What type of insulation or technique would you recommend for ceiling and walls before drywall goes up?

Just did a California Fill type room addition but has a low slope roof. Joists are about 9 inches deep. Fascia block vent holes connect old roof with new. New roof is some sort of flat roof membrane with foil on sheathing facing attic. (We don’t have real innovative contractors or architects here–Sorry).
House is in San Diego.
Thanks for your help.
GBA Detail Library
A collection of one thousand construction details organized by climate and house part
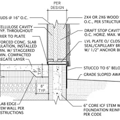
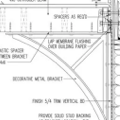
Replies
It would have been better to put 5-6" of fiber faced rigid roofing polyiso between the roof deck an membrane than anything you'll be able to do on the interior.
Do you have pictures?
This wasn't done. SO.....................................Attached are photos.
more photos
oops photo again
Lisa,
You have several options. Here are two articles that discuss your choices:
Insulating Low-Slope Residential Roofs
How to Build an Insulated Cathedral Ceiling
What type of insulation would you use to get the most air space about it? Is there a rigid type that might have more bang for the thickness so to speak?
Lisa,
The two insulation materials with the highest R-value per inch are closed-cell spray polyurethane foam and a type of rigid foam called polyisocyanurate. Both insulation products are rated at between R-6 and R-6.5 per inch.
Thanks. I need about R-30 so I think about 5 inches of the rigid would work and give 4-5 inches above it. Do you think usng this rigid insulation is the best approach in this situaion? I know they make compressed fiberglass for cathedral ceilings but it would only give me an inch to 3 inches at the most above it. I don't know anything about other types hence my question.
"We don't have real innovative contractors or architects here--Sorry"
Are you sure that's the case? There have been a lot of "green" projects in San Diego and it does have a Green Building Council.
I can only speak for the contractors and architects I have dealt with on small residential projects like mine. I am sure there are better ones out there, especially if you have big bucks, but I haven't personally met them or know how to source them (and I have a budget). My architect didn't know anything about a SIP panel or ICFs or about insulating flat roofs, passive solar, etc. Don't know how or when he was educated. The contractors I have met are even worse when it comes to trying anything different; but again its a money thing because there are more talented subcontractors they can learn from but you are paying more for this I guess. So most of us middle class try to educate the contractors and architects ourselves, and it gets quite aggravating of course. Believe it or not, San Diego has alot of qualities similar to a smal conservative town. But I won't go on about that. Tell me more about the Green Building Council?
Lisa,
I don't know why the contractor drilled holes in the blocking at that location. Any ventilation channels have to go between the top of the insulation and the roof sheathing, not in the bottom of the rafter bays.
If you install rigid foam sheathing, the best location for it is on top of the roof sheathing. That means you will need a second layer of roof sheathing on top of the foam, plus new roofing. If your roofing is already installed, it's too late for that.
Your mention of fiberglass is off base. Please re-read the two articles I linked to. You can't use fiberglass here. I think you will probably have to install spray polyurethane foam.
The roof and sheathing is already on. This is the way the architect designed it. This new room goes slightly over the old roof and old exterior wall (now an interior wall) and this is the only place we can get ventilation into the old roof. The articles don't really apply in this situation (and unfortunately my architect never read them) and the City of San Diego doesn't really care about ventilation of a roof as they told me to my face.
Come on guys. Give me a retrofit solution. Or else I don't quite understand. Its not the ideal situation, but can't I use some insulation in these 9 inch bays and pull a little bit back from the frieze block holes on each end and also hopefully find an R-30 thats less thick so air flows over it?
Lisa,
I've given you a suggestion -- spray polyurethane foam. I have also given you links to two articles that explain the reasons why it's very hard to use air-permeable insulation (like fiberglass) or a vented approach in a low-slope roof.
Since you can't really vent this roof, the two most obvious choices are rigid foam above the roof sheathing (which isn't feasible because you have already installed the roofing) or spray foam under the roof sheathing.
I HAVE TO vent the roof. If you are saying I can use SPRAY foam in the VENTED roof then I have two questions. Will this interfere with the foil on the interior sheathing and isn't this stuff flammable? In southern California was trying to avoid this if possible.
Lisa,
It's very difficult to vent a low-slope roof. It's possible, but difficult. I doubt if you really want to do it.
If you do, all of the necessary steps are outlined in my article, Insulating Low-Slope Residential Roofs.
