What’s the best way to renovate/rebuild an old south-facing exterior wall?

Hi All – I am a newbie to this group but have considerable building experience remodeling and renovating homes, and completing unfinished properties. Still, I am no expert building contractor.
I just bought an older home in Northern Nevada that was built in the 1970’s. We are South of Reno. It is high mountain desert, very dry most of the year, and around 5000 feet. The map says we are between zones 5B and 6B. The southern exposure of the home experiences huge heat gains during sunny days. Inside temps in the rooms on the south side of the house usually lag the outside temp by no less than 5 degrees F, which means that during 95 degree days the inside temps are 90 when I don’t run an AC. The Hardyboard siding on that exposure is heavily weathered so I do plan on removing and replacing all of that.
The wall construction is 2×4 and consists of drywall over bare studs on the inside and hardyboard over studs on the outside with what appears to be 15# felt paper between the studs and the hardyboard. The space between the 16″ OC studs is insulated with kraft paper faced fiberglass with the paper facing against the drywall.
We have quite a view so all these walls have very large windows. The room with the worst heat gain has the largest: 2 windows that are 60″W x 72″H. The windows are double pane and are probably original argon gas based windows. All of the windows have heavy condensation stains between the panes so its pretty obvious that the seals have been compromised and most likely the argon gas is entirely depleted. I also plan on replacing all of the windows in this house.
Last but not least, this home experiences serious problems with dust infiltration. After a couple of days of high winds (not unusual this year) there is a fine coating of dust everywhere so its obvious that the WRB is failing as far as wind leakage and intrusion is concerned.
I want to bring this wall up to current standards or beyond. I figure why pay a ton for advanced HVAC if the walls are leaking heat (and dust) all year long. I want to start with making the walls as good as possible and with improving the WRB to as high a standard as possible. I have read with great interest everything I could find on this site, especially those articles discussing polyiso, but my reading and studying on the topic has produced as many questions as it has solved:
- Should I sister in 2×6 studs so I have a larger void for insulation or is it more energy effective and/or cost effective to use sheet(s) of 4×8 polyiso between the 2×4 studs and the exterior siding? It seems to me that the 2×6 studs may not be as cost effective because of the additional labor of furring the windows to make them line up with the newly extended exterior. On the other hand, two layers of 3/4 or 1″ polyiso 4×8 sheeting adds its own special problems with mounting and weatherproofing new replacement windows.
- Or, instead of #1 above, would it be better to just replace the fiberglass batts with 16″W polyiso between the studs? Obviously I could get up to 3.5″ of polyiso between the studs but I assume there is a point of diminishing returns where the heat loss transmitted by the wooden studs and fasteners exceeds any gain of additional insulation
- The consummate question would then be whether a combination of the above would be the most energy effective and cost effective? Maybe the 16″ batts of polyiso between the studs (how thick?) plus two sheets of .75 polyiso mounted horizontally under the siding?
- Along with the question of combining solutions and methods: what kind of siding should I consider? I know there are siding solutions that include polyiso or polystyrene cladding on the inside.
- Lastly is the question of repairing/replacing the WRB to resolve the issue of air leakage. I guess the most effective solution would be largely dependent on which of the above solutions for insulation are chosen?
GBA Detail Library
A collection of one thousand construction details organized by climate and house part
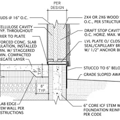
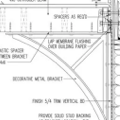
Replies
There are many ways to build a good wall. If I was doing it, I'd use external insulation to reduce thermal bridging through the studs. If you use exterior insulation and also insulate between the studs, you need to make sure that at least a certain percentage is outside. There are articles here on that topic. See, among other articles, "Calculating the Minimum Thickness of Rigid Foam Sheathing"
The next decision wrt exterior insulation is which kind? If you use mineral wool, instead of EPS, that will likely change the location of your drainage plane, flashing, etc, so this is a decision that needs to be made early in the design process.
Between the studs, I'd look at dense-packed cellulose if you have local installers with experience. If not, mineral wool batts would be the next option but a large improvement over fiberglass batts.
Polyiso loses some R-value at colder temperatures, so if you go with polyiso on the outside layer, make sure you de-rate it's R-value when you figure out your interior/exterior ratios.
If you are replacing windows, as well as exterior siding and insulation, you have an opportunity to review your fenestration. Most people at this site feel that the passive solar houses of the 70's were a mistake [edit-poorly designed] , and that you should add windows where you want them for views, then make your building envelope better. This is especially true if you already have overheating and perhaps insufficient overhangs. See "Reassessing Passive Solar Design Principles" & related articles by Martin.
Sounds like you've got a great place to live, hope you come up with a design that lets you enjoy it to the fullest.
Roger,
Here are links to the two articles that Andrew was talking about:
Calculating the Minimum Thickness of Rigid Foam Sheathing
Reassessing Passive Solar Design Principles
You mentioned that you plan to install new siding and new windows. If you plan to install new siding, you will be working from the outside of the wall, not the interior.
You said that you plan to remove the existing HardiBoard. It may be possible to leave the HardiBoard panels in place -- I'm assuming they are 4x8 panels or 4x9 panels, not lap siding -- and use the HardiBoard as sheathing. It's also possible to remove the HardiBoard as you plan to do, and to install new OSB or plywood sheathing instead.
With work on this scale, it's possible to pay close attention to airtightness so that you end up with a low-infiltration wall. There are lots of ways to do it.
The easy way is to hire a spray-foam contractor to install closed-cell spray foam between the studs. In theory, that work could happen from the exterior (if you remove the HardiBoard). That approach doesn't address thermal bridging through the studs, but it will do an excellent job of air sealing.
