What is the best way to insulate a central supporting post?

We are building a “High performance” 30’x34′ house in northern NH. R32 ICF foundation in place and capped . R30 subslab 25 PSI XPS in place. Unfortunately builder placed a central steel/concrete filled lolly column (supporting post) for the 34′ beam of the subfloor down the center penetrating the 6″ XPS to a central footer. Not sure how much of an issue this is but worried about this penetration. Slab not yet poured. Put on hold to consider alternatives.
We have a number of options:
a) wrap the post in R20-R30 which is the present plan. (the top of the post is attached and therefore is cannot be entirely wrapped)
b) pull the central post and replace the some of the foam with 60 PSI or similar and replace the post (requires significant work and builder not confident point load of post on even 60 PSI foam won’t sag) and reinforce concrete under the post.
c) pull the post, jag hammer some of the footer to dig deeper, pour 8″ concrete slab in central area and add rebar under the post for structural integrity…. Will likely only get R20 in a central section of the slab in that case… (again @ 1/2 days extra work)
Thoughts?
Experience with supporting posts centrally (this is the only on across the 34′ span)
GBA Detail Library
A collection of one thousand construction details organized by climate and house part
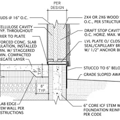
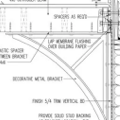
Replies
Phil,
1. Are you the owner or the GC?
2. What do the plans and specs require? Did the builder goof? (If so, the builder is responsible for the costs and has to make it right.) Or did the architect / designer forget to indicate the required detail on the plans?
I would not put foam insulation under a concrete pier unless you have engineering to show that it's OK. In situations like that, the best you can sometimes do is to dig a deep hole for the footing and line the sides of the hole with foam, but pour the concrete onto grade.
Honestly, I don't know that I'd worry about it. A small "thermal siphon" like that is probably equal to a very small area of window glass above grade somewhere in the building shell. After all, it's protected by the rest of the slab insulation around it. It would be worse if it were at the perimeter of the building.
Owner, Martin
Both occured
Plans did not detail where the post went (ie appeared onto the concrete then footer put in by builder)I In agreement re costs. Learning.....
What do you think is best solution?
Phil
I never can understand why so many build first and plan second. I get plans by others still to this day with no mechanicals plans And no details of complicated assemblies like screen porches with half walls.
I say choose your option and move forward at this point. Lesson learned.
Phil,
We've had to deal with this situation as well, but our columns weren't placed yet, so that could change the situation. We chose B, but you'll need a structural engineer to verify your loading will be adequate if you go that route.
60 psi foam carries a huge amount of load. A 30" x 30" footing is 900 sq inches, and at 60 psi, that's 54,000 pounds, a massive load for a small house. The PSI is usually measured at 5% compression, which is substantial and could lead to cracking, so XPS recommends a 3:1 safety factor, which would get you down to a safe level of compression with the likely reduced load.
In the similar situation, we thinned up the foam a bit on top of the already poured cold footing, thickened the floor slab at the column with extra rebar for extra slab stiffness, and cut the column shorter to bear on top of the floor slab.
I agree with David. It isn't worth the heroics involved to deal with what is a tiny area of uninsulated steel going down into relatively warm sub-soil. You will probably lose more heat through you main drain or even the ground on you electrical service. These are insignificant penetrations.
Hi,
I'm in the process of buying a 109 year old frame house. There appears to be an retrofit insulation job that was done at some point (small evenly spaced plugs in wood siding). The interior walls are a mixture of drywall and plaster. I have a thought to hire a contractor to remove some of the wood siding to see if there is a moisture problem. Do you have any tips regarding this endeavor?
Jenny,
First of all, it would be better to start a new thread with your question instead of posting it on an existing thread.
To address your question, however: what evidence do you have that your walls have a moisture problem?
Hi Martin,
First of all thanks for reminding me for the mistakes that I have committed in posting a new query in the continuous thread. But I thought since same issue is being undertaken here I have shared my problem also. However, I came across the decision of developed moisture problem on the wall soon I found mold and mildew on the inside surface of cold exterior walls. I, therefore thought to hire a experienced contractor to resolve the issue. What’s your take on it?
Jenny,
If you have mold on the interior side of a cold wall, that is usually evidence of either air leakage through your building envelope (your exterior wall), or elevated indoor humidity, or both.
To solve the first problem, you need to seal air leaks in your envelope. The best way to do that is with blower-door-directed air sealing.
To solve the second problem (if it exists), you need to locate the interior moisture sources and see what you can do to mitigate them, or you need to increase your ventilation rate (for example, by running your bathroom exhaust fan for more hours per day than you presently do).
If you are unsure how to diagnose these problems, I urge you to hire a home performance contractor to conduct an energy audit of your home.