Here are the steps:
1. Specify very deep roof trusses. [As far as I can tell, you didn't do this.] The trusses should be deep enough for 12 to 16 inches of insulation (depending on your climate), plus room for an air gap of at least 6 inches between the top of the insulation and the roof sheathing. Even better: frame the roof separately from the ceiling, so that there is an attic that is deep enough for human access.
2. Provide vents at the perimeter of the shallow attic. [As far as I can tell, this is impossible in your house. For one thing, you don't have an attic.] These can be soffit vents, fascia vents, or wall-mounted vents, as long as the vents allow exterior air to connect with the air gap between the top of the insulation and the underside of the roof sheathing.
3. Provide one or more vented cupolas (“doghouses”) in the center of the roof. [My guess is that you don't want to build one of these.] Most building codes require 1 square foot of net free ventilation area for every 300 square feet of attic floor area; half the ventilation area should be located at the perimeter of the building, and half of the area should be located at the cupolas near the center of the roof.
4. Perform air sealing work at the ceiling before the insulation is installed. Pay close attention to electrical penetrations, plumbing vent penetrations, the top plates of partition walls, and access hatches. The ceiling should be airtight as you can make it. [This step is valuable, no matter what type of insulation you choose.]
Because of all of the significant difficulties associated with taking this approach, I strongly advise you to build an unvented roof assembly.
Once again, I strongly urge you to read the two articles I linked to.
Martin, I reviewed the articles and have spent time in coastal San Diego. The climate is very moderate year round. I think local best practices apply. Your last post to me is way off the mark as to building a vented roof. There may be areas where all the concern for night sky cooling does apply but I bet San Diego is not one of those areas.
I say get a contractor to do the work there that he has done repeatedly well and is experienced at. Internet based advice is with no contractual obligation is OK to me only if you then follow up with contracting with a local experienced contractor.
If your architect didn't provide insulation details then correction of this project starts with getting a set of plans from an insured professional plans provider. One benefit of this site would be for you and your contractor and plans provider to join so as to view all the plan details this site has for one source of reference.
Last thought. Do what works in your area via someone who knows how to do it.
Martin, not being onsite I agree that an unvented spray foam solution works, but since most homes out there have not an ounce of spray foam must be other builds possible. Millions CA homes are fiberglass batt insulated. The coastal climate is so mild insulation is like the last concern. Traffic and earthquakes a bit more to me. ;)
AJ,
You're certainly right that San Diego has a different climate from most other locations in the country.
My article on low-slope roof insulation described a cluster of rotting roof problems in Arizona. But just because a technique fails in Arizona, doesn't mean it won't work in San Diego.
I think it's always safer to stick with mainstream advice. But if local experts in San Diego do things differently than the way it's done elsewhere, there may be good climatic reasons to justify their idiosyncratic details.
So, Lisa, if you want to seek out local advice, AJ might be right.
OK. So now I'm totally confused as to what will or won't work. Who is an expert in my area that I can trust who realy understands the science and won't set the project back a month or two which I can't afford ?
Lisa,
What is the main reason that you don't want to create an unvented roof assembly using spray foam?
OK. Here we go again. The new room addition slightly covers the old roof of the existing house which is a VENTED low slope roof (about 3:12) with gable vents higher and frieze block circular vents on lower end of which half these holes would be covered by the new room addition if we didn't add new exterior holes to the new addition to try and replace some of the ventilation low down for the old roof. I would have to change the entire old roof to nonvented which seems overwhelming in a leaky California 1975 house which didn't even have wall insulation or double pane windows on any of the walls (which we are slowly converting as we remodel). In addition as I said the new addition has some sort of foil faced roof sheathing to the interior which needs about an inch of air space below I think to work. Of course spray foam is flammable also but I guess most insulation is. This is a high fire hazard area but most of southern California is I guess. I broached the subject of nonvented with the Title 24 engineer and architect but they both looked at me rather dazed and skeptical. I broached the subject of a different roof design for the addition but the architect just didn't want to go there because the roof is sort of complicated by a previous addition and I guess he was trying to save me some bucks maybe. Hope this helps explain it.
A couple of things: The foil facer on the roof deck is nearly useless, even WITH an air gap, but may have been intended as a work-around on a Title 24 requirement for high SRI "cool roof" colors on on the exterior(?). To really meet spec it would take a true radiant barrier with air gaps on both, not just one side of it.
But the energy performance specs for roofs under Title 24 can also be made with thermal mass roofs &/or higher R.
