling rate has dropped to under 2 years, and as the levelized cost of the power crashes through various cost barriers, the doubling rate is accelerating. There are no real impediments to that curve continuing. At the utility scale solar is now cost-competitive with combined cycle natural gas power at $3/MMBTU long term natural gas contract pricing.
The utility scale cost of solar today is likely to be the unsubsidized rooftop solar cost by 2022. In general it's safer over the long haul to bet on manufacturing learning curves than to count on volatile commodity pricing.
If you value your health, you should add mechanical ventilation irrespective of your airtightness. Back when my house was ACH 6.2, the indoor CO2 PPM still equalized at 1100 PPM with all occupants home, which has been discovered to impair cognitive performance to a measurable extent. It's even more important if you plan to have any non-sealed-combustion gas burning appliances in the house, like ranges, water heaters, fireplaces, wood stoves, etc. If you build a house where natural drafts through the leaky envelope alone can provide enough indoor air quality for the occupants, it's probably going to be incredibly uncomfortable in the cold weather of your area.
In terms of payback, obviously you want to hit the low-hanging fruit first. The most obvious would be beefy attic floor insulation. If the guys are already blowing it in up there, the marginal cost to add more should be relatively low. Decent windows are another. Your house needs windows; the cost to upgrade to better ones will never be cheaper. Don't skimp on quality and get junk windows that will themselves need replacement within your lifetime.
Consider other things that will be cheap and effective to add during construction, but expensive or impossible to add later. Slab/foundation insulation, for example. The first R has the most dramatic effect, so even R-5 (below code min in many places) will be hugely better than R-nothing.
In new construction, I always urge people to consider insulated masonry walls over wood. You'll avoid the headaches and expenses of dealing with rot, mold, flammability, destruction by insects, drywall damage, and drywall replacement. The house will be hugely more durable over time. CMU walls with exterior insulation, AAC, precast concrete sandwich panels, InsulTech blocks… there are many good options, and most areas have contractors who know how to build with at least one because masonry is commonly specified for commercial, government, and institutional construction. It'll be more expensive, sure, but hey, you're building your dream house here, right? Why not do it right the first time?
Brad,
There is no single answer to your question. The answer depends on many factors, including how long you expect to live in your home, your best guess of future energy prices, and your family's attitude toward global climate change.
For an overview of the complexity of these calculations, see this article: Payback Calculations for Energy-Efficiency Improvements.
If you are building a house for your family, and you intend to live there for many years, remember that you have one chance to get things right. Many of the details we're talking about -- insulation levels and airtightness -- are hard to fix after a house is built.
Of course, at a minimum you need to meet local building code requirements. Like Dana, I feel that it's important to focus on airtightness during construction -- because trivial changes during construction can have huge effects on your home's energy performance for decades to come. Try to seal your thermal envelope against air leakage, and verify your work with a blower door.
When it comes to insulation choices, I urge you to educate yourself on two topics: (a) problems with installation quality when fiberglass batts are specified, and (b) thermal bridging through studs and rafters. Once you've learned more about these topics, you may conclude (as many GBA readers have) that there is great value in specifying one or more continuous layers of exterior rigid foam.
Thanks for the comments. I was hoping for "here's some great studies in cold climates that compared the cost and savings of code compliant homes with additional levels of insulation" :) The building science report that Dana linked looks like a good read.
The code required here is still IECC 2006 & it appears to be the standard practice even for custom home. The builder I talked to a couple of days ago mentioned that they were doing more spray foam in the walls instead of fiberglass because it wasn't much more expensive. I'm aware of the thermal bridge from the structure & I will use some external foam boards, it's a question of how much. ICF is pretty standard for the foundation walls.
I just read the 2015 IECC & I think I'll use that as a baseline and look at the upcharges and savings for going up from there.
Dana said "Blown attic insulation is cheap. The additional cost of an "extra" 3-4" of fluff to hit R60 rather than R49 is cheap enough to be financially rational. Building with "energy heel" trusses deep enough to allow sufficient depth for R60 over the top plates of the walls is not a real cost adder, but you have to specify it.". I talked to my designer about this last week, he said that 14" truss heel was standard, 16" was a little extra. 16" is enough for R60?
With cellulose you get about R60 @ 16" settled depth, but that usually involves an initial depth of 18". A typical coverage chart looks like this:
http://nationalfiber.com/docs/CelPakSpecSheet1209.pdf
For that product it takes 17.7" initial depth to acheive a settled R60 performance @ 16".
GreenFiber wants 18.37" for the initial blown depth:
http://www.greenfiber.com/images/coveragechart/814201344741PMINS541LD%20Fact%20Sheet%20-%20PM-6.3-19%20Rev%20D%205-13.pdf
So you really want 18"- 20" energy heels unless for some reason they're charging an arm & three toes for the additional depth. It's usually a pretty nominal charge.
