What methods are remodelers using to control bulk moisture when installing blown insulation in existing walls?

Insulation is needed to control heat loss, but if it is blown into walls that do not have appropriate flashing and a complete drainage plane, there is an opportunity for water to get in the wall causing significant damage to the structure. I have been searching for a solution to this for years with no luck. Anyone have any good ideas?
GBA Detail Library
A collection of one thousand construction details organized by climate and house part
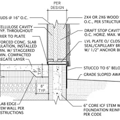
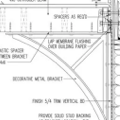
Replies
Hi Carl
I saw a remodel in New Orleans where they pulled the interior walls and the siding that covered the band joist and lined the interiors of the stud bays with tarpaper that was threaded down over the band and stapled out an inch or two onto the studs to direct water away from the insultion and out over the band to below the top of the foundation. We tried this last fall on a gut rehab with good success. In both cases the insulation was spray foam ( open cell picture frame application ) to seal the tarpaper to the studs and plates before filling the cavity. I have tons of pictures and some video of the project if yo want to take a look.
Michael,
Could you please provide a link to those pictures and video of your project? Visual details would provide a good understanding of the process.
Appreciate your help.
Michael - I appreciate the info, but I am really looking for solutions where the walls are not opened up. I am heading to the conclusion that there is no solution to this problem - and that we should not be blowing insulation into existing walls without first stripping siding, flashing windows, and installing a drainage plane. But there will be lots of people blowing insulation in walls and causing lots of long term problems.
Carl,
Here in Vermont, contractors have been filling the walls of old houses with dense-packed cellulose insulation for 20 or 30 years. We have lots of experience with the method. We are not seeing wholesale wall failures or a huge spike in wall rot.
There are signs that exterior siding paint is now failing faster than it used to. This is consistent with the fact that the siding is now colder than it used to be, a little wetter on average than it used to be, and slightly slower to dry than it used to be. Obviously, the paint would last a little longer if it were installed over a rainscreen. But that's expensive to do. So here in Vermont, people either (a) accept the fact that their siding looks a little ragged towards the end of the painting cycle, or (b) paint more frequently, or (c) call up the vinyl siding contractor.
I think you are expressing a little too much concern about the chances that insulating existing walls will lead to huge moisture problems. What you want is a wall that dries well -- ideally to both sides. Existing houses usually dry well. Here in Vermont, old houses have board sheathing under clapboard siding. The exteriors tend to dry well. Interiors are old lath-and-plaster without poly; they also dry well.
Adding cellulose does reduce the drying potential of the entire assembly somewhat, but cellulose provides a moisture buffer and tolerates minor problems, as long as wetting incidents are followed by a drying opportunity.
Of course, if you can identify an obvious problem with exterior flashing or water entry, that needs to be addressed. Otherwise, I wouldn't worry so much.