Both polyurethane and polyisocynurate are flammable, but at a fairly high kindling temp. In a San Diego climate you could even safely use a high-density spray fiberglass (1.8lb Spider or Optima) or cellulose in an unvented roof assembly without risk of roof rot due to the high air-retardency. The 1.8lb+ fiberglass would have a higher R/inch, but wouldn't necessarily outperform the cellulose, due to the much higher thermal mass of the cellulose. In 9.25" nominal 2 x 10 cavities either would put you north of R30 with some margin.
To meet IRC code in an unvented cavity with fiber fill requires R5 of air-impermeable foam between the roof deck and fiber: http://publicecodes.cyberregs.com/icod/irc/2012/icod_irc_2012_8_sec006.htm Unless the roof deck is inherently vented from above (metal on purlins, or tile roofs) without exterior-side vapor barriers, an inch of closed cell polyurethane would be the best bet. But since the roof deck has a foil facer on the interior it renders the requirements for under-deck venting or R5 air impermeable insulation between the fiber & roof deck moot, since there's no way for the roof deck to dry toward the interior side in the first place, and isolating it with air-impermeable insulation won't affect interior-side moisture drives, since unless it's perforated on a tight grid the foil is a powerful vapor barrier. (Got a product name or spec for that decking?)
Filling the cavities completely with cellulose keeps liquid moisture from every forming on the foil in that climate, since the cellulose itself adsorbs the moisture when the roof deck is below the dew point of the interior air, without damage or loss of function. With fiberglass there is a small risk of condensation events at the roof deck foil, but it's small and of little consequence due to the fairly good air-retardency of 1.8lbs density fiberglass.
Roofing type (and color) matter, but with the foil-facer on the roof deck it doesn't matter much. Were it unfaced decking the WUFI simulations for different stackups in San Fransiso or Atlanta outlined in Table 3 of this document would have relevance:
http://www.buildingscience.com/documents/reports/rr-1001-moisture-safe-unvented-wood-roof-systems
But with the foil vapor barrier on the interior face of the roof deck nothing about the interior stackup (including venting) has much affect on the moisture content of the roof deck. Putting a vapor impermeable membrane roof on the exterior of foil-faced roof decking is already a mistake- any moisture that is already in the roof deck will take literally decades to leave (!). If it were my house (and it isn't) I'd just stuff it full of cellulose and re-assess in 25-30 years when it's time to re-roof. Odds are pretty good it'll be fine, but if it isn't. replacing the decking with unfaced plywood decking and putting R5 rigid insulation over the exterior, under the new roofing would be in order. But there's no reason for doing that now, rather than 30 years from now- it is what it is.
You keep telling me unvented in the new addition. What happens to the old roof now when we cover up the lower vents for it? This part of the roof has no foil. It has shingles on it. No insulation above I'm sure. Fiberglass batts in the bays. Its about 3 % slope.
Dana and Martin are IMO giving you complicated plans and no one to do the plan. I say that is plane nuts. Do what your builder and architect agree to do period. Do what you can afford.
I am guessing that your budget is key to what you do.
Thanks for the reality check. They keep saying unvented but then I would be covering up half the vent holes to the main roof. So I'm guessing then I would need to convert the entire house to unvented ?. Can't really afford that right now and unfortunately the contractors/architects here seem to be behind the eight ball on how to do this. Was trying to get a happy medium. Oh well, the house will need a new roof one day. Maybe then I'll change it.
AJ: There's nothing complicated about blocking the vents, filling the bays up with cellulose and waiting until re-roofing time for re-assessment. That IS the course of action I'd take at this point, were it my house (which it isn't.)
The roof venting hardly matters in a San Diego climate, and that's a fact. There is literally no science behind the "1 square foot of net free ventilation area for every 300 square feet of attic floor" applicable to your climate, though that is/was a handy rule of thumb for much colder climates in bygone decades. As long as you don't have something really atrocious like foil or poly on the interior side of the older section, you won't be trapping moisture that would otherwise have been venting. Venting the old roof out through some circuitous path through the low-slow new roof has very dubious moisture purging flow rates at best- not enough stack effect drive, and a lot of flow impedance. Covering up the vent holes may not meet code, but in your climate it's not very likely to create an issue. There are MANY homes in climate zone 3 that don't have soffit-to-ridge venting, and have gone more than 50 years without incurring moisture problems at the roof deck, many of them with blown rock wool or fiberglass batts stuffed into those unvented bays.
Your wintertime interior moisture drives are pretty low and mean roof deck temp pretty high- you won't be rotting out the roof deck in just a few years (or even a few decades) unless you keep the interior humidity at sauna or greenhouse levels. If the roof leaks copious water there's an issue, but it's not as if the poorly implemented venting would have saved you any in repair costs in that eventuality.
