What’s a better stackup for R-value and moisture management for a cathedral ceiling?

I have a hand framed area between ganged room in attic trusses that I could potentially turn into a cathedral ceiling. The spacing between the gangled roof trusses is 10′ and is hand framed with 2x6s running perpendicular to the top chord of the trusses. The 2x6s are attached with metal joist hangers that are attached to the top chord. (Think flush installed purlins). The finished ceiling material will be blue board gypsum and veneer plaster. The finished roofing is asphalt shingles over 15# felt with 5/8″ plywood sheathing. Building location is climate zone 6, Green Bay, WI. Go Packers!
My initial plan was to frame a flat ceiling and insulate as you would a normal attic ceiling. I would not have continuous eave to attic venting for the 10′ wide area, but since the surrounding trusses are at 24″ o.c spacing and my soffit panel net free area exceeds the net free area of the ridge venting I think I would have enough ventilation to avoid other problems.
However, I have since gotten used to the airy feel of the cathedral ceiling and think it might be worth the extra expense to insulate it this way. The best options I can think of are as follows:
1. Insulate between the hand framed 2x6s with cc spray foam. I think a good installer could average 5″ of foam if sprayed directly to the roof sheathing. This option would have an r-value well below code but would provide a tight assembly. Drywall installation and install would be simple. Installed cost of approx $5/sf. Concerns would be the cost and replacing roof sheathing at later date.
2. Install r-21 batt in direct contact with roof sheathing followed with (3) 2″ layers of one lb density eps foam and 1″ of polyiso with taped seams. If I do the labor I could install this for approx $1/sf without the costs of long screws and strapping that would be required. My material costs are quite low since I was able to buy 2″ reclaimed eps in perfect shape for $2/sheet. My concerns are the roof sheathing has zero drying potential to the inside and the difficulty of installing the thick later of foam. Also, would condensation or frost occur on the underside of plywood sheathing?
3. Install 2x6s on edge running the opposite direction as the hand framing to increase the total cavity depth to 11″. With this install I thought I would install cut and cobble eps foam tight to the roof sheathing to the depth of the first 2×6 and spray the second 2×6 area with cc spray foam. Cost per square foot $5.30. I think this construction would be easier, but the cost is much higher. Drying potential would be zero. There would be a small amount of thermal bridging where the 2x6s intersect. If needed, the roof sheathing could be easily replaced.
4. Install 2x6s on edge as above, but install 5″ of cc spray foam first against the roof sheathing and install dense packed cellulose to fill the second 2×6 cavity. Cost would be approx $6.30 per square foot. I’m not sure if the moisture buffering of the cellulose has any benefit if there is nothing to “buffer”. Concerns are that replacing roof sheathing could be difficult if ever required due to the spray foam. Also, it’s the most expensive option.
On paper, option 2 looks the best, but please share your thoughts or alternate ideas. This would be in an approximately 250 sf area.
GBA Detail Library
A collection of one thousand construction details organized by climate and house part
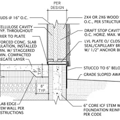
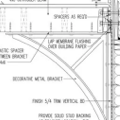
Replies
Rick, if you replace the 2X6s with 16" open web floor trusses set as purlins in their stead, 2" of EPS on the underside of the truss with various combinations of EPS and batt between the trusses could achieve R-49 or greater insulation levels and still provide and 1 1/2 vent space below the top cord of the trusses; so you wouldn't have to worry about the condensation and ice dam issues associated with unvented roofs in cold snowy areas.
Kevin, that's a pretty good idea and one that I hadn't that of. I still think it would be almost impossible to install a topside air barrier trying to cross all the diagonal webbing in the trusses.
Either way, my structure is already framed so I need to stick with a hot roof. As detailed with multiple layers of foam and taped seams, I can't foresee an issue with ice damns, but that's why I'm seeking alternate opinions and advice from builders/owners.
1: 5" of closed cell foam has a vapor permeance just over 0.2, which means it's closing in on being a moisture trap for the roof sheathin, between the 0.1 perm (or less, if you have something like Ice & Water Shield up there) and 0.2 perm foam. What's more, it's an environmental travesty, since it's blown with HFC245fa, which has a 100 year global warming potential roughly 1000x that of CO2.
