What are the potential problems in an open-cell foam sealed attic when voids and inconsistencies exist?

Along with the open-cell insulation, a radiant barrier roof sheathing was utilized. In most cases, half of the roof framing member (12″ TGI truss & 2″ X 10″ out-looker) surfaces are not encapsulated. There are potential areas where exterior wood framed attic walls are not insulated or sealed off from the attic space. The foam insulation was applied after A/C duct and Can lighting fixtures were in place between the framing members. Most ceilings are cathedral with a tongue & groove wood finish. I am seeing unexplained water damage at different levels of the roof sheathing and roof membrane systems. These conditions have been exposed, repaired, exposed again with moisture still a problem. This project is in central Florida.
GBA Detail Library
A collection of one thousand construction details organized by climate and house part
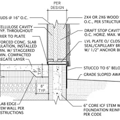
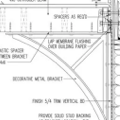
Replies
Is there anything between the t & g finish ceiling and the TGI truss rafters?
Is the foam sprayed directly onto the foil-clad roof decking?
Yes, the T & G ceiling was nailed directly to the TGI truss.
Yes, the open-cell insulation was sprayed directly foil-clad plywood roof sheathing.
Michael,
It's hard to know what is going on from your description. Can you post some photos?
Water stains are usually indications of either (a) roof leaks or (b) condensation, which occurs when hot, humid air -- in your case, probably exterior air -- encounters a cold surface (in Florida, that usually means a surface that has been cooled by an air conditioning system).
If the foam was installed to create a conditioned attic, it must be continuous. There can be no interruptions in the home's air barrier or thermal insulation. Any discontinuities would obviously be problems.
The foil on the roof decking is useless as a radiant barrier when it's in direct contact with the foam. Radiant barriers need an air space to have any thermal benefit at all.
The foil is also a true vapor barrier, and so is the roofing membrane, so even tiny leaks from fastener penetrations have effectively no drying path, let alone any membrane seam leaks. It would have been better had the insulation been applied to the t & g with a vented air gap between the foam & roof deck and no foil, &/or if there had been a ventilation space above the roof deck with something semi-permeable like #15 felt on the roof deck, and not an impermeable membrane.
Can you tell us more about the exact products used in the stackup on top of roof deck?
Following up on Martin's comments, it it's the t & g that is showing the damage (and NOT the roof deck), that could be from outdoor air leaking in via the unsealed uninsulated walls and condensing on colder materials in the rafter bays, dripping onto the t & g.
Another over looked scenario is an over sized HVAC system if the foam was added after the fact.
Other options to look for are poor ventilation, lack of air exchange (No ERV installed) and /or a poor installation of the foam. If the foam is shrinking or cracking open showing small to large voids your dealing with an installation issue which could potentially be a toxic issue.
Over sized HVAC systems will cause excessive condensation. The only solution is to size the HVAC correctly or install a whole house dehumidifier. This can prove to be a costly band-aid. I would also suggest calling the SPFI company back to have them perform a blower door test and thermal imaging scan on the home and correct the inconsistencies.
If they refuse to fix the problems (installation related claims) then your only choice is to call upon a certified SPFI contractor approved by ACC, CPI, SPFA or a similar certifying trade organization and to also call upon the chemical manufacturer or distributor your contractor uses for assistance. No one wants any more bad publicity then what has already taken place. That's my opinion for what it's worth.
This is a seven year old home. The roof has been routinely checked due to unexplained occurrences of moisture at wall and eave locations. At no time has a breach in the roof membrane been exposed. However, staining below has caused us to open the roof at wall, eave and field locations to discover moisture. The flashings appear to have rust at the inside part of the roof flange and not at the membrane termination.
There are (2) different roof assemblies.
Assembly -1: 2.5/12 pitch Foam adhered, Concrete Flat Tile Roof with an underlayment membrane comprised of a nailed 43# anchor sheet and a torch applied, granulated modified bitumen cap sheet. Evidence of moisture including water staining, white fungus, deterioration is showing on much of the sheathing when exposed. Most staining is at the joints in the sheathing, at fasteners, including the deck nails and areas where there are voids in the insulation. We have also discovered some areas of concentrated moisture where the 43# has been permeated and water has accumulated on the bottom side of the modified cap sheet.