The more labor-intensive approach would be to install an adequately thick layer of rigid foam on the exterior side of the HardiBoard (or on the exterior side of the new OSB or plywood sheathing). That's the approach I would take.
When you install the new windows -- low-SHGC windows, of course -- you'll have an opportunity to install perfect flashing in the window rough openings, and the window flashing can be integrated with the new water-resistive barrier (WRB). If you take this approach, you need to pay attention to airtightness by taping the seams between the HardiBoard or OSB panels with high-quality tape like Siga Wigluv or Zip System tape.
Thanks Andrew. Great Advice and gives me lots of food for thought. You didnt mention whether or not you thought that sistering in 2x6's alongside the 2x4's would be worth the cost and effort of installing them and of having to rebuild all of the window and door headers?
Roger,
Regarding the sistering of studs, I probably wouldn't take that approach. I would concentrate on airsealing and getting an adequate amount of insulation outside of the sheathing to meet your overall R-value goals for your wall.
I'll put in another plug here for GBA: if you haven't been coming to this website for a while, there is a lot to absorb. And if you are building, you will save yourself a lot of time/grief/money by getting a GBA subscription and making sure that you've planned the entire build before you commence building. Green Basics, Stategies and Details, plus Martin's seminal article "How to Do Everything" will pay back many times over. If you already know this...let others know! End of plug, and no I do not have any association with GBA, other than being a regular visitor.
Thanks much Andrew
Yes! I have been cramming on the articles and "how-to's" all over GBT for the past week or ten days and there really is a wealth of information. Better yet, so far everything I have read sounds like great and current advice. I havent found anything that seemed obsolete or old school and continue to spend every moment I can spare reading new articles and posts as well as reviewing other articles already read. Great Job Guys!!!
In answer to post #2 - thanks for the great advice Martin. One additional question I would have is in regards to the issue of whether or not to use that first layer of external sheathing, especially if I remove all of the existing Hardiboard. The Hardiboard is the only siding on this house, i.e. there is no sheathing on the outside of the studs and then the Hardiboard on top of that.
I am leaning strongly towards removing all of the old hardiboard and the existing insulation. Then, using spray foam to seal all of the drywall penetrations. After than filling the space between the studs with 3.5" of denim batts. After that I favor two layers of 4'x8' 3/4" foam overlapped and tightly taped so as to form the WRB and the wind barrier. Lastly, a standard external siding material over the top of the foam. I would also use polyiso as the first layer and EPS as the second layer to somewhat offset the sensitivity of polyiso to colder weather.
As a reminder (for this discussion) we are in zone 5, in Northern Nevada, high mountain arid plateau at around 5000 feet. It is very dry most of the time with humidity in the 15%-30% ranges. Wintertime temps get as low as 10 and summertime sees a lot of 90's and perhaps a dozen or so 100 degree days. This valley can get severe winds, mostly from the south; but they can whip through the valley at 80 mph with gusts higher (we had that last week during the start of the Little Valley Forest Fire).
So, to use sheathing under the Polyiso sheets or not??
Thanks much
Roger,
Exterior sheathing is required on most houses to brace the walls (provide racking resistance). If you have any doubts about whether sheathing is needed, or if you have a plan to use an alternative method of bracing like let-in bracing, you need to talk to an engineer. Otherwise, install plywood or OSB sheathing.
I strongly suggest that you install furring strips between the rigid foam and the siding. The furring strips create a ventilated rainscreen gap, and provide something you can fasten the siding to.
For more information on these issues, see these two articles:
How to Design a Wall
All About Rainscreens
Thanks Martin - great references... I hadnt seen either as of yet.
I have recently discussed the issue of sheathing vs no sheathing with my CE. His take was that if you use sheet siding you gain nothing by applying sheathing first. However, my concern is that by using polyiso or EPS sheeting under the siding I would be compromising the anti-racking strength as now the siding is no longer in direct contact with the wall studs. Do you agree?
Also, I hear and appreciate your advice on using furring strips to create a rain gap, but I wonder if the payback is quite as high here in Nevada where there is little rain - at least not like the southeast?
Lastly could you please elaborate on the configuration of 2 layers of foam sheeting. Should either (or both) layers be faced? If so, should the (radiant) facing be towards the interior or exterior?
Thanks so much for the great advice.
Roger,
Q. "My concern is that by using polyiso or EPS sheeting under the siding I would be compromising the anti-racking strength as now the siding is no longer in direct contact with the wall studs. Do you agree?"
A. Yes, and your engineer will agree too. Talk to your engineer -- and take his or her advice.
Q. "I hear and appreciate your advice on using furring strips to create a rain gap, but I wonder if the payback is quite as high here in Nevada where there is little rain - at least not like the southeast?"
A. It's a judgment call; in any case, I don't think the word "payback" applies here. A lot depends on what type of siding you intend to install. Many types of siding shouldn't be fastened directly to rigid foam -- especially wood siding.
Q. "Could you please elaborate on the configuration of 2 layers of foam sheeting. Should either (or both) layers be faced?"
A. The facing on the rigid foam, if any, is mostly irrelevant. That said, faced EPS is easier to tape than unfaced EPS.
Q. "Should the (radiant) facing be towards the interior or exterior?"
A. There is no benefit from a radiant barrier unless it is facing an air space. If you aren't planning a rainscreen gap, there will be no thermal benefit from aluminum facing. If you want the thermal benefit -- it's only about R-1 or R-2, assuming that you have an air space -- then include a rainscreen gap, and install the aluminum facing so that it's adjacent to the rainscreen gap. For more information, see Radiant Barriers: A Solution in Search of a Problem.