2: The facers on the polyiso are true vapor barriers, with a combined vapor retardence less than 0.03 perms. This is all but guaranteed to be a problem.
3 & 4: see problems with stackup #1.
Kevin's approach has merit IF it has sofftit-to-ridge venting of the roof deck, AND the interior side can be made sufficiently air tight.
A code-legal zone-6 unvented stackup would be R24 air-impermeable insulation applied directly to the underside of the roof deck, and R25 fiber below that, with no interior side vapor retarder except for latex ceiling paint. That would be 4" of ccSPF (an enviro-disaster, and potential moisture trap), or 7" of open cell foam with R25 fiber below that. Open cell foam is blown with water, and uses only about 40% of the polymer per unit R, but it's also more vapor permeable, which presents potential problems, but not as bad as one might think. Most half-pound ocSPF would run only 5 perms @ 7", which in combination with the 5 perm standard latex paint means the vapor permenace between the roof deck and interior space is about 2.5 perms. As long as the interior is air tight, that would be good enough for a zone-6 climate.
You could improve upon that with a "smart" vapor retarder such as Certainteed MemBrain or Intello Plus between the fiber and ceiling gypsum, which is sub-1 perm when the proximate air has a relative humidity below 35% or so, but becomes vapor open when the proximate air is over 50%. So in the spring when the roof deck warms up in the mid-day, releasing it's moisture into the foam & fiber the RH in the cavity rises high enough that the vapor retarder opens up and lets it out. Then at night when the roof deck temps drop, re-adsorbing some of that moisture, it closes back up, limiting how much moisture gets in from the interior.
Code is silent about the use of variable permeance vapor retarders, but they DO work pretty well, unless it's a pool/hot-tub room, or you actively humidify the place to over 40% in winter.
Another approach is to put 2" of ccSPF on the roof deck (about 0.5-0.6 perms) to protect the roof deck, with R38 fiber on the interior side of that. Without a smart vapor retarder the roof deck is still fine, but you may have wetting of the cold side of the insulation during protracted cold weather. (If you use cellulose it would buffer most of that moisture without damage or loss of function, but it wouldn't meet the letter of code. WITH a smart vapor retarder this approach is pretty solid, and if the interior RH is 35% or less, the smart vapor retarder behaves like a class-II vapor retarder, which would meet the spirit (if not the exact wording) of the code.
The best approach would be to put R24+ as rigid foam above the roof deck, R25 under the roof deck, in which case you are golden.
If your total R-value is something other than R49, as long as 50% or more of the total R is air-impermeable, you have no condensation or roof deck adsorption issues to be concerned about. But if it's on the interior side, it's best if the total vapor permeance between the roof deck and conditioned space is no lower than 0.5 perms, so that the roof deck can actually dry in a season.
Dana,
I've seen the recommendation for foam on both sides of the roof sheathing, but wouldn't that also be a moisture trap? Martin seems to think a foam sandwich on walls is a bad idea. I thought I remember reading that an asphalt shingle roof is nearly a vapor barrier in one of Joe L building science insights. If this is the case, how does the roof sheathing accumulate moisture if it's blocked on the underside with an air barrier.
I really want to avoid the thick layer of cc spray foam if can be avoided for the reasons you have outlined and also for the expensive install. How about 6" of type 1 eps installed tight to the roof sheathing (cut and cobble), followed by an inch of cc to seal everything up, followed by the fibrous insulation? This still meets code since the eps foam is air impermeable. Does it have enough drying potential?
I still don't understand why the fibrous insulation against the roof sheathing is a problem as long as the foam beneath (interior foam) is properly applied and air tight...Unless that moisture is making it's way in from the shingles?
I used normal #15 felt underneath the shingles.
Rick, I was making my suggestion with the thought that you had the roof already framed and shingled. To be clear the steps of the not so easy task of replacing the 2X6s would be. One: cut away the lower portion of the 2X6 leaving a just 2” attached to the sheathing. Two: remove the ends and joist hangers to make room for the new hangers. Three: clamp the new truss along side the 2X2 remnant and nail through the remnant to sister them together. Four: nail on the joist hangers to permanently secure the ends.