Assembly - 2: .5/12 pitch Low-Slope Roof System comprised of a mechanically fastened anchor sheet, a torch-applied mid-ply membrane and a torch-applied granulated cap sheet. This system terminates at eave flashing and wall flashing details. The moisture is occurring between the torch mid-ply and cap sheet membranes. The cap sheet was replaced in one area where moisture had completely separated the membrane. A recent core of this area shows the materials have again separated.
In my opinion, Sir your dealing with a spray foam installation issue. See here....
http://masonknowles.com/docs/troubleshooting_sprayfoam_insulation_jlc2010sept.pdf
I can pretty much guarantee you the chemical manufacturer will concur. Your only recourse is to find the installer and make an insurance claim on his/her policy. Chances are high the claim will be declined due to workmanship error. The same can be said from the homeowners policy. This results in one action, courts. In Florida the courts have protections in place for issues like this which are found under 10 years. Unfortunately the builder will be the named defendant if he hired the insulator. This could be a better scenario for the homeowner then chasing the insulator. I know of a few people in Florida going through the same thing.
The stackup is highly vapor retardent on top (as anticipated). Any moisture that gets into the decking can only escape at the seams, so it's not too surprising to find the issues following seam lines. The fact that it's predominately at the wall/roof boundary hints that exterior air is finding it's way to cooler condensing surfaces.
Without a site visit this could be pretty tough to make a definitive diagnosis.
The pictures show a section where there were insulation voids over what appears to be an air conditioning duct(?). That may be sufficient to make the roof deck cold enough for condensing at that spot, but with an air-impermeable vapor impermeable layers on both sides of the wood, that's not going to cause a problem with the roof deck, even though it isn't great for energy efficiency. For much moisture to get into the cold wood, it has to be in contact with humid outdoor air.
Imperfect as the foam installation might be, it's primary contribution to the problem would be if it's not actually air tight, a factor that IS test-able (with a blower door.)
In the grand scheme of things, the biggest cause of moisture problems is direct bulk wetting, from leaks or improperly lapped flashing/weather barriers etc.
Next in line is air leaks allowing humid air to come into contact with surfaces & materials cold enough to condense or adsorb moisture from that air.
Way down the line below that comes vapor diffusion. Vapor diffusion can be an important factor for allowing assemblies to dry when wet, but it is only rarely the proximate cause.
Dana theory is out the door here. This failure is not as complicated as your explanation.
A bad job is just that which leads to more problems with OC & CC foam.
Here's where Dana theory comes in to play in this former GBA article....
https://www.greenbuildingadvisor.com/blogs/dept/musings/open-cell-spray-foam-and-damp-roof-sheathing
Pasted from http://www.sprayfoam.org/technical/faqs.....
Can spray foam shrink?
When improperly applied, some SPF, particularly closed-dell foams, products may shrink and pull away from structural members. Improper equipment settings or excessive pass thicknesses can result in foam shrinkage. While isolated amounts of shrinkage can occur, the number and size should not be extensive. Cracks and gaps caused by shrinkage can compromise the air sealing performance of the SPF, and could result in moisture condensation problems in colder climates. Extensive shrinkage should be repaired.
What causes delamination and adhesive failures with SPF?
Much like painted coatings, SPF should strongly adhere to nearly all construction materials that are clean, dry and free of oils and grease. If the substrates are free of oil, dust, dirt and moisture, and applied according to manufacturer’s instructions, there should be no problems with SPF adhesion. Adhesion should be occasionally checked by tearing a small area of foam from the substrate. When properly adhered, the foam itself should tear, leaving a thin but visible residue of foam on the substrate. However, SPF may not adhere well to some construction materials, such as polyethylene sheeting, under-cured concrete (containing excessive moisture or surface contaminants) and certain metals. These materials may need special surface treatments, such as primers or coatings, before SPF can be applied.