Brad,
Any complications with raised-heel trusses typically only occur in areas with high wind or seismic requirements. Then the structural blocking between the heels adds considerable labour to what is typically a pretty quick job of framing the roof.
I think it's interesting and legitimate to question whether it's worth spending more for a well air sealed and super insulated home. But what about the rest of the house? You could argue that many people choose appliances, fixtures, and finish work that is more expensive than needed, with absolutely no financial payback. You can spend either $150 or $600+ on a highly rated toilet at local box stores. Looking at that example (which can be repeated on dozens of other decisions in a home), I think spending more for an energy efficient home makes sense if it fits within your budget.
While this is somewhat anecdotal, I know there are builders/architects in the Northeast (zones 5-6) who claim they can build (or have built) "pretty good" or net-zero ready homes that are only +/- 10% more expensive than standard code compliant houses.
While I don't have comparison numbers, I'm know our house build was more expensive because of energy efficient upgrades to the building. What I like about that is we are able to heat and cool the house 99% of the time with a single ductless mini-split ($3k installed after rebate), we have backup electric heaters for the occasional -20f night. That makes sense to me versus a more complicated/expensive heating system.
Looking at your situation: cold (but not extreme) climate, lots of sun, conservative energy habits....if you built your house to "pretty good" or net-zero ready insulation and air sealing levels, it would allow you to have a relatively inexpensive and simple heating system. Maybe 2 ductless mini splits, go all electric appliances, install an appropriately sized solar PV system, and you've got a net zero house. With some passive solar in your sunny climate with a slab for thermal mass, you could probably coast through moderately cold periods of the year (and power outages) with minimal or no heat.
Brian wrote: "I think it's interesting and legitimate to question whether it's worth spending more for a well air sealed and super insulated home. But what about the rest of the house? You could argue that many people choose appliances, fixtures, and finish work that is more expensive than needed, with absolutely no financial payback. You can spend either $150 or $600+ on a highly rated toilet at local box stores. Looking at that example (which can be repeated on dozens of other decisions in a home), I think spending more for an energy efficient home makes sense if it fits within your budget."
Brian I think your comparison of spending on higher end finishes vs money on the envelope is a bit of a red herring. All that should matter in regards to the envelope upgrades is that the extra expense either pays for itself over a given time period or it doesn't. Just because high end finishes do not pay for themselves doesn't mean if you have extra money in the budget you should take it and put it into the envelope irregardless of payback. If the payback is there then I'm all for it, if not then either enjoy a lower mortgage or your high end finishes. There is some value real or perceived in enjoying the home you live in. At least its something visible that you can appreciate as opposed to something hidden behind the sheetrock that will never be seen nor paid for in time. A home is the biggest investment most will make in their lifetime. I think Brad is correct in trying to find out the point in which upgrades make long term sense to his pocketbook.
I don't see my thoughts on finish expenses in a house build as misleading or distracting (red herring). Maybe my point is that it seems common for people to ignore or be financially skeptical towards energy efficiency upgrades, while freely spending money in other areas. I'm also not knocking expensive finishes.
I do disagree with this: "All that should matter in regards to the envelope upgrades is that the extra expense either pays for itself over a given time period or it doesn't."
Like the real and perceived value of other parts of the home, envelope upgrades can have that too, even if the expense doesn't payoff in measurable energy savings. Envelope upgrades can lead to "payoff" in comfort, build quality, and owner satisfaction.
Well if the envelope is poor enough to cause discomfort I would assume that upgrades would in fact pay off. Not trying to ruffle feathers, I just tend to look at envelope specs or improvements as a cost benefit analysis with dollars being the primary factor. I just dont see the satisfaction in creating an envelope better than 95% or whatever percent you use of other homes if the long term dollar net is negative. To each their own. If the choice is envelope improvements that do pay back over fancy finishes I would agree envelope improvements would be the better choice. Finishes can be upgraded later. I just wish appraisals would take into account the homes energy efficiency. At least in our area there is no additional value added.
Brad, you seem to be asking when is the point of diminishing returns crossed. I agree this is a legitimate issue that could be reviewed continually as costs change. I feel that there is no hard point, and that you have quite a bit of cushion before you might experience an actual loss. I have found my concern reduced after reading the following articles.
Attached is an article from PBS News Hour that argues investing in energy efficiency is more profitable and safer than any investment in the stock market or other financial instrument for a variety of reasons. Among them: even if both investments result in $100 in your pocket at the end of the year, the returns from a cheaper utility bill will be tax free, and the investment is protected with homeowners insurance!
Paul Soloman in his "Making Sense" series also wrote that it is a better investment for many reasons (I'm sorry I cannot now find this article). One of his arguments was that in new construction, the added investment in energy efficiency will result in a net profit (i.e. money in your pocket) if the house is mortgaged and the cost of the mortgage plus the monthly utility expenses are compared. In other words, the more expensive mortgage resulting from the increased building costs plus a cheaper annual energy cost will be less than a typical build with higher monthly energy costs. This calculation means the payback period begins in the first year!