Top side air barriers, though good practice to prevent insulation from blocking the ventilation space and reduce convective losses in fibrous insulation, aren’t code required. Their benefit in reducing convective losses increases with the steepness of the roof slope. A tight barrier is only critical when insulation is blown into purlin bays, to prevent blockage of the ventilation space.
Insulation and air sealing alone won’t prevent ice dams. The better insulation can just lead to a deeper accumulation of snow and allow for higher ice dam backing up water further into the house. Asphalt shingles over felt provide no protection against leaks from ice dams. Many builders address this by covering extensive areas of the roof with ice and water shield. But, ice and water shield blocks all outward drying potential of the sheathing.
"I've seen the recommendation for foam on both sides of the roof sheathing, but wouldn't that also be a moisture trap? "
That's no more of a moisture trap than closed cell foam directly on the underside of the roof, since even a #15 felt + asphalt shingle layup runs 0.1-1.3 perms- the edge of Class-I vapor retardency. Peel & stick membranes are WELL into Class-I vapor retardency- as vapor retardent at 6 mil poly ethylene (or more). There really is no drying-toward the exterior through shingled roofs- in cold climates there will be snow & ice above the shingle for weeks or months on end, which is why the vent them on the under-side of the roof deck.
But by putting foam above the roof deck you...
A: keep the roof deck warmer (=drier, taking on less wintertime moisture from interior moisture drives, and beginning the drying season sooner)
...and..
B: you can use less foam on the interior, to allow higher drying rates toward the interior.
" How about 6" of type 1 eps installed tight to the roof sheathing (cut and cobble), followed by an inch of cc to seal everything up, followed by the fibrous insulation?"
That can work if perfectly air tight, but perfection is hard to hit even on day-1, let alone over the lifecycle of a building. Better to put the R24 EPS on the exterior of the roof deck, which keeps the roof deck much warmer (= drier), held down either with 2x furring for a vented nailer-deck, or a sacrificial nailer deck of 1/2" OSB through-screwed to the rafters. With the latter, you'll be replacing some sheets of nailer deck when you re-roof if it leaked, but unless you wait until the roof is totally ratty (say, year 40 of a 25 year shingle) most of it would hang-in for the duration. And, putting it on the exterior thermally breaks the rafter elements with R24 foam, which is a significant performance boost even at a 10% framing fraction.
Rick, on second thought; even with your unvented roof options you’ll need to add ceiling joists to support the drywall. A likely method would be to hang them off ledger boards secured to the truss struts. With that method there would be no additional cost to set the ceiling lower to accommodate a ventilation space below the existing 2X6 purlins. It would just result in a lower ceiling. I’m not sure if the 2X6’s would trap enough more heat or hinder air flow in a way that would necessitate a larger than normal airspace below the 2X6s.
Rick - the ideal way is to add a 2nd row of 2x6's below the first (either hung with plywood scraps, or fastened to ledgers on the walls) , leaving about 20" from the bottom of the lower ones to the roof deck. This eliminates thermal bridging in this assembly, and allows you plenty of room to install R60 insulation with a ventilation channel. Or add 4" of closed cell spray form to the roof decking, eliminate the vent channel and fill in below that with batts or loose fill insulation. You can install an air barrier below the ceiling to control air leaks. Either way, it's pretty easy to do.
You also need to add insulation to the side walls of the cathedral to bring that up to the correct insulation level.
@Bob Irving
If I don't go with the cc spray foam approach I think that's what I will do. I can attach 2x4 standoffs to the existing 2x6 purlins and then install 2x6 non-structural rafters to the standoffs to attach drywall. I would then be able to use a fluffy insulation. Unfortunately I probably can't dense pack unless I were able to somehow attach insulweb on the top side and bottom of the insulation cavity.
It's a shame that cc spray foam has so many issues, as it's a great problem solver.
When HFC245fa is banned for use in this application, the foam vendors will switch over to an HF01234__ variant, as has happened in Europe.
The environmental hit from the polymer and fire retardents would still be there, but at comparable densities HFO1234 sprayed polyurethane would be no worse than pentane-blown polyisocyanurate is now.