What combination of foam insulation for this wall?

I’ve got a wall that has seen substantial water damage, and the existing fiberglass insulation is destroyed (along with the studs, sheathing, and sill, but that part I’ve got covered).
The existing wall was:
1/2″ sheetrock, paper-faced fiberglass between 2×4 16oc, 1/2″ ply sheathing, 1/4″ EPS, aluminum siding
I despise fiberglass insulation. The contractor who is doing the repairs asked me what I would like instead of fiberglass, but I’m not sure what to spec.
I’m in central NJ.
I would prefer 3.5″ foil faced polyiso. However, the thickest foil faced polyiso available in my area is 2″. I would sandwich two layers, but I worry about the double vapor barrier due to two layers of foil. No one seems to sell unfaced polyiso in my area.
I cannot do continuous foam because we’re not replacing the entire wall, so the width of the wall cannot change. All insulation needs to fit in the stud bay and I’ll have to live with the thermal bridging.
Would the following wall arrangement work?:
1/2″ sheetrock, 2″ foil faced polyiso btwn studs, 1.5″ unfaced XPS btwn studs, 1/2″ ply sheething, tar paper, house wrap, 1/4″ EPS, siding
GBA Detail Library
A collection of one thousand construction details organized by climate and house part
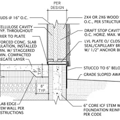
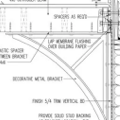
Replies
Without knowing for sure which side the moisture drives are it would be risky to put foil facers in there.
Unless it had facers on it the 1/4" EPS should have allowed reasonable drying rates toward the exterior. But if it DOES have a foil or plastic film facer on it, it almost certainly has to come out to be able to use foil facers on the interior side of the sheathing which would require re-siding. If you ARE re-siding, be sure to properly lap the window flashing to the housewrap, and go with at least R3 on the exterior (R4 if you're close to the edge of US climate zone 5), which will take more than 1/4" (which is only about R1.)
The best you can do without re-siding and adding sufficient exterior R for dew-point margin at the sheathing is to caulk the sheathing to the framing from the inside of the stud bays with acoustic sealant caulk, taping over any seams with housewrap tape then reinforcing the tape with a layer of duct mastic for a more permanent bond to the wood, and install cellulose in the cavity (either damp-sprayed, or dense-packed in mesh), and install a smart vapor retarder such as Certanteed MemBrain or Intello Plus on the interior before installing the new sheet rock.
The cellulose would buffer & redistribute any moisture that makes it into the wall cavities, the smart vapor retarder would limit the wintertime interior moisture drive, but becomes vapor open when the warmer weather starts releasing any accumulated moisture from the sheathing & cellulose, maximizing the drying rate toward the interior.
Mind you, the vast majority of moisture problems in studwalls with your prior stackup is bulk water leakage from the exterior. If the window flashing is absent or improperly lapped to whatever tar-paper you have next to the EPS it could be bringing water between the EPS and sheathing. If there ISN'T any, that's the problem! Rather than doubling up a layer of felt with a layer of housewrap, pick one- either will work, but there is no point to having both. But the window flashing still has to lap properly onto whatever you picked.
David,
It would be helpful to know why this wall had such a serious moisture problem, and why you believe that the problem has been remedied.
The approach you are describing is the "cut-and-cobble" approach. This method is rarely used by insulation contractors, but is sometimes used by homeowners. For more information, see Cut-and-Cobble Insulation.
I agree with Dana that it would be good to know whether the existing layer of 1/4-inch rigid foam includes a vapor barrier. If we don't know whether this wall can dry to the exterior, it's hard to make a recommendation.
If you don't want to install fiberglass insulation, you could install dense-packed cellulose or open-cell spray polyurethane foam. If the wall system can't dry to the exterior, I wouldn't advise the use of closed-cell spray foam.
The moisture issues are unrelated to any insulation or vapor barrier; some missing flashing and a hole in my lower roof, and an unextended downspout from the upper roof positioned about 4" away from it was literally dumping all of the water from my gutter down into the wall. I only bought the house a year ago, and one of the first things I did was extend the downspout into the lower roof's gutters, and the hole itself is protected by eaves from the upper roof. As a result, since I moved in I never noticed any actual water in the house. My contractor feels that this hole was probably there when the house was built, so over the last years the entire wall cavity rotted out, including the top plate, studs, sill, and subfloor it was sitting on, all the way down to the block foundation walls. This issue is now fixed.
I unfortunately don't have the luxury of spray foam or cellulose, because I can't wait for scheduling with a contractor to do it. My wall is currently open on both sides and tarped, and NJ is currently seeing -5 degree weather in the evenings. My options are limited to what I can purchase from a home center and install myself.
The foam was so destroyed by the water that I have no idea if it was faced or not. I can at this point do either, but wouldn't putting a vapor barrier on the last 1/4" of the wall be a bad idea in a heating dominated climate? Vapor from the house would in time make it to the sheathing and condense, because the 1/4" insulation's R-value is negligible compared to the wall cavity insulation leaving the plywood at near-outside temperature.
David,
If you are installing new 1/4-inch EPS, and you can be sure that this layer is vapor-permeable, you can install almost any type of insulation between the studs that you want. Two layers of cut-and-cobble polyiso would work, although it would have all of the usual disadvantages of any cut-and-cobble job. Having multiple foil layers in this type of foam stack-up won't cause any problems, as long as your sheathing can dry to the exterior.
One day I will re-side my house to get rid of the aluminum siding I have now. At that point I'll pull the sheathing, replace the aged and sagging fiberglass with Roxul, replace the sheathing, and do 2" polyiso before putting on LP SmartSide. At least, that's the dream. :) Until then, cut-and-cobble is the best I can do for these sorts of partial wall repair jobs.
Are you sure I can do two layers of foil-faced? Let's say I do a 2" foil faced followed by 1.5" foil faced followed by sheathing. If the inside temperature is 70 and the outside temperature is 0 (worst case design), the temperature of any air trapped between the layers would be approximately 30 degrees. If any vapor does manage to get from the interior through the spray foam around the edges and into that space and linger, wouldn't it definitely now condense and drip down onto the sill plate?
If you can get mineral wool batts from a local home improvement store or lumber yard, you could do a lot worse. I love this stuff. It has a very good R-value (R-15 for 3.5"), it's easy to install well, and it's totally hydroscopic. Like fiberglass but better in every way IMHO.
Lowes, Home Depot, and Menards all carry it in varying capacities; at some places it's a special order and at other places they'll just have it right there on the shelf.
I can get mineral wool batts, but they have no vapor barrier. Somewhere in this system there needs to be a vapor barrier or retarder.
David,
There is no building science reason or code reason to install an interior vapor barrier. All the code requires is a vapor retarder; vapor retarder paint will work.
However, it's always important to pay attention to airtightness. In your case, you should do what you can to make the wall sheathing layer and the drywall layer as airtight as possible.
If you go ahead with your cut-and-cobble plan, your layers of polyiso will be installed in an airtight manner. You won't have any vapor diffusion through the foil-faced polyiso, since foil-faced polyiso is a vapor barrier. And you won't have any way that indoor air can flow between your polyiso layers, unless your installation method is extremely sloppy.