What is a good and resilient approach to weatherizing a log home?

I recently audited a log home in central Vermont (climate zone 6). Unsurprisingly, it was really very leaky (19ACH50). The client is willing to go fairly deep with regards to weatherizing the home, and we both agreed that a reasonable approach seemed to be building a 2x wall inboard of the existing logs and filling the stud bays, including a varied amount of space behind the new stud wall. I would prefer to hold the new stud wall at least an inch off the logs, if the lose of interior space would be acceptable. The whole structure is less than 1200 sq ft, so it’s not a big home, and losing more interior square footage than might be strictly necessary could be a hard sell.
I’m wondering if anyone can make the case for a specific amount of spray foam behind the stud wall, as a continuous layer? Beyond “more is better”, is there a minimum safe amount that will avoid the risk of condensation against the face of the logs? I’m thinking to shoot for 4″ of foam – a 2×3 wall would give me roughly 1 1/2″ foam behind the studs, on average.
Am I thinking about this correctly? Is there another approach that I should consider before defaulting to foam?
Any advice would be greatly appreciated.
Thanks!
Dave
GBA Detail Library
A collection of one thousand construction details organized by climate and house part
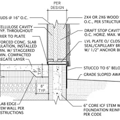
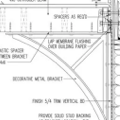
Replies
Dave,
There are two basic approaches to this challenge. You can either add insulation on the exterior, or you can add insulation on the interior.
I favor the exterior approach, because it doesn't take up interior space. The problem with an exterior approach is creating a planar surface. If the logs are close to co-planar, you can use a layer of exterior rigid foam, followed by housewrap, furring strips, and siding. If the logs are far from co-planar, you can install vertical 2x4s, carefully shimmed to be co-planar, followed by spray foam.
If you have to work from the interior, your approach will work. If you use 100% spray foam, there is no minimum or maximum thickness of the spray foam, other than the minimum needed to create an air barrier -- generally about 3 inches for open-cell spray foam or 1.5 inch for closed-cell spray foam. (For more on this topic, see Air Leakage Through Spray Polyurethane Foam.)
If you want to use a combination of spray foam and fluffy insulation (like fiberglass) on the interior, then you have to follow the rules for flash-and-batt jobs. To learn more about those requirements, see Flash-and-Batt Insulation.