An important difference between this case and the prior GBA article is the impermeable foil on the interior side of the roof decking.
https://www.greenbuildingadvisor.com/blogs/dept/musings/open-cell-spray-foam-and-damp-roof-sheathing
Another distinction is that the house is located in US climate zone 2, not 3 or 4, but with foil clad roof decking wintertime condensation issues would result in wet foam, not wet roof decking.
Yes, it's a crappy foam job, but not the clear proximate cause of the problem. The stackup is a problem though, as outlined previously.
The bond strength between foil & foam is evident in the autopsy photos- the foil tended to stick as much to the foam, not the sheathing itself. Bonded or not, the foam is incapable of forcing moisture into the wood decking through 0.05 perm aluminum foil.
Dana,
Is foil backed sheathing an approved substrate to install OC foam on? How do we know the sheathing was in new condition when it was installed and not damaged? How do we know the foil covered sheathing was not left out in the weather for a prolonged period of time before it was installed? How do we know the foil was well bonded to the sheathing prior to installation? Where are the ICC-ES Evaluation Reports to support this was a proper installation of combined materials?
Maybe the original poster would be so kind to share this information with us?
I had the opportunity to see open cell foam perform like this in zone 5. The oc foam was completely separated from the sheathing, but well bonded to the rafters and studs. When the oc foam was removed, a previously applied mold abatement paint applied over the sheathing was very damp with condensation. The oc foam was also permeating a chemical odor associated with a poor installation. The roof oc foam was coated with an intumescent paint which did not meet the manufacturers mil thickness leaving the color of the foam exposed in the overlaps.
The foam also shrunk upon itself as shown in the above photos. The remediation crew did not have to use much effort to remove the oc foam using only a butter knife to separate the foam from the rafters and studs.
I believe as more time passes we will start seeing more and more of these failures. Roofing crews will be the first reporters of this issue. I'm also aware of a 10,000 sq. ft home in zone 5 where the entire roof was removed due to mold, name brand oc foam and sheathing rott after 5 years of service.
This home was heated with hydronic under floor heating and cooled with central air. The basement had in slab heating with 4 inches of polyiso under it. This home build was controlled by structural engineers and an architect step by step through the process. Nothing was assembled without some form of expert intervention and this included the foam manufacturer inspections. It still failed.
In response to the last post by Richard Beyer. This project is a very large (10,000 sq. ft.) custom home. The design is very modern having many different roof levels and vertical walls that intersect each other. There are many areas where roof structures cover both conditioned living space and large areas of exterior overhang or porches. Due to the unique design, much of the roof structure required a combination of engineered trusses and conventional framing. The construction created many conditions where if the framing was not completely encapsulated from below (which it is not), air gaps to the roof membrane were left wherever joints in the sheathing lined up. That along with a very inconsistent OC job that is separating from the trusses seems to creating all different scenarios of moisture, depending on the differentials in temperature, humidity, pressure, etc. between the attic and roof surface and everything in between. Also, the intersecting walls are in insulated with conventional Batt insulation. Most of these walls carry through from interior to exterior conditions up to the roof structure. Finally, the large overhangs (3- 4 ft.) are not insulated. Many areas of the roof sheathing is showing stains from moisture at the perimeter even though the roof membrane is in tact and no signs of leakage to the stucco enclosed soffit exist as would be the case in a normal roof failure. The project was completed over approximately an 18 month process. The sloped (tile) roof areas were covered with a 43# dry-in immediately after the sheathing was installed and inspected. The low-slope roof areas were covered with a mechanically fastened anchor sheet and a torch applied smooth surface modified bitumen, including an 8" wall flashing detail. A metal "L" flashing was installed at the walls, fastened and sealed to the wood wall sheathing. The house wrap overlapped this detail. The granulated torch down cap sheet for both roofs was installed (6) months later, after all trim and stucco was completed. At no time during the dry-in stage was water intrusion evident. An addition layer of 43# dry-in was installed on the sloped roof to provide a proper, bondable surface. The tile finish of the sloped roof was installed a year later. The roof was gone over several times to ensure the membrane was 100% prior to the tile being loaded and after it was loaded. Our first experience of moisture intrusion occurred approximately a year later and has continued at many different areas and roof details since.
Oops... Post went on wrong topic somehow... I moved it.