What are the cost coefficients for applying pretty good building techniques?

Recently, I was given some feedback that the kind of strategies I was looking to use in a new home are ‘complicated’ and ‘add a lot’ to the overall cost.
That didn’t sound quite right to me, so I’m looking to ensure that my beliefs about the cost of applying building science/higher performance building techniques are grounded in reality.
I know that many folks on here have a lot more experience with this stuff than I do – I probably learned about all or most of these items from Green Building Advisor – and I’m hoping to benefit from your collective experiences to come up with a well founded generalization around how much certain ‘good practices’ should add to the cost of construction.
Given that costs vary wildly by region, I’m hoping to generalize this based on a percentage. I put some questions I’m thinking about below, but welcome any other additions to this list:
What would be % difference between a conventionally sheathed + wrapped house and using ZIP system?
What % extra work is involved in framing a house and using air sealing techniques like sealant on the sill plate, taping the sheathing to the foundation, rolling zip tape, using a flange to extend the air barrier to the ceiling?
What % extra cost is involved in using dense pack cellulose as opposed to fiberglass?
What % extra cost is associated with using a ventilated rain screen assembly vs nailing directly to the sheathing?
What % additional cost should a ‘normal’ (not Zehnder) ERV add to a house?
What is the % additional cost of installing a tilt/turn window, as compared to similarly sized double hung windows (note: not including the cost of the window itself)
GBA Detail Library
A collection of one thousand construction details organized by climate and house part
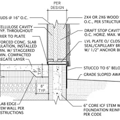
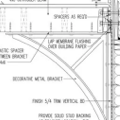
Replies
The ZIP system is common here in the northeast on low-budget builds because it's a fast way to get sheathing, air sealing and WRB all in one step. I would say that it adds nothing to the cost but if a contractor hasn't used it yet (hard to imagine, but possible) then they might be adding an upcharge for the uncertainty.
The air-sealing techniques add a few hours and up to several hundred dollars in materials for an average house.
Cellulose vs. fiberglass is very location-dependent. Around here cellulose costs up to twice as much as fiberglass batts.
Rain screen battens cost a few hundred dollars in materials for a typical house, and a few hours to install them. They do make installing windows and doors more complicated so add a few more hours for that.
Balanced ventilation systems cost $3K to $10K installed, depending on the equipment, project layout and installer.
Window costs vary widely. The least expensive tilt//turns I use cost about the same as a double-glazed Marvin Elevate, which is the lowest-end window I typically use, at roughly $1200 per average-sized windows. You can get cheap, double-glazed PVC windows for less than half that price.
I realize those aren't the percentages you asked for but overall I would say that you're looking at somewhere in the ballpark of 5% to 10% extra to build a house to somewhat high-performance standards.
What's not included in that range is that usually people who want high performance are willing to forgo luxuries like fancy interior and exterior trim, high-end kitchen appliances, complicated rooflines, rarely-used square footage and other ways of spending money on houses. If you're looking at an ultra-basic house as a starting point, with no "slop" to trade off. If you're looking at a typical new, middle-class or upper middle-class home, tradeoffs can result in a PGH costing no more than its neighbors.
Also not included is the improvement in comfort, health, ability to withstand power outages, durability/maintenance, reduced heating system size, etc..
Most builders simply don't want to change how they already do things and they charge more than is reasonable if you force them to do it. As a designer, I find that it's better to find builders already on board with the principles and work together to find systems they find effective. That's not possible in every market.
Michael,
I guess it depends on what kind of windows you use, and where in the wall they fall, but with flanged ones fastened to the sheathing I don't find adding a rain-screen alters the way I handle them at all. The window and head-flashing get installed, and the opening sealed. Then the rain-screen furring is attached around the opening.
Malcolm, do you need to trim the windows differently?
In general, would you say your experiences and Michael's are similar? That 'pretty good' building techniques don't add a significant surcharge to a house?
Adam_F,
No, with flanged windows installed on the sheathing, everything mimics the same wall without the rain-screen.
I'm afraid I can't be of much help concerning the up-charge. Unlike Michael, I've always designed and build code compliant houses, not high performance ones. Our code here in BC now mandates what would be considered a Pretty Good House, so the distinction that used to exist has largely disappeared.
Thank you for your thoughts on this topic, Michael. I appreciate the thoroughness and thoughtfulness of your response. I certainly don't mind you giving actual numbers!
I am trying to be careful about comparing apples to oranges when it comes to costs, but my takeaway is that in a scenario where where there is a willingness to trade off on or defer certain amenities, the added cost should not really amount to much at all, relative to the overall cost to build.
Deleted
Hi Adam,
I have built many houses, but only one high-performance building, and am in the process of building a high-performance house. You will probably be disappointed to learn there is no percentage unless it is in a development of identical builds. Here is what I have learned. Not only do different regions have different pricing they have different requirements, climates, and wage rates not to mention architectures and available building materials (I could not source cellulose period in my area until six months ago). In the end, whether it is a high-performance home, or a basic build to bare code. It comes down to how good your plan is and how you train your employees and regular subs. A rainscreen is always good, air sealing with a proper ventilation system is fantastic. It can be inexpensive and not bad on labor, or it can be a nightmare of poor planning, or poor workmanship, or worse not understanding the technology, or subs that don't understand and do it "the way they always have". I don't like exterior insulation, but I live and work in a high desert climate and can train how to frame a double stud wall very easily to a framer who has never done it. If I lived in a marine or wet climate my likes would be different and my plan would be different. A well-trained team is solid gold, they can earn a higher wage and still cost less than a slow, inexperienced, or poorly motivated team. Once I feel I really understand the science, the materials that are best for my customers, and how to get the details done right in a fast workflow and use materials that are best for the environment. Then my goal will be 6%. Why? That is the sweet spot for my market to sell that upgrade to every customer that comes through the door. It is good for the environment, it is good for my bottom line, and it gives my customers a TCO that pays them back over time. For every percentage point over 6% there will be a percentage of houses sold that don't go high performance. We will see how it goes.
I think what may be left out of your equation too is the ability to potentially downsize your heating/cooling equipment, as well as, your overall annual energy expenses which will add up over time (vs one-time purchase to install these items).
That's a good point. I would consider that something that might fall under the category of a 'trade-off' -- if I apply building science informed techniques and they reduce my heating/cooling loads, it would potentially mean paying more for air sealing and less for mechanical equipment.