For myself, I used the article "High R-Value Walls In All Climate Zones" for a guide (BuildingScience.com).
David,
In that interview, Hilton Dier made some generalizations. The generalizations apply in some cases -- most notably, to residential PV systems installed in states with net-metering contracts and SREC payments. (See, for example, Making Room for a PV Array.)
In the interview, Dier also makes a passing reference to a $100,000 deep energy retrofit. The type of investment is totally different from a $13,000 investment in PV, as I explained in another article, Deep Energy Retrofits Are Often Misguided.
Higher R houses are far more than just about the net present value of the future energy savings or hedge value against potential energy price inflation. It's at least as much about making it a more resilient house with higher comfort levels. This is not a simple financial calculation.
One major repair related to built in moisture traps incurred by a need for interior side vapor barriers (or failure of a vapor barrier) can cost more than the "extra" inch of exterior foam that would have allowed the assembly to not need them.
Some extra-R and better air tightness also allows the house to cruise through mid-winter temperatures with much lower risk of plumbing freeze-up in the event of an extended power outage too. It doesn't take anywhere near a PassiveHouse level of performance to design a freeze-up proof house in a zone 5 climate, but it usually has to be somewhat higher performance than code minimum.
These sorts of resilience factors can be considered as having something akin to insurance value. That is a real value, yet completely unrelated to the value of net energy cost savings.
In most residential energy markets the present value of moving from IRC 2003 levels to IRC 2015 levels is much higher than the cost delta in even a 10 year analysis. Taking it from IRC 2012 to BA-1005 levels ( see Table 2: http://buildingscience.com/file/5806/download?token=GouEIX9Y ) is nearly always NPV positive in a 50 year lifecycle analysis on energy savings alone, even assuming zero energy inflation, and often in less than 20 years. If/when solar leveraged by heat pumps is cheaper than condensing natural gas on a lifecycle basis, the financial analysis changes, but you'll have a house capable of taking full advantage of that eventuality.
Gas won't always be as cheap as it is today- it's a commodity with volatile pricing, currently trading near historical lows. But solar will never be more expensive than it is today- it's cost trajectory over time is in one direction. PV is still a relatively young manufacturing technology on a fast learning curve. Even if PV + heat pumps isn't currently cheaper on a lifecycle basis than natural gas + condensing furnaces in your area, that day WILL come- probably before the gas burner's full lifecycle is up.-
It is pretty hard to calculate finacial value when we can only guess what energy will cost in the future. The knowledge that future energy costs don't matter is itself worth something.
Dana mentioned resilience. I turned off the heat in our pretty good house on April 12. Since then, we've had nightime lows in the 25-45° range and daytime highs between 38 and 65. Today it's snowing and 35°
The interior temperature right now is 69° . It hasn't been colder than 68° in the two weeks since we turned off the heat.
Stephen- the future cost of electricity will be bounded by the levelized cost of PV, which is shrinking year on year, and will eventually cross over natural gas energy costs (fairly soon, when leveraged by heat pumps.)
It sounds like with springtime type weekly solar gains YOUR house idles along about 35F above the average outdoor temp. In winter the solar gains can be either lower or higher than in spring time, somewhat dependent on snow cover and shading factors, but the shorter daylight hours would probably reduce that spread to something like 20F, but probably not as low as 15F. But that would be sufficient for freeze control in a zone 5 climate. The colder days are clearer, with higher solar gains. Cold snap weeks in Denver or Boulder have ultra-sunny days with mean-daily temps in the mid-teens, even when it dips into -10F territory over night. With a 20F delta from the average temp those colder weeks interior temps could hit the 30s with the power out for several days in a row, but it wouldn't be a hard freeze indoors. If the house started out at 68F it would take most of a cold week to drop that low indoors. In average mid winter weeks in Denver it would be in the high 40s or even low 50s Fon solar gains alone. That's not PassiveHouse warm, but it's fairly well freeze protected with the power out.
Another comfort factor to consider, both in selecting insulation stackup and interior surfaces, is noise. From my own diy experience, I've a noticed a difference in sound abatement for high density cavity fill vs commodity density and no exterior insulation vs exterior foam board. Anecdotally I've heard of really great results from exterior rock wool board. The same is also my experience for builder grade vinyl vs fiberglass and triple pane. These are really hard items to retrofit. If your site is at all noise impacted now or in the future, I'd consider better sound control via better insulation and surface isolation.
Some good thoughts here. A greater payback would be a smaller home. Not talking tiny homes, because those usually aren't practical. But going to the size of a typical apartment in your area is a good start. There is a lot of research to get the lowest square footage and still make people happy done with apartments. That square footage is a lot less than McMansions being built currently.
For all good ideas about insulation and more importantly air sealing, the greatest thing you can do is build smaller.