When it's time to re-roof, an inch of rigid foam over the roof deck is both dew-point insurance and a thermal break. But there's no urgency here, the way it might be in a much colder climate.
Missing from your posts Dana.... Others
1 project is or right at insulation time. Plans might exist that have been checked by building department. Budget is set. Workers are set. Architect is set.
So now you say stop. Redraw plans via a few internet posts. Forget the existing plan. resubmit plans that the existing plan person does not know how to design. Might have to wait for approval. Find a contractor to read this thread or whatever and take a shot at doing a design he has never done.
I just think many times what is proposed is possible yes but missing in big picture practicality.
So, good idea Dana. But only those actually involved know what is doable. The design is just a small part of the whole picture is my point in my posts.
AJ,
The only reason that Dana and I offered advice was because Lisa asked, "What type of insulation or technique would you recommend?"
If she had a plan recommended by the architect and approved by the local building department, fine. In such a case, I would agree with you that it is almost always best to go along with the architect's specs -- especially if there is no reason to doubt that the architect has a good approach.
But for some reason, she decided to ask for advice.
I dunno AJ, the architect & Title 24 engineer were looking "...dazed and skeptical..." on the concept of an unvented approach, but she didn't say exactly what their plan was, other than hints about leaving an inch gap for some ventilation and to allow the foil facer to provide (whatever dubious) performance enhancement. She asked for and got the realistic alternatives.
Whether the proposed alternatives fly with the Title 24 inspectors isn't known, though she did state, "...the City of San Diego doesn't really care about ventilation of a roof as they told me to my face". but you seem to be suggesting that I simply not answer the question(?). There's no "doing a design", or "Redraw plans", or "resubmit plans " if the San Diego building department (rightly, IMHO) doesn't care about roof deck ventilation- all that's needed is to verify that the installed R-value actually meets code.
Given that circumstance there's nothing to redraw or resubmit to go with the recommended Plan-B. Same rafter cavity, same (or higher) R, different stuff- only the venting (that the city doesn't care about) changes. If that requires a delay for new code approval I'd be surprised.
Thank you so much Martin and Dana for the building science and AJ for the reality checks. The reason I'm asking is because the whole original concept seemed to not make sense and didn't make any more sense when I actually saw it built !!! (but who am I to argue with an architect or engineer) The city is vague or noncommital because they just aren't trained on alot of newer or green techniques and likewise architects and contractors, especially here in San Diego where many older homes still don't have insulation or double pane low E windows. Title 24 code is slowly bringing these things up into the light of day but it is a slower progress for residential than commercial. At least this is my theory. Ventilation was sort of an afterhtought by the architect, not a concern to the city even when there's code so it alludes me as to why except for above theory. . Now whether I can get away with changing the plan without city approval is another story. Technicaly probably not, but no one really cares anyway. Right? So.......................I can cover up the gable vents probably easy enough and probably the turbines with something I guess. Spray the insulation to the underdeck Right? and then do I remove the fiberlass insulation between the lower bays or leave it? How much cellulose would you spray?. I need room to at least crawl in the attic. And AJ is nice enough to say I can wait until I re-roof the rest of the house to put insulation above. Right?
You can safely leave pre-exising fiberglass in the old roof section. A full 9.25" rafter fill of cellulose in the new roof would deliver R32-R34, exceeding your code-min with a bit of margin.
Any type of active ventilation like turbine vents would be a mistake, since it's as likely to draw more conditioned space air into the attic than from the outdoors. Passive vents are fine.
So just to re-cap. Cellulose blown in is really my only option right now (without ripping off the roof). The contractor's idea of a couple of layers of thick rigid foam (sealed in really well from below) and leaving space with baffling for the vent holes and above it will probably cause a moisture problem. Right?
Lisa, there must be countless insulation/drywall contractors in your area. Find a trustworthy one by stopping at construction sites that you get a feel are worthy and stop into the supply houses and explain your needs. Either your contractor knows his trade or get another sub. Etc to aid you and him or you.
Most any method done well will be OK in your mild climate, if your guys can do what Dana posts do that. If your contract calls for your foam idea and is backed up by years of good outcomes and that's what you want to do then do.
Dana, my basic frustration many posts at GBA is the fact that a project is in progress and suddenly the day before next days work posts start flying as what to do or install or... The worst thing to have be part of a project. Throw off the schedule the budget, toss the plans, toss the profit, delay the next customer, mess with the code inspectors, maybe make too quick a decision. Impulse spend more than one can afford, endless. Ie, plumbing faucets picked out after rough in, go pick up faucets and find out it's a special install coming directly thru the back wall....